Introduction
To defray energy costs, many industrial plants have their own boilers to generate steam in order to produce a portion of their energy needs. In addition to generating power, the steam may also be used directly in plant processes or indirectly via heat exchangers or steam jacketed vessels.
Problems
The raw water used to feed the boilers contains varying levels of impurities that must be removed to protect the boiler and associated equipment. Pre-treatment processes such as reverse osmosis, ion exchange, filtration, softening, and demineralization may be used to reduce the level of impurities, but even the best pretreatment processes will not remove them all and will continuously carry some dissolved mineral impurities into the boiler.
These dissolved impurities accumulate in the boiler water when steam is made; only pure water leaves the boiler. The increasing concentration of dissolved solids leads to carryover of boiler water into the steam, damaging piping, steam traps, and other process equipment. The concentration of dissolved solids increases until the boiler water can no longer hold all of them in solution and a saturation point is reached. They then begin to drop out becoming suspended solids and forming a sludge or scale on the boiler walls and piping.
Boiler problems are avoided by periodically discharging or “blowing down” water from the boiler to reduce the concentrations of suspended and total dissolved solids. Surface water blowdown is often done continuously to reduce the level of dissolved solids, and bottom blowdown is performed periodically to remove sludge or suspended solids from the bottom of the boiler. The frequency and level of blowdown required each day depends upon the concentration of impurities and the rate at which they build up in the boiler water.
Boilers operating on soft water will require more top or skimmer blowdown to remove dissolved solids, whereas boilers operating on hard water will require more bottom blowdown to remove the settled solids. While control of suspended and dissolved solids in the boiler is critical, care must be taken to avoid excessive blowdown, as this would increase the demand for make-up (feed) water, treatment chemicals, and fuel.
Benefits/Solutions
The benefits for proper boiler blowdown control include the following:
- Reduced operating costs (less feedwaterconsumption, chemical treatment, and higher heating efficiency).
- Reduced maintenance and repair costs (minimized carryover and deposits).
- Cleaner and more efficient steam.
- Minimized energy loss from boiler blowdown can save about 2% of a facility’s total energy use with an average simple payback of less than one year.
The most common methodologies used for boiler blowdown control include: (1) continuous, (2) manual and (3) automatic.
Continuous blowdown utilizes a calibrated valve and a blowdown tap near the boiler water surface. As the name implies, it continuously takes water from the top of the boiler at a predetermined rate to reduce the level of dissolved solids. The rate is usually set slightly greater than necessary to maintain safety protocols.
Manual blowdown is accomplished at most plants by taking boiler water samples once a shift and adjusting the blowdown accordingly. This grab sample approach means that operators cannot immediately respond to changes in feedwater conditions or variations in steam demand and scaling conditions can occur and go undetected until the next sample check.
Automatic blowdown control is achieved by constantly monitoring the conductivity value of the boiler water, adjusting the blowdown rate, and the duration based on a specific conductivity set point. This provides control of the water chemistry.
Manual blowdown control cannot maintain this level of control more than 20% of the time. Upgrading from manual blowdown control to automatic control can reduce a boiler’s energy use by 2 – 5 percent and blowdown water losses by up to 20 percent.
Feed water usually contains one limiting component such as chloride, sulfate, carbonate, or silica. Even if the component is not conductive, as is the case with silica, its concentration is usually proportional to a component that can be measured by conductivity. Therefore, conductivity is a viable measurement for monitoring the overall total dissolved solids present in the boiler. A rise in conductivity indicates a rise in the “contamination” of the boiler water.
Summary
The frequency and duration required for boiler blowdown is significantly affected by the water quality. Improving feedwater quality through makeup water, chemical treatment and proper blowdown control can significantly reduce treatment and operational costs including:
- Reduced operating costs
- Reduced maintenance and repair costs
- Cleaner and more efficient steam
- Energy savings
Increased efficiency and reduced operating costs can be achieved by using the Yokogawa Conductivity Series line of products. Control configurations will carry with the application and the customer’s requirements.
Product Recommendations
Conductivity Measurement System:
Process Liquid Analyzer:
2-wire FLXA202 Conductivity Analyzer
4-wire FLXA402 Conductivity Analyzer
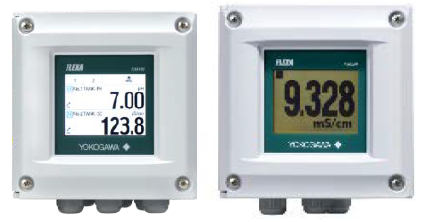
Sensor Selection:
Analog and Digital SMART sensors are available. Analog options allow users to interface with a system that has been used historically. SENCOM™ technology, which allows sensors to transmit and receive data when connected to a transmitter/analyzer or a PC. The SMART digital sensors maintain specific measurement and calibration data on an integrated chip along that is an integral part of the sensor providing easy plug and play solutions. The data management software optimizes the performance of sensors for enhanced reliability and process safety.
Option #1:
SC42-S*34 Large-Bore Conductivity Sensor
(fittings available for Flow-Thru, Insertion, or Immersion installations)
Option #2:
SC4A Conductivity Sensor
(fittings available for Insertion, Sanitary, or Retractable installations.)
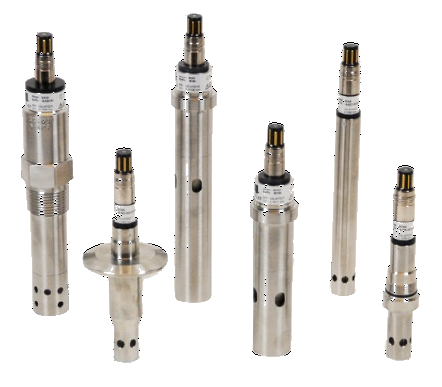
Another alternative would be Toroidal or Inductive Conductivity Sensor:
ISC40 Inductive Conductivity Sensor (fittings available for Flow-thru, Insertion, or Immersion installations)
Industrii similare
-
Power
In the mid 1970s, Yokogawa entered the power business with the release of the EBS Electric Control System. Since then, Yokogawa has steadfastly continued with the development of our technologies and capabilities for providing the best services and solutions to our customers worldwide.
Yokogawa has operated the global power solutions network to play a more active role in the dynamic global power market. This has allowed closer teamwork within Yokogawa, bringing together our global resources and industry know-how. Yokogawa's power industry experts work together to bring each customer the solution that best suits their sophisticated requirements.
-
Petrol & Gaze
Yokogawa has a wealth of experience in every part of the oil and gas business, from offshore and onshore facilities to pipelines, terminals, and deepwater operations. We provide solutions that enhance safety, ensure accurate and reliable operation, and increase plant efficiency.
-
Chimic
Chemical plants rely on continuous and batch production processes, each posing different requirements for a control system. A continuous process calls for a robust and stable control system that will not fail and cause the shutdown of a production line, whereas the emphasis with a batch process is on having a control system that allows great flexibility in making adjustments to formulas, procedures, and the like. Both kinds of systems need to be managed in available quality history of product, and to be able to execute non-routine operations. With its extensive product portfolio, experienced systems engineers, and global sales and service network, Yokogawa has a solution for every plant process.
-
Celuloză & Hârtie
The paper and pulp industry is highly competitive and must meet ever-changing market needs. Yokogawa helps realize energy-efficient plants which are globally sustainable.
-
Food & Beverage
At Yokogawa, we understand that today’s food and beverage companies face unprecedented challenges in climate change, consumer demand, and increased global competitiveness. Overcoming these challenges will require innovative solutions that focus on key areas of production, asset management, and food safety and quality.
-
Petrol & Gaze Downstream
The oil & gas downstream industry has been facing an increasing number of challenges in recent years. These include the changing characteristics of the feedstock to be processed, aging of process facilities and equipment, rising cost of energy, lack of skilled plant operators who can run a refinery safely and efficiently, and the ever-changing requirements from both the market and the customer.
Over the years, Yokogawa has partnered with many downstream companies to provide industrial solutions focused on solving these challenges and problems. Yokogawa's VigilantPlant solutions have helped plant owners to achieve maximum profitability and sustainable safety within their plants.
Produse & Soluții similare
-
2-Wire Transmitter/Analyzer FLXA202
The FLEXA™ series analyzers are used for continuous on-line measurements in industrial installations. With an option for single or dual sensor measurement, they are the most flexible two-wire analyzer available.
-
2-Wire Transmitter/Analyzer FLXA21
The FLEXA™ series analyzers are used for continuous on-line measurements in industrial installations. With an option for single or dual sensor measurement, they are the most flexible two-wire analyzer available.
-
Conductivity Analyzers
Conductivity meters, analyzers and transmitters are used for continuous process measurement and monitoring of conductivity, resistivity, WIFI, demineralizer water, RO water, percent concentration, boiler blowdown and TDS.
-
Conductivity Sensors
Conductivity sensors and electrodes are used to measure process conductivity, resistivity, WIFI, demineralizer water, RO water, percent concentration, boiler blowdown and TDS. Various installation options including retractable, flow thru, immersion, and direct insertion. Proper electrode/sensor selection is critical for optimal measurement results.
-
Contacting Conductivity Sensors SC42/SC4A(J)
The measurement of specific conductivity in aqueous solutions is becoming increasingly important for the determination of impurities in water. Yokogawa has designed a full range of precision sensors and instruments to cope with these measurements, even under extreme conditions.
-
Digital SMART SENCOM™ Adapter, SA11
Reusable SMART adapter, requiring only the analog sensor to be disposed of when it reaches the end of its lifetime. With the SENCOM 4.0 platform, Yokogawa delivers reduced costs and waste while contributing to its long-term business goals of a sustainable future for all.
-
Inductive (Torodial, Electrodeless) Conductivity Sensor ISC40
The model ISC40 sensors are designed for use with the FLEXA ISC analyzers. This combination exceeds all expectations for conductivity measurement in terms of reliability, accuracy, rangeability and price performance.
-
Multi Channel 4-Wire Analyzer FLXA402
The FLEXA™ series analyzers are modular-designed analyzers used for continuous online measurements in industrial installations. They offer single or multi-sensor measurement.
-
Pure Water (Low) Conductivity sensors SC4A(J)/SC42
Intended for the low conductivity applications found in the semi-conductor, power, water and pharmaceutical industries, these sensors are in a convenient compact style.
-
SENCOM™ SMART Digital Sensors
Yokogawa’s SENCOM SMART Sensor Platform is an innovative analyzer platform that optimizes maintenance, reduces configuration time, and simplifies in-field maintenance and calibration.