Analyzer that realizes real-time feedback and adds value to users through active use such as process control and safety control
- Energy-efficient furnaces, etc., and safety and stable operation contribute to improving OPEX and reducing environmental impact.
- Rapid feedback of process output to the control program, which is essential for optimal operation.
- Release of cumbersome sampling devices and drive components from maintenance.
- Realization of direct measurement under severe process conditions such as high temperature and corrosiveness.
The TDLS8000 is an analyzer that can solve these problems.
Details
The most trusted laser analyzer designed specifically to meet all of your requirements in one robust device that is easy to operate and maintain.
Your benefits
- Measurement with a line using a laser does not miss dangerous thermal unevenness.
- By using a reference cell, low concentration gas is also measured with high accuracy.
- The optical path length can be measured up to 30 m and can be measured up to 1500℃ of hot gas.
- It can also be installed in dangerous places by acquiring Japanese explosion proof authentication, IECEx certification, ATEX certification, FM (US, Canada), KOSHA certification, NEPSI certification, and EAC explosion proof certification.
- The sampling device is unnecessary, and it is easy to install because of its compact design.
- Non-contact type sensor without consumables, i.e. maintenance due to leakage or deterioration is unnecessary.
- It is possible to replace the parts on the spot while they are still installed during repair, and it is possible to reduce the plant shutdown and repair costs due to downtime.
Features: Reasons for high reliability
Enable for safe operation, safety level SIL2, and explosion proof standards.
It conforms to the certification of the safety level SIL2 in accordance with the International standards IEC61508, and can also conform to the SIL3 by duplexing the analyzer.
In addition, the solid body conforms to various explosion proof standards of the area-segmented Zone2/Div2 or Zone1/Div1 and can be installed in dangerous places.
No PC is required for direct simple operation and maintenance with intuitive 7.5-inch color touch screen HMI.
It supports 10 languages: English, German, French, Spanish, Portuguese, Russian, Hungarian, Korean, Chinese, and Japanese.
Provides all information, including trend graphs, and can be remotely installed.
Standard communication functions that can be checked and adjusted both on-site and at remote locations. (Installation and maintenance cost reduction)
The HART and Modbus TCP communications standards are standardized and can be setup and adjusted by our FieldMate.
Fully field repairable with 50 days of data and spectra storage
Data for 50 days are stored, and can be analyzed when installed in the process.
Compact design for one-man installation without sacrificing ruggedness
Modular design allows replacement and re-operation of components at the site
System configuration according to the plant situation
System configuration according to the plant situation
By connecting to FieldMate via standard HART communication, setting and adjustment can be easily done without HMI. A small display is standard equipment at both ends (sensor control unit and laser unit). The transmittance required to adjust the light axis is always displayed, making it easy to adjust the light axis.
System Configuration with HMI
The 7.5-inch color touch screen HMI YH8000 can improve on-site monitoring and operability.
Multi Analyzer Configuration with Remote HMI
Up to 4 TDLS8000 can be connected per HMI for remote control.
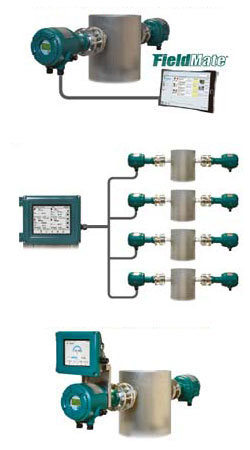
Main specifications of TDLS8000
Measurement object | O2, CO, CO or CH4, CO2, CO + CO2, H2O, NH3, NH3 + H2O, H2S, HCl concentration in combustion exhaust gas and process gas | |||
---|---|---|---|---|
Measured components and range | Measured component | Min. range | Max. range | |
O2 | 0-1% | 0-25% | ||
CO(ppm) | 0-200 ppm | 0-10,000 ppm | ||
CO+CH4 | CO | 0-200 ppm | 0-10,000 ppm | |
CH4 | 0-5 % | |||
NH3 | 0-30 ppm | 0-50,000 ppm | ||
H2O (ppm) in non HC | 0-30 ppm | 0-30,000 ppm | ||
H2O (ppm) in HC | 0-30 ppm | 0-30,000 ppm | ||
CO (%) | 0-20 % | 0-50 % | ||
CO (%) + CO2 (%) | 0-30 % | 0-100 % | ||
NH3 + H2O | NH3 | 0-30 ppm | 0-5,000 ppm | |
H2O | 0-5 % | 0-50 % | ||
H2S | 0-5 % | 0-100 % | ||
CO2 (%) High Range | 0-1 % | 0-5 % | ||
CO2 (%) Extend.Range | 0-30 % | 0-50 % | ||
H2O (%) | 0-10 % | 0-100 % | ||
HCl | 0-50 ppm | 0-5,000 ppm | ||
Hazardous area classifications | Division 1, Zone 1; Explosion-proof/ Flame-proof type; FM (US, Canada), ATEX, IECEx, Korea, NEPSI, Japan, EAC, INMETRO Division 2, Zone 2; Non-Incendive/Type n; FM (US, Canada), ATEX, IECEx, Korea, NEPSI, EAC, INMETRO, Japan |
|||
SIL Certification | The TDLS8000 expect digital output (2 points), digital input (2 points), valve control output (2 points), and digital communications (HART, Modbus/TCP) are certified in compliance with the following standard. IEC 61508:Functional safety of Electrical/electronic/programmable electronic related systems; SIL 2 capability for single analyzer use, SIL 3 capability for dual analyzer use. | |||
Marine certificate | DNV Type Approval | |||
Certification for Emission Monitoring | QAL1 |
Main specifications of HMI : YH8000
Display | Touchscreen 7.5 inch TFT color LCD panel, 640 x 480 (VGA) |
---|---|
Hazardous area classifications |
Division 2, Zone2: Non-Incendive/Type n; FM (US, Canada), ATEX, IECEx, Korea, NEPSI, Japan |
Related products and Maintenance parts
[Related products]
IF8000:
The Process Insulation Flange protects the TDLS8000 from process gas pressures, heat, dust, and corrosive components from the process gas.
It can be used for protection during direct mounting or bypass mounting.
Use in the following cases.
- When the process gas pressure exceeds 500 kPa
- If the temperature of the process is high and the temperature of the process window exceeds 55℃ even if the process window is purged.
- If the process has a large amount of dust and the process windows are purged to prevent dust from adhering to the process windows or corrosive components from entering the process windows.
YC8000 Flow Cell : Used to sample and measure gases at any location.
Calibration cell : Used for offline calibration and validation.
Unit connection cable : Used to connect the sensor control unit and the laser unit.
[Maintenance parts]
O-ring : Replace the O-ring when it is removed for periodic inspection, etc.
The simple and robust TDLS8000 assures the reliable and less maintenance operation of the analysis.
Fired Heater Combustion Safety and Lifecycle Management
Yokogawa TDSL8000 and CO + CH4 measurements provide reliable information to achieve:
- Combustion efficiency improvement
- Safety improvement
- Longer lifetime of the coils and coil hangers
- Higher throughout of the process heating
Limited O2 Concentration
O2 Measurement for Safety and Process Monitoring & Control Yokogawa TDLS8000 02 analyzer achieves:
- No sampling system operation
- Fast response analysis
- No interference analysis
- Less maintenance operation
TDLS8000 Activity Example
In this way, we are making use of our products.
O2 and HCl measurement at waste incinerators
Since this is a non-contact measurement, the measurement of exhaust gas from waste incinerators, which have a large amount of dust and corrosive components, is not problematic with TDLS™. In addition, since measurement can be performed at high temperatures, measurement and high-speed control can be realized in the vicinity of the combustion section, thereby improving the operating efficiency.
O2 was measured for safety and quality control at chemical plants and steel works.
The TDLS eliminates the problems of maintaining sampled filters, delaying responses, and interfering gases.
O2 and CO were measured to monitor the fire prevention of coal and pulverized coal storage.
Temperature and CO-measurements are essential for detecting the ignition of coal and bag filters in storage tanks.
The reference cell can stably measure low concentrations, which were Display at 0% in other products. High-speed measurement is possible without concern of dust clogging.
H2O measurement for various moisture monitoring.
Measure the water content of the drying oven, such as cellophane, gypsum, plywood, paint, and food, from the % level of water to the ppm level of water in the manufacturing process, which is unpleasant.
O2 and CO were measured in an electric furnace.
It is possible to measure the O2 and CO of the exhaust gas generated in the electric furnace and perform melting without waste.
Exhaust gas from high-temperature and high-dust electric furnaces has proven to be an installation method to suppress the effects of the exhaust gas, and can be measured without problems.
Flow to Order
This is a basic flow, although it differs depending on the customer's area and plant.
For details, please contact us without concern.
*Please tell us about the status of the plant in order to propose the best specifications for your application.
The items related to the status of the factory are as follows.
- Application
- Setting conditions, Optical path length
- Gas pressures, Temperature
- Dust amount
- Gas composition (Measurement range and Gas concentration)
Maintenance Flow
Return to the repair shop is unnecessary during maintenance. Parts can be replaced at the site and restored immediately.
* Since the TDLS is equipped with a self-diagnosis function and supports predictive maintenance, sudden stop of the plant can be avoided in principle.
Other-company products
TDLS8000 : Even in the event of an outbreak
Other services
Enhancement of service network
Servicemans from all over the world are responsible for installation and installation.
Resources
Fired heaters are used for various processes in oil refining and petrochemical plants.
In maintaining and managing industrial plants, monitoring waste water pH/ORP is both a legal obligation and an unavoidable necessity for protecting the environment. Monitoring without an attentive eye can lead to severe consequences.
Considering safety and environmental issues such as combustion efficiency and decreasing NOX and CO in exhaust gas, it has become important to control O2 concentration in garbage incineration processes.
Industrial Combustion sources such as thermal cracking furnaces and, process heaters play a critical role in the process industry.
The ammonia (NH3) gas is injected to remove the NOx and thus reduce the NOx concentration in the stack flue gas. With conventional NH3 analyzers that perform measurements indirectly, NH3 concentrations are obtained through a sampling system. Therefore, there are problems with the maintenance and running costs of the sampling system, and time delays in measurement. The TDLS8000 Laser Analyzer is the solution to all these problems.
Electrolysis plants create hydrogen and chlorine from a brine solution. Chlorine gas generated from the anolyte of the electrolysis tank generally contains between 0.5 to 2.0 vol% H2O. The sample is then cooled and filtered to remove brine, subsequently coming out as wet chlorine gas. The wet gas is sent to a drying tower where it is treated with sulfuric acid to get moisture down to the ppm level.
Caustic soda and hydrochloric acid, produced in electrolyzer plants, are fundamental materials used in varieties of industries; chemicals, pharmaceuticals, petrol-chemicals, pulp and papers, etc. Profit is the result of the effective production with minimized running / maintenance cost. Proper control of the process brings you stabilized quality of products with the vast operational profit.
O2 measurement in hydrocarbon vapor is used for safety monitoring in vacuum distillation columns in petroleum refining. With conventional paramagnetic oxygen analyzers, O2 concentrations are obtained through an extractive sampling system, which conditions the sample prior to being analyzed.
Storage tanks are used in a variety of industries ranging from holding crude oil to holding feedstock for vinyl chloride monomer (VCM).
O2 measurement is used to safely recover flue gas containing a high concentration of CO from a converter furnace. With conventional paramagnetic oxygen analyzers, O2 concentrations are obtained through a sampling system to recovery flue gas. Therefore, there are problems with the maintenance and running costs of the sampling system, and time delays in measurement.
If a sensor is not operating, the manufacturer cannot detect moisture in the chlorine and must stop the process. Unfortunately, sensors can deteriorate and deliver inaccurate measurements due to contact with the process.
Spectrometric technology can assess many critical characteristics about products, but it has limits. It can be challenging to determine when the line has been crossed
With fired heaters, users hope to get greater efficiency and reduced emissions but often are disappointed. Given the number of fired heaters operating every day and their importance in the process industries, any improvements realized across the board will have huge impacts. More units can reach their potential with some simple changes in work practices and technology upgrades.
Downloads
Instruction Manuals
General Specifications
Technical Information
- Oxygen Analyzer Selection Guide (727 KB)
Looking for more information on our people, technology and solutions?
Contact Us