Executive Summary
Energy Brix Australia Corporation,
Morwell, Victoria, Australia
Energy Brix Australia Corporation (EBAC) commissioned Yokogawa Australia Pty. Ltd. to modernize the Morwell Power Station and Brown Coal Briquetting Plant by replacing their control and monitoring systems with a modern Yokogawa CENTUM CS 3000 distributed control system (DCS) and a range of field instruments. EBAC is a long established electric utility in Morwell, which is in the coal rich Latrobe Valley region approximately 150 kilometers east of Melbourne, Victoria.The Morwell Power Station has an installed generating capacity of 180 MW and was built in the 1950s by the State Electricity Commission of Victoria to generate power for the national power grid. The Morwell Station also provides process steam to the adjacent brown coal briquette factory.
This extensive modernization of the Morwell Station's control systems by EBAC and Yokogawa Australia was completed in 2008. EBAC's goals for undertaking this extensive DCS upgrade were to:
- Reduce station operating and maintenance costs
- Generate additional power for export
- Improve plant operating flexibility
- Provide modern conditions for plant operators
- Reduce plant emissions
Following the successful completion of this complex and challenging project, Yokogawa Australia and EBAC were jointly awarded the prestigious 2009 PACE Zenith Australia Industry Award for their leadership in the application of technological excellence and innovation. The PACE Zenith Awards were established in 2004 and are presented to Australian industry annually for outstanding achievements in technological excellence and innovation. Yokogawa Australia's projects have previously won awards in 2005, 2007, and 2008.
Low pressure condensing turbine generator
The Challenges and the Solutions
The application of modern DCS technology at the Morwell Power Station was highly successful in achieving EBAC's objectives. This project accomplished the following:
- Optimized the use of labor by enabling a preventive maintenance approach
- Optimized the plant's operating configuration by allocating turbine loads, allowing the station to operate at continuous maximum capability
- Coordinated station control (range and pressure and process steam pressure), which in turn allows maximum plant flexibility by optimizing boiler and turbine loading to take account of fuel quality variation, plant condition, and briquette factory process steam demand
- Optimized the consumption of brown coal fuel and minimized flue gas discharge by fully automating combustion control on all boilers
- Minimized the consumption of fuel oil, improved furnace stability, and reduced plant stress and operating costs as a result of the automation of brown coal combustion
- Reduced thermal stress on the plant as a result of automating the boiler final steam temperature control
- Significantly improved plant safety by automating drum level control and furnace temperature control
- Increased operational flexibility and improved station response to load demand variations by fitting modern digital governors to all five turbine generators
- Increased consistency of plant operations and reduced rate of load variation
- Reduced maintenance costs through tighter control and more consistent/less stressful operation by reducing the number of significant excursions outside plant design parameters
- Significantly increased continuous MW load output from the available capacity, while minimizing steam wastage and improving operating efficiency by automating steam consumption across all turbines and condensers
- Introduced a new screen-based operator interface that allows operators to monitor plant operations while relying on automation systems to maintain the plant in a stable and controlled condition throughout all steady state, load change, and plant upset conditions
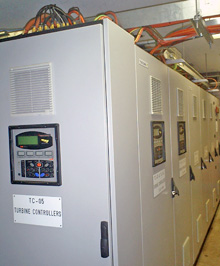
CENTUM CS 3000
control system cabinet
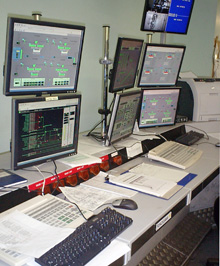
CENTUM CS 3000
station operator consoles
Customer Satisfaction
EBAC believes that the engineering complexity and innovation involved in installing 21st century control systems technology in an old plant was quite remarkable. Not only did the project increase the reliability of electricity supply, it reduced plant stress and decreased its maintenance costs. This was accomplished by optimizing the use of raw fuels. The successful outcome of this control system modernization project will allow the Morwell power generation and briquetting facility to operate well into the future while meeting anticipated economic and emissions standards.
Peter Morrow, General Manager of EBAC (left) and Philip Nicholson, Principal Engineer of Yokogawa Australia (center) accepted the PACE Zenith Award from Jeremy Needham of Mitsubishi Electric, sponsors of the Transport, Power and Infrastructure category.
Related Industries
-
Power
In the mid 1970s, Yokogawa entered the power business with the release of the EBS Electric Control System. Since then, Yokogawa has steadfastly continued with the development of our technologies and capabilities for providing the best services and solutions to our customers worldwide.
Yokogawa has operated the global power solutions network to play a more active role in the dynamic global power market. This has allowed closer teamwork within Yokogawa, bringing together our global resources and industry know-how. Yokogawa's power industry experts work together to bring each customer the solution that best suits their sophisticated requirements.
-
Thermal
Thermal power using coal, oil or gas as fuel accounts for the majority of electric generation throughout the world.
Prodotti e Soluzioni Correlati
-
Distributed Control System (DCS)
Our distributed control system (DCS) enables automation and control of industrial processes and enhanced business performance. Over 30,000 systems entrust Yokogawa DCS to deliver their production goals.