Flow performance extends cell membrane life with accurate, reliable, and stable performance - saving millions of dollars in membrane repair costs, reducing instrument maintenance costs and production downtime, and production loss.
Chlorine is used as an intermediate chemical in the production of high-demand products such as bleach, acids, and PVC. The chlorine manufacturing process includes many electrolysis cells (figure 1). Water and ultrapure brine flow into the cell and chlorine (Cl2), hydrogen (H2), sodium hydroxide (NaOH), and other solutions flow out.
Separating the electrolysis cell compartments is a delicate cation permeable membrane that is extremely costly to repair or replace. To protect that membrane, the system must be kept in balance by monitoring and adjusting not only the flow rates into and out of the cell but also the pressure at the Cl2 and H2 headers. Without balance or accurate flow control, the membrane can be damaged and downstream operation, product quality, and safety can be jeopardized.
Challenges
Since the electrolysis cell process fluids are highly corrosive, the process pipes around the cell must have no exposed metal. Nonmetal pipes or liners reduce conductivity and allow electrostatic noise to build up. Conventional magnetic flowmeters (magmeters) rely on conductivity to measure flow accurately. The electrostatic noise hampers the magmeter operation, which, in turn, can cause poor balance on either side of the membrane, leading to membrane tears, and require significant expense for membrane repair or replacement.
Another source of poor magmeter operation and membrane risk comes from the corrosion of conventional magmeter electrodes by the process fluids.
Flow measurement difficulties can become so significant that to preserve the membrane from damage, some chlorine manufacturers turn to managing the flow manually.
Solution
Accurate flow measurement from magnetic flowmeters (magmeters) can save customers millions of dollars in membrane repair costs and production loss. Yokogawa’s ADMAG Total Insight (TI) AXG® magmeter offers stable flow measurement and greater reliability to help maintain a healthy environment for the electrolysis cell membrane.
The noise present in the cell’s nonconductive pipes poses no problem for the ADMAG TI magmeter thanks to Yokogawa’s patented dual-frequency excitation method. By combining traditional high and low excitation frequencies, the magmeter offers the benefits of both methods, including ruggedness and high accuracy.
In addition, the ADMAG TI AXG magmeter offers several features that allow it to provide superior corrosion resistance. A spring-loaded electrode design prevents corrosive chemical exposure due to the process material migrating around the electrodes to the coils and the terminal junction box. The PFA liner is injection-molded into the punch plate of the AXG. This helps support the longevity of the flowmeter’s liner by making it more rugged for harsh processes. Together, these features greatly extend the life of the flowmeter, reducing instrument maintenance costs and production downtime.
Key Advantages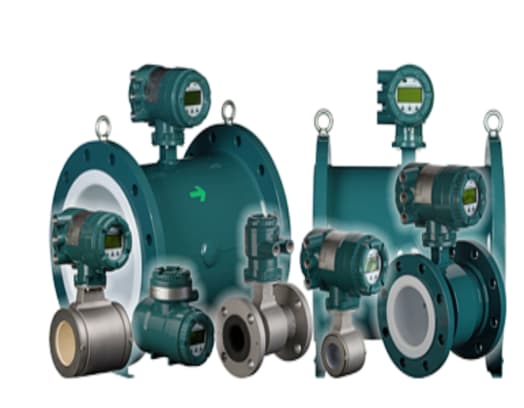
- Avoid costly repairs and prolong the life of electrolysis cells through accurate flow measurement and stable balance of fluids.
- Reduce process upsets through improved noise immunity provided by the dual-frequency excitation.
- Reduce instrument maintenance thanks to the magmeter’s strong resistance to corrosion.
Industries
-
Chemical
Chemical plants rely on continuous and batch production processes, each posing different requirements for a control system. A continuous process calls for a robust and stable control system that will not fail and cause the shutdown of a production line, whereas the emphasis with a batch process is on having a control system that allows great flexibility in making adjustments to formulas, procedures, and the like. Both kinds of systems need to be managed in available quality history of product, and to be able to execute non-routine operations. With its extensive product portfolio, experienced systems engineers, and global sales and service network, Yokogawa has a solution for every plant process.
Related Products & Solutions
-
ADMAG AXG
Magnetic flowmeters for oil & gas, chemical, pulp & paper, food & beverage, and metal & mining applications
-
ADMAG TI - AXG Ethernet Flow Meter with EtherNet/IP Connectivity
- Yokogawa ADMAG TI AXG Flow Meters with EtherNet/IP connectivity
- Industrial applications include pharmaceutical, food/beverage
-
Magnetic Flow Meters
Achieve stable measurement and quick response times.
Have Questions?
Contact a Yokogawa Expert to learn how we can help you solve your challenges.