Click here to learn about Control Room Design
Key areas for Operational Excellence Transformation
Operational Excellence Transformation is Yokogawa and KBC’s co-innovated portfolio of solutions and services.We provides comprehensive solutions for business automation in all four areas using consulting and digital technology.
Operational Risk Management
Yokogawa's Operational Risk Management deals with managing safety, health and environmental risks on both individual and process levels in a reliable and risk-free manner. It involves the end-to-end process of designing, visualizing and orchestrating plant production and business systems.
Key Operational Competencies in Operational Risk Management
- Process Safety Management: Maintain License to Operate, preserve Business Reputation, and create value by utilizing and adhering to operating integrity processes to prevent loss of containment or catastrophic loss
- Personal Safety Management: Protect human assets by providing safe practices to improve behavior and culture
- Environmental Management: Provide processes to protect the environment through operating integrity, and ensure compliance with environmental, regulatory and/or internal requirements
- Community Relations: Define and establish processes and protocols to communicate and implement emergency response plans, and enhance interactions in the community
- HSSE Reporting and Compliance: Assure visibility and achievement of HSSE goals and compliance requirements, by monitoring, learning and improving continuously through processes, initiatives and KPIs
- Plant Protocols and Security: Provide processes and strategies to protect assets and infrastructure from threats, and control access to vulnerable processes and equipment
By combining Yokogawa’s product portfolio and KBC’s consulting services, we provide our customers best practices and domain knowledge that empower them to improve their operations, as well as a digital platform that supports such activities and initiatives. Our Operational Risk Management scope does not only cover partial improvements in the organization, but also optimizations in plant operations to achieve continuously improving safety, reliability and operability.
·Supply Chain Optimization
- Optimize management of supply, whether oil in the ground or feedstocks for a refinery or chemical asset, in light of product market demands. This provides operators with the agility to take full advantage of market conditions.
·Asset Operations and Optimization
- Optimize the potential of physical assets, by pushing throughput and maximizing the production of the highest value products, whilst minimizing variable costs such as energy.
- Deliver small and large CAPEX projects, on time and on budget, to deliver growth and meet environmental requirements.
·Asset Management and Integrity
- Confidently ensure asset reliability and availability, whilst controlling maintenance costs. This assures the asset always meets expectations and is always available to capitalize on short term market opportunities.
Control Room Design
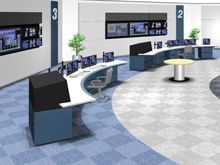
Yokogawa launched its control room design service soon after releasing the first distributed control system onto the market in 1978. Users come from a wide range of industries including iron & steel, chemicals, electric power, gas supply, oil refining, water supply, and many more. Yokogawa ranks very high in customer satisfaction in control room design thanks to the company's wide ranging experience, expertise, and dynamic designs.
Customer Challenge
Creating Synergy and Flow in Control Rooms
All aspects of the work environment must be taken into consideration when designing control rooms. These aspects include operator comfort, ergonomics, safety, ease of communication, functionality, automation of systems, and business policy.
Streamlining these aspects and creating a synergy through the layout and design of the control room is the key to achieving streamlined and safe operations.
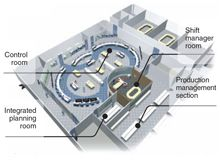
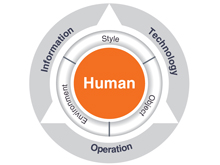
Our Solutions
Achieving Safety, Comfort, and Innovation in Human-Centered Design
Human-centered design prioritizes safety, health, and comfort. Yokogawa's concept of control room design has evolved over a long period and allows us to achieve superior customer satisfaction. While a control room needs to be highly functional and enable operators to complete their daily tasks, the design must also be balanced to meet comfort requirements allowing each person to work with maximum efficiency - including the plant manager. This is the key to successful control room design. Yokogawa designs are based on a thorough understanding of control systems, plant operations, and ergonomics.
Depending on the facility, once you have provided information such as the site plan, existing control room drawings, control room photos, and system configuration, our experts will work with your team to develop a proposal containing the draft design, including conceptual designs, material selection and layout planning. If you are considering a grass-roots project, control room consolidation, or control system migration - then now is the time to visualize how the control room will be designed.
Customer Benefits
Reliable Operator Performance as a Result of Ideal Working Environment
An appropriately designed control room will make people feel relaxed and secure. As a result, operators and managers can fully concentrate on plant operations and stability. Additionally, improvements in data integrity and data availability accelerate communication between units to optimize the total operation.
Another intangible but valuable effect of innovative control room design is the motivation that it creates, especially in young operators. Most operators and plant managers are stimulated by new control rooms, new systems and new ways in operation. It is important o note that improvements in control rooms and production centers create several benefits at the time of the improvement, and in the future.
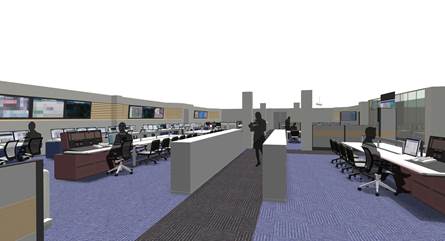
Details
Yokogawa's control room design consulting service is based on standardized Six Sigma DMAIC methodology. This provides clear and effective steps to achieve a defined target while ensuring consistent and high levels of service quality.
1. Define | Define target for control room design, e.g.
|
---|---|
2. Measure | Use questionnaire to acquire customer information
|
3. Analyze | Survey existing control room (If there is one)
|
4. Improve | Prepare draft design that includes the following:
|
5. Control | Issue and introduce draft design
|
Resources
The consolidation of control rooms was conducted in several refineries in the 1990s and early 2000s as a means of reducing the number of operators and improving the efficiency for enhancing competitiveness. The characteristics of consolidated control rooms vary, reflecting the history of a refinery.
When considering improving the efficiency of plant operation, major focus is put on process units, control systems and production or operation management. However, it is also important to prepare a comfortable and safe environment for operators, who are trying to operate the plant more efficiently every day using control systems.
Videos
Dr. Maurice Wilkins - executive advisor at Yokogawa speaks with Alastair Greener from the Business Reporter at the Daily Telegraph and shares his thoughts on Process plant operators, automation and how they need to work together in a crisis.
Hľadáte viac informácií o našich ľuďoch, technológiách a riešeniach?
Kontaktujte nás