About the SINOPEC-SABIC Joint Venture and the Tianjin Projects
SINOPEC SABIC Tianjin Petrochemical Co., Ltd.,
Tianjin, China
SINOPEC SABIC Tianjin Petrochemical Co., Ltd. (SSTPC), a 50/50 joint venture between Saudi Basic Industries Corporation (SABIC) and China Petroleum & Chemical Corporation (Sinopec), has constructed a huge, integrated refinery and petrochemical complex in Tianjin, China. The petrochemical facility at this complex was built at a total cost of 18.3 billion RMB (US$2.7 billion) and has an annual capacity of 1.0 million tons ethylene and the remainder is downstream products such as polyethylene, ethylene glycol, polypropylene, butadiene, phenol, and butene*.
The ethylene cracker, eight downstream units, and all associated utilities took just 27 months to build and began commercial production in May 2010 after a three month pilot operation phase during which ethylene production capacity was ramped up to the present annual capacity of 1.0 million tons. The refinery initially had a production capacity of 5.0 million tons, but this was soon increased to the present 15.0 million tons.
In addition to expanding local production, the complex will upgrade the chlorine-alkaline industry in Tianjin and promote economic development of the New Binhai District and Tianjin municipality. Initial estimates indicate this will support an annual GDP increase of more than four percent in Tianjin and trigger investment of an additional 100 billion RMB (US$14.8 billion) in downstream and associated industries.
*Capacities for other downstream products produced at the Tianjin petrochemical facility: Gasoline hydrogenation: 650,000 tons, LLDPE: 300,000 tons, HDPE: 300,000 tons (INEOS Innovene S process), PP: 450,000 tons (LyondellBasell Spherizone PP), EOEG: 420,000 tons (Dow technology), Phenol: 350,000 tons, butadiene, 200,000 tons, MTBE: 120,000 tons, butane: 50,000 tons
The Challenges and the Solutions
SSTPC wanted to achieve a major increase in production capacity through the construction of large-scale and fully integrated oil refining and petrochemical production facilities. The company was looking to achieve specific cost, safety, and environmental protection targets, and required a partner with high quality project execution capabilities. To accomplish these objectives and meet these challenges, SSTPC turned to Yokogawa. As the main automation vendor for the refinery and petrochemical facility projects, Yokogawa successfully installed CENTUM CS 3000 production control systems, Exaquantum plant information management systems, Plant Resource Manager (PRM) packages, and over 40,000 HART field devices, including Yokogawa EJA transmitters and valves. In this undertaking, Yokogawa engineers were involved from the very early project stages and worked closely with their counterparts at the Sinopec Engineering Institute (SEI) and 10 engineering companies.
A closer look at some of the product solutions provided by Yokogawa follows.
1. Process data management is a key issue in the petrochemical complex because plant efficiency needs to be continuously monitored to prevent the occurrence of major problems that can lead to costly plant shutdowns. Once a shutdown occurs, a lot of work and energy must be expended to start it up again. Yokogawa's Exaquantum helps to prevent this by providing a window into the various processes at this huge complex by continuously analyzing their data.
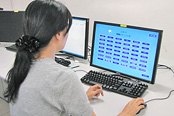
Exaquantum for monitoring plant efficiency
2. Maintenance of thousands of HART devices throughout the refinery and petrochemical facilities would be very time consuming if field operators had to check them one at a time. With Yokogawa's PRM package, operators can determine at a glance whether field devices from Yokogawa and other vendors are in good working order. This allows a much more efficient proactive maintenance approach that results in significant savings in maintenance costs.
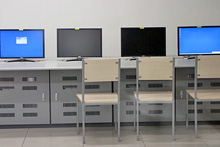
PRM for proactive maintenance
3.For more efficient engineering work, CENTUM CS 3000 engineering stations and other vendor's engineering stations are all together located in this room. On-Line maintenance capability of CS 3000 is very much appreciated by SSTPC engineering department.
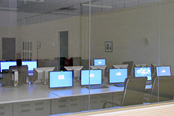
Plant wide engineering room
4. Process engineers are always looking for the best control strategy to improve production efficiency and product quality. They need to confirm the current process situation and identify whether a new strategy can achieve the desired improvements. SSTPC engineers do this in the second floor system room.
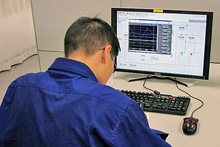
Optimizing production
The central control room for petrochemical plants
Customer Satisfaction
Zhang Senlin, Vice Deputy Director of the Equipment Managing Department, said, "We are very much satisfactory that this huge refinery and petrochemical complex has been running very smoothly without any major problems since January 2010. We appreciate Yokogawa's project members working together as "One Team." We completed all configuration based on the same standard specifications and procedures. And we appreciate the easy configuration of the CENTUM CS 3000 system and its high reliability. It will bring huge savings in maintenance of the entire system."
Przemysł
-
Przemysł chemiczny
Chemical plants rely on continuous and batch production processes, each posing different requirements for a control system. A continuous process calls for a robust and stable control system that will not fail and cause the shutdown of a production line, whereas the emphasis with a batch process is on having a control system that allows great flexibility in making adjustments to formulas, procedures, and the like. Both kinds of systems need to be managed in available quality history of product, and to be able to execute non-routine operations. With its extensive product portfolio, experienced systems engineers, and global sales and service network, Yokogawa has a solution for every plant process.
-
Przemysł petrochemiczny
Petrochemical companies’ needs are extremely diverse. To come out ahead in today’s highly competitive marketplace, producers are striving to improve quality and productivity. Yokogawa provides tailor-made solutions for these needs based on its long and wide-ranging experience in this field.
Powiązane produkty i rozwiązania
-
Plant Information Management System (Exaquantum)
Exaquantum can acquire data from all facets of a process and transform that data into easily usable, high-value, widely distributed information.
-
Plant Resource Manager (PRM)
Have the facility managed properly for high-reliable and stable plant operation? PRM contributes to improving the quality of maintenance plans and optimizing maintenance costs throughout the plant life cycle.
-
Distributed Control System (DCS)
Our distributed control system (DCS) enables automation and control of industrial processes and enhanced business performance. Over 30,000 systems entrust Yokogawa DCS to deliver their production goals.