Executive Summary
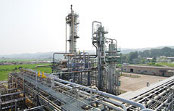
Analysis of Operator Expertise Leads to
at Gas Plant in Niigata, Japan
To improve safety and efficiency at this plant, INPEX needed to bring the graphical user interface (GUI) on its production control system (PCS) human-machine interface (HMI) stations up to international standards, specifically the ASM Design Guidelines1, ISA-5.52, ISO-92413, and API RP 11654. INPEX turned to Yokogawa for a solution because the company had expertise in developing advanced operator graphics (AOG5) solutions. A team of Yokogawa engineers visited the plant to conduct a detailed analysis, review the tasks carried out by operators, and learn about the plant's operations. In accordance with general principles on industrial design and human engineering, Yokogawa then redesigned the GUIs for the HMI displays to reduce operator errors, make their work easier to perform, and reduce physical stress. Throughout this project, the Yokogawa team followed the Six Sigma DMAIC methodology:
DMAIC overview
Steps | Contents | Period |
---|---|---|
Define | Design scope, design team setup | 1 week |
Measure | Investigation of operation environments | 2 weeks |
Analyze | Style design, task analysis, proposal | 6 months |
Improve | Evaluation, consulting to the team | 6 months |
Control | Final evaluation, final report | 1 month |
As the work periods overlapped, this process took 9 months, from start to finish.
The Challenges and the Solutions
After a careful review of the operation and the design of the GUI, the team identified five issues:
- Plant operators had to quickly scan many different process graphic displays and trend displays to understand what was happening throughout the plant, hampering their ability to take quick and appropriate action.
- The information displayed was not color coded based on priority.
- The layout of text, graphics, etc. was confusing and easy to misread, leading to operator errors.
- The overview displays lacked detailed information and were of limited use to the operators.
- Although the operators had access to multiple monitors at their workstations, they had received no training in their use and the extra monitors were not being used.
Yokogawa's industrial design and ergonomics engineers proposed the following solutions
Design of task-based displays
The team reviewed and analyzed how the plant's most experienced operators carry out their monitoring and control tasks, examining the purpose of each task, the data needed, the displays used, how information was used to control an operation, and how information was used to monitor operations. Based on this, the process data was ranked by level of importance and documented in a task analysis sheet.
In the redesign of the displays, careful consideration was given to factors such as the relationships between information, pop-up window position, and navigation between displays. Some of the redesigned task-based graphic displays are shown below.
Improved presentation of process data
In a display, the color of the background, text, and graphics can have a significant impact on usability. Based on interviews with this plant's most experienced operators, and in accordance with ergonomic principles, the project team employed the AOG approach to redesign the GUI color scheme and layout and make process data easier to read. This also was done with CAMS for HIS, a standard consolidated alarm management function for Yokogawa's CENTUM VP PCS that was introduced to address the issue of alarm flooding. After a reprioritization of all the system alarms, the alarm color scheme was redesigned based on priority.
Utilization of KPI display
A KPI display provides information on every aspect of a plant's operations that its operators are responsible for, including output, quality, efficiency, and safety. They help motivate operators by showing how their work impacts plant performance. The following display shows four different types of KPIs and can be viewed on a single large screen positioned behind the double-tiered HMI screens.
Define graphic display hierarchy / monitor layout
To make effective use of the double-tiered HMI screens and a single large screen in the control room, a four-level hierarchy was defined for the graphic displays. Since plant operators mainly interact with task- and plant facility-based displays (levels 2 and 3), these were mainly assigned to the lower monitor in the double-tiered HMI. Level 1 displays along with the level 2 loop-watch displays were assigned to the upper monitor in order to navigate into level 3. KPI display is presented on the single large screen to share plant performance information between all control room users. This arrangement allows operators to stay on top of what is happening throughout the plant and quickly identify any abnormal conditions.
Through the AOG service, other package solutions were also proposed to help this plant achieve operational excellence. For example, to make use of a task time estimation program that INPEX developed, Yokogawa proposed the introduction of the Exapilot operation efficiency improvement package to eliminate operational mistake by manual calculation, and to reduce working time for alternative tanks usage.
Customer Satisfaction
The operators and managers at the INPEX Oyazawa plant initially were not sure how ergonomic design and knowledge-based technology could benefit them, but came to appreciate this approach after seeing how it improved not only alarm design and procedural automation but also the overall operations at their plant. The project team created the radar chart shown on the right, and assigned scores for a range of criteria, before and after this consulting project.
The following points are the major benefits that this project provided to INPEX:
- Shortened operation monitoring cycle
- Timely identification of abnormal conditions
- Fewer operator errors
- Reduced operator workload / eye fatigue
- Improved transfer of skills and expertise
- Increased motivation to improve operations
- Effective operator display design
- Graphic symbols for process displays
- Ergonomic requirements for office work with visual display terminals
- Recommended practice for pipeline SCADA displays
- A PCS graphic design service provided by Yokogawa that is based on human factors engineering and knowledge engineering. AOG emphasizes ergonomic design, and seeks through improved color selection, layout, and so on to improve operators' situational awareness. Based on insights gained from experienced personnel, this ensures operators have ready access to all the information they need to make effective decisions.
Gerelateerde Industrieën
-
Olie & gas
Yokogawa heeft diepgaande ervaring in elk deel van de olie- en gasindustrie. Van offshore- en onshore-installaties tot pijpleidingen, terminals en diepwateractiviteiten. Wij leveren oplossingen die de veiligheid verhogen, een nauwkeurige en betrouwbare werking garanderen en de efficiëntie van de installatie verhogen.
-
Upstream olie & gas
De upstream-industrie omvat offshore- en onshore-activiteiten, waaronder automatisering van boorputten, raffinage, voltooiing en scheiding om ondergronds of onder water ruwe olie en aardgas te winnen en te bewerken.
Wanneer aardolie naar de oppervlakte wordt gebracht, moet het worden gescheiden voordat het wordt vervoerd. Primaire en secundaire scheidingsfasen verdelen gewoonlijk de gasstroom, waterstroom en oliestroom in een driefasen scheiding. Voor het vervoer van gas is een pijpleiding nodig en kan een raffinageproces in de upstream fase voorafgaand aan het vervoer plaatsvinden. Vloeistoffen kunnen via tanks of pijpleidingen voor verwerking worden verzonden, waarbij nauwkeurige niveaumetingen vereist zijn.
Gerelateerde producten & oplossingen
-
FAST/TOOLS
Originating as the Flexible Advanced System Techniques (FAST) project, FAST/TOOLS today is a comprehensive, fully-integrated SCADA application suite. Powerful and flexible, FAST/TOOLS serves installations ranging from 50-point unit processes to multimillion-point offshore production and pipeline systems that extend over thousands of miles.
-
Gedistribueerd besturingssysteem (DCS)
De DCS maakt automatisering en controle van industriële processen en verbeterde bedrijfsprestaties mogelijk. Meer dan 10.000 fabrieken vertrouwen op Yokogawa DCS om hun productiedoelen te bereiken.
-
Procedural Automation (Exapilot)
Procedural Automation (Exapilot) provides a flexible methodology to capture, optimize and retain procedural knowledge in a process plant while meeting requirements in reliability, flexibility, and lifecycle costs.