Click here to learn about Incident/Near Miss Management
Key areas for Operational Excellence Transformation
Operational Excellence Transformation is Yokogawa and KBC’s co-innovated portfolio of solutions and services.We provides comprehensive solutions for business automation in all four areas using consulting and digital technology.
Operational Risk Management
Yokogawa's Operational Risk Management deals with managing safety, health and environmental risks on both individual and process levels in a reliable and risk-free manner. It involves the end-to-end process of designing, visualizing and orchestrating plant production and business systems.
Key Operational Competencies in Operational Risk Management
- Process Safety Management: Maintain License to Operate, preserve Business Reputation, and create value by utilizing and adhering to operating integrity processes to prevent loss of containment or catastrophic loss
- Personal Safety Management: Protect human assets by providing safe practices to improve behaviour and culture
- Environmental Management: Provide processes to protect the environment through operating integrity, and ensure compliance with environmental, regulatory and/or internal requirements
- Community Relations: Define and establish processes and protocols to communicate and implement emergency response plans, and enhance interactions in the community
- HSSE Reporting and Compliance: Assure visibility and achievement of HSSE goals and compliance requirements, by monitoring, learning and improving continuously through processes, initiatives and KPIs
- Plant Protocols and Security: Provide processes and strategies to protect assets and infrastructure from threats, and control access to vulnerable processes and equipment
By combining Yokogawa’s product portfolio and KBC’s consulting services, we provide our customers best practices and domain knowledge that empower them to improve their operations, as well as a digital platform that supports such activities and initiatives. Our Operational Risk Management scope does not only cover partial improvements in the organization, but also optimizations in plant operations to achieve continuously improving safety, reliability and operability.
·Supply Chain Optimization
- Optimize management of supply, whether oil in the ground or feedstocks for a refinery or chemical asset, in light of product market demands. This provides operators with the agility to take full advantage of market conditions.
·Asset Operations and Optimization
- Optimize the potential of physical assets, by pushing throughput and maximizing the production of the highest value products, whilst minimizing variable costs such as energy.
- Deliver small and large capex projects, on time and on budget, to deliver growth and meet environmental requirements.
·Asset Management and Integrity
- Confidently ensure asset reliability and availability, whilst controlling maintenance costs. This assures the asset always meets expectations and is always available to capitalize on short term market opportunities.
Incident/Near Miss Management
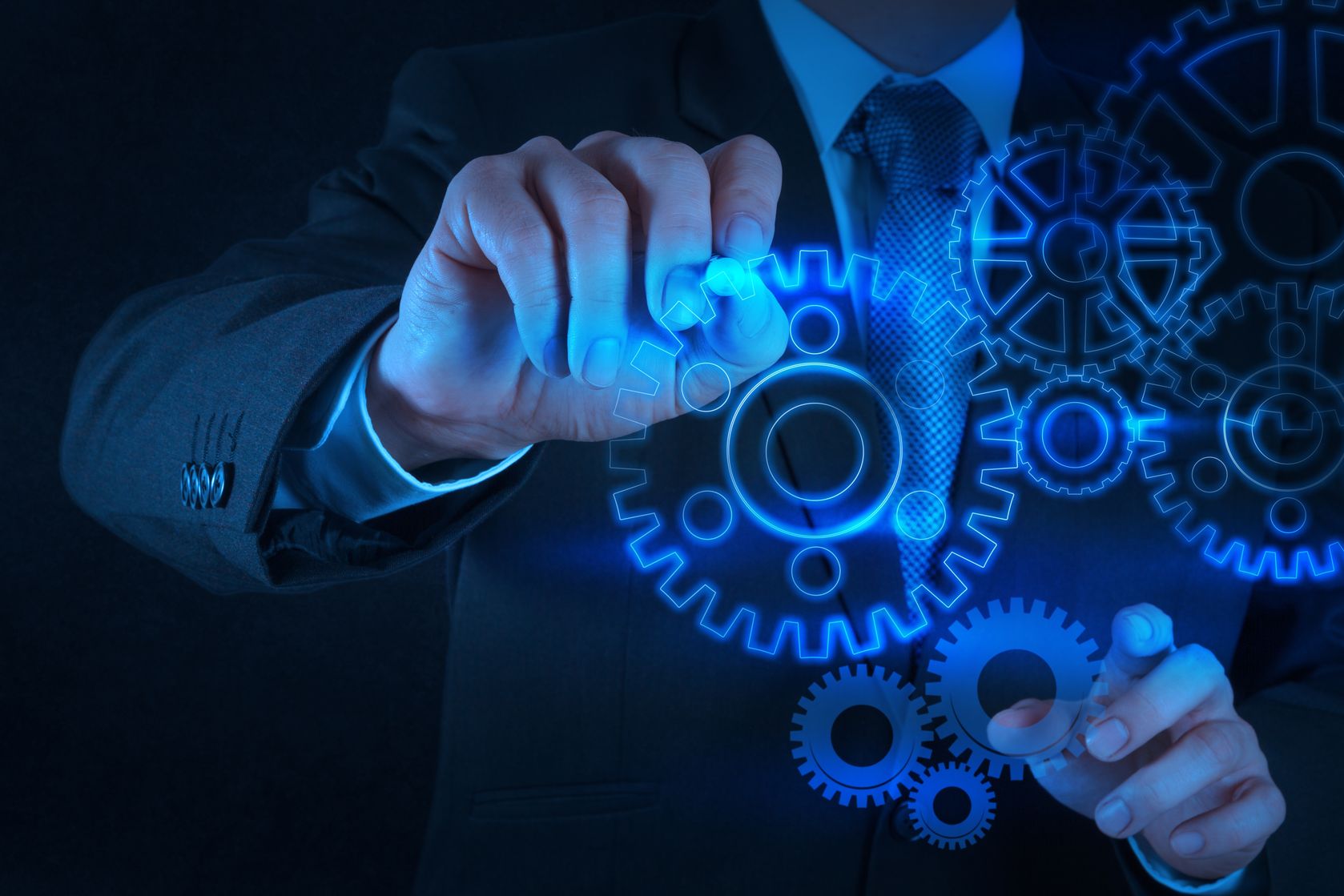
Incident Management is an essential business process to help avoid major incidents and near misses that lead to major accidents in complex chemical operations facilities. Incident Management’s key objective is to monitor compliance to the key Health Safety and Environmental (HSE) guidelines defined by ‘Process Safety Management’ a regulation, promulgated by OSHA.
Our solution focuses mainly on managing the operational safety risk of chemical operations through the following three components of plant operations: People-Plant-Process. Safety Compliance Management is meant to ensure compliance to internal and external statutory/legislative safety requirements
Incident Management is one part (module) of Yokogawa's fully integrated Operations Management System.
Customer Challenge
Ensuring Safety Compliance
- Paper based reporting and investigation of incidents and near-misses create a lack in visibility and accountability
- Corrective and preventive actions are often not tracked
- Information regarding HSE practices followed in plant operation is scattered in different systems (mostly paper based)
- Non-compliance often goes undetected due to lack of effective monitoring measures
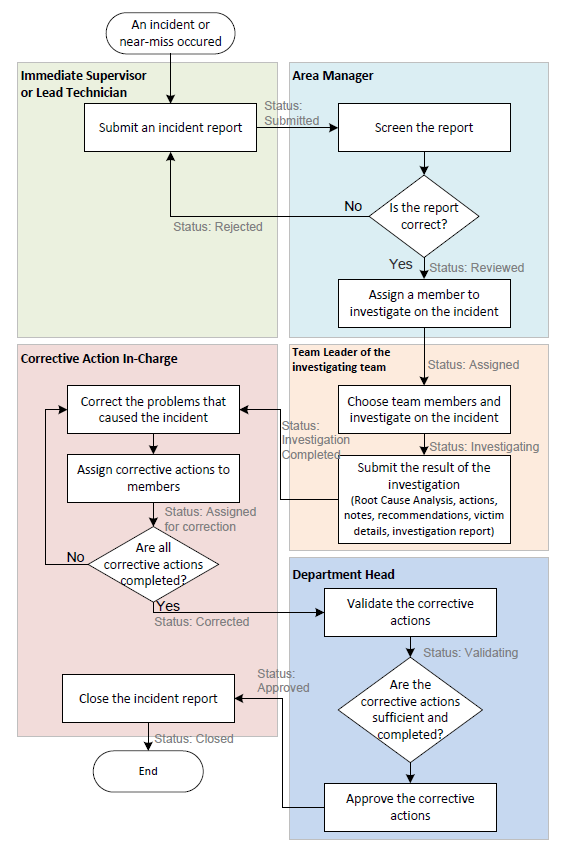
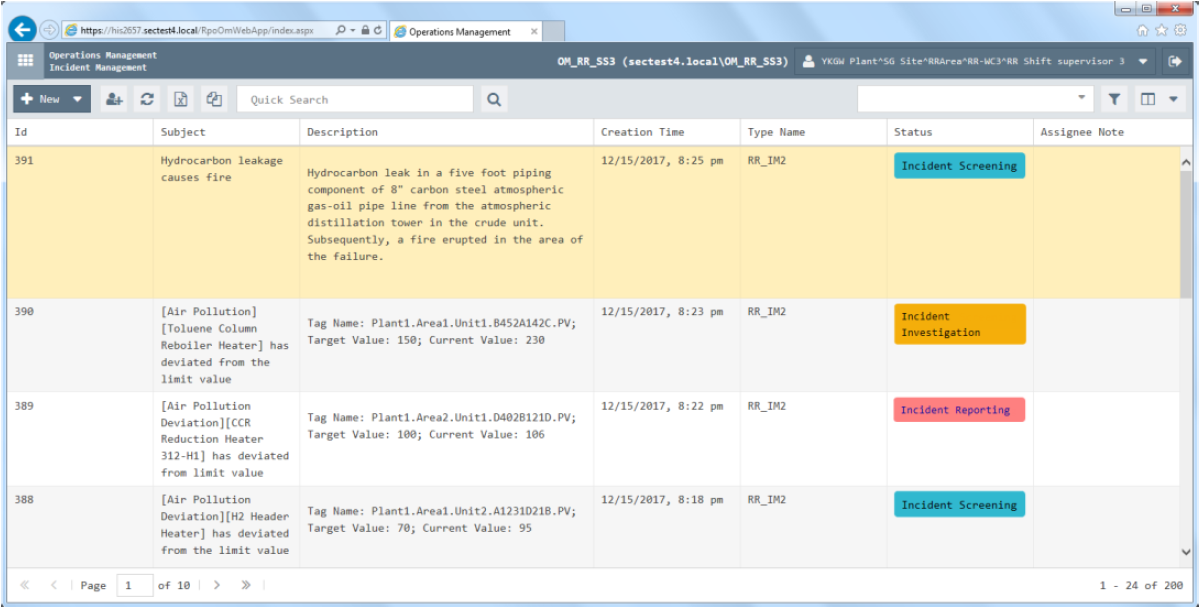
Our Solutions
Report, Investigate, and Close out Workflow for Incident Management
This module will give plant personnel with the ability to track and manage plant wide incidents/near misses, non-compliances, supports manual or/and automated creation of Incident/Compliance reports.
Key Features:
- Preconfigured Incident investigation work flow based on best practices (Reporting to Close Out)
- Enforced approvals workflows based on statuses
- Configurable templates for data entry at each stage of Incident investigation reviews and approvals
- Preconfigured Risk Assessment Matrix
- Preconfigured Root Cause Analysis Tree
- Auto email alerts, notifications to all stakeholders for due dates
- Integrated with EDMS to maintain latest revised control documents
- Complete audit trail of user actions updating Incident investigation information/status
Customer Benefits
Track, Trace, and Monitor your Safety Compliance
Compliance to OM Practices
- Compliance to shift handover (Time of Handover)
- Compliance to Standing Instruction (SI) requirements i.e. tracking on SI acknowledgement, SI expiry
- Compliance to planned Basic Operation Care activities
Compliance to Operating/Safety Envelopes
- Top 10 critical alarms and safety/excursion/bypass/overrides are automatically logged per shift report
- Process excursions (Number of exceeds, max/min hits, average) monitored and auto reported shift report
Visibility to Operations
- Comprehensive dashboard for daily status of plant performance and production KPI's
- Easy access to all shift logs, instructions, checklists and events across plant ensuring effective collaboration between planning, operations and maintenance
Improved Productivity
- Integrated, automated collection and analysis of data from various systems (SAP PM, PTW, Historian, alarm management, LIMS and more)
- Automatic data entry prevents human error and to free up valuable operations resources
Operational Reliability
- Knowledge repository for proactive and consistent actions in plant operations
- Rapid data mining for common issues, incidents, captured lessons learned
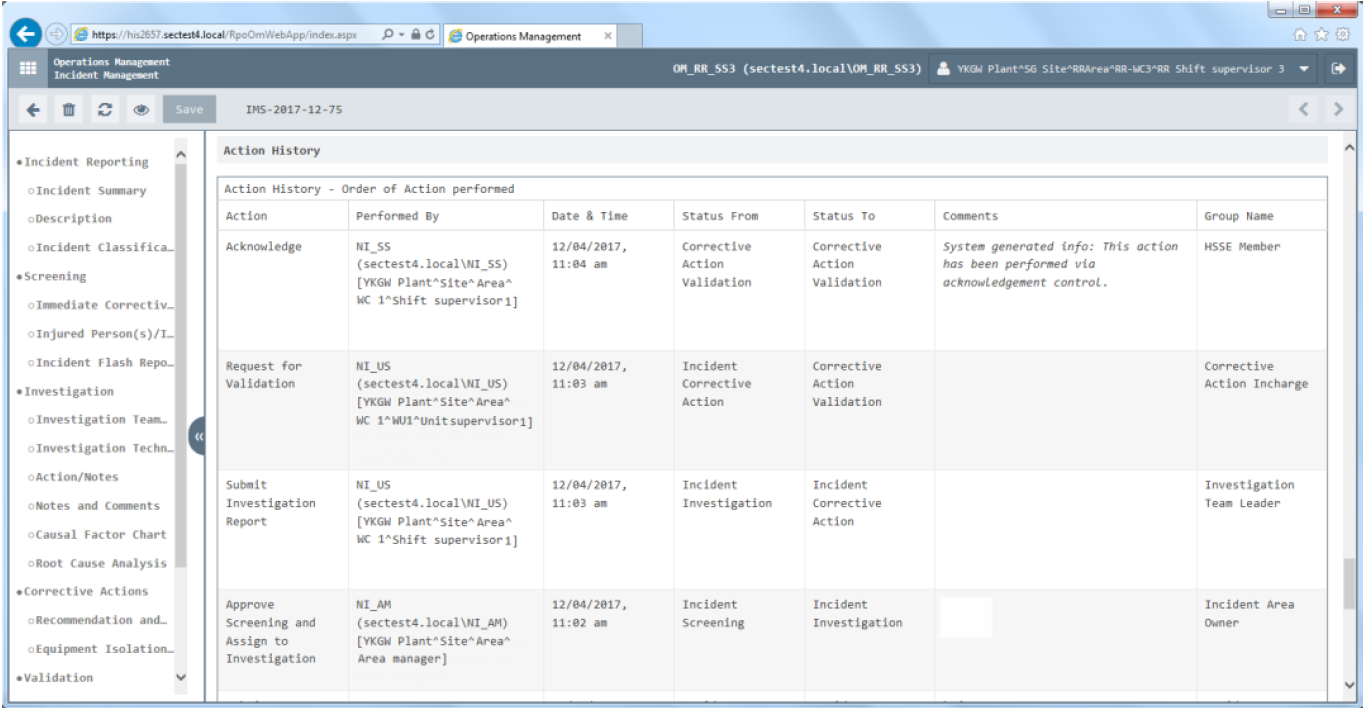
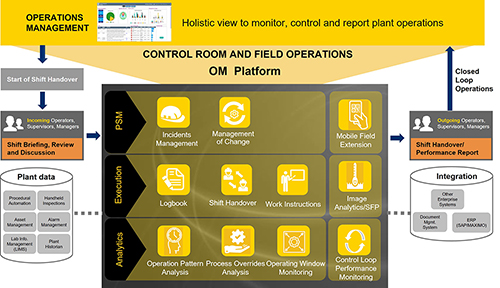
Enabling Technology
Yokogawa’s Operations Management System helps to ensure Safe and Reliable Operations by digitizing necessary information for Operation Management Practices. This results in improved productivity through standardized work practices, streamlined processes, plus improved communications and coordination across departments.
További információkat szeretne a munkatársainkról, technológiánkról és megoldásainkról?
Kapcsolatfelvétel