Yokogawa will be exhibiting at the CHEMUK 2021 conference and exhibition which will be held at the NEC in Birmingham from 15th to 16th September 2021.
CHEMUK is the only dedicated trade show and speaker programme for the UK’s chemical industries. It showcases the latest plant equipment, technology, supply chain materials & services supporting the chemicals industries that drive operational performance, efficiency, safety, sustainability, compliance and more.
Meet Yokogawa's Donal Bourke, who will be a panellist on the ‘The Drive Towards Digitalisation - The Future of Digitalisation in UK Process Industries.’ On stage 4, at 11:00 to 12:00 on Wednesday 15th September.
Biography: Donal Bourke
Donal Bourke is Manager for Yokogawa UK & Ireland's New Business and Digital Enterprise Solutions (DES) business groups. He is a graduate of Griffith College Dublin (BA) and holds an MSc in Information Systems Management from NUI Galway.
As the manager for Yokogawa's DES Group, Donal works with customers in the process manufacturing industries providing professional services and technologies for IIoT, OT Cyber Security and Smart Manufacturing.
Also presenting is Dr Puya Afshar who will present ‘From Data Collection to Actionable Insights: A Best Practice Approach’ on Stage 4, at 14:20 to 14:40 on Wednesday 15th September.
Biography: Dr. Puya Afshar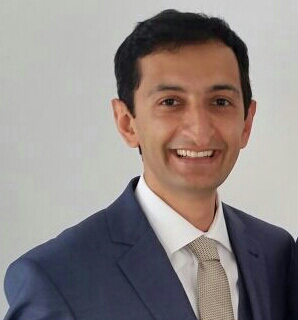
Dr Puya Afshar is a Senior Consultant for Yokogawa UK Limited. He is a graduate of KN Toosi University of Technology (BSc) and Tarbiat Modares University (MSc) in Tehran and received his PhD in Advanced Process Control from the University of Manchester in 2007, focusing on the application of Artificial Intelligence and data-based optimisation in process control. Puya worked for The University of Manchester as an R&D fellow and published more than 30 technical articles in various journals and international conferences. He joined Yokogawa UK in 2011, delivering several major projects in the oil, gas, and chemical sectors. Currently, he works in his capacity as a senior consultant within the Advanced Solutions Consultancy Group and his main areas of focus are Data Historians, Data Analytics, and Alarm Management consultancy services.
Abstract:
With the advancement of computer hardware, software and networking devices, manufacturing and process plants have equipped themselves with state-of-the-art infrastructure enabling them to produce vast amounts of data. This data is collected from various sources including supply chain, production and business systems. Data historians transfer large volumes of real-time-data from production facilities to users on multiple platforms, with negligible latency. However, possession of large volumes of data does not necessarily constitute better economic prosperity, unless two main challenges are addressed:
- Data is often kept in databases disconnected from the business systems, making it difficult to see the big picture of the operations
- Data is often used reactively, therefore not much insight is captured from processes to deliver true business value
By adopting complex computational techniques and powerful analytical modelling such as AI, IT companies have made advances in decision support systems for data analytics. However, the true value of data analytics can be realised through a consultancy approach where data science techniques are interjoined with field knowledge and technology. In this paper, we propose a best practice methodology for data analytics in the process and manufacturing industries. This is designed with knowledge of data integration, machine learning, and industrial production systems, as well as expertise in collaborating with plant management and operation.
Register for your free two-day visitor pass at www.chemicalukexpo.com
Related Industries
-
Chemical
Chemical plants rely on continuous and batch production processes, each posing different requirements for a control system. A continuous process calls for a robust and stable control system that will not fail and cause the shutdown of a production line, whereas the emphasis with a batch process is on having a control system that allows great flexibility in making adjustments to formulas, procedures, and the like. Both kinds of systems need to be managed in available quality history of product, and to be able to execute non-routine operations. With its extensive product portfolio, experienced systems engineers, and global sales and service network, Yokogawa has a solution for every plant process.