The VERIS Accelabar® is a unique flow meter that combines two differential pressure technologies to produce an operating range never before attainable in a single flow meter. Combining a unique toroidal nozzle design with the VERIS Verabar® averaging pitot tube, Accelabar is capable of measuring gases, liquids, and steam at previously unattainable flow rate turndowns tested up to 65:1 with no straight run requirements.
The Accelabar can be installed as the primary element of a differential pressure flow measurement solution using the proven technology of the VERIS Verabar® averaging pitot sensor. In addition, the VERIS Accelabar® can be furnished as a ready to install flow meter system complete with the primary element, configured transmitter, and RTD, along with other secondary instrumentation. Yokogawa offers multivariable transmitters that can be used as a secondary element depending on the need of a volumetric flow rate or mass flow rate.
Using Accelabar as the primary element and Yokogawa’s pressure transmitters with DPharp technology as the secondary instrumentation delivers the following advantages:
- Accuracy: up to ±0.5% of rate over the entire flow range
- Repeatability: ±0.05% over the entire flow range
- Turndown: up to 20:1
- Line Sizes: 1 inch to 12 inch
- Reduced cost of installation
Accuracy
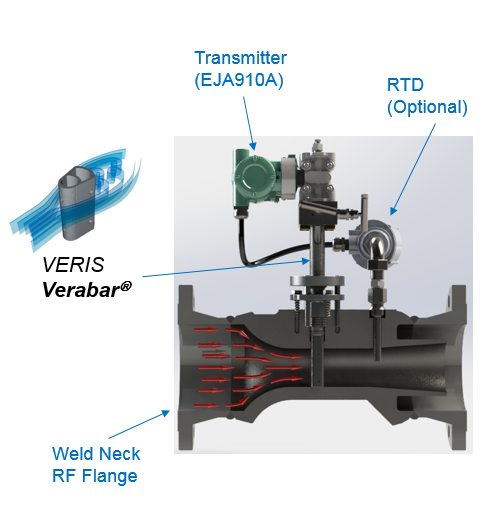
The Accelabar’s flow nozzle is specifically designed to accelerate, condition, and linearize the velocity profile for Verabar averaging pitot to measure the differential pressure accurately.
Repeatability
The Verabar is a bullet shape averaging pitot with low-pressure ports located forward of the fluid separation point. The Accelabar precisely locates it within the stabilization zone. Here it measures the DP output to increase the rangeability (turndown). The design produces a constant flow coefficient; yielding high repeatability. It is the only design capable of providing this overall performance.
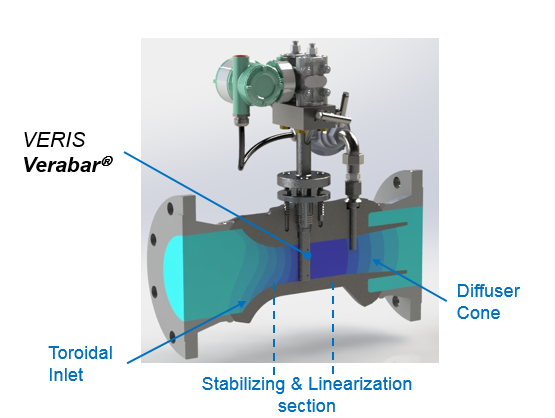
Details
Optional RTD
An optional RTD can be supplied in a thermowell for dynamic compensation of mass flow rates. With the optional RTD, there is no need for an external temperature sensor or an insertion hole in the pipe, which increases safety standards.
No straight run required
The VERIS Accelabar® can be used in extremely limited straight run piping configurations. All necessary straight run is integral to the meter. The stabilization and linearization of the velocity profile within the throat of the nozzle eliminate the need for any upstream or downstream pipe runs, reducing maintenance and initial costs.
High turndown
Other flow meters may not have sufficient fluid velocity to generate adequate turndown. The Accelabar has a nozzle that significantly increases the differential output, increasing the operating range. Depending on the flow conditions, Accelabar can have a turndown ratio of up to 65:1.
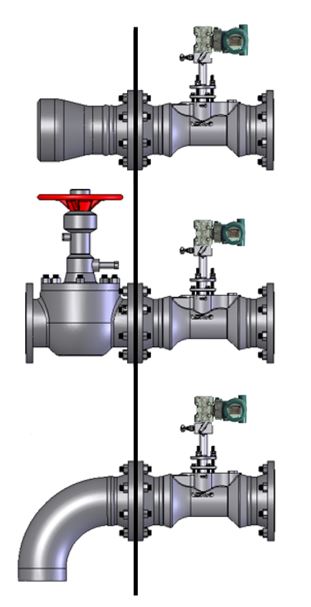
Patented design
The VERIS Verabar® located within the nozzle accurately measures the fluid’s velocity profile due to the nozzle’s patented “settling distance” design, which accelerates, linearizes, and stabilizes the velocity profile.
Wide Variety of Special Materials Available
Beyond standard model designs, the Accelabar is available in an array of exotic materials, connections, and dimensional configurations to better fit unique applications.
Natural Gas
The VERIS Accelabar® is used to meter gas flow to heaters that vaporize LNG to gaseous natural gas for use during peak periods in the winter season. The VERIS Accelabar® was the only solution able to meet installation, turndown, and reliability requirements.
Application | 3” Sch 40 Natural Gas |
---|---|
Flowing Pressure/Temp | 80 PSIG/70°F |
Max/Min Flow Rate | 60,000 SCFH / 1,000 SCFH |
Flow Turndown | 60:1 |
Chemical Plant
Piping constraints required the flow meter to be installed with no upstream or downstream straight run, bolted directly between a valve (upstream) and tee (downstream).
Accelabar is able to accurately measure current flow rates (low velocity), since the required 15:1 flow turndown is well within the operating limits of the Accelabar. Since there are no straight run requirements, the location between the upstream valve and downstream tee is adequate because the straight run is integral to the Accelabar.
Steam Related
Accurate flow measurements in steam applications are difficult to obtain because of the fluctuating high temperature and high pressure process conditions and having to retrofit into existing piping. The Accelabar is the ideal fit for these applications due to the wide variety of materials and connections available. In addition, with the Accelabar, there are no straight run requirements, allowing it to fit into existing steam pipes.
-
EJX910A
This transmitter precisely measures differential pressure, static pressure, and process temperature; then uses these values in a high-perfomance on-board flow computer to deliver fully compensated Mass Flow.
-
EJX930A
Designed specifically for high static pressure applications, this transmitter precisely measures differential pressure, static pressure, and process temperature; then uses these values in a high-perfomance on-board flow computer to deliver fully compensated Mass Flow.
Resources
Looking for more information on our people, technology and solutions?
Contact Us