Background
Removal of free oil and grease from a wastewater stream reduces the potential for equipment problems downstream.
Three forms of oil are encountered in wastewater treatment at a refinery:
Free oil, also known as floating oil, is removed by either skimming the surface in a skim tank or by gravity separation in an API separator.
Emulsified oil is composed of oil droplets in stable suspension within the wastewater. Removal requires chemical addition to reduce the pH followed by the addition of dissolved oxygen or nitrogen to remove the emulsified oils as they break free from the wastewater.
Dissolved oil is a true molecular solution within the water and can only be removed by biological treatment.
Figure 1 is a typical biological wastewater treatment schematic; however, other treatment options exist, as well. Biological treatment systems are commonly used for “normal” industrial oily wastewater streams, and can also be used to treat sanitary waste. A disadvantage is a difficulty in sustaining the biomass environment due to high swings in wastewater concentrations, total dissolved solids (TDS), and temperature.
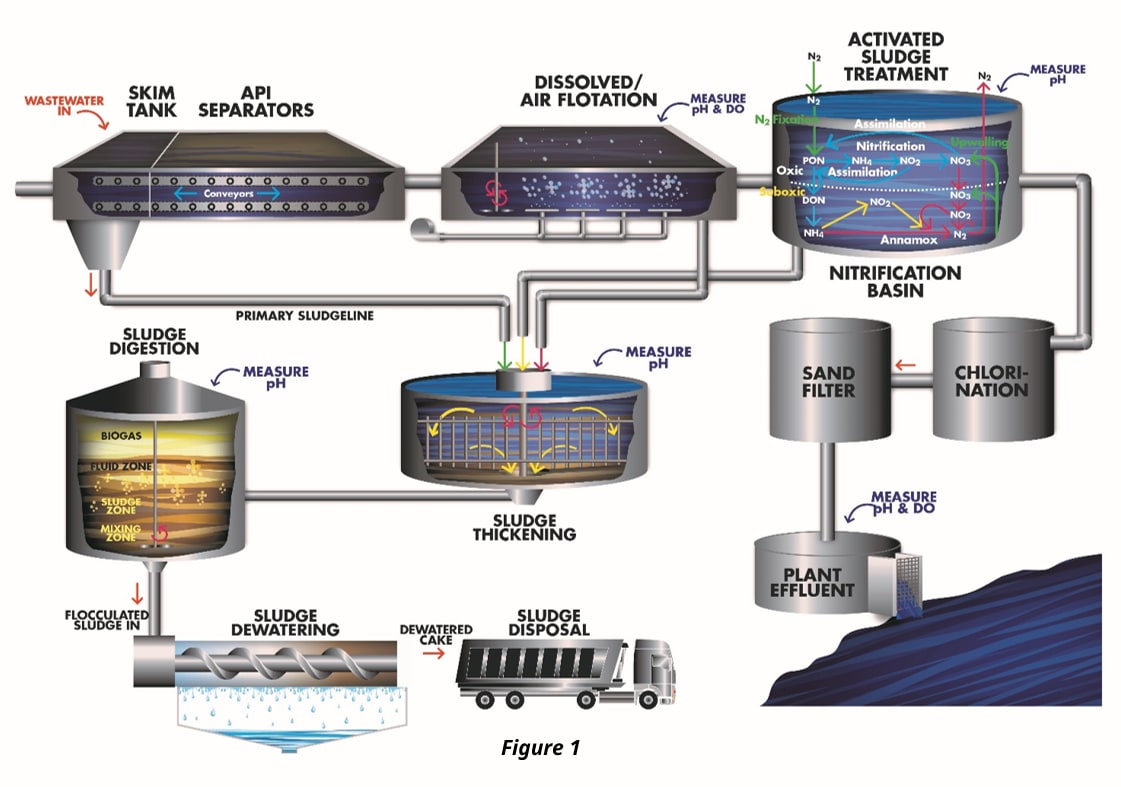
Introduction
API Separators: American Petroleum Institute (API) separators are normally the first and most important step in wastewater treatment at a refinery. It uses the differences in specific gravity between oil and water to filter out the majority of free oil within the mixture. The lighter oils will remain at the top of the liquid and can be skimmed off, while the heavier oil will settle to the bottom.
Figure 2 shows a detailed drawing of a typical API separator. A conventional oil-water separator contains a conveyor to assist in the separation of the heavier oils and grease, a scraper/skimmer, and a baffle.
pH is typically measured at the outlet as an indication of potential problems such as flocculation in the secondary treatment. It is important to note that because emulsified oil is still present in the water mixture, the coating will occur and result in a sluggish reading.
At this point in the treatment process, the emulsified oil is still insoluble. The removal of the emulsified oil requires either a chemical addition to reduce the pH or use of emulsion breakers.
Dissolved/Air Flotation: Once treated, the wastewater often enters an air flotation unit to remove the emulsified oil as it begins to break free from the wastewater, using dissolved oxygen or nitrogen.
Bioreactors or Activated sludge treatment (see Figure 3): In this phase, the wastewater still contains dissolved oil in true molecular form. The only way to remove the remaining dissolved oil is through biological treatment. This and the remaining steps are the same as those in a typical wastewater treatment facility.
Process components such as biomass blends, air, return activated sludge (RAS), waste activated sludge (WAS), and throughput must be in balance to obtain complete synergy. It is essential to monitor and control all factors that influence the efficiency of the biological conditions in the basin, for example:
Temperature: Most biomass achieves optimum efficiency in a temperature range between 10-40°C. Increasing or decreasing the temperature can result in increasing or decreasing the rate at which the organisms consume and reproduce. All chemical reactions taking place are also affected by the process temperature.
pH: For most systems, the pH should be kept between 6.5 to 8.5. When the pH is too high or too low, the biomass loses the ability to convert the food to energy and raw materials. Since a pH below 6.5 can cause the growth of fungi, fungal bulking will require adjustment using a caustic, lime or magnesium hydroxide.
Low Nutrients: If nitrogen and phosphorus are not present in sufficient amounts, it can limit the growth rate of the biomass. A sign of nutrient deficiency is foam on the aeration basin.
Dissolved Oxygen (DO): DO is a critical measurement and will be maintained between 1-3 mg/L. The concentration is an indication of the basin environment; whether it is in denitrification (excess nitrate, NO3) or nitrification (excess ammonia, NH4) environment. Essentially, the DO measurement is used to minimize ammonia breakthrough. It is not uncommon to see NH4 and DO measurements together.
Septicity/Toxicity: Septic wastes contain elevated amounts of sulfides and organic acids (such as acetic acid). Other organic materials and heavy metals are also toxic to biomass. They reduce their efficiency or can even destroy them.
Summary
Maintaining proper pH measurements upstream and decrease problems seen downstream.
Product Recommendations
pH Measurement System
Process Liquid Analyzer:
2-wire 24VDC Loop Power FLXA202 Analyzer
4-wire AC or DC FLXA402 Analyzer
Sensor Selection:
FU20/FU24 wide-body four-in-one pH sensor.
Analog and Digital SMART sensors are available. Analog options allow users to interface with a system that has been used historically. SENCOM technology, allows sensors to transmit and receive data when connected to a transmitter/analyzer or any PC. The SMART digital sensors maintain specific measurement and calibration data on an integrated chip in the sensor; providing easy plug and play solutions. Management software optimizes the performance of sensors for enhanced reliability and process safety
Holders:
PB30 Floating Ball, when using S200256L8 adapter
Dissolved Oxygen Measurement System
Process Liquid Analyzer:
2-wire 24VDC Loop Power FLXA202 Analyzer
4-wire AC or DC FLXA402 Analyzer
Sensor Selection:
Option #1:
DO30G Galvanic Sensor
Holders:
PB350G Angle Floating Ball
FD30 Immersion Fitting
Option #2:
DO70G Optical DO Sensor
Hamilton VisiFerm Optical DO Sensor
*Please note that an external 24 VDC power supply, like the Yokogawa DOX10, must be used with the sensor.
Holders:
PB350G Angle Floating Ball *Available as special*
FD40 Immersion with K1523JA adapter
Note: For additional information on this application contact the local Yokogawa Process Liquid Analyzer Department
Industries
-
Water & Wastewater
All water, regardless of its source, has value. However, with water resources being finite, a focus on "One Water" is necessary to maximize every drop within the water system, ensuring a stable supply of clean and safe water. As we consider current and future needs, planning and implementation are critical for long-term resilience and reliability, meeting both community and ecosystem demands. Yokogawa believes water is a human right for all. Thus, contributing to a sustainable water cycle is one of our Sustainable Development Goals (SDGs).
Related Products & Solutions
-
2-Wire Transmitter/Analyzer FLXA202
- FLEXA™ series analyzers FLXA202
- Continuous on-line industrial measurements
- Most flexible two-wire analyzer available
-
2-Wire Transmitter/Analyzer FLXA21
The FLEXA™ series analyzers are used for continuous on-line measurements in industrial installations. With an option for single or dual sensor measurement, they are the most flexible two-wire analyzer available.
-
All-in-One pH/ORP Sensor Series FU20 and FU24
The FU20 and FU24, all-in-one pH and ORP, sensors show how Yokogawa applies the motto "Simple is best" to sensor technology.
-
Digital SMART SENCOM™ Adapter, SA11
Reusable SMART adapter, requiring only the analog sensor to be disposed of when it reaches the end of its lifetime. With the SENCOM 4.0 platform, Yokogawa delivers reduced costs and waste while contributing to its long-term business goals of a sustainable future for all.
-
Measuring Sensor DO30G
The DO30G sensor for dissolved oxygen is designed for use in water treatment plants such as sewage treatment works, effluent activated sludge process, and potable water treatment. It is also effective in river monitoring, intake protection, fish farming, and other fields where water quality is important.
-
Multi Channel 4-Wire Analyzer FLXA402
The FLEXA™ series analyzers are modular-designed analyzers used for continuous online measurements in industrial installations. They offer single or multi-sensor measurement.
-
Dissolved Oxygen Sensors
- Dissolved Oxygen (DO) sensors/electrodes
- Polarographic, galvanic, optical measurement
- Floating ball, retractable, flow thru, immersion, direct insertion installation
-
SENCOM™ SMART Digital Sensors
- SENCOM™ SMART Digital Sensors
- Maintain specific measurement/calibration data on integrated chip
- Data exchanged between sensor and process transmitter or PC using data management software like SPS24
Have Questions?
Contact a Yokogawa Expert to learn how we can help you solve your challenges.