Energy Monitoring understands and visualizes your energy usage. Yokogawa and KBC offer the solutions and services needed to overcome your energy monitoring challenges.
Click here to learn about Energy Monitoring
Key areas for Operational Excellence Transformation
Operational Excellence Transformation is Yokogawa and KBC’s co-innovated portfolio of solutions and services.We provide comprehensive solutions for business automation in all four areas using consulting and digital technology.
Asset Operations and Optimization
Asset Operation and Optimization deals with realizing the potential of physical assets by pushing throughput and maximizing the production of the highest-value products, while minimizing variable costs, such as energy. It ensures small and large capital expenditure projects are delivered on time and on budget, to achieve growth and meet environmental requirements. Through these competencies, it will be possible for companies to take full advantage of their physical assets. Yokogawa’s Asset Operation and Optimization solution leverages industry-leading technology to generate precise operating information to increase operator insight, ultimately leading to improved performance and profitability.
Key Operational Competencies in Asset Operations and Optimization
- Asset Strategy: Define the requirements of plant capacity, operability and production to align with corporate strategy.
- Asset Improvement: Improve plant profitability by expanding plant operating window and/or adding/modifying plants
- Asset Optimization: Optimize the plant by enabling shift teams to execute activities as per plan and within operating window boundaries
- Asset Operations and Process Control: Operate the plant by enabling shift teams to implement plans effectively and manage abnormal situations
- Capital Projects Delivery: Screen options, engineer and deliver capital projects that are cost-effective, timely and fit for purpose
With our track record of providing project execution and thorough lifecycle services and KBC consulting, our customers can obtain practical and deep insights on maximizing their physical assets. Together, we aim to contribute and actualize improvements not only for profitability, but also for overall safety, operability and reliability.
·Supply Chain Optimization
- Optimize management of supply, whether oil in the ground or feedstocks for a refinery or chemical asset, in light of product market demands. This provides operators with the agility to take full advantage of market conditions.
·Operational Risk Management
- Reliably control safety, health and environmental risk at a personal and process level. This assures the robustness required to avoid catastrophic losses.
·Asset Management and Integrity
- Confidently ensure asset reliability and availability, whilst controlling maintenance costs. This assures the asset always meets expectations and is always available to capitalize on short term market opportunities.
Energy Monitoring
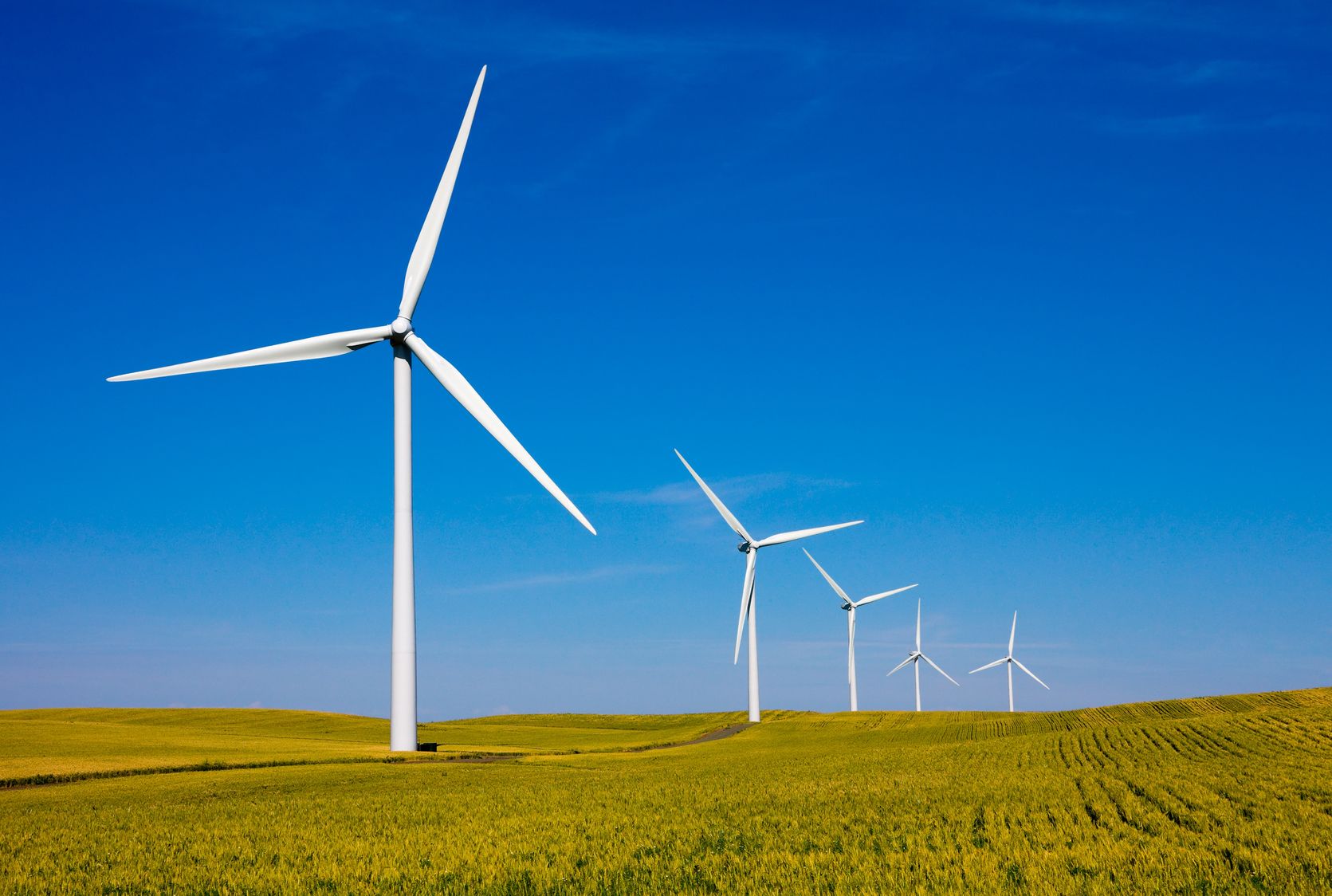
Improving manufacturing efficiency demands constant action. From uncovering operational waste to identifying areas for continuous improvement, we must always pursue a cycle of visualizing, analyzing, and solving energy saving challenges. Together, Yokogawa and KBC offer the solutions and services needed to overcome your energy monitoring challenges.
Customer Challenge
Different Companies, Different Challenge
Challenges can vary and range from turning off lights and saving energy in individually powered equipment such as boilers, pumps, and compressors - to overall energy management in factories and companies (FEMS*). Yokogawa aims to play a significant role in supporting these energy saving measures for customers worldwide, for a better future.
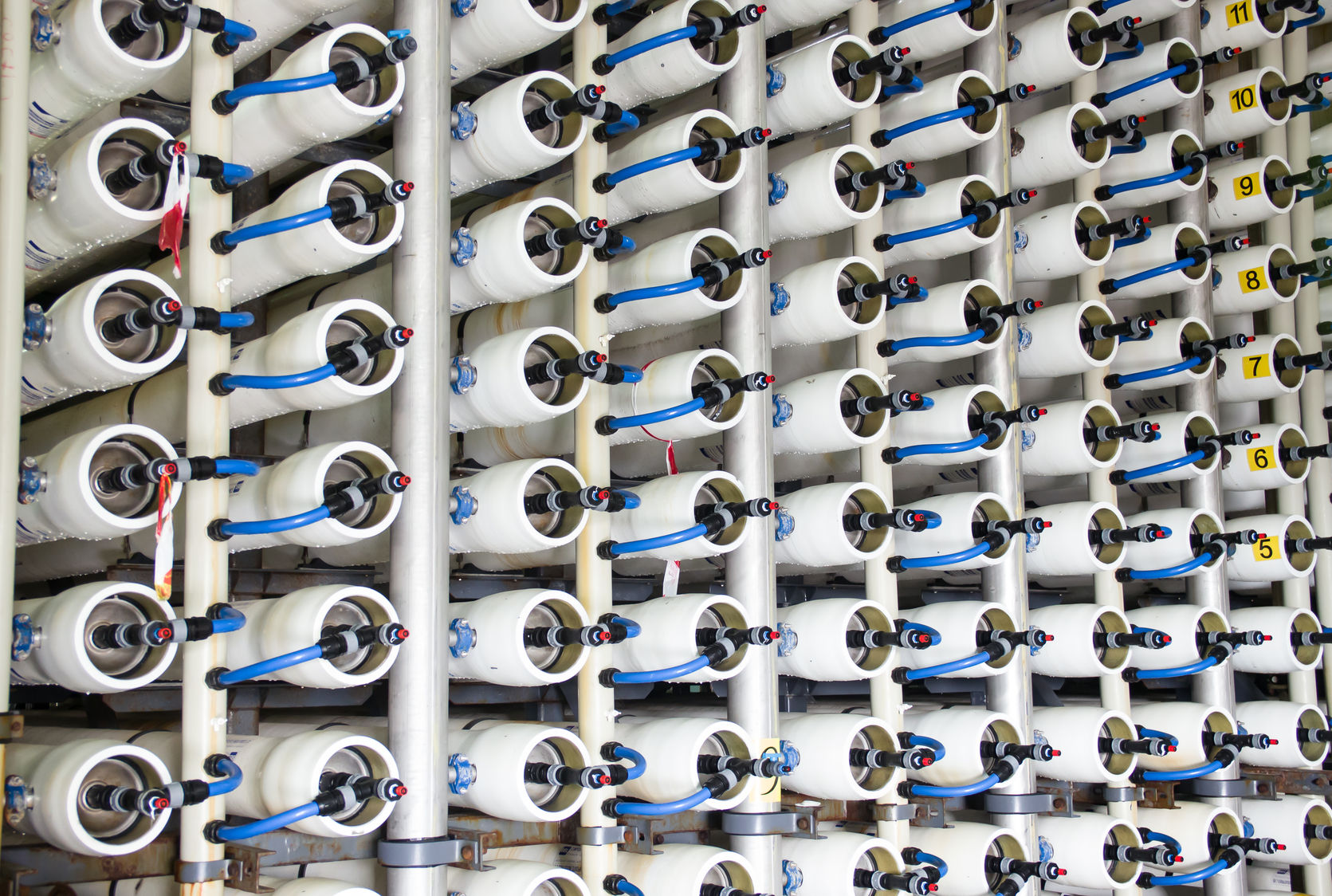
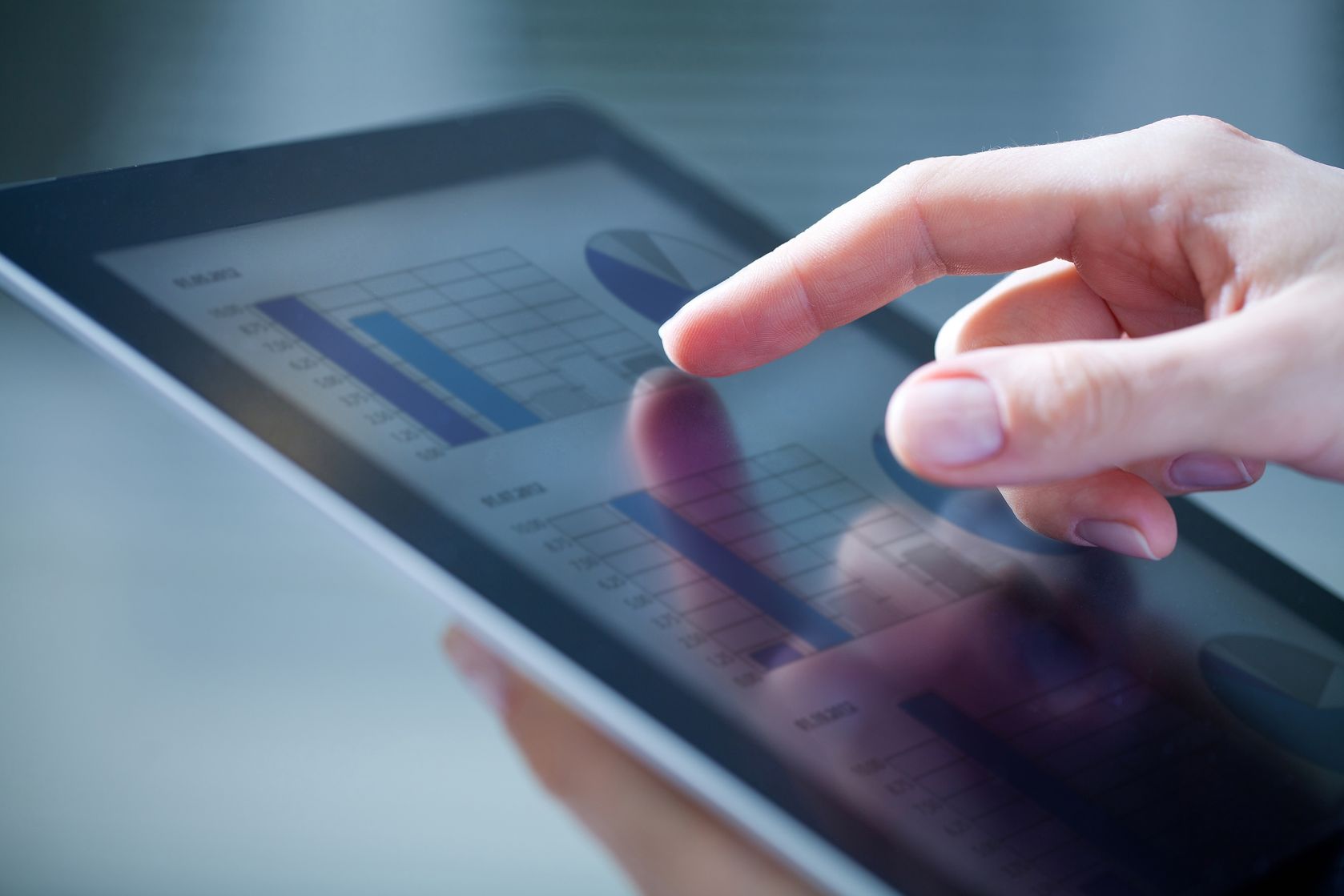
Our Solutions
Understand and Visualize Your Energy Usage with Visual MESA
The first step in creating an energy saving plan is to understand the current situation. By measuring energy and visualizing it in graphs and reports, we can identify waste and discuss savings targets. At plants with diverse energy sources, it is difficult to fully ascertain usage conditions. In addition to power, we must measure air conditioning, steam flow, and other quantities to understand the comprehensive consumption patterns from the offices to the factories. We can also look at the energy consumption as it relates to the in-service conditions at the factories. While energy is needed to make things, it's not uncommon to discover energy overuse due to the tendency to emphasize quality and ease of manufacture. To continuously work toward energy savings, it is urgent that we visualize energy usage, and develop a comprehensive solution form that point forth.
Customer Benefits
Tailored Solutions Lead to Specific and Continuous Benefits
After having a complete and comprehensive understanding of the current state, facilities are able to set benchmarks and specific goals for what they would like to achieve. Common benefits are as follows:
- Gain awareness of operational waste; monitoring these areas to make continuous improvements
- Identify sources of waste in real-time
- Set energy usage targets at individual factories and offices
- Create mechanisms through which anyone, anywhere, anytime can visualize the results of continuos improvements
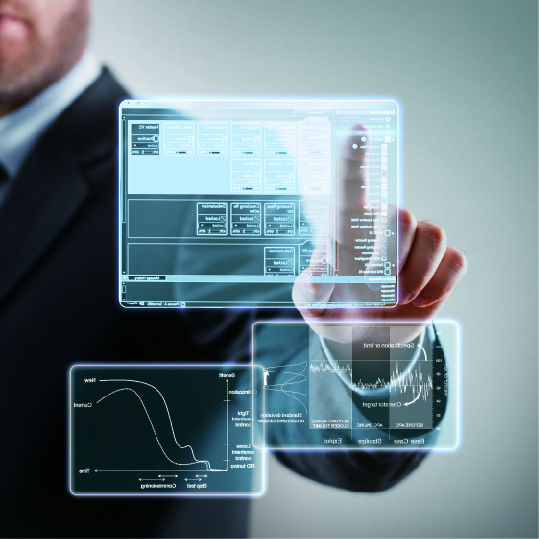
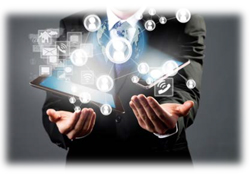
Enabling Technology
Energy Monitoring Give You What You Need to Ensure Continuous Improvements in Your Energy Saving Efforts
Energy Monitoring is powered by a model-based calculation engine which is the Visual MESA rigorous, first principle, energy calculation software based on the Visual MESA simulation engine. It calculates EnPIs, mass balances and other energy-related data, and has capabilities of Data Validation, Energy Balance and Mass Balance.
Energy balance is calculated based on the energy consumption within boundaries such as each plant or equipment. Mass balance is calculated based on balance error of energy sources such as steam, electricity and fuel.
For more information: Visual MESA
Ressources
Adding process considerations improves energy savings and production performance.
Downloads
Brochures
Rechercher plus d'informations sur nos compétences, technologies et solutions
Contactez-nous