Reduce your field work in the commissioning phase
Yokogawa‘s Commissioning Support Package (CSP) is an application that automates loop checks and associated field device start-up operations using communications protocols such as HART or FOUNDATION™ Fieldbus.
CSP consists of two software packages,
- PRM Commissioning Support Package (PRM CSP)
- Field Commissioning Support Package (F-CSP)
CSP helps to reduce the burden of instrumentation setup and inspection during plant construction and their periodic inspections and repairs. It considerably reduces the risk of project delays.
For smooth commissioning
The start-up and commissioning processes in a plant are subject to considerable risks of delays. During project execution, the installation and configuration of field devices, connecting them to the system and verification of signal accuracy must all be completed in a timely manner. By using PRM CSP and F-CSP, it is possible to reduce the time required for equipment checks and shorten the construction period required for plant start-up.
Details
PRM CSP
PRM Commissioning Support Package (PRM CSP) is a tool to automatically perform connection check for HART devices and Foundation™ Fieldbus devices during the plant start-up or maintenance. PRM CSP helps decrease the device check time during the plant start-up or maintenance by automating various works, which enables to shortening the total work hours and contributes to improve quality of performance.
Many field devices can be found in plants, and commissioning the plant requires checking whether the devices were installed in the correct location. Checking the location means opening each piece of equipment one by one―a labor-intensive process. But with the PRM commissioning support package(PRM CSP), rather than having to open the equipment, you simply send a command to a device from the PRM CSP and view it on the device’s display. This greatly reduces the time it takes to perform connection checks.
More efficient equipment connection checks
Connection loop checks during commissioning confirm that each field device is correctly connected with the DCS and functioning properly. However, field devices might be disconnected when pipes are flushed in preparation for a test run of the plant in order to avoid being damaged. In such a case, the loop check must be done once again after the field devices are re-installed.
The application scope of PRM CSP in a general plant start-up procedure is as follows.
Automatic Loop Check (PRM CSP)
Conventional loop checks require considerable on-site work, such as setting values and checking them in the actual devices. With PRM CSP, loop checks can be performed automatically from a central control room for all field devices connected to the control network. By streamlining the loop checking process, project hours and human errors are reduced. Those can lead to improved work quality.
In the PRM CSP input loop check,
(1) send a command from PRM CSP to change the device’s output value. Next, (2) read the output value from the device on PRM CSP via Exaopc (for HIS) and confirm its accuracy.
In the PRM CSP output loop check,
(1) change the output value for the device on PRM CSP through the HIS, (2) use a PRM CSP command to read the valve’s readback value from the device and confirm that the value changed to the desired value.
Interlock Check
Interlock checking is typically very time-consuming. PRM CSP enables the setting of parameters on field devices to be automated, which can significantly reduce the number of manual operations. Settings can also be quickly restored to their initial conditions. This eliminates many of the burdens of manual operations involved in interlock checking.
Automatic generation of operations reports means reduced labor and improved quality
- Reduce man hours
Manually organizing descriptions of work performed and formatting it into reports is very labor-intensive. With PRM CSP, you can load test data from range checks and comprehensive loop checks, and automatically create operations reports. This greatly reduces reporting man hours. - Improve report quality
Assembling all work contents and data by hand invites errors. The PRM CSP loads data and automatically generates reports in a standard format, which cuts down on reporting errors. Plus, users can flexibly customize the format to create high quality reports that fit the customer’s circumstances.
F-CSP
Field Commissioning Support Package (F-CSP) is a software package to perform loop (input/output) inspection working with N-IO nodes of CENTUM VP/ProSafe-RS effectively and contributes to reduce the time of device checks and shorten the construction period for start-up.
Pre-implementation of start-up work
Settings of N-IO nodes, confirmation of operations for I/O modules, and inspections (Connection Check, HART Range Comparison Check, Signal Conversion Check, Parameter Download and Loop Check) between N-IO nodes and field devices can be performed by the application information defined by F-CSP during start-up.
The value of start-up work by F-CSP
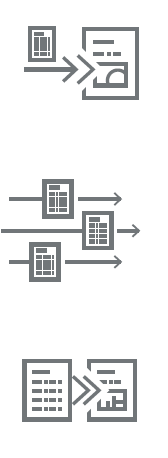
I n a d v a n c e
By installing and wiring N-IO nodes and field devices in advance, it is possible to start-up N-IO nodes and field devices with F-CSP even during engineering.
P a r a l l e l
F-CSP works with the N-IO nodes. Start-up work can be concurrently carried out in respective N-IO nodes by using multiple F-CSPs. Also, since applications can be created at the
engineering office, work on site and at the engineering office can be performed in parallel.
S e q u e n t i a l l y p e r f o r m e d
Inspection checks and acceptance tests can be performed sequentially once F-CSP has done the configuration for the FCS / SCS. Inspection work can proceed smoothly without delays.
Project execution by using modular construction (F-CSP, PRM CSP)
For the projects applying “Modular Construction,” Field Commissioning Support Package (F-CSP) can perform I/O loop check (pre-commissioning) at the site in parallel with creating the application by N-IO (Network I/O) type of CENTUM VP and ProSafe-RS. This parallel work shortens the construction period for the entire project, minimizes the risk of delays due to design changes, and makes commissioning more efficient.
Project execution image applying modular construction
In conventional construction, it is necessary to develop applications and perform construction after FEED and design, then proceed to commissioning. However, if the application specifications were changed after the system was shipped, it would take a lot of time for on-site corrections and reworking.
In a project that adopts the modular construction method, it is possible to carry out construction and pre-commissioning in parallel with application development after FEED and design. It is possible to perform commissioning in advance, independent of application development, and to reduce the risk of delays due to design changes.
Downloads
Op zoek naar meer informatie over onze mensen, technologie en oplossingen?
Contact