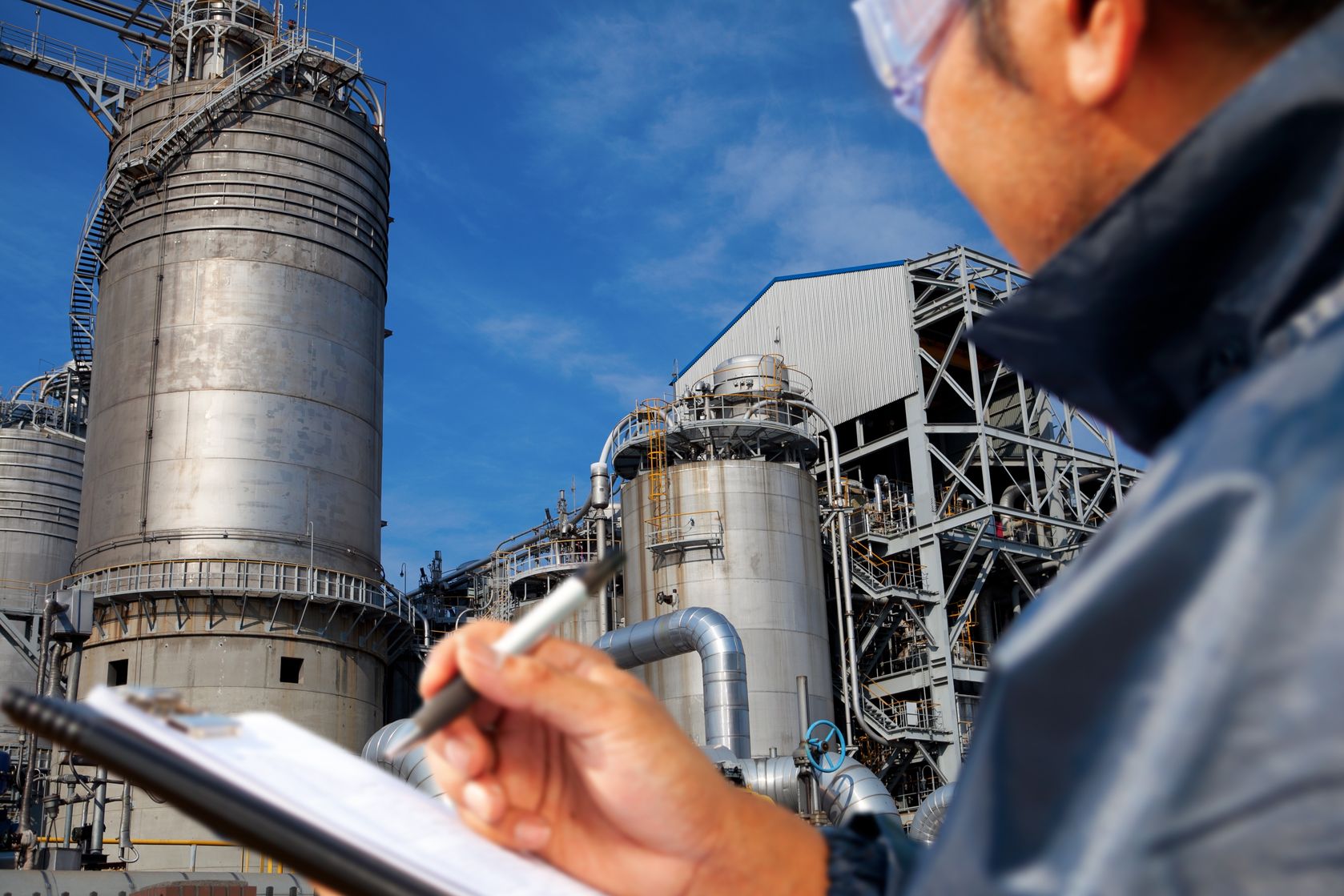
With careful planning and implementation, Yokogawa can help you achieve a safe, cost-effective, and value-added hot or cold cutover migration process for your system.
Challenges for Customers
Upgrading your current assets is necessary for long-term growth and expansion, however, migrating your system produces its own set of challenges and risks.
Customers choose to migrate their systems for two main reasons:
- Keeping up to date on the latest technologies and functions
- Solving problems such as rising maintenance costs, inability of a system to be adapted to support newer applications, declining reliability, and necessity of intensive vendor support.
In either case, the migration process poses its own set of challenges and risks. For instance, the old and new systems might be fundamentally different in design and function, or the migration must be carried out without disrupting production. The plant is at risk of disruptions from delays, technical issues, or errors arising from lack of experience. Strategic planning of migration work is essential for a smooth transition.


Our Solutions
Our commitment to working with you to achieve the ideal plant will play a crucial role in any system migration project.
Taking into account your plant’s operations and the state of its facilities, Yokogawa works with you to carefully plan and implement a hot or cold cutover from your existing system to a new DCS. Through close collaboration with your plant personnel and a methodical approach, we are able to minimize disruptions to your plant’s operations while moving the individual control loops and controllers over to the new system.
Benefits of hot and cold cutover:
- Hot cutover - Significant cost savings because no shutdown and zero downtime
- Cold cutover - No risk of shutdown during changeover work
In most cases, a combination of hot cutover and cold cutover is usually used.
Customer Benefits
Safe, cost-effective, and value-added migration
Yokogawa works with you in the following ways to ensure a safe, cost-effective, and value-added migration process:
- Assessing risks and advising on how best to address them
- Optimizing existing assets
- Maintaining quality
- Minimizing production loss
- Providing long-term support
Through our extensive experience, we understand that the key to success for any migration project to ensure a safe and disruption-free changeover is mutual trust and effective cooperation among all stakeholders. An effective team approach, preparation of key reference data documents, meticulous planning, technical leadership and expertise are also important.
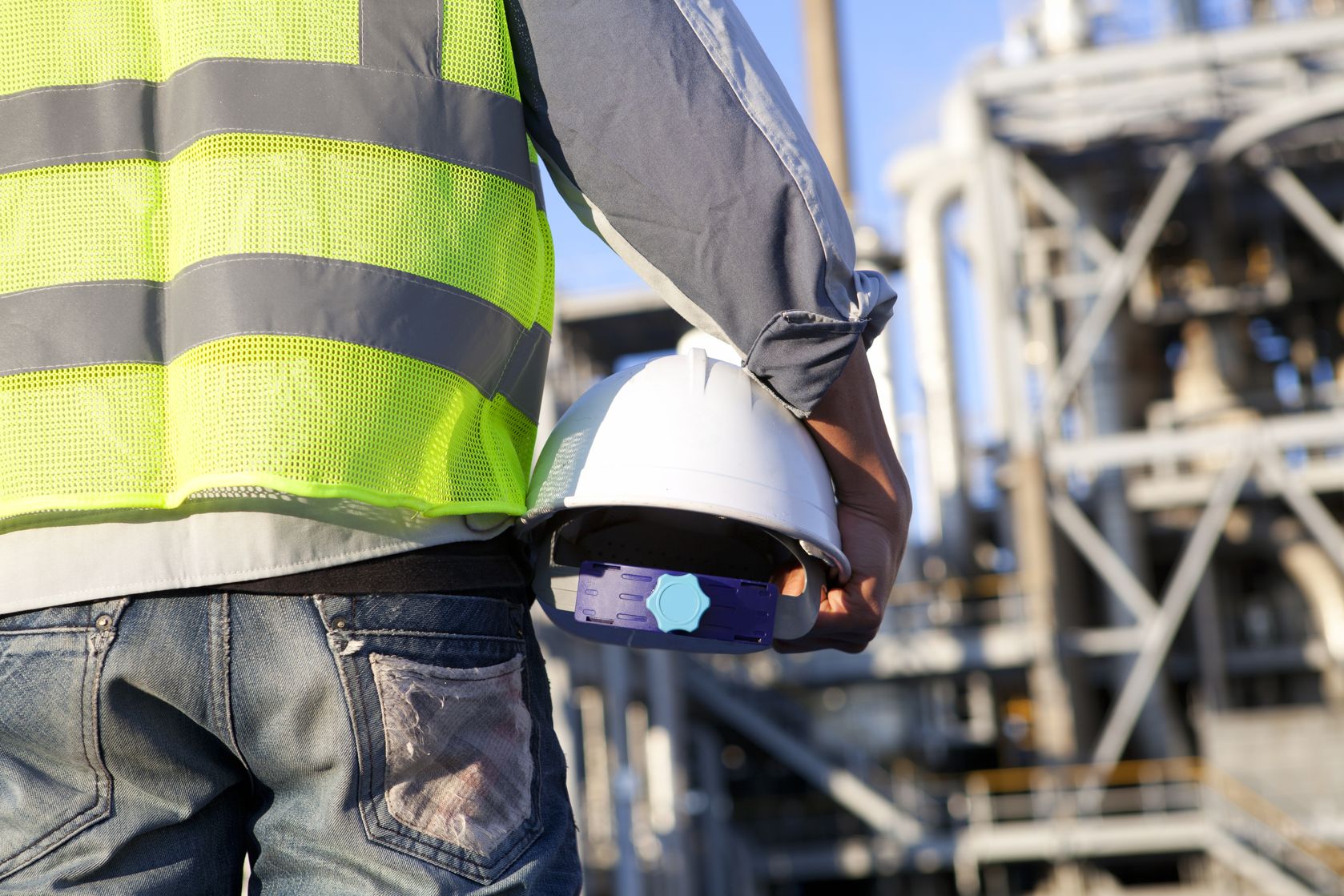
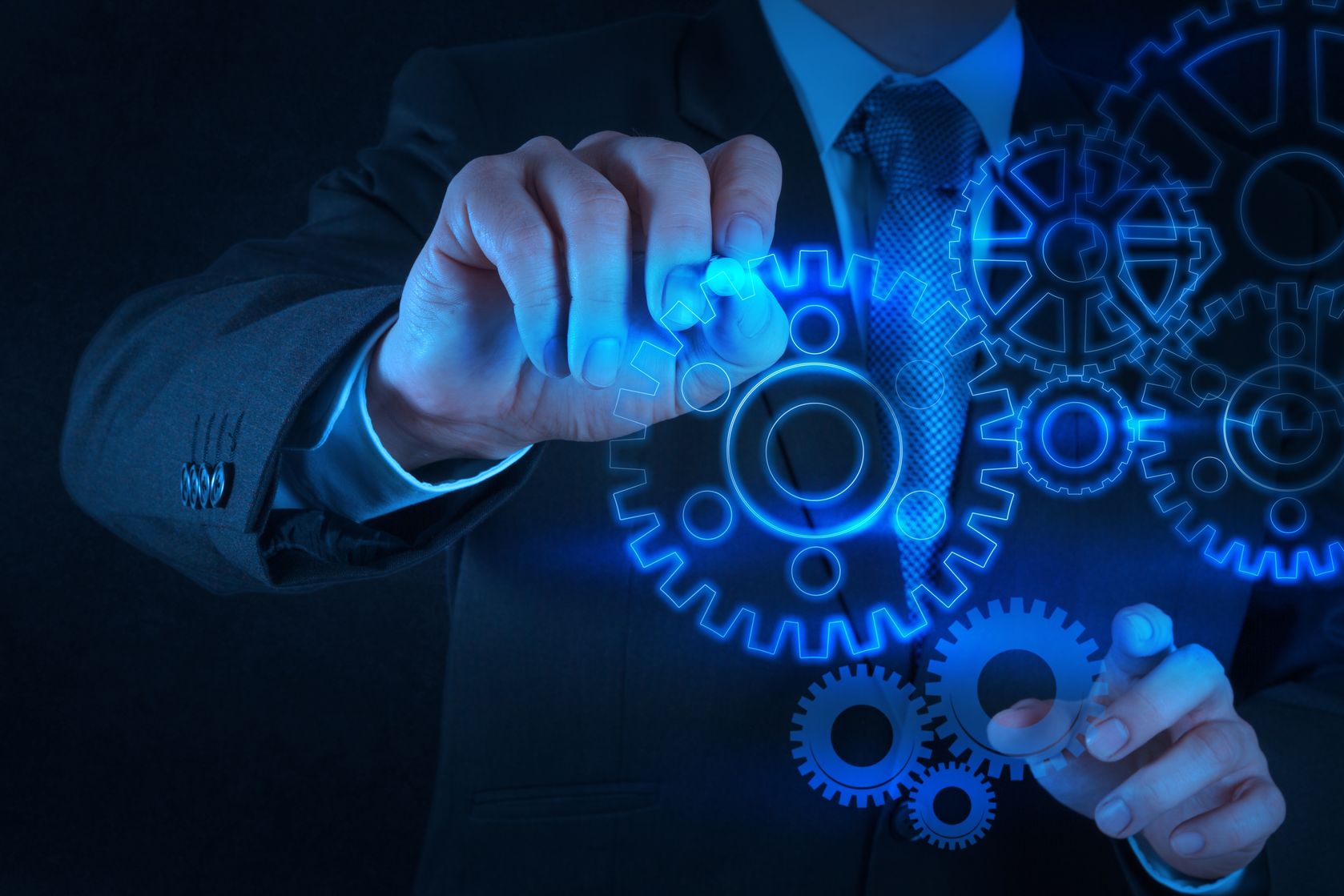
Enabling Technology
Safe, cost-effective, and value-added migration
We perform a smooth migration to minimize plant downtime and raise your operation rate, help you to continue using your valued application assets, achieve seamless connections to higher level systems and subsystems, and provide a virtual environment for operator training.
The Yokogawa modernization solution:
- Database conversion tools for maintaining intellectual property
- Reuse of existing wiring and cabinets
- The seven 9's reliability of the CENTUM VP system
- No gateways, bottlenecks or constraints
- A onetime project, not different projects spread over many years with unknown costs and results
- The latest technologies, from PCs, networks and controllers to asset management toolsets
Details
Minimizing interruptions to plant operations
Taking into account your plant’s operations and the state of its facilities, Yokogawa works with you to carefully plan and implement a hot or cold cutover from your existing system to a new DCS. Through close collaboration with your plant personnel and a methodical approach, we are able to minimize disruptions to your plant’s operations while moving the individual control loops and controllers over to the new system.
Resources
- To replace the existing CENTUM XL control station with the latest Yokogawa CS 3000 hardware and upgrade the control network.
- The plan was to minimize plant downtime by doing a hot cutover from the old to the new control system.
- Smooth and safe switchover to the new system
- Easy-to-use, easy-to-engineer system, plus various post-installation enhancements
- Tuned controllers for smooth plant operation and better traceability of process upsets
- Various other improvements thanks to advanced process control and MVC implementation
The Mathura refinery is a strategically important facility that supplies diesel, gasoline, aviation turbine fuel, kerosene, liquefied petroleum gas, furnace oil, and bitumen to customers throughout northwestern India.
- Yokogawa successfully carried out the upgrade of off-site system in a 48 hour shutdown period with Seibu Oil.
- Control room design for HSE and smooth communication contributes to the operational efficiency and safety.
News
-
Press Release | Corporate Feb 12, 2013 Yokogawa and Soteica Visual MESA Enter Comprehensive Partnership to Address the Energy Management Solutions Business
- Joint initiative will provide new solution services for sitewide energy efficiency optimization -
Looking for more information on our people, technology and solutions?
Contact Us