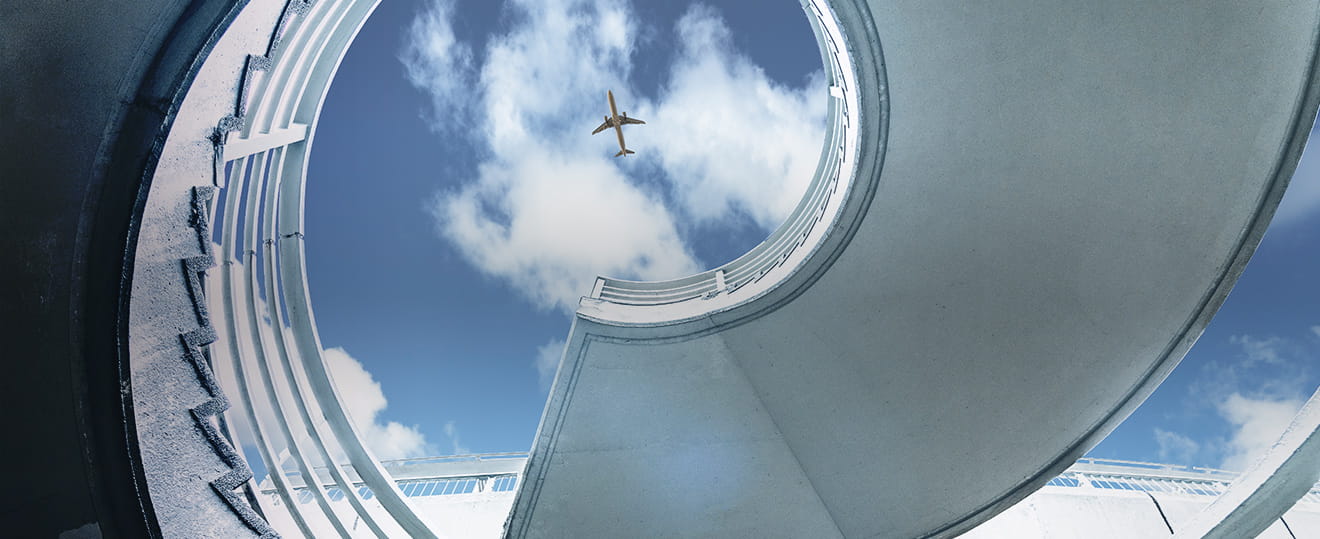
From Automation to Autonomy: The Next Iteration of Industry
The automation of manufacturing has come a long way in a relatively short time. While its conceptual origins can be traced back hundreds of years, the most significant practical evolution has occurred since Ford Motor Company’s introduction of the assembly line in 1913. Fast-forward one century, and robots have gone from science fiction to commonplace application in industrial environments. And now we stand on the cusp of a new era—one in which machines will be able to execute complex control functions that have not been pre-programmed, and without being directly operated by humans. What does the future that industrial autonomy will enable look like? What benefits can we expect to enjoy?
Make No Mistake—Human Fallibility is a Formidable Obstacle
― Despite decades of technological innovation in the manufacturing industry, human error remains the most common cause of industrial accidents
The environment surrounding companies changes daily, increasing in uncertainty and complexity. Companies that fail to detect these changes well in advance, and fail to analyze the potential impact and fortify their resilience to risk accordingly, become unable to fulfill their social responsibilities. Corporate coexistence with society and contribution to making it sustainable are crucial to a company’s success.
More than any other single industry, the manufacturing sector is under the greatest pressure. Failure to ensure proper plant operation can lead to serious accidents, so manufacturers are pulling out all the stops to ensure safety in workplaces and compliance with regulations governing environmental preservation. The practice of health, safety, and environment (HSE) management has become essential to maintaining and enhancing corporate value.
According to a 2017 study by British market research firm Vanson Bourne that targeted hundreds of companies in the US and Europe, including manufacturers, 23% of incidents of unplanned downtime in manufacturing were the result of human error. And, given the aging of workers in the industry, the incidence of major accidents related to human error will likely become more frequent. Global Energy Talent Index Report 2019, a study targeting people in the oil and gas industry in 162 countries, revealed that 43% of industry personnel are aged 45 or older. When those surveyed were asked when they believed this skills crisis—also referred to as the Great Crew Change—would impact oil and gas, 40% of respondents said that the effects were already being felt.
In the manufacturing industry, targets for measurement and management are varied and include facilities, equipment, and devices. Work processes have become increasingly intricate, and there are usually numerous organizations involved. And companies must overcome personnel and other limitations to ensure the preservation and maintenance of their facilities in optimum condition over their long life cycles.
“When the industrial revolution happened there was the Luddistic movement, and there was a fear that machinery would replace all the labor. Whenever we had a technological revolution we had this fear. So if you look backwards, these fears were not justified, and I think they were driven by our very human inability to visualize what new jobs will be created by this new technology.”
Branko Milanovic, economist; excerpt from Gawker interview (June 3, 2016)
Manufacturers are working to make facility management smarter using state-of-the-art digital technologies such as IIoT, AI, and big data, toward mitigating risk to the maximum extent possible and achieving optimal operation. This will lead not only to improved operation, but to enhanced work efficiency and the optimization of utilities.
Companies are looking to increase manufacturing process efficiency, and are taking another look at the roles of humans and machines in these processes. To minimize both the risk of human error and costs, they are attempting to eliminate the human element from certain tasks. Installing sensors, for instance, would enable the remote monitoring of status at all facilities. And the use of the facility management data collected would contribute to improving both efficiency and productivity.
To accelerate business strategy implementation, companies are utilizing digital technology in information sharing and collaboration, with data analysis driving their decision-making processes. This leads to production optimization and partial autonomous operation. Some of the companies working toward digital transformation have introduced autonomous devices and equipment.
A key in determining the future of the manufacturing industry will be the establishment of a new definition for the human-machine relationship. Can they eventually work cooperatively, creating a new synergistic effect that benefits industry and society?
Choose the Right Partner for the Journey to Industrial Autonomy
― Yokogawa’s unrivaled breadth of technological experience, expertise, and vision will help ensure a smoother IA2IA transition
Yokogawa believes that the transition from IA2IA—industrial automation to industrial autonomy—is already underway. But it won’t happen overnight. The key to a successful evolution will be to proceed in a linear fashion, one step at a time. Business processes and structure will have to be innovated, and a successful digital transformation must already be in the rearview mirror. Consults with numerous customers reveal that expectations are extremely high. Yokogawa, based on the customer’s desired direction, has determined its own course of action, manifested in the form of a roadmap to the realization of IA2IA. In tandem with its customers, Yokogawa is working to accelerate this transformation. It is also considering offering value to customers in the form of industrial autonomy-based business opportunities and business model creation.
Companies that have set a course for complete autonomy will allocate resources to it when they determine it to be the best investment. They will identify the processes best suited for automation, and those that will generate the highest return on their investment. Even if an investment appears sensible, however, product types are varied, making efficient automation of some processes difficult or impossible. In such cases, the strategic automation of certain procedures within those processes will bring benefits.
This leads to fewer fixed tasks for humans, freeing up their time and energy for high value-added work. Naturally, tasks that are physically challenging or impossible for humans are ideal targets for automation. This also applies to tasks that put humans into potentially dangerous situations, and this leads to improvement from the standpoint of HSE. A 2017 report issued by the World Economic Forum forecasts, over a ten-year period through 2025, a cumulative decrease of 13% in industrial injuries and accidents.
Oil and gas industry work entails certain risks that can place human workers in hazardous circumstances. To advance safety at production and processing facilities while also suppressing operating costs, Yokogawa has entered into an agreement with a robotics technology developer from the Netherlands—whose approach to technology is highly compatible with the robotics service platform vision of Yokogawa—to expand the deployment of robots at particularly dangerous locations. Yokogawa believes that this partnership will lead to the investigation of opportunities for collaboration on cutting-edge solutions.
Yokogawa’s expertise in control and measurement, cybersecurity, AI, digital twins, and cloud technology and its familiarity with both operational technology (OT) and information technology (IT) enables it to co-innovate with customers to create new value by integrating these technologies to stay in tune with changes in customers’ business environments. Yokogawa has the ability to support customers regardless of how far they have come in their digitalization voyage.
Yokogawa serves as a trusted partner to its customers by walking beside them on each step of the journey from industrial automation to industrial autonomy, and affording them increased flexibility and responsiveness in corporate management. Yokogawa’s aim is to create a new model for the manufacturing industry characterized by cooperation among humans, machines, and systems, and through industrial autonomy, generate new business opportunities and paradigms.