Comprehensive Temperature Monitoring That Can Quickly Detect and Identify Abnormalities in Plant Equipment Without Omission
To date, temperature monitoring of plant equipment has often relied on spot sensor monitoring or human patrols, making it difficult to reliably monitor temperatures without blind spots resulting from technological and cost barriers. Meanwhile, deteriorating facilities, the aging of veteran employees, and a shortage of personnel continue to pose significant challenges for companies in implementing HSE (Health, Safety, Environment) policies.
Yokogawa Electric’s Fiber Optic Temperature Sensor DTSX solves these problems. Predictive maintenance using fiber optic temperature sensors is now being introduced in a wide range of fields, including steel, electric power, and chemical plants, as well as transportation infrastructure.
DTSX, the Fiber Optic Temperature Sensor
Using sensing technology that takes advantage of the characteristics of fiber optic cable, DTSX is a temperature sensor that can be laid out following the shape of the object to be measured. By detecting temperature changes over long distances and across wide areas in real time, equipment abnormalities can be detected at an early stage. The strength of this system is that it can measure and monitor an entire factory, including areas that are difficult to measure with conventional fixed-point temperature sensors and thermal cameras. As a complement to point and surface monitoring, constant line monitoring makes a substantial contribution to predictive maintenance of production facilities and social infrastructure.
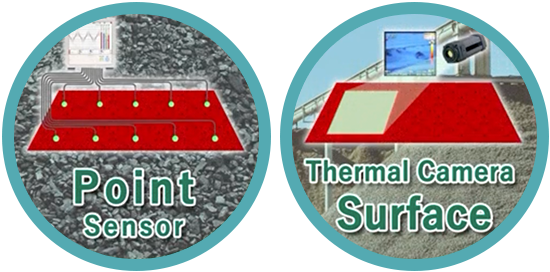
The Temperature Monitoring the DTSX Provides
- Monitoring distance: to 50 km
- Monitoring temperature: -200 to 300 °C
- Shortest monitoring cycle: Approx. 5 seconds
- Temperature resolution: 0.03°C
- Fire detection standard (EN 54-22) certification acquired (DTSX1)
* Each specification dependent on conditions
Difference Between Predictive and Preventive Maintenance
What is “predictive maintenance”?
This is a maintenance method in which plant facilities are constantly monitored to detect signs of trouble. Data collected by sensors installed on production lines, etc. is analyzed and assessed, and countermeasures are taken as appropriate for the conditions. As such, it can be considered a kind of CBM (Condition-Based Maintenance).
What is “preventative maintenance”?
This is a maintenance method that prevents problems by periodically inspecting and maintaining plant facilities. Regardless of whether the equipment is in good or bad condition, at a certain point in time, parts replacement and other maintenance will be performed. As such, it can be considered a kind of TBM (Time-Based Maintenance).
-
DTSX1 Fiber Optic Heat Detector
DTSX1 stores the functions required for heat detection in one box. DTSX1 analyzes the temperature data with high accuracy by measuring with fiber optic sensor cable and perform high temperature heat detection.
-
DTSX3000 Distributed Temperature Sensor
The DTSX3000 is a distributed temperature sensor developed in response to the demand that “one unit be used to monitor temperature distribution a longer distance and a wider area”. A flagship model that meets the expectations for long-distance temperature measurement and high temperature resolution.
-
DTSX200 Distributed Temperature Sensor
The DTSX200 is a standard version that is ideal for temperature measurement, for medium-sized areas, and for areas where the distance of fiber optic sensor cables is short. It has excellent environmental resistance because it consumes less power and is less dependent on the temperature measurement environment.
Details
Advantages of the Fiber Optic Temperature Sensor DTSX
Failure to detect equipment abnormalities, such as unusual temperature rises, can lead to fire or malfunctions if left undetected. The DTSX provides efficient predictive maintenance by constantly monitoring temperature changes without omission, thereby preventing problems before they occur.
Constant Monitoring 24 Hours a Day, 365 Days a Year
Patrols and other labor-intensive monitoring methods involve a heavy workload and the risk of danger. If a problem occurs outside of patrolling hours, detection may be delayed and damage may spread.
By installing the DTSX on the object to be measured, it can be remotely monitored 24 hours a day. Problems can be detected quickly and their location identified, thus minimizing damage. This also reduces human labor, thereby avoiding hazards and reducing costs.
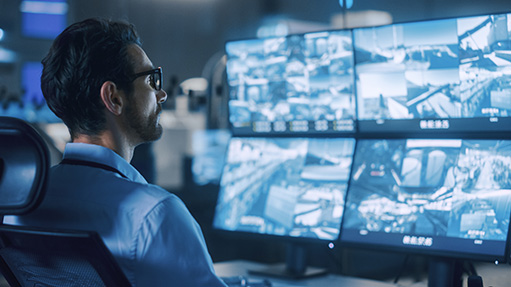
Reliable Temperature Monitoring Over Long Distances and Wide Areas
Conventional fixed-point temperature sensors, thermal cameras, and patrols are extremely expensive and do not provide reliable, omission-free temperature monitoring over long distances or wide areas. To start with, there are areas that cannot be measured or monitored on points or surfaces, and areas that are not easily accessible to people.
The DTSX can provide uninterrupted, highly accurate measurements over long distances of up to 50 km using fiber optic cables, allowing real-time monitoring of temperature changes. Predictive maintenance is achieved through comprehensive temperature monitoring of the entire plant.
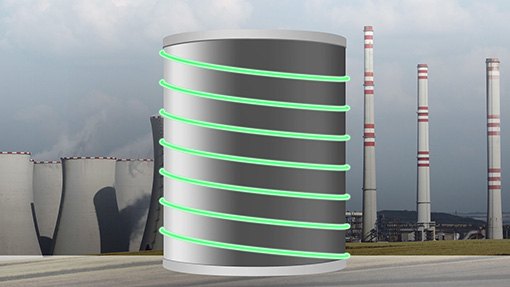
Flexible and Simple Installation
Multi-point measurement using fixed-point temperature sensors requires cables for each point, complicating the system configuration and installation work.
Conversely, system configuration for the DTSX is extremely simple. It can be laid out flexibly along the path and shape of the object to be measured, and measurement is performed with a single fiber optic cable. Fiber optic cables are themselves conductors, so they do not require compensating lead wires. In addition, compared to long-distance and wide-area temperature monitoring using other kinds of temperature sensors, installation and operation costs are low.
High Compatibility With Production Control Systems
A temperature monitoring solution is only truly effective when it is coupled with a production control system or monitoring system that provides integrated management of the entire system lifecycle.
DTSX is highly compatible with Yokogawa Electric’s signature integrated production control system DCS (Distributed Control System) and wide-area distributed monitoring system SCADA (Supervisory Control and Data Acquisition), making it easy to build integrated management and monitoring systems. As such, it contributes not only to measurement but also to optimal management and operation of the entire facility.
Example of linkage with production control system
Excellent Environmental Resistance
Fiber optic sensors do not use electrical or electronic components in the sensor section, and therefore offer superior environmental resistance compared to other temperature sensors.
They are not affected by electromagnetic noise, whether in environments where electromagnetic waves are generated, such as near power sources, or if there are lightning strikes. Moreover, because they do not use electricity, they can be used in explosion-proof areas. They also have the advantage of high durability, enabling stable measurement over a long period of time and reducing the overall running costs of the monitoring system.
Expected Benefits
- By quickly detecting equipment abnormalities that could lead to fires and other problems and identifying their location, accidents can be prevented and stable operation achieved.
- Long-distance, wide-area, 24-hour remote monitoring solves the challenges of personnel shortages and monitoring costs.
- Switching from periodic preventive maintenance (TBM) to predictive maintenance performed according to conditions (CBM) improves the efficiency and quality of maintenance operations.
Industries/Applications Served by DTSX
The economic and social losses incurred when a production line is shut down due to a major fire or equipment failure are immeasurable. DTSX helps maintain stable plant operations, protecting customer assets and public confidence.
Continuous Temperature Monitoring of Bus Ducts (Bus Bars)
Bus bars, which stably supply large amounts of current to manufacturing facilities, are often covered with bus ducts for safety reasons. Since bus bars are often installed in dangerous and harsh locations such as underside of the ceilings, high places and under floors, it is difficult to detect promptly abnormal thermal patterns such as abnormal temperature.
As a benefit of continuous temperature monitoring of bus ducts (bus bars) by DTSX, it enables not only prompt detection of abnormal temperature, but also enables preventive maintenance of facilities, stable operation, and BCP (Business Continuity Plan).
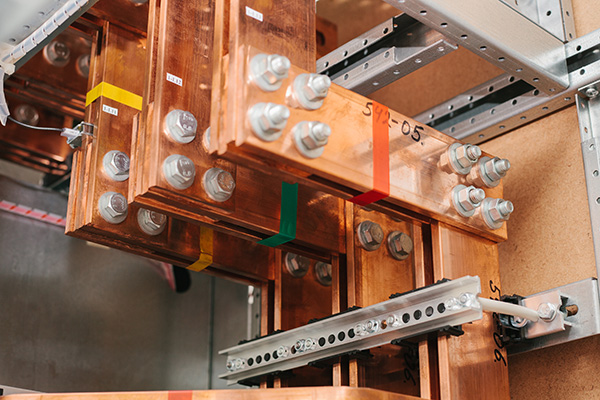
Manufacture of In-vehicle Lithium-ion Batteries
In some cases, lithium-ion batteries can experience sudden rises in temperature, resulting in thermal runaway. In factories that manufacture large quantities of lithium-ion batteries, it is essential to monitor temperatures in manufacturing process shelves, storage shelves, and exhaust ducts.
Just by laying cables, DTSX can provide thorough comprehensive monitoring of large shelves, and can also monitor ducts in ceiling cavities that are out of human sight. This allows supply chain disruptions resulting from unforeseen shutdowns to be avoided.
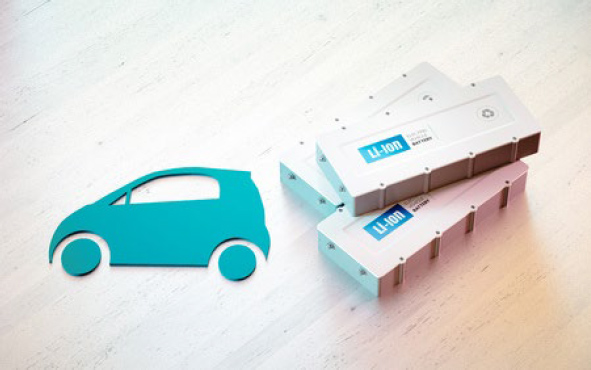
Conveyor Belt Rollers
Fires caused by roller failure on long-distance conveyor belts in large mining facilities can lead to unexpected shutdowns. For example, a mere one-hour shutdown at a major mine can result in production losses of approximately 50 million yen.
DTSX enables constant remote monitoring of all conveyor belt rollers, something that is difficult to achieve with human inspection and fixed-point sensors, thereby helping to avoid stoppages and maintain stable operations.
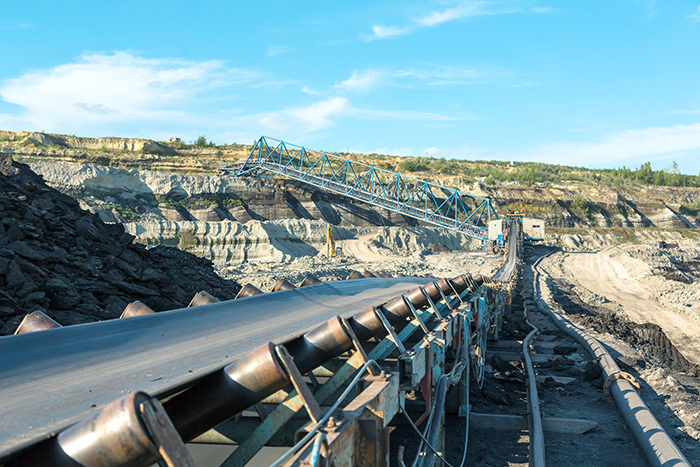
High-Temperature Furnaces
The manufacturing industry operates a wide variety of high-temperature furnaces. If the firebricks attached to the inside of a furnace deteriorate or fall off due to aging or other factors, not only will this cause increased heat dissipation and reduced combustion efficiency, but it may also lead to accidents such as a rupture of the outer steel shell or an emergency shutdown of the process.
DTSX monitors changes in the temperature of the furnace wall surface to quickly detect abnormalities in the inner wall and prevent problems before they occur.
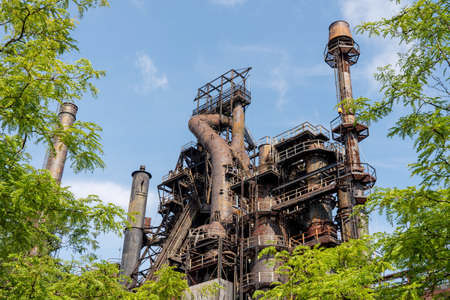
Application Example
Superior Solutions in CAPEX and OPEX
Because a fiber optic cable serves as the temperature sensor, the cable can be simply laid at the site, and no power supply or other installation work is required. In addition, because there are no mechanical components in the fiber optic sensor cable, it is not susceptible to failures. When used to monitor temperatures across wide areas, it optimizes disaster prevention and maintenance costs through lower CAPEX (capital expenditure) and OPEX (operating expenses) than other temperature sensors.
Applications and Compatible Models
Ressources
What if you could detect signs of abnormalities in bus ducts (bus bars) quickly during maintenance and inspection work and respond to them at just the right time? Yokogawa DTSX monitoring solution constantly monitors connections that tend to deteriorate over time and contributes by pinpointing abnormality locations and reducing workload of maintenance personnel, helping to ensure stability in plant operations.
A belt conveyor fire detection solution employing the DTSX distributed optical fiber temperature sensor can greatly reduce crises that can threaten a company's survival.
Smart Monitoring of Manufacturing Process Shelves and Storage Shelves (In-vehicle Lithium-ion Battery Applications)
Prevention of Fires in Exhaust Air Ducts in Battery Assembly Process (In-vehicle Lithium-ion Battery Applications)
Temperature Monitoring Solution for
Quick Detection of Fires in Fume Ducts
Monitoring of Soundness of Power Supply Bus Bar (In-vehicle Lithium-ion Battery Applications)
Monitoring of Separator/Electrode Drying Furnace Temperature Distribution (In-vehicle Lithium-ion Battery Applications)
With industrial and economic development comes increasingly large and advanced power plants and factories. Nevertheless, we find many cases where the original cables, cable tunnels, and other components of the power infrastructure have languished under continuous operation.
Reactor/Furnace Wall Healthiness Monitoring with a Fiber Optical Temperature Sensor
Temperature Monitoring Solution forMaximum VSD Operating Efficiency
Downloads
Brochures
- Distributed Temperature Sensor DTSX3000/DTSX200 (2.1 MB)
- Temperature Sensing Solutions (596 KB)
Communiqués de presse
-
Communiqué de Presse | Solutions & Products Dec 11, 2024 Yokogawa Releases OpreX Subsea Power Cable Monitoring to Detect Damage and Enable Condition-Based Maintenance at Offshore Wind Farms
-
Communiqué de Presse | Projects Feb 15, 2024 Yokogawa Provides Remote Operation/Monitoring System and Video Monitoring Solution for Japan's Largest Wind Farm
- Achieving system-wide optimization of offshore wind turbines and onshore facilities -
-
Communiqué de Presse | Solutions & Products Dec 27, 2021 Yokogawa Commences Research Project with JAXA Space Exploration Innovation Hub Center
Contributing to the safety of space facilities through research and development of optical fiber sensing technology
-
Communiqué de Presse | Solutions & Products Oct 15, 2018 Yokogawa Releases the DTSX™1 Fiber Optic Heat Detector
-
Communiqué de Presse | Solutions & Products Aug 11, 2014 Yokogawa Releases DTSX3000 Distributed Temperature Sensor
- Industry-leading measurement distance and temperature resolution for maintenance of plants and other infrastructure -
Rechercher plus d'informations sur nos compétences, technologies et solutions
Contactez-nous