Yokogawa’s distributed temperature sensors ensure comprehensive monitoring of thermal events in real-time, limiting facility damage by decreasing the risk of fire/duct explosions in exhaust air/fume ducts, allowing for early detection and quick response.
Application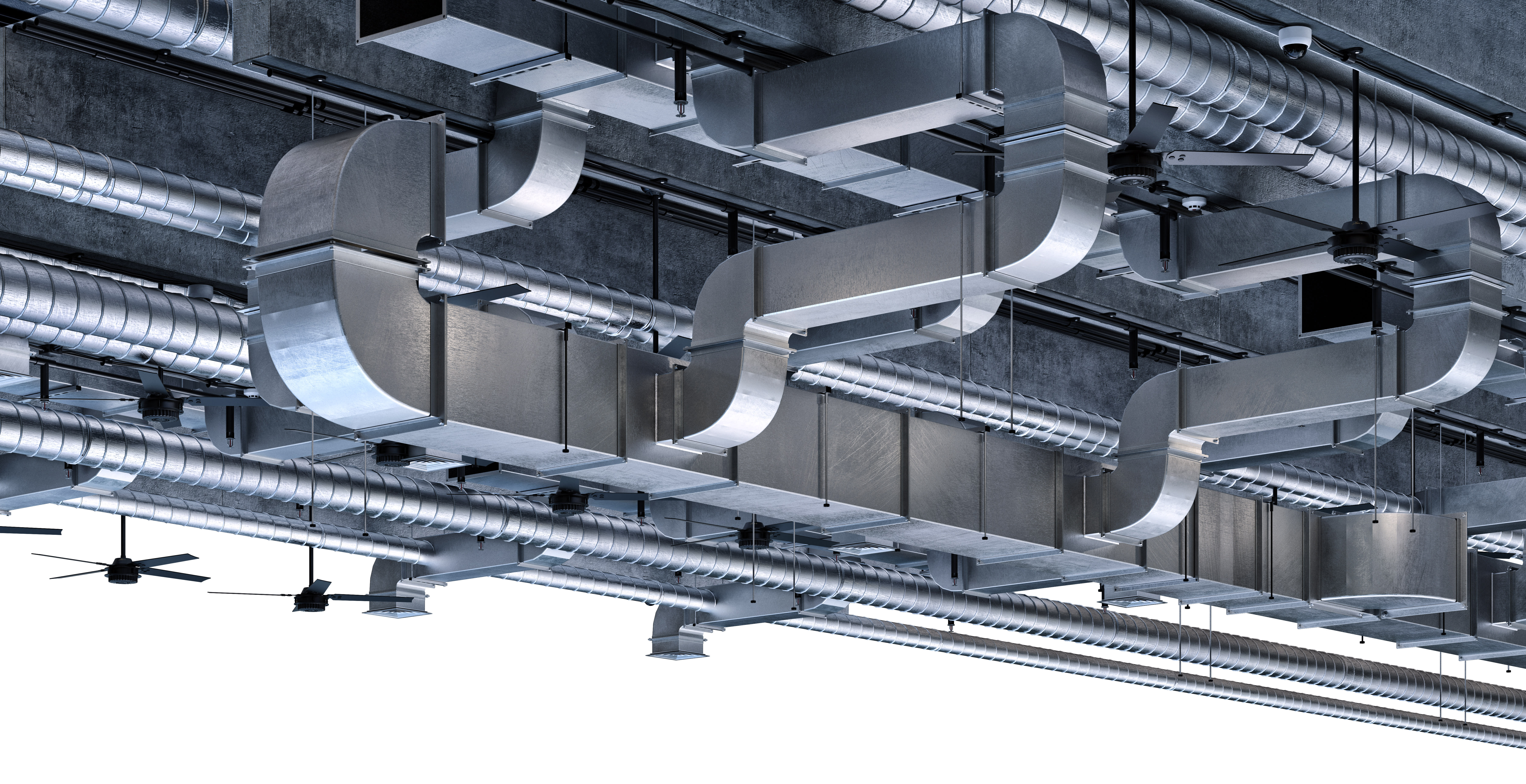
Most manufacturing facilities must remove air through ducts to eliminate the influx of materials that might contaminate the product or harm workers. In some processes, the air contains material such as fine aluminum dust that can cause explosions or fires in the air ducts.
In steel industry has fume ducts in rolling mills, and oil is sprayed on the rollers to reduce friction and stabilize product quality.
The oil vapor, together with dust and other materials, is sucked up into fume ducts mounted directly above the rollers. The oil residue builds up on the inside of the fume ducts and is dried by exposure to high-temperature gasses, making it highly flammable even at relatively low temperatures.
Challenges
Potentially flammable dust in the ducts increases the risk of explosion. Some dust explosions are not detected until they have negatively impacted the facility — such as when a catastrophic duct failure occurs or when smoke is found outside of the building.
To monitor these ducts, maintenance must ensure they are clean of materials that could cause fire or explosive events. These ducts are typically in hazardous locations, are in very poorly lit areas, or are installed in hard-to-reach places such as at ceiling height. Assuring proper cleaning can place team members in potentially risky situations.
Traditionally, manufacturers use thermos cameras or point sensors to detect heat in the ducts. Both technologies require the use of many units in strategic locations, which can mean increased construction and installation. During the life of the technology, maintenance costs can be significant for each device. And in the end, either solution could leave a facility with blind spots that could lead to a loss of coverage.
Solution
Yokogawa’s distributed temperature solutions (DTSX) ensure comprehensive monitoring of exhaust air/fume ducts in a facility. More economical than conventional sensing methods, the DTSX1 heat detector uses fiber optic cable and can be installed in or on ducts, regardless of the length, without blind spots.
The DTSX1 has a flexible configuration and can be set up to suit the environment where it is installed. If the temperature goes out of specification in the duct, the DTSX1 can point to the specific area in the duct so the condition can be addressed quickly. The DTSX1 supports various alarms including differential temperature where the fiber optic cable is paired with an external thermometer alarm. Or an alarm can be a simple upper-limit or rate-of-change alarms.
This can lead to the discovery of thermal events at an early stage, allow for quick response, and limit the damage to a minimum.
Currently, the DTSX1 is being used in heat detection and fire detection applications around the globe. Users in facilities such as distribution warehouses and Lithium-ion battery production and storage facilities have avoided loss of production and late deliveries.
Data recording can be added easily to the solution with Yokogawa’s GA10 data logging software, which gathers the temperature data and enables users to build a data acquisition (DAQ) system without programming.
The DTSX1 conforms to EN54-22 which is the European Standard for Fire Detection and Fire Alarm Systems – Part 22: Resettable line-type heat detectors.
Key Benefits
- Reduced risk of production slowdowns or injuries through successful heat monitoring with no blind spots in the air/fume ducts.
- Lower costs of installation and maintenance thanks to fewer devices and equipment demands.
- Fewer risks to team members as no regular maintenance of the DTSX solution in hard-to-reach places is required.
Industries
-
Chemical
Chemical plants rely on continuous and batch production processes, each posing different requirements for a control system. A continuous process calls for a robust and stable control system that will not fail and cause the shutdown of a production line, whereas the emphasis with a batch process is on having a control system that allows great flexibility in making adjustments to formulas, procedures, and the like. Both kinds of systems need to be managed in available quality history of product, and to be able to execute non-routine operations. With its extensive product portfolio, experienced systems engineers, and global sales and service network, Yokogawa has a solution for every plant process.
-
Mining & Metal
Mining operations produce valuable minerals or geological materials from the Earth. Economical recovery often requires high throughput and high availability of the process with low operation costs, and stringent safety and environmental regulations.
-
Pharmaceutical
Under continual pressure to increase profitability, maintain government compliance, and meet emerging market opportunities, the pharmaceutical manufacturing industry faces unique challenges that require unique solutions. As one of the world’s leading industrial automation suppliers, Yokogawa is poised and prepared to deliver those solutions, creating individualized lean manufacturing techniques that deliver consistent, measurable results.
Related Products & Solutions
-
DTSX1 Fiber Optic Heat Detector
DTSX1 is an all-in-one heat detection solution. It is a self-contained, ready-to-install solution.
-
Distributed Fiber Optic Temperature Sensor
Enhance process visibility and safety with cost-effective measurement solutions.
Have Questions?
Contact a Yokogawa Expert to learn how we can help you solve your challenges.