Introduction
Delayed Coker is a type of coker who's process consists of heating residual oil feed to its thermal cracking temperature in a furnace. The most important variable in industrial furnace control is temperature. Temperature is measured throughout the furnace in different zones and temperature effects the materials being manufactured and therefore must be precisely monitored to prevent deviations in quality of the final product.
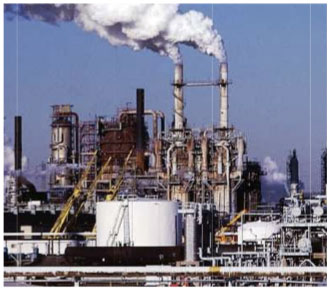
Benefits
- Minimized plant startup time and downtime
- Improved product quality, continuous temperature monitoring leads to improvement of the product quality
- Reduced maintenance effort (NO wires, NO routing problems, NO cable maintenance issue)
- Optimized fuel consumption and reduced operation cost (OPEX)
- Reduced total power consumption, low power consumption devices enable cost savings
- Enabled easy integration with existing host system, industry proven Modbus platform enables easy and seamless integration with a wide range of host systems
Requirements
Coker tube furnace is the heart of the delayed coking process. The heater provides all the heat in the process. The output temperature of the furnace is typically around 500 degree C.
- Temperature monitoring is required due to the following reasons:
-
- Coker furnaces are designed to have a constantly rising temperature gradient to reach the thermal cracking temperature quickly and thus optimize the fuel consumption.
- The burners are controlled by the measurement of tube temperatures.
- The furnace needs to be decoked or cleaned. Continuous operation of the cork drum forms a layer of insulation on the inner lining of the tubes resulting in the variation of temperature on the coke drum skin.
- Delayed coking is one of the processes used in many refineries. Depending on the capacity, number of coke drums in operation varies from 4 to 8. Each coke drum will require up to 24 temperature points to be monitored.
Solution
Three YTMX580 multi input temperature transmitters were installed. Each of these accepts 8 temperature inputs and it reduces the quantity of transmitters required to only 3 on each coke drum. Field wireless access point was installed on the control room located 600m from the measurement area with dense obstructions. Two repeaters were used to establish redundant communication paths between the measurement devices and the field wireless access point. The field wireless management station was integrated with 3rd party host system using RS485 series Modbus communication.
The ISA100 wireless system provides an easy customizable GUI with deterministic topology monitoring for the operator. It identifies the wireless condition such as error rate of both primary and secondary communication paths to visualize communication quality.
Conclusion
- Wireless solutions enabled reduction of huge bundles of cable running from the field to the control room.
- High capacity Lithium Thionyl battery powered devices enabled savings in OPEX with proven battery life of better than 1.6 years with an update time of 10 sec for the temperature measurements (eight inputs).
- Industry proven Modbus platform enabled easy integration with existing 3rd party host systems.
- Wider application coverage ISA100 wireless minimized infrastructure which reduces installation time and expense, this is reflected as direct savings to the users.
- Best in class signal availability of ISA100 wireless architecture with stable wireless connections proved to be a trustworthy wireless solution, perfectly meeting the user requirements.
- Maintainable topology reduced the cost of ownership and enabled more points to be added as necessary in the future.
Yokogawa has a proven track record of delivering reliable, scalable and open technologies for a century. ISA100 wireless solutions address the specific challenges of the industrial automation industry while lowering cost ownership for our end users and maximizing their return on the investment.
相關業種
-
精煉
在不斷變化的市場中,煉油廠不僅是原油加工單位,而且是利潤中心。同時,人們強烈意識到煉油廠設施安全性的重要。為了實現盈利,效率及環境保護的長期目標,需要包括計劃,調度,管理和控制的總體生產解決方案。憑藉在自動化領域多年積累的專業知識,橫河可以為您提供經濟實惠的完善的整體解決方案,改善操作並使世界更清潔。
-
石油和天然氣下游
近年來,石油和天然氣下游產業面臨著越來越多的挑戰。這些挑戰包括待加工原料的特性變化、工業設施及設備的老化、能源成本的上升、缺乏能夠使煉油廠安全有效運行的熟練技術工人,以及市場和客戶的需求不斷變化。
多年來,橫河與許多下游公司合作,致力於提供應對這些挑戰和問題的工業解決方案。橫河的解決方案幫助工廠投資者盡可能實現最大的盈利能力和工廠內可持續的安全。
相關產品&解決方案
-
YFGW410現場無線管理站
YFGW410現場無線管理站具備符合ISA100.11a標準的系統管理/安全管理/網關功能,與現場無線接入點(YFGW520)和/或現場無線媒介轉換器(YFGW610)組合使用,可構建完整的現場無線系統。
-
YFGW520現場無線接入點
YFGW520現場無線接入點具備基於ISA標準的骨幹路由器功能,與現場無線管理站(YFGW410)和/或現場無線媒介轉換器(YFGW610)組合使用,可構建完整的現場無線系統。
-
YTA510無線溫度變送器
高性能溫度變送器YTA510接收熱電偶、RTD、歐姆或DC mV輸入信號。該變送器通製無線信號傳輸製程變量以及設定參數。該變送器採用內定電池,由於無需硬接線,因此可降低安裝成本。通信規格以ISA100.11a協議為基礎。
-
YTMX580多點輸入溫度變送器
YTMX580至多可接收8點測量輸入值,如熱電偶(8種類型:K、E、J等)或RTD信號(3種類型:Pt100等),並將相應的測量輸入值轉換為無線信號。它也可以接收DC電壓、電阻和4~20 mA DC信號輸入。
-
現場無線
無線解決方案的靈活性可減少對基礎設施的投入,同時可以對工廠運營有更深入的了解。