A terminal or large depot is a storage area where Oil, Gas, or Chemical products are received through cross-country pipelines, tanker trucks and/or marine vessels, which are then stored in a tank farm. These products are re-distributed by truck, barge, rail car, or other means. Yokogawa has accumulated more than 2 decades of experience in terminal automation and offers comprehensive knowledge and expertise in improving your logistic operations.
Click here to learn about Off-site & Terminal Management
Key areas for Operational Excellence Transformation
Operational Excellence Transformation is Yokogawa and KBC’s co-innovated portfolio of solutions and services.We provides comprehensive solutions for business automation in all four areas using consulting and digital technology.
Supply Chain Optimization
Supply Chain Management deals with satisfying customer demands by selecting the most appropriate feedstocks the plant can process efficiently, and delivering the products to the customers with maximum efficiency. Today, most of the industry SCM solutions are executed manually and/or separately. In most cases, specialized planning and software packages that have been implemented previously are not connected to other systems, such as sales and distribution and real-time production systems. As a result, the benefits of SCM are not fully realized.
Yokogawa's strategy to improve supply chain management starts with defining the corporate long-term strategy and aligning it with operations, maintenance and all other functions involved in the entire value chain. It includes:
Key Operational Competencies in Supply Chain Optimization
- Term Contract Planning: Commercial and economic evaluation of long-term contract obligations
- Supply Chain Planning: Economic optimization of the hydrocarbon supply chain for short-term, mid-term, long-term and strategic time horizons
- Price Deck Formulation: Generate price forecasts based on optimization boundaries and time horizons for feedstock and products
- Supply Chain Scheduling: Schedule optimized operations (process inventory and blending) over time, taking logistical constraints into account
- Commercial Contracting: Develop and negotiate favorable and competitive contract terms for feedstocks and products
- Inventory Management: Measure and reconcile the amount of each product made and raw materials consumed to produce an accurate material balance through production accounting and oil loss measurement
Yokogawa's approach to supply chain management involves digitalizing operations from supply to distribution. We then adopt the identified end-to-end optimization strategy to discover and manage all hidden costs (wastes) in the long chain. Our main objective is to find the Global Optimum to enable Just-in-Time in manufacturing and delivery for suppliers and customers, using minimum inventory and movement.
By applying digital technologies onto the end-to-end process of the supply chain (manufacturing raw materials to final products and managing purchase orders to good receipts), we may be able to improve the following:
- Customer & Supplier Experience: Deliver personalized engagement with an improved understanding of the product value directly to customers and suppliers
- End-to-End optimization: Extend the optimization horizon using real-time information on supplier delivery and customer demand across organizations and companies involved in the long supply chain
- Information Mobility: Enable optimal delivery and visibility by tracking personal location and activities with mobile technology
- Predictive Insights: Anticipate demand, supply and asset requirements with better insights
- Digital Business: Improve overall business agility and borderless collaborations by eliminating internal information silos
By combining Yokogawa’s product portfolio and KBC’s consulting services, we provide our customers best practices and domain knowledge that empower them to improve their operations, as well as a digital platform that supports such activities and initiatives. Our Operational Risk Management scope does not only cover partial improvements in the organization, but also optimizations in plant operations to achieve continuously improving safety, reliability and operability.
·Asset Operations and Optimization
- Optimize the potential of physical assets, by pushing throughput and maximizing the production of the highest value products, whilst minimizing variable costs such as energy.
- Deliver small and large capex projects, on time and on budget, to deliver growth and meet environmental requirements.
·Operational Risk Management
- Reliably control safety, health and environmental risk at a personal and process level. This assures the robustness required to avoid catastrophic losses.
·Asset Management and Integrity
- Confidently ensure asset reliability and availability, whilst controlling maintenance costs. This assures the asset always meets expectations and is always available to capitalize on short term market opportunities.
Off-site & Terminal Management
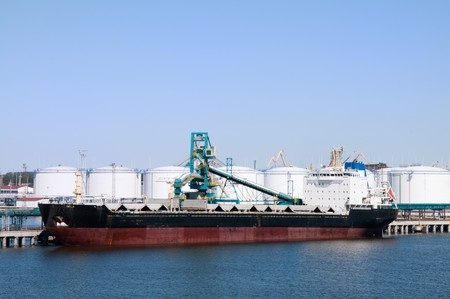
Off-site Movement, Blending, and Terminal Management Solution
A terminal or large depot is a storage area where Oil, Gas, or Chemical products are received through cross-country pipelines, tanker trucks and/or marine vessels, which are then stored in a tank farm. These products are re-distributed by truck, barge, rail car, or other means. Yokogawa has accumulated more than 2 decades of experience in terminal automation and offers comprehensive knowledge and expertise in improving your logistic operations.
"Refining" is a process to produce various oil products from crude oil, to blend them into the final products and to ship to the decided destinations. In the refinery, process units called "on-site facilities". The other facilities in the refinery is called "off-site facilities" including storage facilities, oil movement facilities and blending facilities, etc. Yokogawa proposes the solutions for automating and optimizing the off-site operations.
Customer Challenge
Shipping Customer Orders Within the Quality, Safely, Efficiently, and Accurately is a Perennial Problem in Terminal Operations
A typical medium size terminal has more than 1,500 transfer operations a day, and countless sub-operations (line clearances, heating, circulation, etc.)
- Every transfer and sub-operation needs to be tracked and recorded in detail, so that it can be charged to the client
- Contamination & Demurrage caused by operation mistakes and equipment
- Complexity due to multiple clients sharing resources
- Uncertainty caused by shipping schedule, assets availability, parcel availability, etc
- Gain/Loss accounting
- Identification of shrinkage
- Traffic Management
- Blending
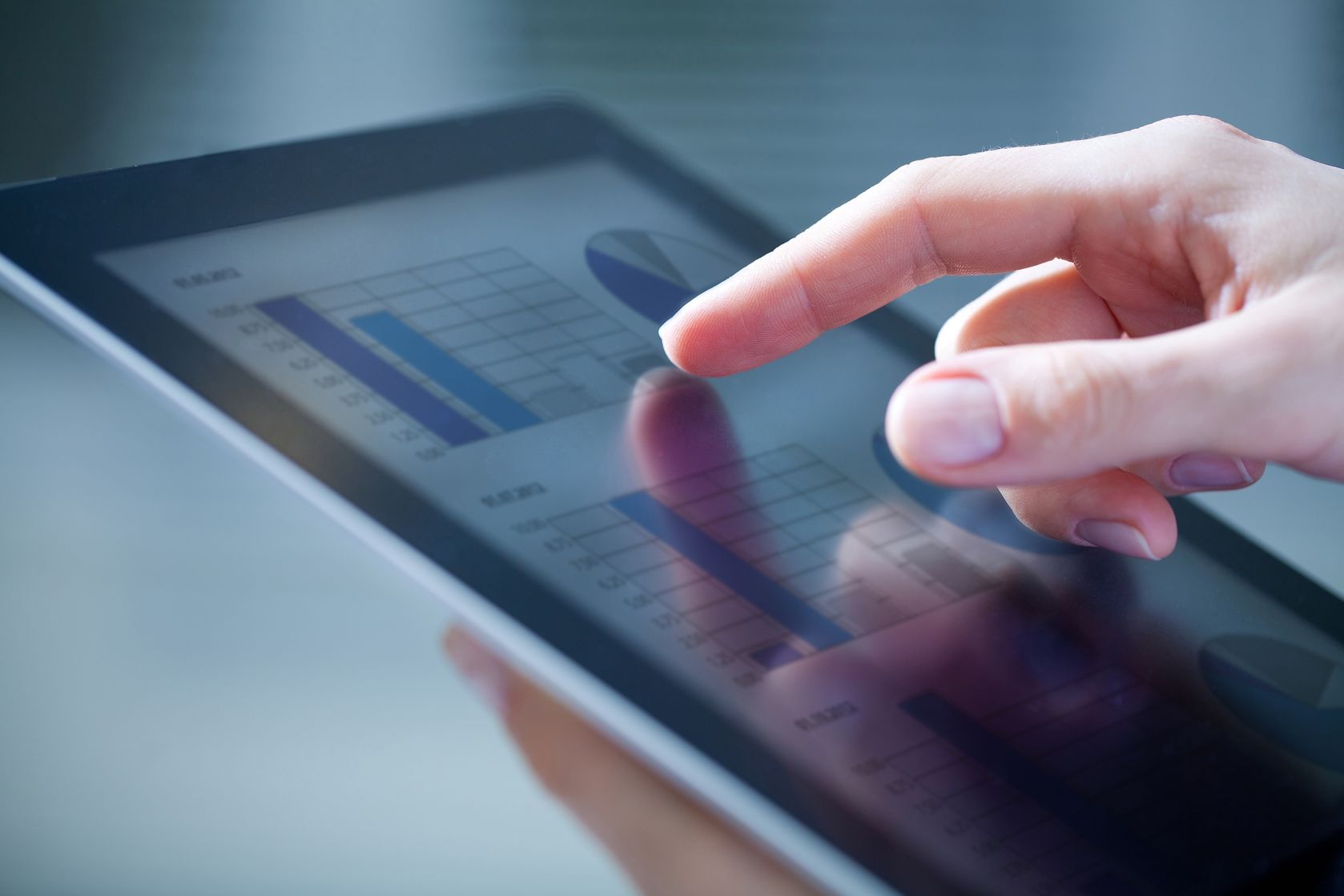
Our Solutions
Oil Movement Suite VP(OMSVP) & Terminal Logistics Suite VP (TLSVP)Helps You Overcome Your Challenges
Improve Safety: Interlock procedures to avoid mis-operations, and integrated smart-alarm management to help reduce operator load, improving overall safety
Improve Efficiency: Enabled by automated equipment scheduling, flexible route optimization, and blend recipe optimization. Together, these three ensure minimized turnaround time with optimized inventory usage
Improve Availability: Due to the inbuilt intelligence, OMSVP and TLSVP automatically re-route operations around failed equipment ensuring optimum terminal operations. OMSVP and TLSVP is able to provide this capability due to its integration with leading edge Plant Asset Management systems.
Improve Human Reliability: Simulated operations allow operators to learn in a safe environment - Advanced Operating Graphics supports the trained operators by making complex operations clear and simple, focusing on the most important tasks at hand - but when mistakes do happen, we catch them... the system will then track equipment services to avoid contamination
Customer Benefits
Increased Profit & Increased Availability by Overcoming Logistic Challenges
Reduce Demmurage for Vessel, Just in-time Delivery
- Precise and speedy operation result in less demmurate
Tracability of Operation, Materials, Products, Quality
- Event and operation is recorded sot
Support the Business Process from Purchase Order to Payment
- Seamless connectivity to ERP, business process and control process integration help operation more efficient and robust
Support to Keep Operation Safety, to Keep Quality Correct, to Keep Turn-around Time Short
- Precise instruction and accurate control results in improving turn-around time
- Procedural operational support improve safety without making mis-operation
Increase Profit
- Real-time Loading/Unloading information and inventory data helps to optimize operation
- Speed-up operations precisely
- Operational assists by the system lead to less mis-operation
- Optimization in logistics by using most efficient route, reducing line flushes
- Eliminate contamination
- Real-time terminal data ensures business sustainability
- Data tracking ensures quality throughout the whole process
Increase Availability
- Real-time inventory data ensures loading and delivery
- Equipment run-time monitoring provides maintenance timing to keep equipment functioning properly
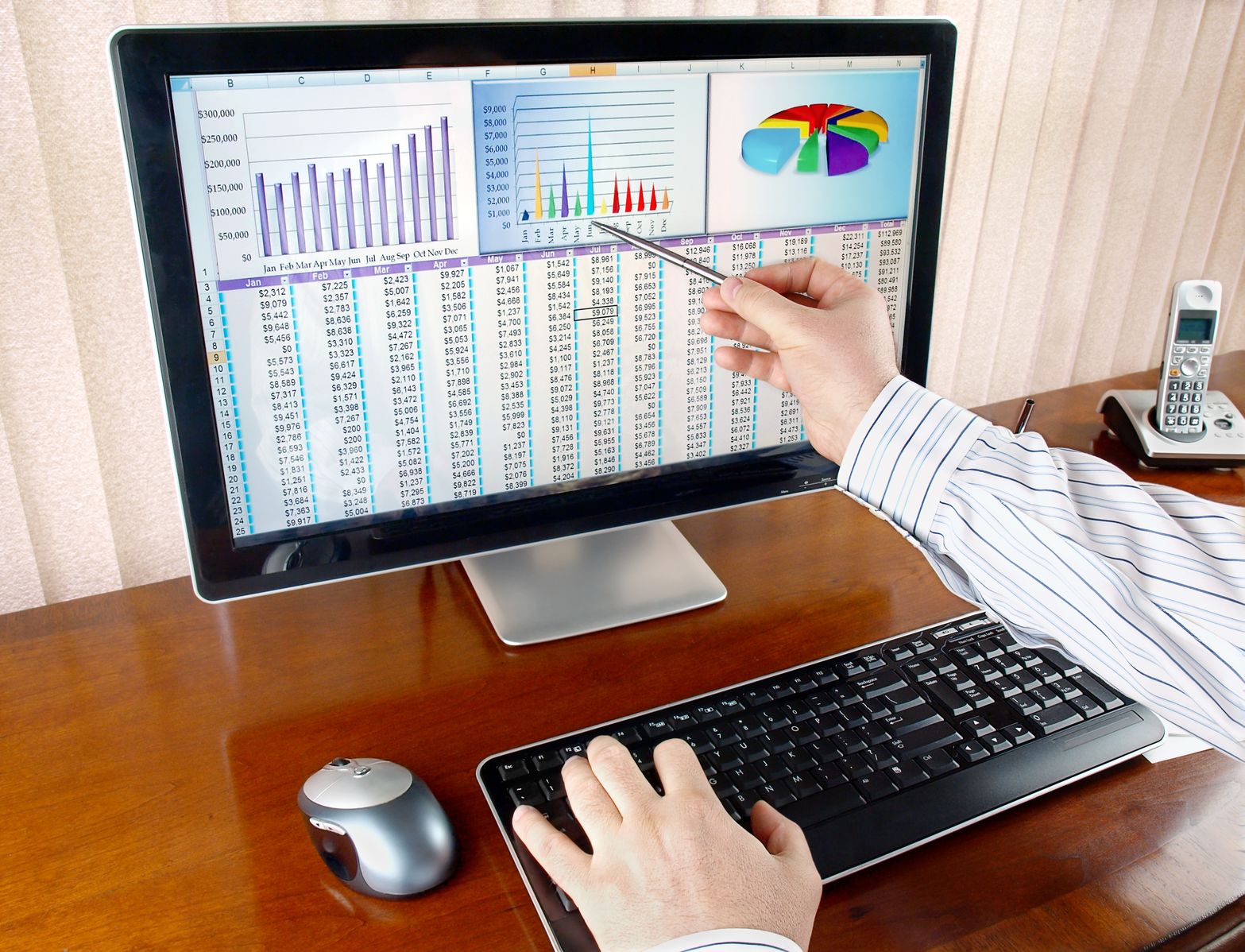
Cerchi più informazioni su tecnologia, soluzioni o sulla nostra squadra?
Contattaci