Introduction
Delayed Coker is a type of coker who's process consists of heating residual oil feed to its thermal cracking temperature in a furnace. The most important variable in industrial furnace control is temperature. Temperature is measured throughout the furnace in different zones and temperature effects the materials being manufactured and therefore must be precisely monitored to prevent deviations in quality of the final product.
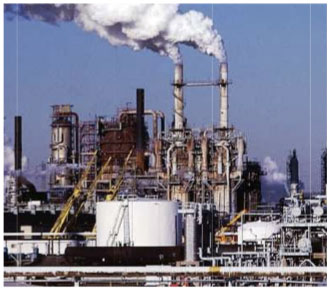
Benefits
- Minimized plant startup time and downtime
- Improved product quality, continuous temperature monitoring leads to improvement of the product quality
- Reduced maintenance effort (NO wires, NO routing problems, NO cable maintenance issue)
- Optimized fuel consumption and reduced operation cost (OPEX)
- Reduced total power consumption, low power consumption devices enable cost savings
- Enabled easy integration with existing host system, industry proven Modbus platform enables easy and seamless integration with a wide range of host systems
Requirements
Coker tube furnace is the heart of the delayed coking process. The heater provides all the heat in the process. The output temperature of the furnace is typically around 500 degree C.
- Temperature monitoring is required due to the following reasons:
-
- Coker furnaces are designed to have a constantly rising temperature gradient to reach the thermal cracking temperature quickly and thus optimize the fuel consumption.
- The burners are controlled by the measurement of tube temperatures.
- The furnace needs to be decoked or cleaned. Continuous operation of the cork drum forms a layer of insulation on the inner lining of the tubes resulting in the variation of temperature on the coke drum skin.
- Delayed coking is one of the processes used in many refineries. Depending on the capacity, number of coke drums in operation varies from 4 to 8. Each coke drum will require up to 24 temperature points to be monitored.
Solution
Three YTMX580 multi input temperature transmitters were installed. Each of these accepts 8 temperature inputs and it reduces the quantity of transmitters required to only 3 on each coke drum. Field wireless access point was installed on the control room located 600m from the measurement area with dense obstructions. Two repeaters were used to establish redundant communication paths between the measurement devices and the field wireless access point. The field wireless management station was integrated with 3rd party host system using RS485 series Modbus communication.
The ISA100 wireless system provides an easy customizable GUI with deterministic topology monitoring for the operator. It identifies the wireless condition such as error rate of both primary and secondary communication paths to visualize communication quality.
Conclusion
- Wireless solutions enabled reduction of huge bundles of cable running from the field to the control room.
- High capacity Lithium Thionyl battery powered devices enabled savings in OPEX with proven battery life of better than 1.6 years with an update time of 10 sec for the temperature measurements (eight inputs).
- Industry proven Modbus platform enabled easy integration with existing 3rd party host systems.
- Wider application coverage ISA100 wireless minimized infrastructure which reduces installation time and expense, this is reflected as direct savings to the users.
- Best in class signal availability of ISA100 wireless architecture with stable wireless connections proved to be a trustworthy wireless solution, perfectly meeting the user requirements.
- Maintainable topology reduced the cost of ownership and enabled more points to be added as necessary in the future.
Yokogawa has a proven track record of delivering reliable, scalable and open technologies for a century. ISA100 wireless solutions address the specific challenges of the industrial automation industry while lowering cost ownership for our end users and maximizing their return on the investment.
Súvisiace odvetvia
-
Refining
In the ever changing marketplace, refineries are seen not only as crude processing units but also as profit centers. At the same time, there is a keen awareness of the need for safety at such facilities. A total production solution that encompasses planning, scheduling, management, and control is required to achieve long-term goals for profitability, efficiency, and environmental protection. With years of expertise in the automation field, Yokogawa can bring you affordable total solutions for improved operability and a cleaner world.
-
Oil & Gas Downstream
The oil & gas downstream industry has been facing an increasing number of challenges in recent years. These include the changing characteristics of the feedstock to be processed, aging of process facilities and equipment, rising cost of energy, lack of skilled plant operators who can run a refinery safely and efficiently, and the ever-changing requirements from both the market and the customer.
Over the years, Yokogawa has partnered with many downstream companies to provide industrial solutions focused on solving these challenges and problems. Yokogawa's VigilantPlant solutions have helped plant owners to achieve maximum profitability and sustainable safety within their plants.
Súvisiace produkty a riešenia
-
Field Wireless
The flexibility of wireless solutions enables less investment in infrastructure while providing greater insights into plant operations.
-
YFGW410 Field Wireless Management Station
YFGW410 Field Wireless Management Station has system manager/security manager/gateway function based on ISA100.11a, and combining this with Field Wireless Access Point(YFGW510) and/or Field Wireless Media Converter(YFGW610) composes the field wireless system.
-
YFGW510 Field Wireless Access Point
YFGW510 Field Wireless Access Poin has backbone router function based on ISA, and combining this with Field Wireless Management Station (YFGW410) and/or Field Wireless Media Converter (YFGW610) composes the field wireless system.
-
YFGW520 Field Wireless Access Point
YFGW520 Field Wireless Access Poin has backbone router function based on ISA, and combining this with Field Wireless Management Station (YFGW410) and/or Field Wireless Media Converter (YFGW610) composes the field wireless system.
-
YTA510 Wireless Temperature Transmitter
The high performance temperature transmitter YTA510 accepts Thermocouple, RTD, ohms or DC mill volt inputs. The transmitters transmit not only process variables but also the setting parameters using wireless signal. The transmitters run on internal batteries, and the installation cost can be decreased since hard-wiring is not required. The communication is based on ISA100.11a protocol specifications.
-
YTMX580 Multi-Input Temperature Transmitter
YTMX580 can accept inputs from up to 8 points of measurement such as thermocouples (8 types: K, E, J, etc.) or RTD signals (3 types: Pt100, etc.), converting the corresponding measurement input values to a wireless signal. It can also accept DC voltage, resistance, and 4 to 20 mA DC signal input.