"Quick detection of fire in rolling mills due to accumulation of oil residue inside fume ducts"
Customer Concerns
Risk of fire in rolling mills due to accumulation of oil residue inside fume ducts
In rolling mills, rolling oil is sprayed on the rollers to reduce friction and stabilize product quality. Most of the rolling oil is circulated and reused, but a small portion evaporates. The oil vapor, together with dust and other materials, is sucked up into a fume duct mounted directly above the rollers, and is then treated with a dust collector.
Over time, oil residue builds up on the inside surface of the fume duct and is dried by exposure to high temperature gasses, making it highly flammable even at relatively low temperatures. Any contact with an ignition source such as an electrostatic spark can cause this residue to catch fire, and in the worst case such a fire originating in the duct can spread throughout the structure.
Most fume ducts are cleaned periodically, but some locations high up inside the ducts can be difficult to access and clean well, making it difficult to entirely eliminate the risk of fire. It is also nearly impossible to manually monitor conditions inside these ducts.
Fume ducts play an essential role in rolling mills, and the breaking out of a fire inside such an installation can have an adverse impact on a company’s bottom line by causing an unplanned plant shutdown.

The Solutions and the Benefits
24/7/365 temperature monitoring in difficult to access locations
When its optical fiber sensor cable is installed on surface of a fume duct, the Yokogawa DTSX distributed temperature monitoring sensor is able to quickly detect any abnormal rise in temperature inside the duct. Around the clock and year-round, the DTSX is able to monitor temperature even in those locations that are too narrow or too high up for human operators to access.
Minimizing fire damage through early detection of abnormal overheating
The amount of damage caused by a fire will depend in part on how long it takes to detect it and determine its exact location. As many rolling mills are unmanned operations, the fire response at such facilities tends to be delayed. The DTSX is an ideal solution for such problems: with a resolution of just one meter, it is able to pinpoint the location of a heat buildup in as little as 10 seconds.
Together with this solution, Yokogawa provides its customers monitoring screens and reporting functions that are customized based on their specific requirements.
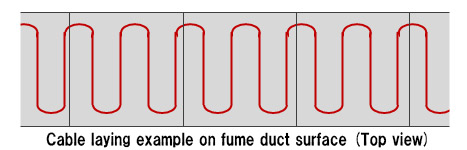
How DTSX Works
Measuring the intensity of Raman scattered light
Using pulses of laser light beamed through an optical fiber cable, the DTSX is able to detect temperature-dependent variations in signal frequency that are the result of a phenomenon known as Raman scattering that occurs along the entire length of the optical fiber cable, and it also can determine the locations of those temperature readings using light that is bounced back (backscattering) to the source.
Example: Along a 6,000 meter optical fiber cable, nearly 6,000 measurement points
By measuring how long it takes light to make a round trip back to the source (backscattering), the DTSX is able to calculate the location for each temperature reading. Abnormalities can be located with a spatial resolution of just one meter.
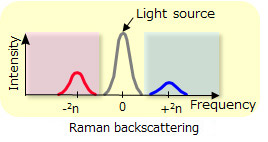
Looking for more information on our people, technology and solutions?
Contact UsZugehörige Produkte & Lösungen
-
DTSX1 Faseroptischer Wärmemelder
Der DTSX1 schützt Ihre Anlagen und Geräte vor einer auffälligen Wärmeentwicklung. Alle erforderlichen Funktionen für die Wärmemessung sind in nur einer Box. Die Messung erfolgt mit einem Glasfaserkabel, welches eine schnelle Branderkennung in einem großen Bereich ermöglicht.
-
DTSX200 [Ausführung für mittlere Distanzen]
Das DTSX200 ist ein einfach zu integrierendes Glasfaser-Sensorsystem, das auf einer Prozesssteuerungsplattform aufgebaut ist.
-
DTSX3000 [Ausführung für lange Distanzen]
Das DTSX3000 ist für konventionelle und unkonventionelle Öl- und Gasbohrungsanwendungen, LNG- und Raffinerieanlagen, die Pipeline- und Tankleckagedetektion sowie für andere Anwendungen, die eine thermische Überwachung erfordern, ausgelegt.
-
System zur faseroptischen Temperaturmessung - Branderkennung/Brandschutz -
Durch unsere Technologie fungiert das faseroptische Kabel selbst als Temperatursensor.
Da es die Temperaturverteilung über eine weite Distanz und einen großen Bereich misst, erkennt es auch partielle Temperaturveränderungen. Es eignet sich daher nicht nur für den Einsatz in der Anlage, sondern auch in Außenbereichen, die eine Temperaturüberwachung erfordern.