Plant managers are amidst a fast-changing business environment. Trends of Industry 4.0, advanced technologies of Industrial IoT (IIoT) & artificial intelligence(AI), and the rise of the energy-saving society and aging population have huge impacts on production activities. Under this situation, they must consider how to improve productivity and safety, train and sustain experienced operators, and cut operation costs all at the same time.
An important approach to address these challenges is to promote DX (Digital Transformation) in production activities. To enable this, the critical action is digitalization -- make the invisible performance of plant assets visible in a digital format.
Within the asset management domain, low-cost wireless monitoring technologies are disrupting portable condition monitoring (CM) and more traditional preventive maintenance activities such as walk-around inspections. To track asset health and performance, online diagnostics CM is rapidly transforming to become predictive, where data is translated into actionable insights with guaranteed outcomes through digitalization.
Asset Performance Management (APM) is a leading-edge solution to make asset performance monitorable, analyzable and integrated across the entire plant – all of which are also preconditions promoting DX to ultimately achieve a profitable and sustainable plant.
-
A Wireless IIoT Solution Sushi Sensor
Sushi Sensor is a wireless solution for Industrial IoT (IIoT). It has excellent environmental resistance, and adapts LoRaWAN®, a wide area wireless communication method that realizes power saving and long-distance communication.
-
OpreX Asset Health Insights
Unified cloud-based asset management and monitoring service to eliminate unplanned downtime and increase operational efficiencies.
Details
Asset Performance Management (APM) is a leading-edge solution to make asset performance monitorable, analyzable and integrated across the entire plant – all of which are also preconditions promoting DX to ultimately achieve a profitable and sustainable plant.
Click here to learn about Asset Performance Management
Key areas for Operational Excellence Transformation
Operational Excellence Transformation is Yokogawa and KBC’s co-innovated portfolio of solutions and services. We provide comprehensive solutions for business automation in all four areas using consulting and digital technology.
Asset Management and Integrity
Asset Management and Integrity practices are critical to ensure the reliability and availability of such assets while keeping maintenances costs to a minimum, and to capitalize on short-term opportunities in the market. With domain knowledge and experience, Yokogawa and KBC ensure its customers maximize their assets' value through asset management and integrity products, services and solutions.
Key Operational Competencies in Asset Management and Integrity
- Maintenance and Integrity Strategy: Determine the best asset maintenance and integrity strategy based on equipment integrity objectives, as well as corporate and asset portfolio strategies
- Asset Care Planning: Provide systems and methodologies to optimally define the activities needed to maintain equipment in its designed operating conditions
- Reliability Assurance and Analytics: Provide analysis of equipment health to determine the best maintenance approaches.
- Defect Elimination: Identify activities that mitigate and eliminate sources of unreliability to assets or facility systems
- Inspection: Review inspections performed on equipment to identify specific maintenance activities. This will be done in coordination with, or by, the inspection group.
- Contractor Management: Manage contractors to utilize their services efficiently and effectively
- Minor Projects Delivery: Screen options, engineer and deliver low- or no-capital projects to replace existing equipment or achieve incremental improvements that are cost-effective, timely and fit for purpose
- Turnaround Maintenance: Perform special equipment maintenance to retain asset design and operational integrity. This involves longer shutdowns or outages of the unit or the system.
- Routine Maintenance: Perform normal equipment maintenance during operations to retain asset design and operational integrity. This involves short-term or low-impact shutdown of the unit or the system.
In addition, through Yokogawa’s reliability-based Asset Management portfolio, our customers can:
- Contribute directly to corporate goals and objectives; We help our customers assess and design how they utilize their assets to achieve the following:
- Reduction in production cost per unit
- Reduction in unplanned breakdown of assets
- Increase in efficiency of maintenance operators
- Reduction in safety and environmental-related incidents
- Enable informed and operations-centric decision-making
We combine risk and reliability best practices with our customers’ actual plant operations set up to identify and focus on critical assets that drive the largest contributions in their company. By identifying critical assets – failure root causes and recommended actions – resources and requirements are prioritized accordingly, in consideration of associated risks and consequences.
·Supply Chain Optimization
- Optimize management of supply, whether oil in the ground or feedstocks for a refinery or chemical asset, in light of product market demands. This provides operators with the agility to take full advantage of market conditions.
·Asset Operations and Optimization
- Optimize the potential of physical assets, by pushing throughput and maximizing the production of the highest value products, whilst minimizing variable costs such as energy.
- Deliver small and large CAPEX projects, on time and on budget, to deliver growth and meet environmental requirements.
·Operational Risk Management
- Reliably control safety, health and environmental risk at a personal and process level. This assures the robustness required to avoid catastrophic losses.
Customer Challenge
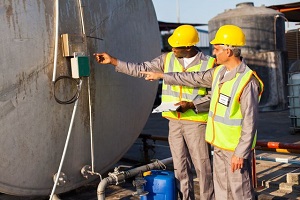
In most production sites, the equipment for plant control is the core of all the systems; plants are initially configured based on such core equipment to achieve production optimization.
Other utilities, which are not classified as core equipment yet still necessary, are also installed in the plant to support stable production. Usually, these are not integrated with the DCS system to save costs. Instead, walk around inspections by operators are executed to detect asset failures.
For further cost reduction, reducing the frequency of the walk-around inspection is an option. However, this results in decreasing the occurrence of early failure detections, which leads to unnecessary post-failure processing and higher susceptibility of failure risks affecting production, as well as overall plant reliability, safety and profitability.
Asset performance management (APM) is an appropriate solution to overcome this challenge.
Our Solutions
Our solution is to integrate process data with remote utilities asset data in the Yokogawa cloud platform, then utilize such data for production optimization. With the Asset Performance Management (APM) solution, an environment that enables cross-sectional analytics of the process data and asset data can be established. This will be one of the key digitalization actions to achieve the business and financial goals of our customers.
The integrated data stored in the cloud can be used not only within plant premises, but also worldwide with the right access. Through this data environment, asset data, which is more accurate due to high collection frequency over than those of walk around inspections, can be combined with real-time process data in high-accuracy analytics.
This feature also provides an essential environment for consulting services related to production optimization. Using plant-wide information, Yokogawa and KBC’s professional consultants, who have a wealth of domain knowledge about plant operations, can evaluate the balance between risks and costs, and provide suitable suggestions for improvement from both business and production perspectives.
Generally, professional consultants support multiple plants simultaneously to provide holistic advice. Due to time and distance constraints, however, it is difficult or impossible for such consultants to visit the production sites they monitor.
Asset Performance Management (APM) is exactly the right solution to solve this problem. It can collect sensing data and store them in the cloud, making it possible for professional consultants to access data remotely. For this reason, Asset Performance Management (APM) can boost customers’ sense-making of data from anywhere.
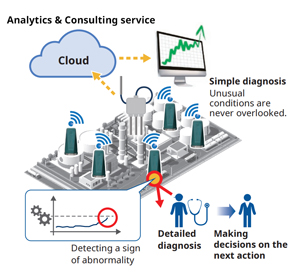
Customer Benefits
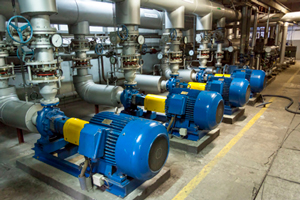
From a plant-wide perspective, Asset Performance Management (APM) offers customers multiple benefits, such as:
- Achieving plantwide data monitoring of core equipment and other utilities to avoid failures before they occur. This reduces plant downtime and lowers plant operation risks.
- Dramatically cutting down the burden and cost of daily patrol inspections. Instead, automatic data monitoring will be enabled, resulting in more accurate and objective monitoring
- Ensuring reliable and best-in-class-domain-based decisions through remote data monitoring and consulting. Experienced operators and/or professional consultants can monitor, analyze and recommend solutions from anywhere and anytime, thus eliminating the risk of lacking knowledgeable experts
From a DX strategy perspective, implementing Asset Performance Management (APM) can accelerate the digitalization of any plant. That is, realizing a plant with more trusted data, improved decision-making agility, broadened view of optimization, extensive use of automation and enough empowered people.
Enabling Technology
Asset Performance Management (APM) is an integrated solution, which covers advanced sensing technology, cloud service, artificial intelligence(AI) technology, analytics and consulting. Yokogawa provides the necessary enabling technologies, combined with advanced sensor devices, domain knowledge and abundant industry expertise.
For sensing, we provide the Sushi Sensor as a wireless Industrial IoT (IIoT) solution to collect asset data across the plant. Key features of the Sushi Sensor are:
- IIoT sensor with excellent environmental resistance
- Easy setup and installation via smartphone
- Two options of data monitoring: cloud and on-premises
For data integration environment, Yokogawa has both cloud and on-premise solutions for plant data monitoring platform. The platform includes a group of standard functions such as data collection, storage and sharing, as well as a KPI dashboard, trend graph monitoring, threshold alarms and notification services. All these functions are ready for quick deployment together with the Sushi Sensor.
Based on this cloud data platform, data can be integrated across the plant and be seamlessly accessible for advanced analytics using AI and machine learning technologies. The professional consultants of Yokogawa and KBC can evaluate risks, provide advice and support services based on their best-in-class domain knowledge and abundant industry expertise.
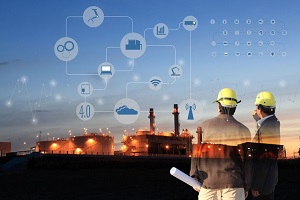
Zdroje
Downloads
Brožury
Všeobecné specifikace
- XS110A Wireless Communication Module (939 KB)
Výkresy
- XS110A Wireless Communication Module (740 KB)
Novinky
Potřebujete víc informací o lidech, technologii a řešeních?
Kontaktuje nás