What is Field Asset Analytics (InsightSuiteAE)
InsightSuiteAE (ISAE) has the capability to diagnose production equipment and field devices around it together, it is easy to identify the cause of abnormalities, which leads to reduction in production risk.
ISAE helps customers to prioritize the right equipment for maintenance and the plant will become more stable.
Click here to learn more detail about Field Asset Analytics (InsightSuiteAE).
Key areas for Operational Excellence Transformation
Operational Excellence Transformation is Yokogawa and KBC’s co-innovated portfolio of solutions and services.We provides comprehensive solutions for business automation in all four areas using consulting and digital technology.
Asset Management and Integrity
Asset Management and Integrity practices are critical to ensure reliability and availability of such assets while keeping maintenances costs to a minimum, and to capitalize on short-term opportunities in the market. With domain knowledge and experience, Yokogawa and KBC ensures its customers maximize their assets' value through asset management and integrity products, services and solutions.
Key Operational Competencies in Asset Management and Integrity
- Maintenance and Integrity Strategy:
Determine the best asset maintenance and integrity strategy based on equipment integrity objectives, as well as corporate and asset portfolio strategies - Asset Care Planning:
Provide systems and methodologies to optimally define the activities needed to maintain equipment in its designed operating conditions - Reliability Assurance and Analytics:
Provide analysis of equipment health to determine the best maintenance approaches. - Defect Elimination:
Identify activities that mitigate and eliminate sources of unreliability to assets or facility systems - Inspection:
Review inspections performed on equipment to identify specific maintenance activities. This will be done in coordination with, or by, the inspection group. - Contractor Management:
Manage contractors to utilize their services efficiently and effectively - Minor Projects Delivery:
Screen options, engineer and deliver low- or no-capital projects to replace existing equipment or achieve incremental improvements that are cost-effective, timely and fit for purpose - Turnaround Maintenance:
Perform special equipment maintenance to retain asset design and operational integrity. This involves longer shutdowns or outages of the unit or the system. - Routine Maintenance:
Perform normal equipment maintenance during operations to retain asset design and operational integrity. This involves short-term or low-impact shutdown of the unit or the system.
In addition, through Yokogawa’s reliability-based Asset Management portfolio, our customers can:
- Contribute directly to corporate goals and objectives ;We help our customers assess and design how they utilize their assets to achieve the following:
- Reduction in production cost per unit
- Reduction in unplanned breakdown of assets
- Increase in efficiency of maintenance operators
- Reduction in safety and environmental-related incidents
- Enable informed and operations-centric decision-making
We combine risk and reliability best practices with our customers’ actual plant operations set up to identify and focus on critical assets that drive the largest contributions in their company. By identifying critical assets – failure root causes and recommended actions – resources and requirements are prioritized accordingly, in consideration of associated risks and consequences.
Supply Chain Optimization
Optimize management of supply, whether oil in the ground or feedstocks for a refinery or chemical asset, in light of product market demands. This provides operators with the agility to take full advantage of market conditions.
Asset Operations and Optimization
Optimize the potential of physical assets, by pushing throughput and maximizing the production of the highest value products, whilst minimizing variable costs such as energy.
Deliver small and large capex projects, on time and on budget, to deliver growth and meet environmental requirements.
Operational Risk Management
Reliably control safety, health and environmental risk at a personal and process level. This assures the robustness required to avoid catastrophic losses.
Field Asset Analytics (InsightSuiteAE)
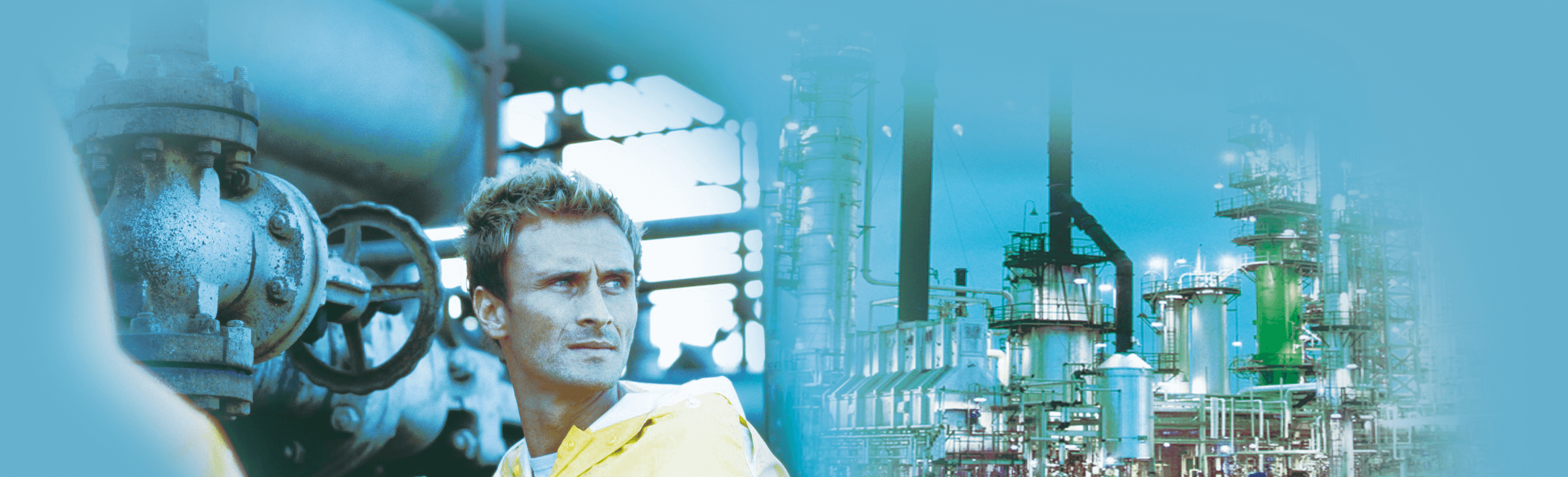
Improve Plant Asset Productivity
With the increasing demand for energy that has accompanied the economic growth of newly industrialized nations, companies need to find every possible way to add value and max out the efficiency of their production processes. And they must find a way to do this without doing harm to the environment and while complying with stringent HSE regulations.
Yokogawa has solutions for a sustainable future that solve the issues you face with your plant assets. We can detect problems at an early stage and put forth proposals that show you the way forward to achieving concrete improvements. We make it possible for you to slash your plant asset operating and maintenance costs while reducing both energy consumption and carbon emissions.
Optimized Operations and Maintenance
Three steps have proven effective in optimizing the efficiency of plant assets. Choose any one of these steps, depending on the condition of your plant assets, as your entry point for using our state-of-the-art diagnostics and services. In this, Yokogawa will work with you in a collaborative efort to get the maximum possible productivity out of your plant assets.
SEE CLEARLY with a birds-eye view, the condition of your plant assets by providing diagnostic solutions
KNOW IN ADVANCE what must be done to optimize these plant assets by providing information-intensive service solutions that precisely detect and analyze their conditions
ACT WITH AGILITY to implement proposals that resolve specific issues and acheive improvements
Challenges for Management and Field Operators
- Increasing Availability
- Improving Efficiency
- Reducing Maintenance and Operating Costs
- Saving Energy
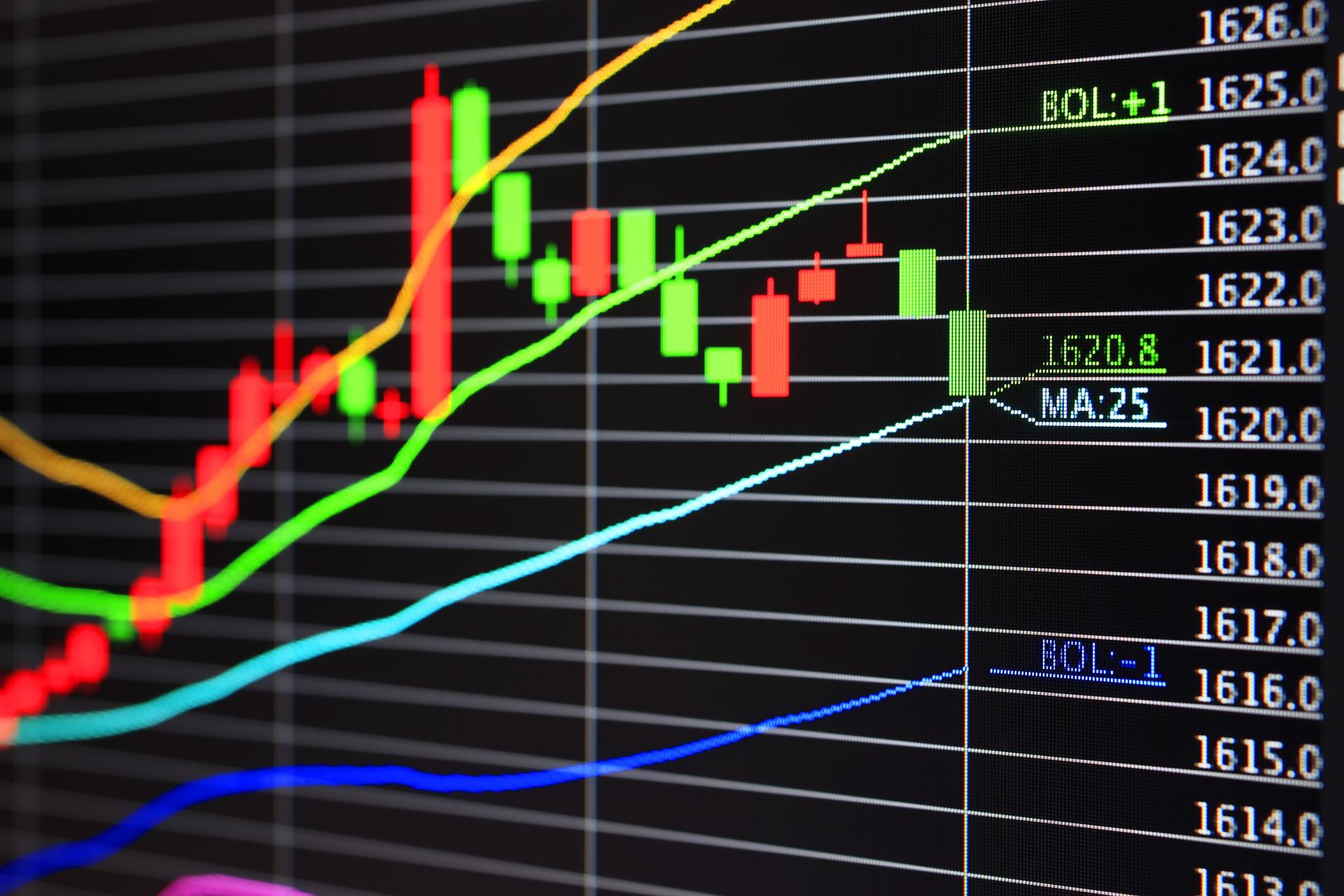
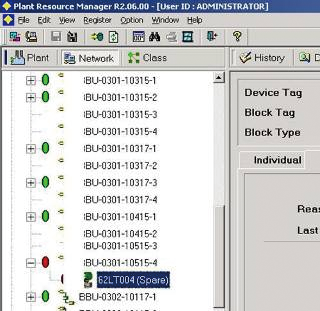
Field Digital Baseline Tuning
The Importance of Field Digital Solutions
One of the major advantages of field digital solutions is the ability to gather large amounts of information on Foundation fieldbus & HART assets. Customers blieve they will have this advantage and be able to reduce downtime and maintenance costs if they install an online and centralized automated asset management system such as PRM. However, if PRM is not effectively managed and alarms and events are not handled correctly, it may be difficult to grasp and diagnose actual asset conditions, negating some of the benefits of field digital solutions
As part of its InsightSuite services solutions, Yokogawa performs field digital baseline tuning of Foundation fieldbus & HART devices to optimize PRM's alarm and event conditions, enabling a condition-based maintenance (CBM) approach that paves the way for asset excellence.
Challenge to Customers
A flood of difficult to comprehend information from field devices
- Root causes of asset problems are difficult to identify and analyze
- Asset management is nearly impossible to plan
- Unable to make optimum use of PRM's solution-oriented functions that can reap the full benefits of plant assets
Benefits and Solutions and Benefits to Customers - Data Analysis, Analysis Report, Detailed Analysis, Countermeasures
working together with the PRM data analysis functions, the InsightSuiteAE service tool facilities the categorization of PRM data and the visualization of actual asset conditions
Yokogawa consulting services identify problematic assets and present solution
InsightSuiteAE's reporting and consulting services enable customers to implement CBM and facilaitate asset management decisions
Asset countermeasures are adapted not only in PRM but also in the device settings, one of the most important and critical steps in advanced diagnostics that promotes asset excellence throughout the plant lifecycle.
Control Valve Diagnostics
The Challenges for Customers
Control valve management plays a key role in optimizing the performance of plant assets and achieving operational excellence.
- High maintenance costs as a result of the frequent need for complex adjustments
- The need to stop or slow down a production line in order to troubleshoot a control valve
- Inaccurate control valve and valve positioner diagnostics
- Insufficient resources for diagnosing and analyzing control valve data from valve positions
- The difficulty of setting up and configuring intelligent valve positioners
Key Features of InsightSuiteAE
- Makes it possible to quickly identify control valve problems
- No special skills or knowledge of terminology required to perform configuration
- Easy to use regarless of valve positioner model
- Like a radar, scans 24/7 for control valve problems
- No need to reconfigure or reset a value positioner to perform diagnostics
- No longer necessary to shut down a control valve and change its parameters to carry out diagnostics
- Employs algorithms that aid understanding by quantifying the impact of valve problems on loop KPI's and automated systems
Benefits for Customers
- Intuitive green (healthy) and red (unhealthy) valve status display quickly identifies problems
- Provides the information needed to make timely valve maintenance decisions. Enables a more proactive maintenance approach.
- User-friendly features eliminate the need for detailed knowlege about valves and field digital protocols
- InsightSuitesAE non-invasive and read-only diagnostic techniques cause no trips or system disturbances
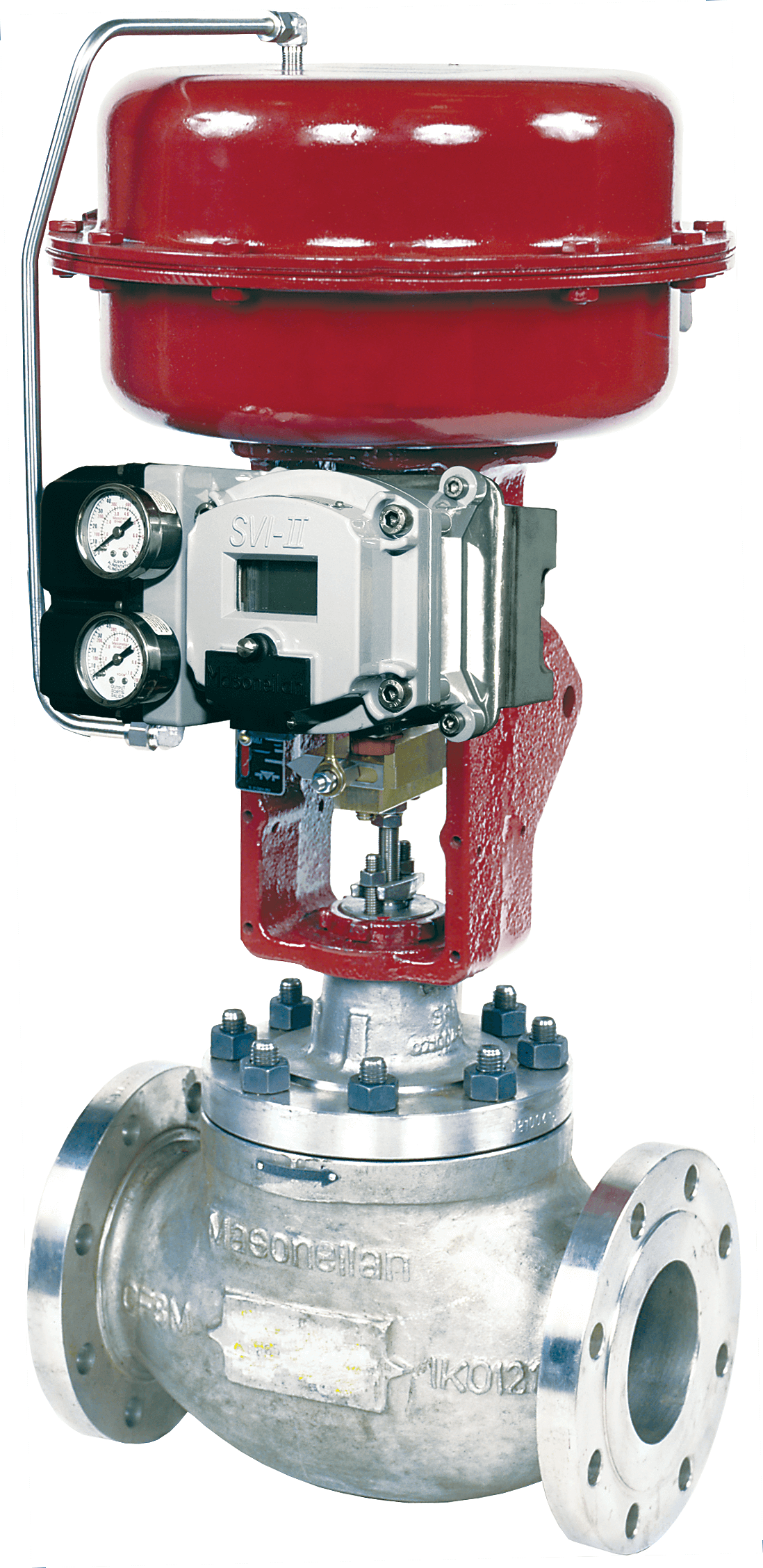
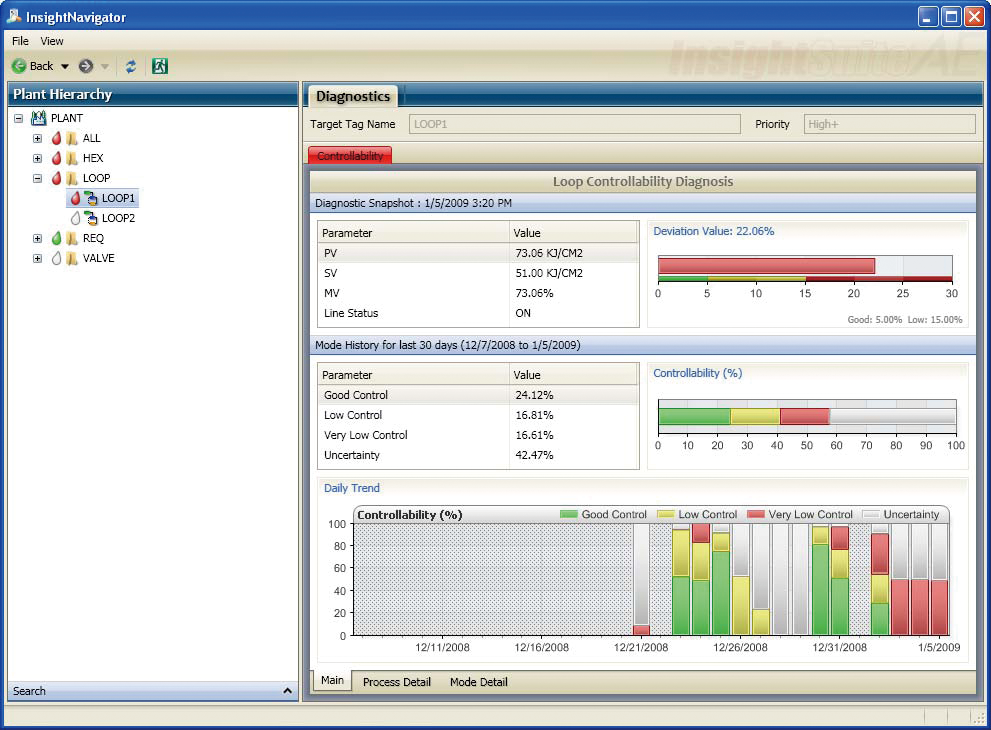
Control Loop Diagnostics
"The ability to quickly and easily identify problems by monitoring all control loops provides a strong foundation for stable plant control"
The Importance of Control Loop Diagnostics
High level plant control is the foundation for productivity improvements. An ideal plant is achieved by optimized plant control, which increases productivity by ensuring that process units and other plant assets operate stably.
While price competition has become increasingly fierce, the number of board operators and maintenance peoples is markedly decreasing due to a shrinking workforce and the retirement of experienced personnel. Our InsightSuiteAE control loop diagnostics service enables board operators and maintenance people to do real-time monitoring of all their control loops at a glance and to quickly and easily identify which ones require maintenance. As a result, it reduces their workload.
In addition, by combining our control loop and control valve diagnostics, major problems such as inadequate tuning of control loops and/or control valves and incorrect configuration of control loops can be better understood.
Benefits to Customers
With Yokogawas consulting and reporting services, customers can identisy and gain insight into problems. It is possible, for example, to identify whether all control loops are operating properly and are correctly automated. We provide the following solutions that make it possible for our customers customers to minimize their maintenance costs:
Evaluation of control loops using simplified key performance indicators (KPIs). No special skills or knowlege of terminology is required to grasp the loop conditions.
Decision support for operators and maintenance people concerning remedial actions that will improve control loop controllability. This includes the generation of a list that will clarify problematic loop behaviors.
A consulting service that identifies problem areas in control loops and analyzes their root causes.
Yokogawa control loop diagnostics use engineering data from the CENTUM distributed control system (DCS). The combined diagnostics for control valves and control loops use engineering data that has been recorded by Plant Resource Manager (PRM). With these tools, it si possible to quickly diagnose problems and change settings.
Vidéos
Yokogawa's InsightSuiteAE leads to the revolving of the plant assets issues throughout the plant life cycle.
Rechercher plus d'informations sur nos compétences, technologies et solutions
Contactez-nous