Yokogawa uses its industrial experience to provide unique solutions to meet the needs of the marine industry, and has been delivering IAS to LNG carriers worldwide for several decades. A long-term partnership with Yokogawa maximizes the total value of ownership with full lifecycle support.

Integrated Automation System
On an LNG carrier, boil-off gas (BOG) is produced by vaporization of LNG in the cargo tank. The Integrated Automation System (IAS) manages the BOG according to the propulsion system as well as controlling and monitoring the cargo system and machinery system. A unified operation and monitoring environment simplifies decision-making for complex LNG cargo and engine control operations. It also incorporates open interfaces so that supervisory computers can access trend data, messages, and process data. All process data can be monitored effectively at the human-machine interface. This makes it possible for operations on the LNG carrier to proceed more quickly and safely.
Challenges
Lifecycle Dynamic Simulator
Dynamic simulator trains the operator to prepare for the unsteady operations
Yokogawa is driving the advanced usage of the dynamic simulator which can be used for multiple
purpose throughout the lifetime of the LNG carrier. The dynamic simulator is ideal for operator
training, and it can be a useful tool to validate the system design by allowing rigorous
system testing under all operating condition.
By combining the ICSS test function with the process dynamic simulator, process
reaction can be predicted.
Customer Challenge

The dual fuel 2-stroke low-speed engine utilizes a high-pressure fuel gas supply system (FGSS). There are many variations of the FGSS processes that consist of the HP compressor, HP pump, reliquefaction, etc.
Our Solutions
The dynamic simulator enables validation of the plant design, control philosophy and operational concept of multiple combinations and cases.
Customer Benefits
This approach is useful for reducing the potential risks of a new process at an early stage of the project.
Enabling Technology
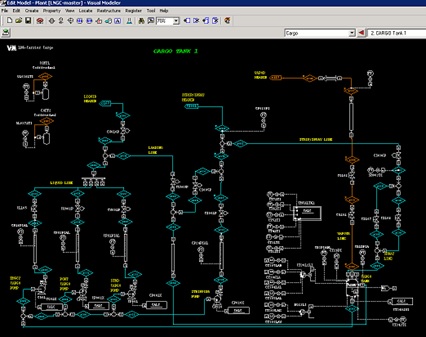
OmegaLand is the general term for integrated environments for dynamic simulators.
OmegaLand consists of functional modules to meet a large variety of applications at different departments of many industries. The dynamic simulation environment of OmegaLand will improve the efficiency of your system at less cost by combining modules to meet your needs.
Fleet Monitoring System
Real-Time Fleet Monitoring System contributes to integrated monitoring of your fleet
Yokogawa provides a real-time base fleet monitoring system with secure data transmission.
Real-time data contributes to monitor fleet conditions without delay and fully customizable KPI
dashboard assists swift decision-making in fleet management.
Network IO
The N-IO (Network I/O) is designed with fewer components; a single module can be configured to support AI, AO, DI, and DO. The optional signal conditioner can be plugged in to support a wide range of I/O signal types. The backplane allows I/O redundancy by design, which eliminates additional space for redundancy and results in a smaller footprint. The flexible I/O configuration of the N-IO minimizes hardware modifications due to design changes during engineering and commissioning.
Automation Design Suite (AD Suite)
AD suite provides an engineering environment that sustains delivery of new technologies throughout the plant lifecycle.Such technologies include modular design, bulk engineering, change management, automatic as-built document generation, and flexible binding.
Yokogawa’s marine know-how comes from a rich history of marine projects, and it has designed that know-how into its AD Suite Class Modules. The Yokogawa marine engineering team with the AD Suite achieves efficient project execution and delivers high quality software for customer satisfaction.
Details
Power Management System
- Control of circuit breakers and monitoring
- Load Dependent Start/Stop
- Load Sharing
- Frequency Control
- Blocking of Heavy Consumers
- Load Reduction to Propulsion Drives
- Load Shedding (preferential trip)
- Automatic restarting after blackout
- Generator Control & Monitoring
- Propulsion Drive Interface
- Emergency Switchboard Interface
Machinery System
- Fuel Oil & Fuel Gas System
- Personnel Alarm System
- Extension Alarm System
- Reduction Gear System
- Fresh, Cooling, Feed Water System
- Bilge Level Monitoring System
- Air Ventilation and Fans
- Compressed Air System
- Lube Oil System
- Machinery Miscellaneous
Cargo Containment System
- Temperature Monitoring
- Pressure Monitoring
- Level Monitoring
Cargo Control System
- Cargo Pumps Control
- Stripping/Spray Pumps Control
- Emergency Cargo Pumps
- Cargo Operation (Loading/Unloading)
Cargo ESDS
- ESD for Cargo Containment System
- Cargo Tank Protection System
- Fuel Gas Master Valve
- Ship/Shore Communication System
Ballast System
- Ballast Pumps & Valves
- Automatic Ballast/Deballast Control
- Automatic Ballast Water Exchange
Steam Turbine
The steam turbine provides propulsion for utilizing the BOG to run the carrier. BOG is spent for boiler fuel, and the steam from the boiler is used to rotate the turbine. The power of the turbine is conveyed to the propeller.
IAS integrates boiler control, gas management, compressor control, power management, etc., using a sophisticated control philosophy.
Dual Fuel Diesel Electric Propulsion
DFDE stands for dual fuel diesel electric propulsion. The propulsion system consists of several generator engines and electrical propulsion motors. Normally, generator engines burn only oil as fuel; however, the DFDE generator engines can burn both oil and gas. The gas or oil is supplied to the generator engine and the propulsion motor is driven by electrical power generated by the generator engine. Then, the power of the propulsion motor is conveyed to the propeller.
IAS integrates gas management, compressor control, power management, etc., using a sophisticated control philosophy.
About Two-Stroke Low Speed Dual Fuel Engines
Characteristics of Two-Stroke Low Speed Dual Fuel Engines
- With the growing environmental awareness in recent years, environmental regulations are being strengthened for marine engines. Currently, the International Maritime Organization (IMO) is working toward the following regulations.
- Reduction of NOx emissions (third regulation)
- Regulation of sulfur oxides
- Reduction of greenhouse gases
- To comply with the third regulation, engineers can use natural gas as fuel instead of heavy oil and perform a lean premixed combustion. In addition, since natural gas does not contain sulfur, the second regulation is satisfied.
- Furthermore, CO2 emissions can be reduced by 20 to 30%. Therefore, the current marine market desires dual fuel two-stroke engines that can be operate on heavy oil or gas fuel as needed. These dual two-stroke low speed engines require LNG gas handling systems to supply suitable fuel on board.
To optimize BOG and fuel economy, YOKOGAWA IAS integrates a fuel gas supply system (FGSS) and reliquefication control for the dual two-stroke low speed engines into cargo and machinery systems of LNG carriers or LNG fuel vessels. Called CENTUM and STARDOM, these systems provide reliable, high performance control of FGSS for dual fuel two-stroke engines, and provide total control of vessels as smart ships.
In a two-stroke low speed engine, the main shaft is directly connected to the engine and the shaft speed is low. Therefore, the propulsion system has higher power, higher efficiency, and higher reliability. Conventional two-stroke low-speed engines only ran on oil, but current mainstream ones can also run on gas. These new two-stroke low-speed engines come in two types each with different combustion methods.
High Pressure: ME-GI
The left figure shows a gas supply system for ME-GI. This is a handling system in which fuel gas is directly injected into the combustion chamber containing pre- ignited pilot oil. In this method supply gas must be pressurized to about 30 MPa in order to inject into the engine.
The basic fuel gas supply system consists of a high pressure LNG pump, forcing vaporizer, and BOG compressor. Depending on customer requirements, a re-liquefaction system can also be added to the system for LNG carriers. When loading LNG, a large amount of BOG is directly boosted to 30 MPa by a compressor and supplied to the engine. However if the amount of BOG generated is small, the LNG is pressurized by a high pressure pump and then heated to around 45 degC and supplied to the engine. If the LNG is a fuel vessel, the FGSS will be more simple.
Low Pressure: X-DF
The left figure shows the gas supply system for the X-DF. This is the fuel gas handling system used when a premixed combustion type dual two-stroke low speed engine is mounted on a vessel. In the premixed combustion method, the fuel gas can be injected at low pressure when the air flowing in from the scavenging port reaches a position higher than the gas valve position while pushing out the burnt gas (exhaust gas) upward.
This system consists of an LNG pump, forcing vaporizer, and BOG compressor. Depending on customer requirements, a re-liquefaction system can also be added to the fuel gas supply system for an LNG carrier. When loading LNG, a large amount of BOG is directly boosted to 1.6 MPa by a compressor and supplied to the engine. However if the amount of BOG generated is small, the LNG is pressurized by a pump directly and then fed into the evaporator, gasified, and supplied to the engine. If the LNG is fuel vessel, the FGSS will be more simple.
Resources
- CENTUM CS 3000 ensures safe and reliable operation of one of the world's most advanced LNG carriers.
- Yokogawa successfully installed a CENTUM CS 3000 integrated control automation system(ICAS).
- MISC could be ensured of better information visibility, performance foresight, and operational agility.
- Yokogawa CS 3000 system has proven in both the Tenaga and the Seri Class LNG carriers that their hardware is very reliable with very less problem.
Over the past decade, companies have been using unconventional drilling technology to extract gas and liquid from the readily available shale formations in North America. As the industry gains experience, the production rates continue to rise based on better use of technology to locate resources and to decrease the time from exploration to production.
As LNG moves from a niche to a major area of the oil and gas industry, experienced suppliers are required to deliver the technologies that support it.
Looking for more information on our people, technology and solutions?
Contact Us