Top Gas Density Measurements
Plant Name: Liquefied Petroleum Gas Producer
Industry: Refining
Introduction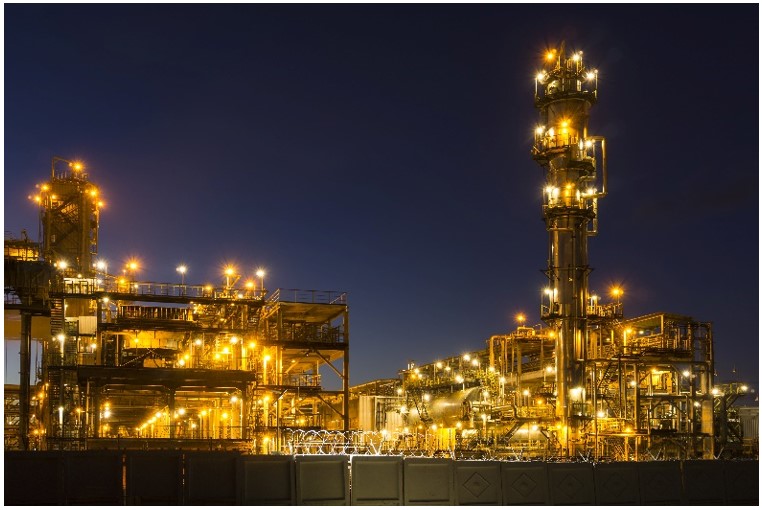
U.S. refineries represent approximately 23 percent of the world's petroleum production, and the United States has the largest refining capacity in the world. Petroleum refining is undergoing intense scrutiny in the United States from regulatory agencies and environmental groups. As a result, releases of pollutants caused by corrosion leaks are becoming high consequence events. Clean air legislation has forced refiners to implement several costly measures to reduce impacts on the environment, both with the types of products they produce and how they operate their refineries.
An oil refinery is an industrial process plant where crude oil is processed and refined into petroleum products such as gasoline, diesel fuel, asphalt base, heating oil, kerosene, and liquefied petroleum gas (LPG). The measurement of hydrogen purity throughout a system allows for efficient control of the process. The “top gas” generated at the top of the distillation column in a petroleum refinery’s fluid catalytic cracker (FCC) is used to produce gasoline and LPG. The composition of the top gas varies with the running conditions of the FCC. The composition of the crude oil and its density (molecular weight) must be constantly monitored and measured.
Process
An atmospheric distillation column or reduced-pressure distillation column refines crude oil into gasoline, kerosene, and lubricating oil in the petroleum refining system. In addition, the petroleum refining system incorporates an FCC to distill high-octane gasoline and LPG from the heavy contents of the crude oil. In many refineries, the FCC serves as the primary unit, converting or cracking low-value, heavy crude oil into a variety of higher value, light products. In the U.S., the primary function of the FCC is to produce gasoline. Modern FCC units can process wide varieties of feedstock. They can adjust operating conditions to maximize the production of gasoline, middle distillate olefins, or light olefins to meet different market demands.
The top gas generated in the fraction column of the FCC passes through a heat exchanger and is then pumped to high pressure. The resulting gas content is transferred to the LPG recovery system and the liquid content to the gasoline generation system. In this process, it is crucial to measure the density (specific gravity) of the gas because the data is essential as a critical parameter in controlling the operation of the FCC. In addition to being used to monitor the system and the quality of the product, this measurement can also help prevent pump pressure surges.
Typical process conditions
- Measurement point: Outlet of the top fraction column in the FCC
- Area Classification: Class I Division 1
- Temperature: 34ºC
- Pressure: 75 kPa to 180 kPa
- Humidity: Wet
- Gas Composition: O2, N2, CO, H2, H2S, C1 to C5
- Dust: None
- Measurement Range: 1,600 to 1,800 kg/Nm3
Yokogawa has introduced the GD402 Gas Density Analyzer for this explosion-protected application. It features an intrinsically safe, explosion-proof design, with fast response, dust-proof, anti-corrosive, and flame-proof construction. The GD402 will ensure stable and rapid measurement of gas density under hazardous conditions. It can display specific gravity and molecular weight readings derived from the density data, and it will significantly reduce the workload by ensuring continuous and accurate measurement.
Challenges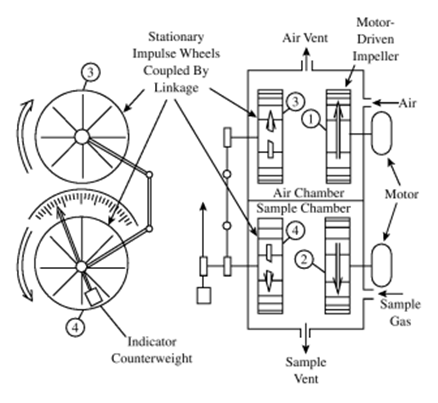
A traditional method used to measure specific gravity is the fan differential analyzer, also known as a kinetic energy or viscous drag type analyzer. This analyzer has two chambers, an air chamber used as a reference and a sample chamber for the measured gas.
Each chamber has a motor-driven impeller that draws the appropriate gas into it. Each gas comes into contact with a stationary impulse wheel and is then vented out of the analyzer. The impulse wheels are linked to each other, and the torques created on the wheels are in opposite directions. The magnitude of the torque is dependent on the specific gravity of the gas.
This design is purely a mechanical means to determine if the sample gas is lighter or heavier than the reference air. This method has many moving parts that are subject to wear. There are motors, impellers, impulse wheels, and linkages. Calibrations are required to compensate for this wear, or a drifting measurement error will occur. This method also consumes reference air with the same pressure and humidity level as the measured gas.
It also does not take a lot of imagination to understand how a dirty sample containing particulates or oil will affect the accuracy of this method.
Solution
Yokogawa’s GD40 Gas Density Detector and GD402 Gas Density Analyzer continuously measure gas density and other valuable parameters, including specific gravity and percent concentration. Yokogawa’s family of gas density products delivers superior performance and reliability in applications where accurate, repeatable gas density measurement is essential. Yokogawa’s gas density analyzers provide accurate measurements with simplified maintenance and operability for applications such as fuel blending, product quality, hydrogen purity, and replacement in utility turbines.
Key Advantages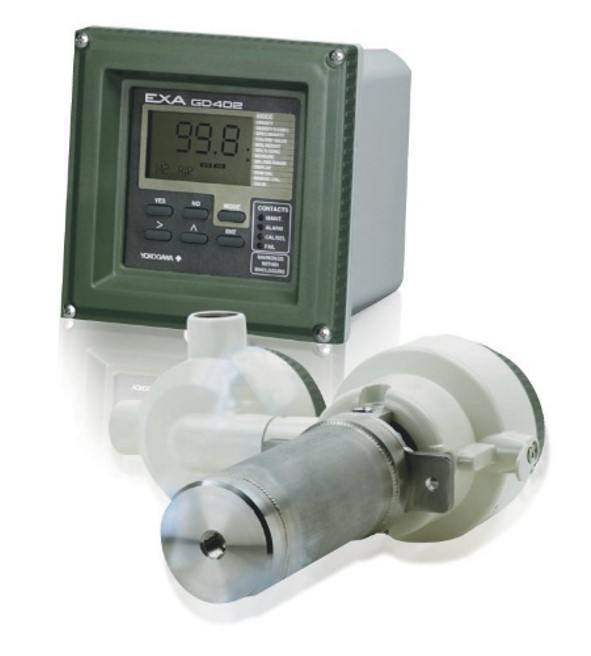
- Ensures stable and rapid measurement of gas density under hazardous conditions.
- Capable of displaying specific gravity and molecular weight readings derived from the density data.
- Significantly reduces the workload by ensuring continuous and accurate measurement.
- Enables improved operation efficiency and plant safety, plus continuous highly responsive and sensitive measurements of gas density, and several other valuable parameters, including specific gravity and molecular weight.
- Two-wire connections between the detector and converter minimize installation costs.
- Only routine maintenance is required, for example, once per three months, depending on the application.
- Allows local configuration via the front panel or remotely by using the (optional) “Brain” terminal.
Industries
-
Oil & Gas Downstream
The oil & gas downstream industry has been facing an increasing number of challenges in recent years. These include the changing characteristics of the feedstock to be processed, aging of process facilities and equipment, rising cost of energy, lack of skilled plant operators who can run a refinery safely and efficiently, and the ever-changing requirements from both the market and the customer.
Over the years, Yokogawa has partnered with many downstream companies to provide industrial solutions focused on solving these challenges and problems. Yokogawa's VigilantPlant solutions have helped plant owners to achieve maximum profitability and sustainable safety within their plants.
Have Questions?
Contact a Yokogawa Expert to learn how we can help you solve your challenges.