Introduction
Industrial Combustion sources such as thermal cracking furnaces and, process heaters play a critical role in the process industry. Because the large amount of fuel such as gas or fuel oil which is consumed in these processes, their combustion efficiency directly affects the performance and operational costs of the production facilities.
Incomplete combustion and the use of too much excess air can lead to higher level of toxic emissions such as CO (carbon monoxide), CO2(carbon dioxide), NOx (nitrogen dioxide), and SO2 (sulfur dioxide).
Challenges
Combustion requires fuel and air (oxygen), and insufficient air causes fuel residue, resulting in incomplete combustion with soot and smoke. On the other hand, excessive air caused problems, such as a larger amount of exhaust gas and heating of excessive air, resulting in lower fuel efficiency. Figure 1 shows the principle of the air-fuel ratio and state of combustion. The air-fuel ratio plotted on the horizontal axis shows the ratio of actual supply air to the theoretical amount of air required for fuel combustion (theoretical air amount).
For combustion furnaces such as heating furnaces and boilers in plants and factories, small-scale controllers such as single loop controllers are employed to optimize the air-fuel control ratio for improving the combustion efficiency. In large combustion furnaces, distributed control systems (DCS) and advanced control (multivariable predictive control, etc.) are used. These mainly control the air-fuel ratio and internal pressure of the furnace to prevent CO, CO2 and NOx (nitrogen oxide) from being emitted and apply a cross limit circuit to prevent incomplete combustion while controlling combustion to maximize efficiency.
Figure 1 : Relationship Between Air-Fuel Ration and Heat Efficiency (Combustion)
Solution
Overview of the TDLS8000 Laser Analyzer
Figure 2 shows the appearance of the TDLS8000 laser analyzer. This analyzer measures the process gas component concentration using tunable diode laser absorption spectroscopy (TDLAS), which measures molecule-specific optical absorption spectra. Figure 3 shows an example of using the TDLS8000 to measure the concentration of flue gas.
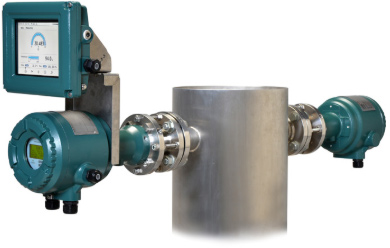
To measure spectra, we employ our originally developed peak area method for accurate measurement even in process environments where the composition, pressure and temperature fluctuate simultaneously. The TDLS8000 suffers no component interference owing to its high spectrum measurement resolution and is directly installed in a process enabling the laser beam to travel through the process windows in a non-contact measurement as shown in Figure 3.
Figure 3 : Installation Example of the TDLS8000
The specific process gas of interest can be reliably measured in near real-time (5 seconds) and at high speed even in high temperature (Max. 1500ºC) or corrosive environments. This advantage enables analysis signals to be utilized directly for process control and management systems, and the TDLS8000 has been rapidly introduced in various industries such as refineries, petrochem, iron and steel and thermal power generation to achieve process improvement and safe operation.
Measurement of O2 and CO Concentrations in Combustion Gas by the TDLS8000
Figure 4 shows an example of using the TDLS8000 analyzer to measure O2 and CO concentrations in a combustion furnace. This example shows that concurrent measurement of O2 and CO concentration while gradually and manually reducing the amount of air supplied to the burner. This experimental data describes the situation; CO generation begun nearly at the O2 concentrations of 2% and sharply increased at the concentration of almost 1.5%, resulting in incomplete combustion, then by increasing the amount of air supply to avoid incomplete combustion, the O2 concentration rapidly increased and the CO concentration decreased again, resulting back to complete combustion. This data also indicated that the CO concentration increased from 100 ppm to 4,000 ppm in just a few minutes.
Figure 4 : O2 and CO Concentration Changes in a Combustion Furnace at Low Oxygen Concentration Operation
Air-Fuel Ratio Control Utilizing CO and O2 Concentrations
According to Lyman F. Gilbert, the CO concentration in the optimum combustion zone (having the highest heat efficiency per unit amount of fuel) is around 200 ppm irrespective of fuel types and devices. However, CO concentration increases rapidly once it has broken through as shown in Figure 4. Thus, either a stable combustion must be kept with sufficient supply of air or a control system must monitor the CO concentration in real-time and keep it constant at a relatively low level.
The amount of air supplied to a burner is controlled by two methods: using a forced draft fan (FD) and damper as shown in Figure 5, or using natural air intake by controlling the opening degree of the damper of an induced draft fan (IDF). The O2 and CO concentrations are measured by the TDLS8000 at the entrance of the flue and then supplied to the control system. The measured CO concentration can be used for combustion control by two methods: controlling O2 when the O2 concentration exceeds a prescribed value and overriding to CO control when the O2 concentration falls below the value, or giving a CO concentration bias (compensation) to the O2 concentration.
Figure 5 : CO and O2 Control System for Combustion Furnaces
Estimation of Economic Effects by Air-Fuel Ratio Improvement
Because the fuel required for generating the same amount of energy can be saved by lowering the set value of O2 concentration in exhaust gas when performing air-fuel ratio control, the direct economic effect by the decrease of O2 concentration in exhaust gas can be estimated. As the economic effects by the improvement, reduction in fuel cost which can be achieved by reducing the excessive O2 while keeping the furnace temperature constant is calculated. Table 1 summarizes a calculation example.1
Table 1 : Example of Economic Effect Calculation by Reducing Excessive Oxygen
*1: Assume to be constant, though it varies depending on the temperature, CO2 concentrations, etc.
*2: (m-l)*A0 is air volume not used for combustion
This example shows a trial calculation for 0.5% reduction of excessive oxygen in the heating furnace of a petroleum normal pressure distillation apparatus(topper) which process oil of 100,000 barrels per day. The result indicates a fuel saving of about 240 kiloliters, worth $113,000 per year assuming a price of $470 per one kiloliter fuel oil.
Furthermore, by reducing the amount of fuel used, CO2 emissions can be reduced. The carbon emission per one kiloliter of fuel is about three tons, so CO2 emissions are reduced by 720 tons per year.
Safety Control by the TDLS8000
A burner management system (BMS) safely controls the burner of the combustion furnace and includes an interlock mechanism and a safety shut-off mechanism to prevent explosion. The BMS must comply with safety standards based on risk assessment such as the international standard (ISO12100) and the EU, USA and Japanese standards (EU standard: EN746, USQ standard: NFPA86, Japanese standard: JIS B9700).
Because the TDLS8000 monitors the CO concentration in near real-time, it increases the reliability of the safety system by inputting a signal of the detected CO concentration to the BMS and is expected for implementing the defined safety requirements. Figure 6 shows a typical system configuration in which the CO measurement capability is added to the BMS burner shut-off system. Yokogawa’s ProSafe-RS integrated safety instrumented system can be employed as the BMS.
Figure 6 : Safety Control in the Burner Control Equipment
In addition to the measurement of CO the TDLS8000 can accurately measure CH4 (Methane) levels providing an extra level of safety during start up where a flame out or a failed burner ignition can cause an explosion.
Conclusion
The TDLS8000 is attracting considerable attention from many refinery and petrochemical plants because it requires little maintenance and can measure the concentrations of O2/CO/ CH4 in the furnace in near real-time.
The technology for combustion efficiency optimization, by measuring O2 can CO concentrations in this application note was established more than twenty years ago.
The TDLS8000 provides a near real time measurement of O2/CO/CH4 in the radiant section of a large scale combustion furnaces and process heaters allowing process owners an unprecedented opportunity to optimize combustion.
Product Recommendations
TDLS 200 (O2/CO/CH4 analyzer)
Note: Various options are available please consult your local Yokogawa Sales Office for more information.
Notes
- Response time: 2-5 seconds
- Process pressure up to 20 bar
- Interference Free
- Process temperature up to 1500ºC
- TruePeak Measurement
- Optical Measurement- No sensor contact with process
References:
- Tsuneo, Hiraoka, “Reduction of Fuel Costs and CO2 Control for Packaged Boilers,” Yokogawa Technical Report, Vol. 44, No. 2, 2000, pp. 85-86 in Japanese
- American Petroleum Institute, “Instrumentation, Control & Protective Systems for Gas Fired Heaters”, API 556 2nd edition, April, 2011.
Gerelateerde Industrieën
-
Stroom
Halverwege de jaren zeventig betrad Yokogawa de energiesector met de introductie van het EBS Electric Control System. Sindsdien is Yokogawa standvastig doorgegaan met de ontwikkeling van onze technologieën en mogelijkheden om onze klanten wereldwijd de beste diensten en oplossingen te bieden.
Yokogawa heeft het wereldwijde netwerk voor energieoplossingen beheerd om een actievere rol te spelen in de dynamische mondiale energiemarkt. Dit heeft een nauwer teamwerk binnen Yokogawa mogelijk gemaakt, waarbij onze wereldwijde middelen en branchekennis bij elkaar zijn gebracht. De experts uit de energiesector van Yokogawa werken samen om elke klant de oplossing te bieden die het beste aansluit bij zijn geavanceerde eisen.
-
Olie & gas
Yokogawa heeft diepgaande ervaring in elk deel van de olie- en gasindustrie. Van offshore- en onshore-installaties tot pijpleidingen, terminals en diepwateractiviteiten. Wij leveren oplossingen die de veiligheid verhogen, een nauwkeurige en betrouwbare werking garanderen en de efficiëntie van de installatie verhogen.
-
Downstream olie & gas
De downstream olie- en gasindustrie wordt de laatste jaren met een toenemend aantal uitdagingen geconfronteerd. Deze omvatten de veranderende kenmerken van de te verwerken grondstoffen, veroudering van procesinstallaties en apparatuur, stijgende energiekosten, gebrek aan geschoolde fabrieksoperators die een raffinaderij veilig en efficiënt kunnen leiden en de steeds veranderende eisen van zowel de markt als de klant.
In de loop der jaren is Yokogawa een samenwerkingsverband aangegaan met vele downstream bedrijven om industriële oplossingen te bieden die gericht zijn op het oplossen van deze uitdagingen en problemen. Yokogawa's oplossingen hebben plantmanagers geholpen om maximale winstgevendheid en duurzame veiligheid binnen hun fabrieken te realiseren.
-
Thermisch
Thermische energie die steenkool, olie of gas als brandstof gebruikt, is verantwoordelijk voor het grootste deel van de elektriciteitsopwekking over de hele wereld.
-
Petrochemie
De behoeften van petrochemische bedrijven zijn zeer divers. Om voorop te blijven lopen in de huidige, sterk concurrerende markt, streven producenten naar verbetering van kwaliteit en productiviteit. Yokogawa biedt op maat gemaakte oplossingen voor deze behoeften op basis van haar lange en brede ervaring op dit gebied.
-
Refining
In de steeds veranderende markt worden raffinaderijen niet alleen gezien als installaties voor de verwerking van ruwe olie, maar moeten ze ook rendement opleveren. Tegelijkertijd is men zich bewust van de noodzaak van veiligheid in dergelijke installaties. Een totale productieoplossing die planning, beheer en controle omvat, is vereist om de lange termijn doelstellingen inzake rentabiliteit, efficiëntie en milieubescherming te bereiken. Met jarenlange expertise op het gebied van automatisering kan Yokogawa u betaalbare totaaloplossingen bieden voor efficiëntere productie en een schonere wereld.
-
Offshore (FPSO FLNG & FSRU)
Offshore exploratie en productie vereist maximale uptime onder zware omstandigheden. Bemande en onbemande installaties hebben behoefte aan betrouwbare geïntegreerde controle- en veiligheidssystemen (ICSS) met geavanceerde mogelijkheden voor bewaking op afstand. Yokogawa beschikt over ultramoderne technologie en uitgebreide ervaring in de uitvoering van offshore projecten van elke omvang en complexiteit van de automatisering.
-
Upstream olie & gas
De upstream-industrie omvat offshore- en onshore-activiteiten, waaronder automatisering van boorputten, raffinage, voltooiing en scheiding om ondergronds of onder water ruwe olie en aardgas te winnen en te bewerken.
Wanneer aardolie naar de oppervlakte wordt gebracht, moet het worden gescheiden voordat het wordt vervoerd. Primaire en secundaire scheidingsfasen verdelen gewoonlijk de gasstroom, waterstroom en oliestroom in een driefasen scheiding. Voor het vervoer van gas is een pijpleiding nodig en kan een raffinageproces in de upstream fase voorafgaand aan het vervoer plaatsvinden. Vloeistoffen kunnen via tanks of pijpleidingen voor verwerking worden verzonden, waarbij nauwkeurige niveaumetingen vereist zijn.
Gerelateerde producten & oplossingen
-
In-Situ Gas Analyzer TDLS8000
Yokogawa’s new TDLS™8000 houses all of the industry’s leading features in one robust device. The platform design is for in situ measurements which negate the need for sample extraction and conditioning.
-
Tunable Diode Laser Spectrometers
Tunable Diode Laser Spectrometer (TDLS) is a laser-based gas analyzer with fast-update optical analysis.