At Yokogawa, we understand that today’s food and beverage companies face unprecedented challenges in climate change, consumer demand, and increased global competitiveness. Overcoming these challenges will require innovative solutions that focus on key areas of production, asset management, and food safety and quality.
Optimized Production
As consumers continue to demand ever-evolving product offerings, food and beverage manufacturers must find ways to improve efficiency and maximize production. Yokogawa’s solutions include measurement and data analysis tools that improve process control and profitability.
Asset Management
Keeping plant assets continually available and profitable requires custom management solutions. Yokogawa’s portfolio of asset management instrumentation identifies failures before they happen, implementing predictive intelligence and integrated protection technologies to improve bottom lines.
Food Safety&Quality
Shopping at the grocery store or opening the refrigerator, products must exceed consumer expectations and meet compliance regulations. Yokogawa works with food and beverage companies around the world, using cost-effective tools that ensure uncompromised, high-quality results.
Bio
From raw material procurement to the production of high-quality food and beverages, Yokogawa has the control and automation expertise to solve your greatest manufacturing challenges and improve your data management, product quality, reliability, and operating costs.
Digital Transformation
With Yokogawa’s automation technologies and extensive field experience, food and beverage companies can customize our digital solutions to fit every need, improving safety, efficiency, productivity, and sustainability.
Well-being
By continuing to develop new automation technologies, Yokogawa helps companies transform their manufacturing environments, freeing workers up to concentrate on higher value-added work.
Upcoming Events
-
Conference Jul 22, 2024 - Dec 31, 2027 Singapore, Indonesia, Malaysia, Philippines, Thailand, Taiwan, Australia & New Zealand, VietnamSustainability Assessment (COSIRI) – Guided Pathway towards Sustainable Food Manufacturing
The Sustainability Assessment COSIRI -Guided pathway towards Sustainable Food Manufacturing was featured in the Yokogawa Philippines Food and Beverage _Modernerization and Innovation Summit-Exhibition-22-23May2024. Learn about Sustainability Assessment enables food factories to formally assess their current level of sustainability. The assessments provide companies with invaluable insights into risk and gaps and what can be done to improve their standing. To help food companies pace their sustainability initiatives, the assessment provides a benchmark of company’s position against industry peers. # Decarbonisation #SustainabilityAssessment
Details
Optimized Production
Yokogawa designs control and automation solutions to help provide a secure, safe, and sustainable manufacturing process. By utilizing our instrumentation, companies get the right information to the right people at the right time.
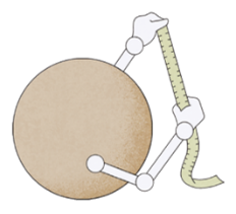
Measurement
Our advanced measurement technologies deliver real-time, actionable insights into the manufacturing process, preventing unnecessary downtime and improving bottom-line profitability.
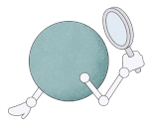
Analysis
Today’s operational challenges demand optimal control, coordinating users and devices simultaneously. No matter what a project requires, Yokogawa has the expertise and advanced technologies to solve even the toughest process challenge.
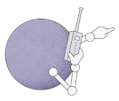
Integration
With so many vital data sources, seamless integration is essential. Our analysis tools deliver information from the field to the office, improving efficiency and enabling well-informed decisions.
Asset Management
Implementing a proactive reliability management strategy is a key component of every successful plant. Yokogawa’s asset management tools provide clarity on facility ledgers, factory stability, safety, and maintenance planning, preventing failures and downtime.
Food Safety & Quality
Protecting against contamination, ensuring the highest product quality, and reducing regulatory compliance risks are critical for success. Yokogawa’s predictive technologies identify problems before they happen, preventing costly recalls.
Resources
Shree Renuka Sugars Limited (SRSL) is a global agribusiness and bio-energy corporation. The company is one of the world’s largest sugar producers and refiners.
Yokogawa provided Mewah, one of the largest vegetable oil processors, with a structured Smart Manufacturing Assessment Workshop.
The company's Industry 4.0 roadmap was clarified through the Smart Industry Readiness Index (SIRI) based workshop.
NISSIN FOOD PRODUCTS selected Yokogawa as a partner to realize a next-generation smart factory.
An integrated MES solution helps fully automate the large-scale food factory in Japan.
- Yokogawa provided control solutions for expansion project in sugar and bio-energy plant.
- Consolidated central control room was designed for safe, comfortable, and efficient work environment.
S&B Sankyo uses the GX20 Paperless Recorder to monitor temperature and pressure in a food processing plant's sterilization process.
Rousselot Ghent won Belgium Factory of the Future Award. Yokogawa has supported Rousselot with automation systems since 1993.
Data of 20,000 tags gathered by Exaquantum helped to find the ideal production parameters.
Kyowa Hakko Bio monitors vibration trends with Yokogawa's Sushi Sensors to prevent unexpected equipment failures.
By using eServ, sensor data and maintenance information are shared with everyone involved in manufacturing.
The introduction of eServ has resulted in a centralized system of facility information. The reason for the loss of production opportunities has become clear, and it has become possible for all members to follow up the progress of the measures.
The TC series of temperature controllers is perfect for controlling the heating temperature of sealing parts and the temperature of sealing rolls (pre-heating) in a variety of different wrapping machinery.
- The new package software running on the CENTUM CS 3000 has enabled flexible configuration and data settings for greater productivity.
- The CENTUM CS 3000 features a standard long-term trend function that can store a year's worth of data on more than 200 tags that are sampled at 2 minute intervals.
One of the critical control points in the brewing process is the monitoring of the progress of the fermentation stage. The DM8 Vibration Type Liquid Density Meter offers high sensitivity and stability, realizes precise control, reduces workload, and reduces instrument costs.
Skim milk is what remains after cream is removed from raw milk. Cream is removed to bring the fat content of the skim milk as close as possible to the lower limit of a designated range. For this purpose, control of the fat content in the cream and the skim milk is essential. The fat content in the cream and the milk has a direct relationship to their density and is controlled by the measurement thereof.
- For remote monitoring (of temperature, pressure, and flow volume), installing the SMARTDAC+ GM in the plant and the SMARTDAC+ GX in the office provides for a scalable, pc-free on-site data monitoring solution.
- You can centralize management of large quantities of data by automatically transferring acquired data to a FTP server.
The discharge of improperly treated industrial chemicals and fuel gas can have a major impact on the environment, posing a serious threat to public health. Concurrent with the global growth of manufacturing operations to keep pace with market trends, many countries are taking measures to deal with environmental problems.
SMARTDAC+ GX series records the clean room temperature, humidity, atmospheric pressure, door openings and closings, etc.
Milk should be processed within 4 to 6 hours of production to make it fit for human consumption. Temperature is a very important parameter which has to be monitored at different stages of milk processing.
What if you could detect signs of abnormalities in bus ducts (bus bars) quickly during maintenance and inspection work and respond to them at just the right time? Yokogawa DTSX monitoring solution constantly monitors connections that tend to deteriorate over time and contributes by pinpointing abnormality locations and reducing workload of maintenance personnel, helping to ensure stability in plant operations.
In the plants of food and beverage manufacturers, there are times when monitoring and recording of production equipment is necessary inside clean rooms. This is an introduction to monitoring and recording in clean rooms using paperless recorders.
In the food industry, the control of concentrations on the production line is critical to product quality, determining, among other things, how good the food tastes. One such procedure for doing this involves taking a sample from the production process and measuring its specific gravity (density) with a hydrometer.
Brewery is facility to produce beer. Breweries process is the manufacturing process of beer, which is a fermented beverage with low alcohol content made from various types of grain. Wheat, maize and other grains can be used for this. Brewing process starts from malted barley that is to form a mash by milling and mixing with hot water. The malt starches are converted to sugars during this process. This sugar rich water is then strained through the bottom of the mash and will be called as "wort". Then the wort will be brought to boil by bringing to the brew kettle. For bitterness or aroma hops are to be added at different times during the boil. Then the wort is cooled and aerated. And brewers yeast is added for fermentation. From the sweet wort the yeast produces carbon dioxide, alcohol and other byproducts. The GREEN BEER undergoes maturation after fermentation. Filtaration and carbonation are the last steps. Finally the beer will be stay in holding tank until it is bottled or kegged.
The paperless recorder DX series automatically calculate the Fo value from the heating temperature and are useful in managing the sterilization process by displaying and recording the value together with the heating temperature.
By using the Multibatch function (an option added with SMARTDAC+), you can efficiently record data from multiple devices onto a single SMARTDAC+.
Using the custom display function that comes standard with DXAdvanced means that you can combine the recorders, displays, and switches used in various kinds of equipment.
Using the batch name + lot number system, past measured data can be recalled for reference by batch name.
Yokogawa's ceramic liner can offer the customer superior resistance to thermal shock and the failure that can occur due to liner cracking. This is due to Yokogawa's use of 99.9% pure Al2O3 for the liner.
- Universal inputs provide support for thermocouple, RTD, voltage, and a variety of other input signals.
- Lineup of models for up to 450 inputs.
Allows multipoint monitoring and recording on a single unit. - Easily enables network-based data management.
file transfers, Web monitoring, and alarm e-mail
By using the computation function of the SMARTDAC+ series Paperless recorder GX/GP, computation option computes the "F-value," or sterilizing value for the sterilization process, so that the computation results can be recorded in the form of data.
With industrial and economic development comes increasingly large and advanced power plants and factories. Nevertheless, we find many cases where the original cables, cable tunnels, and other components of the power infrastructure have languished under continuous operation.
The sterilization temperature prior to the filling process is monitored in the field or office. The temperature data is recorded in an external storage medium.
Fish perform all their bodily functions in water. Because fish are totally dependent upon water to breathe, feed and grow, excrete wastes, maintain a salt balance, and reproduce, understanding the physical and chemical qualities of water is critical to successful aquaculture. To a great extent water determines the success or failure of an aquaculture operation.
- Temperature monitoring at a tank farm
- Temperature and pressure monitoring in tank jungles, three vertical monitoring points.
This introduces a system that uses Ethernet communications to acquire measured values, target values, and control output values from a controller installed on site into a PLC at high speed (ten units' worth within one second).
To defray energy costs, many industrial plants have their own boilers to generate steam in order to produce a portion of their energy needs. In addition to generating power, the steam may also be used directly in plant processes or indirectly via heat exchangers or steam jacketed vessels.
With advances in process automation comes a greater need for level measurement and control. As pressure on at the bottom surface of a liquid is proportional to the height of the liquid's surface, you can measure pressure using a differential pressure transmitter to detect the level of the liquid, acquire the data on the UT75A Digital Indicating Controller, and use the measurements to control the tank level.
In the manufacturing process of Pharmaceutical, Chemical and Food & Beverage industries, the cleaning and sterilization of tanks and piping are done with various cleaning solutions, fresh or hot water and steam after manufacturing products. Clean-In-Place (CIP) is the system designed for automatic cleaning and disinfecting.
Reverse osmosis (RO) is a separation process that uses pressure to force a solution through a membrane that retains the solute on one side and allows the pure solvent to pass to the other side. More formally, it is the process of forcing a solvent from a region of high solute concentration through a membrane to a region of low solute concentration by applying a pressure in excess of the osmotic pressure.
After extraction from sugar cane or sugar beets, juice must be purified to remove the many other organics and minerals that accompany it. The processing to accomplish this is heavily dependent on reliable pH measurement and control as illustrated.
One of the primary applications for high purity water is for boiler feed water. The measurement of pure water pH can be one of the quickest indicators of process contamination in the production or distribution of pure water. Effective chemical treatment of the feed water is vital in maintaining the useful operating life and minimizing maintenance costs of the boiler.
Temperature plays a key role in storage of Molasses to maintain the chemical properties of molasses. When temperature rises over 40.5 degree C, destruction of structure in sugar occurs, which results in losing the feeding property of molasses. There is also a safety concern that a rise in temperature can lead to a rise in storage tank pressure leading to an explosion of the tank.
Measurement and control of Heat Exchanger Leakage can help prevent costly maintenance, repair and downtime. The simple, essentially maintenance-free measurement of condensate conductivity will give the operator information necessary (or provide automatic control) to prevent severe damage to the boiler should a breakthrough of the heat exchanger occur.
Ion Exchange is a method for the exchange of ions between two electrolytes or between an electrolyte solution and a complex molecule. In most cases the term is used to denote the processes of purification, separation, and decontamination of aqueous and other ion-containing solutions with solid polymeric or mineralic ion exchangers.
There are numerous industrial applications where measurements and/or control of a specific chemical strength of the process is critical for optimizing the production of the end product. These specific concentrations are obtained by mixing a full strength solution with water to achieve the desired percent concentration.
Optimizing four key factors will decrease pH sensor costs and optimize process control and overall plant efficiency.
This technical white paper will discuss Yokogawa's CENTUM VP DCS (Distributed Control System) product, hereafter referred to as "CENTUM VP", and the extent of its compliance with Part 11 of Title 21 of the Code of Federal Regulations, (21 CFR Part 11), the Electronic Records / Electronic Signatures Rule.
Sugar and alcohol market are increasing, due humanity needs to find alternatives for fossil fuels dependence. Brazil joins climactic and technologic features to place itself at the forefront of this industry.
The worlds of process automation and production management have been converging for some time. What once used to be islands of automation and production management functionality connected through highly proprietary integration schemes that were costly to maintain have developed into integrated platforms that provide seamless data exchange between the world of automation and the plant floor, the functions of production and operations management, and integration with business level systems.
The world of process automation is governed by procedures. While we like to refer to the process industries as being largely "continuous", this could not be further from the truth. Process manufacturing is constantly in flux.
This document describes the operation and data flow of the Yokogawa Print Wave software using the DX-P Reporter. It will provide a detailed explanation of the Advanced Alarm Reporter functions. The functions described in this paper were first released in Print Wave version 5.5.
Discovering your Baseline with OT Security Risk Assessment
Honeywell and Yokogawa have both been producing Distributed Control System (DCS) platforms for decades, and both are very active in this area. In 1975, Honeywell introduced its TDC2000 platform and Yokogawa brought out CENTUM. These two competing systems emerged from a similar place, oil refining and petrochemical industries, so they started out with similar basic concepts and use cases in mind.
Downloads
Brochures
General Specifications
Certificates
Videos
The Yokogawa business vision states that the company endeavors to achieve Net-zero emissions, ensure the Well-being of all, and make a transition to a Circular Economy by 2050.
YOKOGAWA will contribute to technology evolution particularly in measurement and analytical tools to help build a world where researchers will increasingly focus on insightful interpretation of data, and advancing Life Science to benefit humanity.
Open up control. Open Process Automation (OPA) opens the door to expanded choices, leverage, and customization.
Create a scalable, sustainable architecture. Remove the restraints of proprietary systems. OPA enables you to leverage all available technologies to open up solutions. Explore the possibilities today.
YOKOGAWA creates autonomous operations with high-efficiency automation and optimization that allows growth with minimal deployment of manpower.
Our approach is to leverage state-of-the-art technologies for real-time monitoring and predictive control that allow virtual environments where "digital twin" processes can provide distinct advantages.
As a gateway to further expand Yokogawa's messaging as a One-stop Solution Business, Yokogawa has partnered up with INCIT, to introduce the S.I.R.I. framework.
News
Looking for more information on our people, technology and solutions?
Contact Us