Introduction
To defray energy costs, many industrial plants have their own boilers to generate steam in order to produce a portion of their energy needs. In addition to generating power, the steam may also be used directly in plant processes or indirectly via heat exchangers or steam jacketed vessels.
Problems
The raw water used to feed the boilers contains varying levels of impurities that must be removed to protect the boiler and associated equipment. Pre-treatment processes such as reverse osmosis, ion exchange, filtration, softening, and demineralization may be used to reduce the level of impurities, but even the best pretreatment processes will not remove them all and will continuously carry some dissolved mineral impurities into the boiler.
These dissolved impurities accumulate in the boiler water when steam is made; only pure water leaves the boiler. The increasing concentration of dissolved solids leads to carryover of boiler water into the steam, damaging piping, steam traps, and other process equipment. The concentration of dissolved solids increases until the boiler water can no longer hold all of them in solution and a saturation point is reached. They then begin to drop out becoming suspended solids and forming a sludge or scale on the boiler walls and piping.
Boiler problems are avoided by periodically discharging or “blowing down” water from the boiler to reduce the concentrations of suspended and total dissolved solids. Surface water blowdown is often done continuously to reduce the level of dissolved solids, and bottom blowdown is performed periodically to remove sludge or suspended solids from the bottom of the boiler. The frequency and level of blowdown required each day depends upon the concentration of impurities and the rate at which they build up in the boiler water.
Boilers operating on soft water will require more top or skimmer blowdown to remove dissolved solids, whereas boilers operating on hard water will require more bottom blowdown to remove the settled solids. While control of suspended and dissolved solids in the boiler is critical, care must be taken to avoid excessive blowdown, as this would increase the demand for make-up (feed) water, treatment chemicals, and fuel.
Benefits/Solutions
The benefits for proper boiler blowdown control include the following:
- Reduced operating costs (less feedwaterconsumption, chemical treatment, and higher heating efficiency).
- Reduced maintenance and repair costs (minimized carryover and deposits).
- Cleaner and more efficient steam.
- Minimized energy loss from boiler blowdown can save about 2% of a facility’s total energy use with an average simple payback of less than one year.
The most common methodologies used for boiler blowdown control include: (1) continuous, (2) manual and (3) automatic.
Continuous blowdown utilizes a calibrated valve and a blowdown tap near the boiler water surface. As the name implies, it continuously takes water from the top of the boiler at a predetermined rate to reduce the level of dissolved solids. The rate is usually set slightly greater than necessary to maintain safety protocols.
Manual blowdown is accomplished at most plants by taking boiler water samples once a shift and adjusting the blowdown accordingly. This grab sample approach means that operators cannot immediately respond to changes in feedwater conditions or variations in steam demand and scaling conditions can occur and go undetected until the next sample check.
Automatic blowdown control is achieved by constantly monitoring the conductivity value of the boiler water, adjusting the blowdown rate, and the duration based on a specific conductivity set point. This provides control of the water chemistry.
Manual blowdown control cannot maintain this level of control more than 20% of the time. Upgrading from manual blowdown control to automatic control can reduce a boiler’s energy use by 2 – 5 percent and blowdown water losses by up to 20 percent.
Feed water usually contains one limiting component such as chloride, sulfate, carbonate, or silica. Even if the component is not conductive, as is the case with silica, its concentration is usually proportional to a component that can be measured by conductivity. Therefore, conductivity is a viable measurement for monitoring the overall total dissolved solids present in the boiler. A rise in conductivity indicates a rise in the “contamination” of the boiler water.
Summary
The frequency and duration required for boiler blowdown is significantly affected by the water quality. Improving feedwater quality through makeup water, chemical treatment and proper blowdown control can significantly reduce treatment and operational costs including:
- Reduced operating costs
- Reduced maintenance and repair costs
- Cleaner and more efficient steam
- Energy savings
Increased efficiency and reduced operating costs can be achieved by using the Yokogawa Conductivity Series line of products. Control configurations will carry with the application and the customer’s requirements.
Product Recommendations
Conductivity Measurement System:
Process Liquid Analyzer:
2-wire FLXA202 Conductivity Analyzer
4-wire FLXA402 Conductivity Analyzer
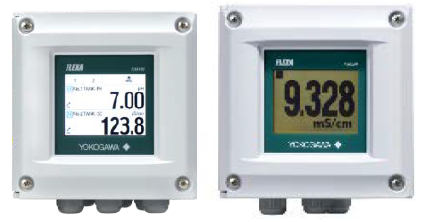
Sensor Selection:
Analog and Digital SMART sensors are available. Analog options allow users to interface with a system that has been used historically. SENCOM™ technology, which allows sensors to transmit and receive data when connected to a transmitter/analyzer or a PC. The SMART digital sensors maintain specific measurement and calibration data on an integrated chip along that is an integral part of the sensor providing easy plug and play solutions. The data management software optimizes the performance of sensors for enhanced reliability and process safety.
Option #1:
SC42-S*34 Large-Bore Conductivity Sensor
(fittings available for Flow-Thru, Insertion, or Immersion installations)
Option #2:
SC4A Conductivity Sensor
(fittings available for Insertion, Sanitary, or Retractable installations.)
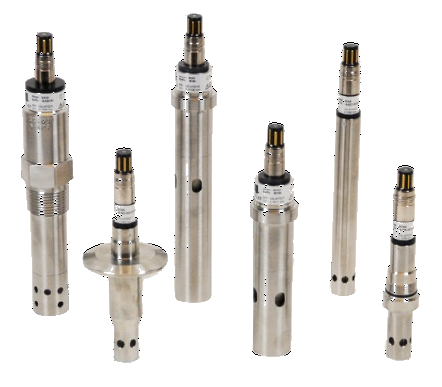
Another alternative would be Toroidal or Inductive Conductivity Sensor:
ISC40 Inductive Conductivity Sensor (fittings available for Flow-thru, Insertion, or Immersion installations)
Verwandte Industrien
-
Power
In the mid 1970s, Yokogawa entered the power business with the release of the EBS Electric Control System. Since then, Yokogawa has steadfastly continued with the development of our technologies and capabilities for providing the best services and solutions to our customers worldwide.
Yokogawa has operated the global power solutions network to play a more active role in the dynamic global power market. This has allowed closer teamwork within Yokogawa, bringing together our global resources and industry know-how. Yokogawa's power industry experts work together to bring each customer the solution that best suits their sophisticated requirements.
-
Chemical
Chemical plants rely on continuous and batch production processes, each posing different requirements for a control system. A continuous process calls for a robust and stable control system that will not fail and cause the shutdown of a production line, whereas the emphasis with a batch process is on having a control system that allows great flexibility in making adjustments to formulas, procedures, and the like. Both kinds of systems need to be managed in available quality history of product, and to be able to execute non-routine operations. With its extensive product portfolio, experienced systems engineers, and global sales and service network, Yokogawa has a solution for every plant process.
-
Pulp & Paper
The paper and pulp industry is highly competitive and must meet ever-changing market needs. Yokogawa helps realize energy-efficient plants which are globally sustainable.
-
Food & Beverage
At Yokogawa, we understand that today’s food and beverage companies face unprecedented challenges in climate change, consumer demand, and increased global competitiveness. Overcoming these challenges will require innovative solutions that focus on key areas of production, asset management, and food safety and quality.
-
Oil & Gas Downstream
The oil & gas downstream industry has been facing an increasing number of challenges in recent years. These include the changing characteristics of the feedstock to be processed, aging of process facilities and equipment, rising cost of energy, lack of skilled plant operators who can run a refinery safely and efficiently, and the ever-changing requirements from both the market and the customer.
Over the years, Yokogawa has partnered with many downstream companies to provide industrial solutions focused on solving these challenges and problems. Yokogawa's VigilantPlant solutions have helped plant owners to achieve maximum profitability and sustainable safety within their plants.
Zugehörige Produkte & Lösungen
-
2-Leiter-Analysator FLXA202/21
Die Analysatoren der FLEXA-Serie werden für kontinuierliche Online-Messungen in industriellen Anlagen verwendet. Mit der Option für die Ein- oder Zwei-Sensor-Messung sind sie die flexibelsten 2-Leiter-Analysegeräte auf dem Markt.
-
2-Leiter-Messumformer/-Analysator FLXA202
Die Analysatoren der FLEXA™ Serie werden für kontinuierliche Online-Messungen in industriellen Anlagen verwendet. Mit der Option für die Ein- oder Zwei-Sensor-Messung sind sie die flexibelsten 2-Leiter-Analysegeräte auf dem Markt.
-
Digitaler SENCOM™ SMART-Adapter, SA11
Wiederverwendbarer SMART-Adapter, bei dem nur der Analogsensor am Ende der Lebensdauer entsorgt werden muss. Mit der Plattform SENCOM 4.0 reduziert Yokogawa Kosten und Abfälle und trägt damit zu seinem langfristigen Unternehmensziel einer nachhaltigen Zukunft für alle bei.
-
Induktiver (Ringsensor) Leitfähigkeitssensor ISC40
Sensoren des Modells ISC40 sind für den Einsatz mit FLEXA ISC-Analysatoren konzipiert. Diese Kombination übertrifft alle Erwartungen an Leitfähigkeitsmessungen hinsichtlich Zuverlässigkeit, Genauigkeit, Bereichsverhältnis und Preis-Leistungs-Verhältnis.
-
Konduktive Leitfähigkeitssensoren SC42/SC4A(J)
Die Messung der spezifischen Leitfähigkeit in wässrigen Lösungen wird immer wichtiger für die Bestimmung von Verunreinigungen im Wasser. Yokogawa hat ein vollständiges Programm an Präzisionssensoren und -instrumenten entwickelt, um diese Messungen auch unter extremen Bedingungen zuverlässig durchführen zu können.
-
Leitfähigkeitsanalysatoren
Leitfähigkeitssensoren und -analysatoren werden für die kontinuierliche Messung und Überwachung von Leitfähigkeit, Widerstand, prozentualer Konzentration und gesamte gelöste Feststoffe (TDS) eingesetzt. Anwendung finden diese Sensoren beispielsweise in Entsalzungsanlagen oder bei der Abschlämmung von Kesseln.
-
Leitfähigkeitssensoren
Leitfähigkeitssensoren dienen zur Messung von Leitfähigkeit, Widerstand, WIFI, prozentualer Konzentration und den gesamten gelösten Feststoffen (TSD). Anwendung finden diese Sensoren beispielsweise in Entsalzungsanlagen, der Wasseraufbereitung in Umkehrosmoseanlagen oder bei der Abschlämmung von Kesseln. Die verschiedenen Installationsoptionen schließen u. a. Wechsel-, Durchfluss- und Eintaucharmaturen sowie den direkten Einbau ein. Die richtige Auswahl von Sensoren ist für optimale Messergebnisse von entscheidender Bedeutung.
-
Mehrkanal-4-Leiter-Analysator FLXA402
Die Analysatoren der FLEXA™-Serie sind modular gestaltete Analysegeräte für kontinuierliche Online-Messungen in industriellen Anlagen. Sie ermöglichen Messungen mit einem oder mehreren Sensoren.
-
SENCOM™ SMART-Digitalsensoren
Yokogawas SENCOM SMART-Sensorplattform ist eine innovative Analysatorplattform, die Wartungsmaßnahmen optimiert, Konfigurationszeiten reduziert und die Wartung und Kalibrierung vor Ort vereinfacht.
-
Sensoren für Reinwasser SC4A(J)/SC42
Diese Sensoren sind für Anwendungen bei niedriger Leitfähigkeit vorgesehen, wie sie in der Halbleiter- und Kraftwerksindustrie-, der Wasserwirtschaft und der Pharmabranche vorkommen; sie zeichnen sich durch eine zweckmäßige kompakte Bauform aus.