Introduction
Two types of polymerization reaction are used to produce styrene-butadiene copolymers, the emulsion type and the solution type. This section addresses volatile organic compound (VOC) emissions from the manufacture of copolymers of styrene and butadiene made by emulsion polymerization processes. The emulsion products can be sold in either a granular solid form, known as crumb, or in a liquid form, known as latex.
Copolymers of styrene and butadiene can be made with properties ranging from those of a rubbery material to those of a very resilient plastic. Copolymers containing less than 45 weight percent styrene are known as styrene-butadiene rubber (SBR). As the styrene content is increased over 45 weight percent, the product becomes increasingly more plastic.
As shown in below figure, fresh styrene and butadiene are piped separately to the manufacturing plant from the storage area. Polymerization of styrene and butadiene proceeds continuously through a train of reactors, with a residence time in each reactor of approximately 1 hour. The reaction product formed in the emulsion phase of the reaction mixture is a milky white emulsion called latex. The overall polymerization reaction ordinarily is not carried out beyond a 60 percent conversion of monomers to polymer, because the reaction rate falls off considerably beyond this point and product quality begins to deteriorate.
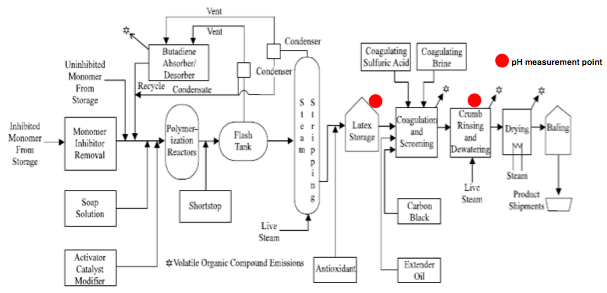
Because recovery of the unreacted monomers and their subsequent purification are essential to economical operation, unreacted butadiene and styrene from the emulsion crumb polymerization process normally are recovered. The latex emulsion is introduced to flash tanks where, using vacuum flashing, the unreacted butadiene is removed. The butadiene is then compressed, condensed, and pumped back to the tank farm storage area for subsequent reuse. The condenser tail gases and noncondensables pass through a butadiene adsorber/desorber unit, where more butadiene is recovered.
Some noncondensables and VOC vapors pass to the atmosphere or, at some plants, to a flare system. The latex stream from the butadiene recovery area is then sent to the styrene recovery process, usually taking place in perforated plate steam stripping columns. From the styrene stripper, the latex is stored in blend tanks.
From this point in the manufacturing process, latex is processed continuously. The latex is pumped from the blend tanks to coagulation vessels, where dilute sulfuric acid (H2SO4 of pH 4 to 4.5) and sodium chloride solution are added. The acid and brine mixture causes the emulsion to break, releasing the styrene-butadiene copolymer as crumb product. The coagulation vessels are open to the atmosphere. Leaving the coagulation process, the crumb and brine acid slurry is separated by screens into solid and liquid. The crumb product is processed in rotary presses that squeeze out most of the entrained water. The liquid (brine/acid) from the screening area and the rotary presses is cycled to the coagulation area for reuse.
Typical Process Details:
Fluid: Crumb slurry
- Fluid composition (normal):
Water: 95% wt
Polymer: 4.06% wt
Fatty acid: 0.2% wt
Extender oil: 0% wt. (Max. 1.45% wt)
Rosin acid: 0.078%wt - Acidity (min/orm/Max): 0.0/3.6/14.0
- Fluid design conditions P@T: 1.033 Kg/cm2- g@115 degC
- Boiling point @ operating pressure: 100 degC
Dew point @ operating pressure: 100 degC
Boiling point @ atmospheric pressure: 100 degC
Dew point @ atmospheric pressure: 100 degC - Density: 980 kg/m3 (Norm)
- Fluid able to foul
Max. pressure: 1.033 kgf/cme-g Tempe: 62 degC
Crumb rinsing and dewatering
Typical Problems:
This is indeed a tough application. The rubber tends to stick on the holder. The rubber does not tend to stick on the glass very much.
Remedies:
To mount the holders in such a way that they can swing with the process flow and make them easy to remove for manual cleaning: 0.5 or 1 m immersion fittings hanging on the hoisting cable on a hook.
Solutions:
- Sensor: SC25V series
- Features SC25V
- External titanium Liquid Earth
- Pt1000 integration in pH compartment giving highly accurate temperature compensation
- CIP and Steam cleaning possible Large internal KCl volume giving the sensor a longer life time
- SC25V-ALP25 for chemically harsh applications and high temperatures
Sensor Holder:
The FD20-P37 comes with hoisting cable made of SS316. When the holder is mounted this way, just hangs in the vessel, then it can swing with the flow. Otherwise the rubber slurry may damage the sensor if the holder is mounted rigidly. Most probably the sensor protection cage must be removed to prevent the polymer to fill the cage.
行业
-
大宗石油化工
无论是生产石化产品、无机物还是中间产品,化工企业都面临着成本和利润率的压力,必须及时有效地交付产品,同时保持安全、合规地运营。此外,化工企业必须应对原料和能源价格的波动,并为市场提供性价比最高的产品组合。
横河电机长期服务于全球大宗化工市场,得到大家的广泛认可。通过我们的产品、解决方案和行业专业知识,横河了解您的市场和生产需求,并将与您合作,在您的工厂生命周期中提供可靠、经济的解决方案。
-
石化
石化公司的需求极为多样繁杂。为了在当今竞争激烈的市场中脱颖而出,生产企业必须努力提高质量和生产力。横河电机在石化领域长期耕耘具有广泛的经验,我们可以为客户的需求提供量身定制的解决方案。
相关产品&解决方案
-
12 mm SC25V pH传感器
SC25V是一款12 mm的pH传感器,包含一个一体型温度元件和一个液体接地电极。
-
2-Wire Transmitter/Analyzer FLXA202
The FLEXA™ series analyzers are used for continuous on-line measurements in industrial installations. With an option for single or dual sensor measurement, they are the most flexible two-wire analyzer available.
-
FLXA202/21两线制变送器/分析仪
FLEXA™系列分析仪用于工业设施中的连续在线测量。它是灵活的两线制分析仪,可选择单传感器或双传感器测量。
-
FLXA402多通道四线制分析仪
FLEXA™系列分析仪是模块化设计的分析仪,用于在工业设施中进行连续在线测量。可提供单传感器或多传感器测量。
-
Immersion Holder FD20
The immersion fittings are designed for either pH or ORP (Redox) measurements in tanks, open vessels and drains. They have a "hoisting cable" for easy maintenance.
-
pH和ORP分析仪
pH和ORP流量计、分析仪和变送器用于pH和ORP的连续过程监测,以确保水/产品质量,如监测污水排放、批量中和、浆料存储、洗涤塔,冷却塔、化学品、水/废水处理和许多其他应用。