Industrial artificial intelligence/machine learning (AI/ML) software and long-range sensors predict maintenance requirements across entire enterprises, increasing productivity and profits.
For product manufacturers, profitability requires safely maintaining efficient operation, minimizing expenses, and reaping as much production from plant equipment as possible. When plants are new, efficiency and reliability are not among the highest concerns, but as equipment ages, unanticipated failures and the resulting reactive repairs often become problematic.
Plant personnel can address this issue by accessing equipment data to identify problematic equipment requiring maintenance. The problem is manually analyzing data to generate insights requires a great deal of time, expertise, and operational knowledge. Custom artificial intelligence/machine learning (AI/ML)-enabled software removes most manual data analysis. The problem is this type of software can be cost-prohibitive to implement and maintain.
Off-the-shelf AI/ML software, such as data logging software, deliver automated anomaly detection and alerting, empower personnel to identify equipment issues before failures occur. This software often serves a second purpose as a centralized repository for multiple devices’ data, including data captured by an Industrial Internet of Things (IIoT) long-range wireless sensor system. These types of off-the-shelf AI/ML software solutions increase operational efficiency, prevent equipment problems, and allow plants to plan maintenance prior to equipment failure.
Three development goals for AI-enabled products
An off-the-shelf AI/ML software solution prioritizes achievement of three goals:
- Maintain healthy conditions in equipment: Log all equipment output, including deviations from the baseline.
- Anticipate equipment maintenance via abnormal sign detection: When equipment variables begin to stray from normal values, the software flags this behavior and alerts personnel to take maintenance measures prior to failure.
- Make AI accessible: End users do not need to be AI experts or contract expensive consultants to configure the software as it is usable by personnel of many skill levels.
In the industrial automation space, a complete AI package includes sensors and controllers to gather data, PC-based software to organize and automatically analyze the data using AI/ML, and a recorder to visualize data (Figure 1).
AI/ML software orients personnel to normal operational levels based on past performance and notifies them when an anomaly is detected.
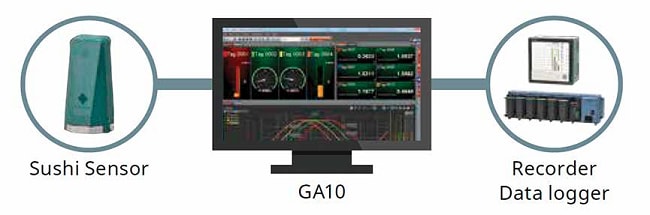
Figure 1: An AI package has a sensor, software to collect and analyze data, and a recorder to visualize data.
Anomaly detection and predictive maintenance
Warning, alerting, and alarming are nothing new by themselves, as control systems often possess user-adjustable high, low, deviation, and out-of-range setpoints. When equipment data exceeds the applicable setpoint, the user is notified.
Automated anomaly detection offers significant improvements beyond these automated functions. When AI-enabled software is first deployed, it undergoes a learning phase during which it monitors the equipment conditions to build a baseline for known, normal operation. Time dedicated to the learning phase varies by application and can be user-defined.
Once the learning phase is complete and a normal operation baseline is established, the AI/ML software begins automatically monitoring the equipment, build reports for personnel review and generate anomaly alerts when operation deviates from its baseline. These alerts provide users advance warning of potential equipment problems.
AI/ML software should offer ease of configuration and user-friendly parameter changes, simplifying these and other types of adjustments. The degree to which current equipment data matches the normal baseline can be given as a health score, signaling advance notice of an abnormality if something is negative (Figure 2).
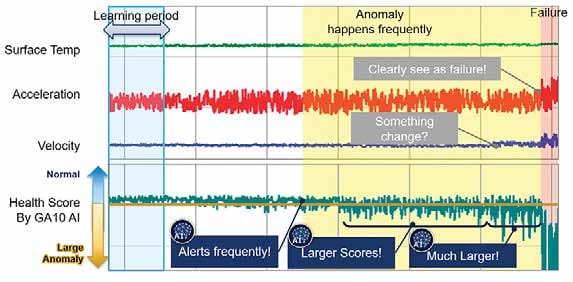
Figure 2: In an example of anomaly detection, an AI/ML software’s health score indicates an abnormality prior to equipment failure.
In addition to identifying abnormalities before equipment failures occur, AI-enabled software is ideal for creating predictive maintenance forecasts. As equipment data deviates from the baseline, AI/ML software shows a declining health score. Maintenance operators can use this indication to determine timelines for scheduled equipment maintenance prior to potential failure. These automated visual insights free up time for tasks besides data analysis and maintenance scheduling.
AI-enabled software functions
Many software suites can wrangle data from multiple devices and measurement points on a network into one location, allowing users to visualize the data using graphs and charts. However, data visualization alone does not inform on the normalcy of the data being viewed. To deal with this problem, AI/ML software employs algorithms that automatically overlay trends and highlight anomalies on the graphical user interface.
With certain types of equipment data, such as temperature or pressure, it is often possible, if not always ideal, to use classical methods of high or low-limit setpoint warnings to detect an abnormality. However, for data such as motor speed or the vibration of a machine, it is difficult to understand if the equipment data is normal without manual and meticulous historical data analysis. This manual analysis is time-consuming and requires a skilled data analyst with extensive expertise, but these experts are in short supply. AI-enabled software transforms this tedious manual process into instant automated insight, comprehensible by all staff (Figure 3).
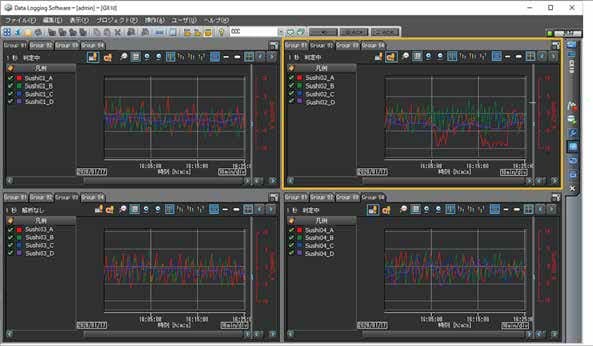
Figure 3: AI/ML software highlights an anomaly screen at upper right with an orange outline.
AI/ML software uses a clustering algorithm to detect anomalies. This means anomaly detection is not limited to data following linear, quadratic, or other basic functions. Advanced AI-enabled software creates correlations among multiple equipment data points when it determines a normal baseline and detects when the relationships are abnormal during operation.
Automatic anomaly detection frees personnel from manual analysis, and it often detects problems missed by data examined using visualization tools such as charts and graphs. This typically results in increased uptime and lower maintenance costs.
Long-range sensors improve data collection capabilities
In the age of IIoT, it is not practical to limit data collection to stationary and accessible processes and areas. Applications like mobile machines and vehicles, rural outpost facilities, and lengthy pipelines generate data worth gathering and analyzing but also present obstacles regarding non-stationary, long-range, and low-power data transmission. Low power-wide area network (LPWAN) systems address these and other issues and are being used across many enterprises to capture data in difficult applications.
A few noteworthy characteristics of LPWAN sensors are:
• They consume minimal power, hence batteries can last several years
• They provide long-range wireless data transmission, capable of transmitting data over several miles
• Highly efficient communication protocols, resulting in lower data usage requirements than 3G, 4G, and 5G.
Each sensor measures vibration, temperature, or pressure, delivering monitoring capabilities for equipment located just about anywhere (Figure 4). A long-range wide-area network (LoRaWAN, a subcategory of LPWAN) enables a connected enterprise without the necessary provisions for wired lines or IEEE 802.11 Wi-Fi.
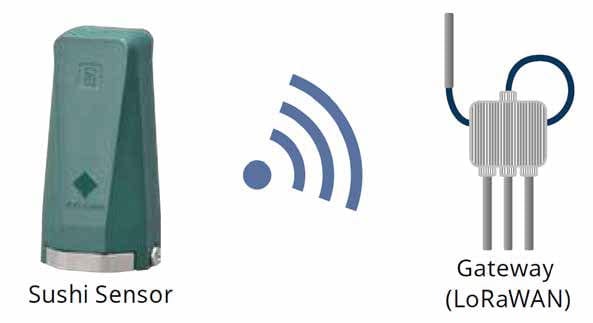
Figure 4: Yokogawa’s long-range Sushi Sensor system can transmit equipment data wirelessly over long distances to a LoRaWAN gateway.
Data transmitted by the sensors can be supplied to host systems, including AI-enabled software. By using the wireless sensors in conjunction with AI anomaly detection software, plant personnel receive a clear window into the operational health and maintenance needs of equipment, no matter where it is located (Figure 5).
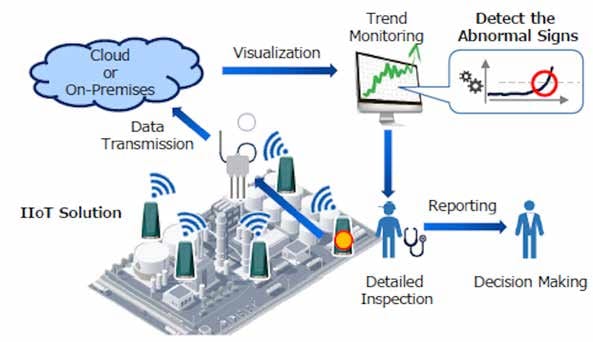
Figure 5: This system uses the LoRaWAN communication protocol to wirelessly transmit data
to a central source from equipment located almost anywhere.
AI-enabled software capability can add years to an asset’s life, avoiding failures and costly repair or replacement.
Detecting anomalies
Detecting an anomaly does not guarantee a failure will occur, but it is almost always of interest to plant personnel. If anomalies were easily spotted or could be produced on demand, there would be no need for AI anomaly detection. However, it is often difficult to produce and acquire abnormal data to create a manual reference point for identification. This challenge is addressed by AI.
After recording equipment conditions during its learning phase, AI-enabled software can detect the slightest anomalies, even if the software has never been exposed to abnormal data in the past. Maintenance personnel can identify which equipment requires maintenance or inspection from the detected anomalies.
Although anomaly detection is already a helpful tool for plant personnel, AI/ML software feature development continues. Rather than only identifying anomalies, the goal is to develop AI-driven control to prevent them from occurring in the first place.
AI as an alternative to equipment replacements
As plants age, equipment becomes less efficient and reliable. At some point, maintenance and repair may become too costly and time-consuming, and equipment replacement may be necessary. This may be the best course of action in some situations, but AI/ML software can reduce maintenance costs to tenable levels.
Using AI-enabled software for analysis and anomaly alerting — in conjunction with reliable, adaptable wired and wireless sensors – extends equipment life, reduces maintenance costs, and increases uptime. Off-the-shelf AI/ML software is a cost-effective solution to provide quick insights into the sources of plant inefficiencies and failures. This capability can add years to an asset’s life by predicting problems and allowing planned minor maintenance prior to complete equipment failure and costly repair or replacement.
Takayuki Sugizaki is an IoT wireless promotion manager at Yokogawa Electric Corporation. He works in the Technical Consulting Section of the CX Strategy Department, specializing in industrial automation products and services. Sugizaki has been with Yokogawa for 18 years and carries 35 years of experience in the electronics industry. He holds a bachelor’s degree in electronic engineering from Shinshu University.
Related Products & Solutions
-
AI Product Solutions
Optimize predictive detection and future prediction with intuitive AI products
-
Data Logging Software GA10
The latest software that enables you to build a DAQ system without programming. Designed for maximum compatibility with Yokogawa recorders, data loggers, temperature controllers, and power monitors, GA10 can also acquire data via Modbus communications.
-
Chart Recorders
- Yokogawa strip chart recorders
- Trend electrical or mechanical signals onto paper
- World-class performance and reliability
-
Sushi Sensor
Optimize processes with a range of wireless measurement and diagnostic solutions.
Have Questions?
Contact a Yokogawa Expert to learn how we can help you solve your challenges.