Plant Information
18V34SG Gas Engine of Wärstilä Corporation
Combined heat & power (CHP) plant
3 Wärstilä gas engines (3 X 6 MWe, 16.5 MWt)
3 hot water boilers
Executive Summary
The Füredi Power Plant project is a showcase for the use of SCADA and STARDOM in a power sector application, and it posed certain unique operation and control requirements. A FAST/TOOLS SCADA system was seamlessly integrated with a STARDOM automation system, providing the information needed by power plant managers, operators, and maintenance personnel to efficiently monitor the plant's operation and analyze its performance. A history database integrated into FAST/TOOLS collects and stores the measured and calculated parameters.
The system covers approximately 16,000 items, collects data, creates shift/daily/weekly reports, and makes monthly calculations. The collected and calculated data is kept for the lifetime of the plant. Through this project, Zugló-Therm Energy Supply Ltd. has achieved the following:
- Easy set point definition for all plant power generation operations
The heat produced by the entire plant and the electrical set points for the engines can be defined in an Excel file every 24 hours, with 15 minute resolution, and this data can be easily exported into the FAST/TOOLS system. - Stable electric power generation
The superior control system can respond flexibly to changing heat demand, focusing on the operational conditions of the gas engines. - Power plant optimization
The control system supports on-line calculation of both plant and gas engine efficiency, enabling adjustments for optimal operation. - Control of electric power generation based on net performance
The control application in STARDOM can automatically calculate the in-house power consumption of the power plant. With this function, the plant can more accurately control the required amount of power to be supplied to the national grid operator.
About the Project
The plant is located at Füredi út in Budapest. The main contractor is Kraftszer Kft., a Hungarian engineering company that has built a number of CHP plants, and the plant will be operated by Zugló-Therm Energiaszolgáltató Kft.
The Füredi power plant consists of three (3) Wärstilä 18V34SG gas engines rated for an electrical output of 18 MWe, three (3) heat exchangers for each engine that supply the hot water for the district heating system, and auxiliary systems for such functions as fuel and air supply. Natural gas is the main fuel for the power plant.
The hot water is distributed by Fötáv Rt., the main district heating utility in Budapest.
Although the emphasis is on the supply of hot water for district heating, the generated electricity is also supplied to approximately 20,000 households on the public power grid. In Hungary this kind of CHP plant is required to have a minimum total efficiency of 65% per month and 75% per year.
The Challenges and the Solutions
1. Easy set point definition for all plant power generation operations
The district heating set points are defined in Excel and sent to the district heating company. As shown below, the Excel data can be imported into FAST/TOOLS with just one mouse click. Plant operators can see the actual daily plant set points on screen.
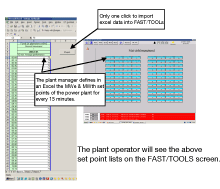
FAST/TOOLS screen
This system is used for the electrical set points as well. In this case the plant manager has to define the set points for each of the three gas engines. Please refer to the Excel sheet below.
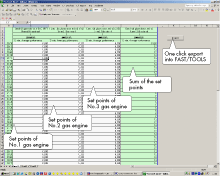
Excel sheet
2. Stable electric power generation
The automation system realized in STARDOM can also recalculate the a.m. set points for each gas engine in the event of a malfunction such as a trip of a gas engine. If one of the gas engines shuts down, the other two gas engines will increase power output to compensate.
3. Power plant optimization
STARDOM calculates the efficiency factors for each gas engine and for the entire power plant, and provides data that operators can use to make the plant operate economically and efficiently.
Scope/Special Features of the Control System
Three fully redundant STARDOM field control node (FCN) stations control different parts of the plant, including the electrical system, district heating system (including the gas engines connected to the PLCs), and air system.
Redundancy is realized at different levels in the FCN controllers such as the power supply, CPU, communications between the nodes, and I/Os. One of the most important criteria is the 10 msec time stamping of electrical signals.
The STARDOM controllers manage the plant's measuring and supervisory control activities, governing approximately 550 hardwired I/Os. Via serial communication lines (MODBUS, IEC-103), they collect an additional 500 signals; 1500 signals are connected through redundant OPC interfaces.
System Details
Control system: | STARDOM FCN and FAST/TOOLS SCADA system |
---|---|
Number of I/O points: | 2500 |
Field instruments: | EJA530A x 9, EJA110A x 13, EJA120 x 2, YTA70 x 2, non-Yokogawa products x 116, manometers x 100 |
Installation: | March 15, 2005 |
Start-up: | April 4, 2005 |
Commissioning: | April 20, 2005 |
Training: | May 15-16, 2006 |
Endüstriler
-
Combined Cycle
The combined cycle power plant is being installed in increasing numbers around the world where there are substantial supplies of natural gas.
-
Power
In the mid 1970s, Yokogawa entered the power business with the release of the EBS Electric Control System. Since then, Yokogawa has steadfastly continued with the development of our technologies and capabilities for providing the best services and solutions to our customers worldwide.
Yokogawa has operated the global power solutions network to play a more active role in the dynamic global power market. This has allowed closer teamwork within Yokogawa, bringing together our global resources and industry know-how. Yokogawa's power industry experts work together to bring each customer the solution that best suits their sophisticated requirements.
ilgili Ürünler & Çözümler
-
FAST/TOOLS
Originating as the Flexible Advanced System Techniques (FAST) project, FAST/TOOLS today is a comprehensive, fully-integrated SCADA application suite. Powerful and flexible, FAST/TOOLS serves installations ranging from 50-point unit processes to multimillion-point offshore production and pipeline systems that extend over thousands of miles.
-
Process Control PLC/RTU
From process plants to remote locations, our process control PLC and Remote Terminal Unit (RTU) help users maximize operational excellence.