Table of Contents
YI-MAC - YOKOGAWA INNOVATIVE MAC
1.1. EARLY SUCCESSES WITH MAC
1.2. YI-MAC VALUE ENGINEERING
1.3. YI-MAC TOOLKIT BENEFITS
1.4. DESIGN OPTIMIZATION AND PLANNING
1.5. COMMITMENT TO DELIVER VALUE
AGILE PROJECT EXECUTION DELIVERY INNOVATIONS IN SYSTEM AND ENGINEERING
2.1. BLOCK BASED ENGG: RE-USABLE APPLICATION LIBRARIES
2.2. NEW INSTRUMENT DATABASE: EASY CHANGE MANAGEMENT
2.3. VIRTUAL COMMISSIONING CAPABILITY → FLAWLESS STARTUP
2.4. FLEXIBLE BINDING AFTER LOOP CHECKS
2.5. NETWORKED PROJECT COLLABORATION
2.6. MODULAR DESIGN: FOCUS ON EARLY VALIDATION
2.7. FIELD DIGITAL: FOCUS ON FULL BENEFIT OF FIELD DIAGNOSTICS DURING STARTUP
NEW YI-MAC VALUE CREATION PROCESS
3.1. PRE-FEED: FOCUS ON END-USER VALUE
3.2. FEED: FOCUS ON VALUE TO EPC
SUMMARY OF TRIPLE VALUE BENEFITS
4.1. VALUE TO END-USER: FOCUS ON INTEGRATING ALL AUTOMATION ASSETS
4.2. VALUE TO EPC: FOCUS ON SHORT DELIVERY AND INCLUDE ALL CHANGES
4.3. VALUE TO PROJECT TEAM: EASE CHANGE MANAGEMENT, VALIDATION AND UPDATING OF FDS
1. yi-MAC - YOKOGAWA Innovative MAC
yi-MAC stands for YOKOGAWA Innovative MAC. It is pronounced as "why" MAC, short for YOKOGAWA.
- Full control of scope and schedule across packages
- Realization of customer expectation
- Single point of responsibility
- Providing fully integrated solutions
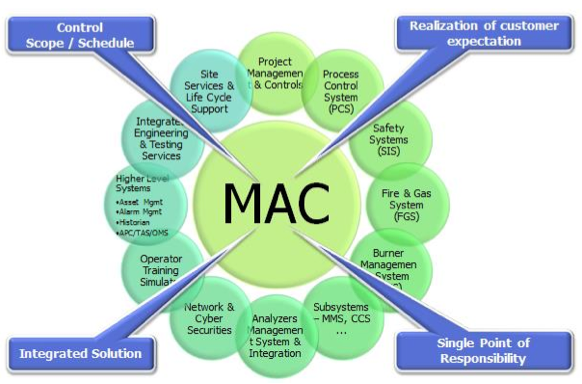
1.1. Early successes with MAC
YOKOGAWA has been delivering MAC project successfully for more than 15 years and has established a Best-Practices based governance system across all its engineering centers. These Best Practices are the result of our wide experience in both Greenfield and Brownfield projects. The resolution which many mature End-Users have adopted is to engage a MAC who assures that the majority of the savings are accrued during implementation phase when good quality FEED/basic engineering results in reduced changes at the later stages. The Business Value covers Risk Mitigation at early phase, CAPEX and OPEX cost reduction and Total Project Life cycle support by the MAC.
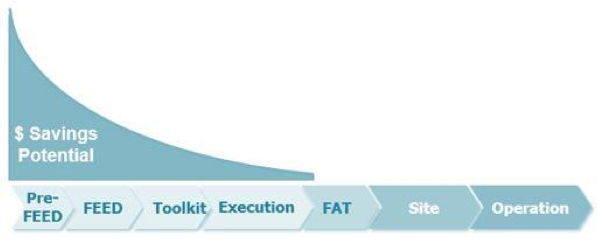
YOKOGAWA Innovative MAC (yi-MAC) services are based on Value Creation workshops and the resulting Value Engineering activities.
- These workshops help identify the functionalities which create most value to the customer, both EPC and End-User.
- The Value engineering process, also called Value Stream, is then defined in which the activities and sequences and MAC, EPC or End-User owners are assigned.
- Based on these agreed activities the most suitable Project execution model is deployed covering Best-Value oriented flexible front/back engineering, Technical core-team structure among other things.
- Following this the Engineering data exchange is prepared using the new CENTUM VP R6 Engineering environment Automation Design Suite and integrated 3rd party tooling.
- The project execution Best-Cost model is then based on this Value stream and results in reduction of all unnecessary waste.
During process simplification, we focus on savings opportunities by challenging business premises and exploring alternate process design options. Next is Value Engineering where we focus on looking for savings opportunities through alternate options in hardware, piping, materials, plot plan, and sequence of work. One of the MAC benefit is to firm-up the Automation vision for the project by identifying value opportunities in line with the overall project objectives through early involvement.
Value creation is one of the added value activities by the yi-MAC team.
1.3. yi-MAC Toolkit benefits
The MAC team of specialists makes full use of the MAC Toolkit, which is a pre-defined set of procedures and templates for each key aspect of the project execution, integration and delivery. Virtualization technologies are utilized and planned to reduce travel of the customer's specialists.
The best value of MAC lies in studying the End-User Lifecycle requirements and how to best plan and design the integration of all functions and systems.
The MAC best practices of YOKOGAWA have continuously evolved and now include always a technical core team who coordinates the requirements of all EPC's with consistency, supported by Global Subject Matter Experts (GSME).
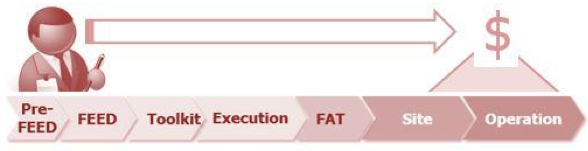
1.4. Design optimization and planning
Single Point of Responsibility: Assigning "Single point of responsibility" to the Automation Experts shifts the System Integration risks to the party with the most experience: the MAC.
Flawless Start-up & Commissioning: Through the use of MAC toolkits, re-usable modules, LCDS, etc. , the MAC ensures full integration & testing of all functions and subsystem interfaces included in the MAC scope will lead to smooth site commissioning and effectively reduce the adverse impact and risk of non- compatibility on commissioning schedule.
Reduced Procurement Costs: Integrated solutions will substantially reduce the direct costs associated with procurement and expediting of various Automation Subsystems.
Standardized Interface Solutions: Standardized interface solutions for many subsystems under MAC scope will ease the maintenance headaches during operation as well as help reduce the life-cycle costs.
The flawless start-up is a concept not to bring critical risks into the site work, including plant start-up, thus not to spend unnecessary time for start-up, and to ensure the 'Ready-For- Start-Up' milestone (RFSU)
1.5. Commitment to deliver Value
Increase understanding by the project teams: The deep understanding of the functional requirements before deciding how to implement them is critical to the project deliverables. Flawless start-up and Life Cycle optimization/extension are the key values to be considered when defining design philosophies.
Improve economics of the project: This is achieved by adding value and reducing waste in each step and activity. In the early phase of the project, a workshop is organized (the value creation workshop) to jointly review each activity from below benefits viewpoint.
Confirm the value of LEAN in each activity of the project: LEAN stands for removal of waste as it has no value to the project.
YOKOGAWA achieves this through Agile Project Execution (APEX):
- Substitution with Lower Cost Alternatives
- Improved Reliability of Project Services
- Standardization of design / implementation / testing
- Best practice with efficiency
- Optimize project resources, Effective tool utilization and Cycle time reductions
- Innovative execution methodologies
- Deployment of new technologies
- Life cycle support
- Enhancement of production safety and efficiency
- Quantify created value throughout the project lifecycle as realized through the Value Creation plan
2. Agile Project Execution Delivery Innovations in System and Engineering
2.1. Block based Engg: re-usable application libraries
Since several years YOKOGAWA set-up Global Industry Centers of Excellence (CoE) to drive value delivery in projects. These CoE's are driving standardization of re-usable libraries of modular controls based on decades of Best Practice in Japan and later Globally, in line with YOKOGAWA's vision of Modular Procedural Automation (MPA).
The real value is delivered when coupling the modular controls with advanced Operation graphics, validated and tested using the Lifecycle Dynamic Simulator (LCDS). By utilizing the LCDS for design validation, engineering hours during the execution phase will increase, but design mistakes will be reduced before site work starts, and thus it is expected to reduce unnecessary time spent at site and to ensure the 'Ready-For-Start- Up' (RFSU) date.
This will result in high levels of information embedded in the operator interface, enabling faster testing and flawless startup. In a typical project of 12 months' time, savings can be achieved of up to 3 months. This becomes possible if EPC contractors and End-users co- work with YOKOGAWA to prepare fit-for-purpose standard libraries ahead of the project.
This is achieved by applying Total Automation Management techniques: combining technologies, embedding retiring operator experience, optimized schedule management as a MAC and superior change management of the new CENTUM VP R6 Automation Design Suite.
All information of the Application libraries is stored in the new Automation Design Suite Master Database (ADMDB). It is not only populated with IO as was the case in previous generations of systems, but is now also storing live updated Functional Design Documents. These include the generic snapshots of the control drawings, the alarm management details, the tuning parameters, the narratives and all other important information.
The IMDB represents the AS- BUILT system when it arrives on site, and remains up to date during the modification made during SAT and start-up. It is therefore a new foundation for flawless start-up and enhanced lifecycle management.
2.2.New Instrument Database: easy change management
The YOKOGAWA Global Engineering Standard has captured the project delivery process in clearly defined phases: FEED, Basic Design, Detailed Design etc.
In the Innovative MAC work process, we select modular controls (Block building) during the FEED. Each module is configured with using generic names together with design documents and the new Instr. Master database is populated with this which reduces the dependency on accuracy of EPC IO list in the early phases of the project.
As more design data becomes available during the execution of the project, the dynamic Simulator models can be improved and tested again to assure dynamic response of combined process units as expected. The controls can already be tuned speeding up the start-up later on.
Management of Change tooling in the new Engineering Platform provides a superior analytical capability to identify dependencies for each loop between controls, start-up sequences, interlocks and advanced user interface.
All project deliverables become "engineering data" Today only Control applications are considered as engineering data. Many project deliverables like documentation, change management, validation, etc. are treated as administrative work. With CENTUM VP R6 these deliverables become also engineering data, supporting the project team instead bind valuable resources or delaying schedule.
Engineers love changes? Changes are not understood as disorder anymore. Customers as well as engineers accept changes as normal way of today's engineering. Change request are smoothly brought into CENTUM VP R6 without interrupting the ongoing implementation process.
Before a change is implemented YOKOGAWA will provide the impact analysis report to the customer. This report clearly explains the system status before and after the change including e.g. CPU loading, network loading etc, providing a true system health assessment.
This capability to capture every change during the total project lifecycle and also plant lifecycle is now also an integral part of CENTUM VP R6 total automation management.
2.3. Virtual commissioning capability → Flawless startup
Our Innovative MAC work process takes this one step further by selecting modular controls (Block building) during the FEED and utilizing the Lifecycle Dynamic Simulator (LCDS) to demonstrate the functionality and dynamic behavior in this early phase.
Each modular designed control philosophy is based on YOKOGAWA's wide experience in each Industry and we have tied up with Process Licensors to develop the simulator models for testing during the lifecycle, starting now during FEED.
'Virtual commissioning capability' as referred to by ARC Advisory Group addresses the need for configurations to be developed and tested with complete hardware independence.
Configurations can be developed and tested using virtual machines, while the target system hardware is being installed and wired at the job site. This can significantly compress project schedules by shortening the critical path, saving huge amounts of capital.
In comparison to conventional MAC execution, the Dynamic Simulator does not reduce delivery man hours. Most probably man-hours will increase as the project team will modify or develop process models and test control logic with models on the iteration basis, but its real value is mitigating risks at site by reducing last-minute surprises related to tuning of control systems and process equipment.
2.4. Flexible binding after loop checks
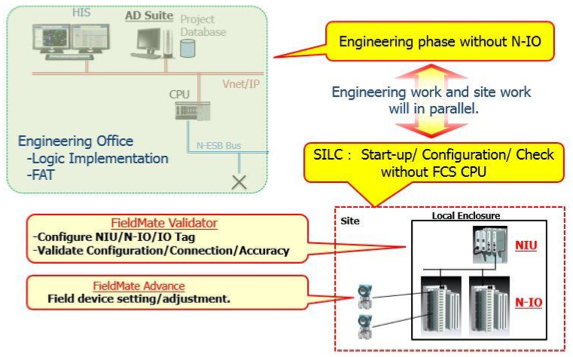
The key benefit of the N-IO will be complete decoupling of application and hardware engineering. The IO racks will be shipped after Hardware FAT and will arrive much earlier on site.
After arrival field wiring can completed well in advance and loop checks can start using the new loop check tool running on FieldMate. The IO list (including device parameters) will be downloaded from the new Instr. Master Database before loop-check starts. After the loop-check is completed, the IO database on the FieldMate Validator will be synchronized with the ADMDB. The synchronization is done using state-of-the-art confirmation-dialogue based verification.
It can be expected that with the N-IO in a typical project of 15 months, the system cabinets can be shipped up to 6 months earlier to site to start wiring.
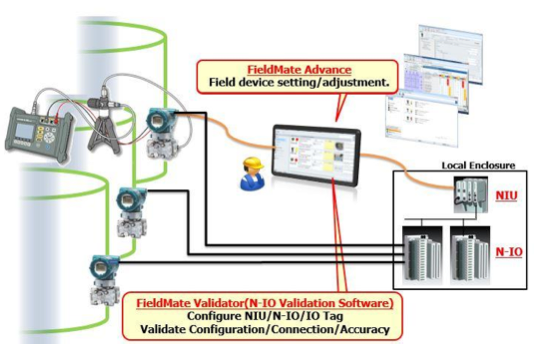
2.5. Networked Project Collaboration
This innovative infrastructure and tooling environment combines remote engineering and virtualization technologies. By working around-the-globe follow-the-sun), it delivers the value of remote engineering, virtual testing, minimized travel, remote acceptance testing etc, and it really accelerates Remote Engineering Work in global projects execution.
Over the last decades, YOKOGAWA has set-up remote engineering centers in various parts of the world. Traditionally work-packs were off-loaded to these centers and the completed and tested system database was delivered in advance of witnessed test with customers.
As the capability of the remote engineering centers has grown and some of the Centers of Excellence are now located there, YOKOGAWA has already started to execute total projects in India, Romania and China.
Additionally tremendous time savings have been achieved in areas of application engineering using training programs set-up by the Global Subject matter Experts, using retired Industry specialists.
This is resulting in high value add delivery in those locations, and many customers now insist to also build the panels and do the witnessed testing in the same location. Thus enormous savings are achieved in the projects both in engineering man-hours, customer travel and project lead time.
This is made possible by the total adoption of virtualization technologies during testing by the Lead engineers and customers while sitting in their home offices. The "cloud" engineering is redefined by YOKOGAWA as executing engineering independent of the location of the master database and actual system hardware. The current levels of availability we have currently achieved are due to reliably designed infrastructure and testing over the last many years in mega size projects.
Utilizing Microsoft virtualization technologies, YOKOGAWA has innovated and adapted the scheme by moving the ADMDB to the most reliable location to safeguard the IP right concerns of our major customer. This can be close to the customer, in the back-office or in the cloud.
With CENTUM VP R6 and remotely connected engineering teams can easily be extended or reduced without reducing quality or effectiveness because there is no need for data exchange procedures as the whole team works on the master database.
Due to levels of flexibility of handling in the IMDB, YOKOGAWA achieves the more important goal of enabling utilization of scarce Global and Local Subject Matter Experts in all its projects. This enables not only the utilization of their expertise, but also the ability to learn and share best practices across projects, accounts and regions.

2.6. Modular Design: focus on early validation
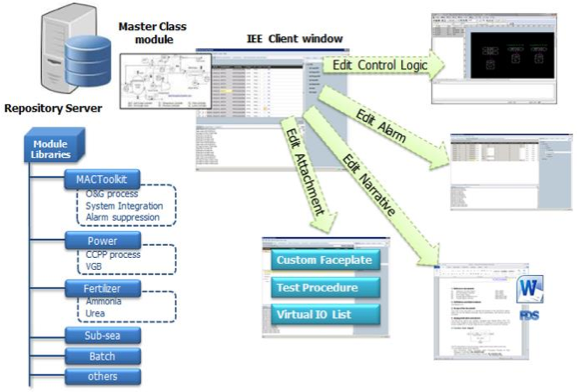
S88, short for ANSI/ISA-88, is a standard for batch (modular) process control. It is a design philosophy describing equipment and procedures.
The starting point of a typical project is the development of a modular structure that allows for validation and change management after instantiation. In order to implement a modular control philosophy one has to subdivide it into control modules, equipment modules and unit modules. The three types of modules are defined as follows:
- Unit module (UM): A unit is made up of equipment modules and control modules. The modules that make up the unit may be configured as part of the unit or may be acquired temporarily to carry out specific tasks such as putting a complete unit into maintenance mode. An example of a unit is a process unit like a tank, a compressor or a jetty.
- Equipment module (EM): The equipment module may be made up of control modules and subordinate equipment modules. An equipment module may be part of a unit or a stand-alone equipment grouping. An example of an equipment module is a pump, a blower or a mixer.
- Control module (CM): A control module is typically a collection of sensors, actuators, other control modules, and associated processing equipment that, from the point of view of control, is operated as a single entity. It includes the alarms, interlocks and tuning parameters.
With this structured approach to segregating the controls of a process, it becomes possible to design the model of the simulator according to the same structure. This will enable re-use across sites tremendously hence increasing the business value of Modular Procedural Automation. By using a global and centrally managed repository server, design consistency can be achieved across projects.
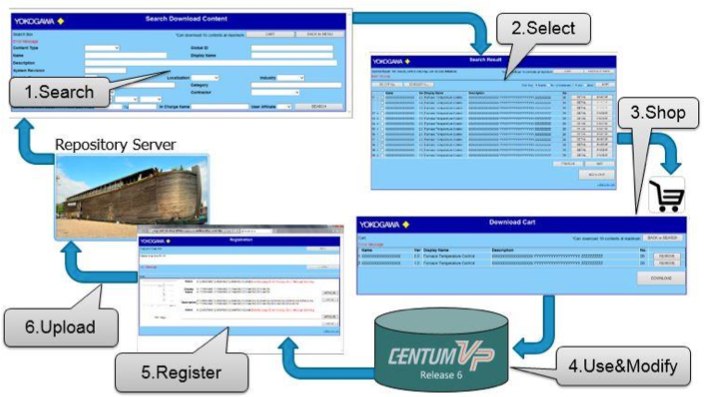
The simulation models can then be tuned for checking the control logics for example: a compressor and the loading and control of several compressors can be dynamically simulated during the FEED and Basic Design.
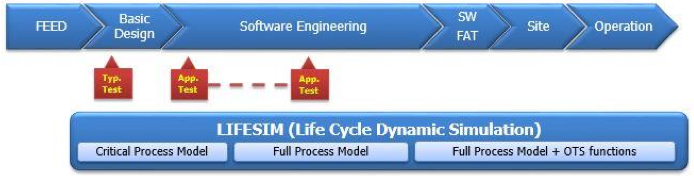
This will test the control philosophy adopted at a very early stage and minimizes risks of making change in the control strategies later on, preventing costly and time consuming changes and re-testing on site on the target compressors.
2.7. Field Digital: Focus on full benefit of Field diagnostics during startup
The technological innovation in the field is advancing at such a tremendous pace that only the combined supply of Field instruments and system from the same supplier can assure optimized use of this functionality.
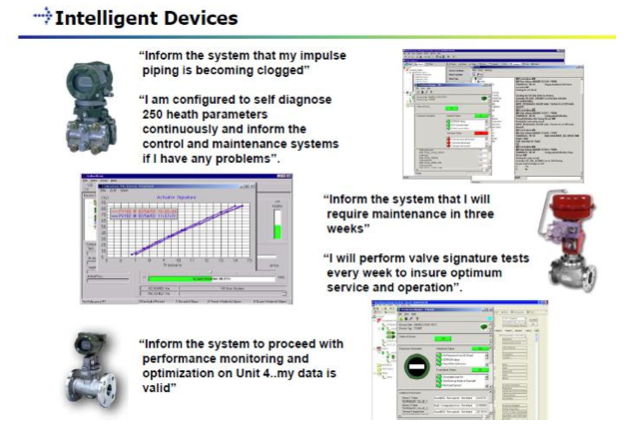
Every YOKOGAWA EJX transmitter is designed to provide the differential pressure, the static pressure and the ambient temperature. Since every EPC is still selecting and designing the P&ID's with single parameter Field Instruments, the opportunity to reduce the number of transmitters is greatly under-utilized. This is the reason why many End- Users insist that YOKOGAWA provides both systems and transmitters, and provides the engineering services to optimally utilize them everywhere.
The result is that YOKOGAWA provides profiles for each transmitter, included in the modular design of the controls, where alarms are automatically propagated to the DCS, maintenance alerts are assigned to the PRM and repeated maintenance alerts propagated to the DCS at the right time. YOKOGAWA as a MAC assures optimal usage of the built-in capabilities of each digital piece of Instrumentation.
The real benefits only present themselves during plant disturbances. It's the End-User who will get all the value.
3. New yi-MAC Value Creation process
As is well known, the traditional MAC value is a result of identification and mitigation of design and integration risks early in the project so that implementation is smooth without surprises. Correcting design mistakes later on in the project takes considerable more effort than during the pre-FEED and FEED.
3.1. Pre-FEED: focus on End-User value
Modularization and Standardization: This is enabled by maximum use of MAC Toolkit. The deliverable in the project is re-use of tested and tried solutions resulting in efficient use of system resources (CPU load etc), Flawless Start-up, Ease of Maintenance, Sustainability in operations by rotating operators across sites as they are all experienced in YOKOGAWA standard modular solutions.
Effective engineering tools utilization: (ePlan, SPI etc) Deliverables in the project are utilizing the IMDB containing all live asset information. This Minimizes manual update assuring the database is the image of the live plant. The integration of other tools like ePlan, SPI etc with the IMDB provides for an effective project delivery platform.
Common set of Advanced control and Optimization strategies: A standard library for each process licensor resulting in learning across plants and sharing of operators.
Modular Procedural Automation (MPA): Implementation of MPA (ISA106) has the goal to harness the experience of retiring operators. This increases speed of correct action of junior operators for safer, more consistent and effective operations.
YOKOGAWA Standard Cabinets & Consoles: This brings the benefit of Zero engineering and Centralized manufacturing in locations where the engineering is done off-shore. This assures that the End-User requirements are applied during EPC phase resulting in ease of maintenance and common look and feel.
Bundled Field Instruments: By combining the Field instruments and analyzers with asset management for equipment / smart instruments optimized design is achieved utilizing diagnostics functionality resulting in maximized ROI of field instrumentation and analyzers through best in class diagnostics.
Specific Process experience by the MAC: By engaging the expertise of GSME and Local SME's (LSME) of various domains, we provide the opportunity for the MAC to validate the EPC input documents assuring that the dynamic validation results in shorter commissioning
Strong capability of handling multiple EPC's: This capability drives pro-active review of Design inputs. YOKOGAWA as an innovative MAC acts as a true End-User representative which results in faster execution before FAT and Flawless Start-up due to less modifications on site.
Seamless integration with the MAC technical core team: This core-team is active during all project phases. This has the tremendous business benefit that all EPC adhere to common design philosophies which follow the early adoption philosophy of the latest technologies. This in turn Ease of maintenance and improved Total Cost of Ownership (for which YOKOGAWA is well known) and reduction through reduced variances.
Align MAC and EPC deliverables and responsibilities: The true value of delivery comes from removing redundancies between MAC and EPC's. The result of this is a common deliverable list to the End-User which in turn reduces the combined cost and risk of EPC and MAC delivery services to the End-User.
Apply software replication work processes: For projects with multiple LNG trains, modular engineering delivers superior results by using the new Engg Platform functionality of Module libraries. This assures ease of maintenance and the dynamic validation results in flawless and drastically shorter commissioning.
Integration of teams under Plant Automation Common Team (PACT): This concept is developed together with a major customer in recent MAC projects. Beside the MAC, each EPC is represented in the PACT to resolve design conflicts quickly and mitigate implementation risks. This common team has the objective to drive flawless startup and design optimization. YOKOGAWA has many satisfied customers where we delivered Flawless start-up and a reduced Total Cost of Ownership during optimized life-cycle.
3.2. FEED: focus on value to EPC
The new yi-MAC philosophy is based on providing value to EPC as well. The following points will illustrate this in detail by identifying tangible benefits.
Alarm design / rationalization: This results in alarm suppression as per design during the project to speed-up correct decision making during commissioning. This reduce recovery period after process upset and earlier commissioning completion and sign-off.
"Cloud" Engg deployment in the project: This results in effective integration between Front and Back offices resulting in Live information sharing, Remote testing and validation without the need to travel.
Fit for purpose training simulators / Life Cycle Dynamic Simulation: Validate design throughout the project lifecycle. Reduce errors and revisions in the later staged of the project, reduces the overall project duration (including start-up and commissioning) and improves dynamic response of the process units during commissioning. The implementation phase may require more manhours as we will apply an iteration method. The key objective of LCDS based project execution is spending more money in early phase of project execution to assure that critical risks are not brought into site work, including plant start-up. As the MAC responsibilities end with DCS handover, these benefits are all value to the EPC.
Decoupling hardware and application design/engineering: This is accomplished by effective engineering tools utilization, accepting late IO changes in the project and through that preventing and minimizing multiple cycles of changes and associated validation risks.
Yokogawa Standard Cabinet and Console design: Zero engineering, centralized manufacturing. Minimize design activities resulting in reduced lead times and reduce cost.
Specific Process experience: This can engaged in validation of EPC input documents. Utilizing the Dynamic validation will result in shorter commissioning.
Joint 'Design to Cost" and "Cost Predictability": The MAC risk register and design practices are based on valuable past project experiences which reduces the risk of cost overruns.
Minimize changes: Elimination of impact of late changes by utilizing the N-IO. This is done by clarity on which information is required during the 3 phases: Typical testing, Instantiation, and flexible binding on site.
Centralized procurement for 3rd Party buyout items: Clear work processes and vendor assessment resulting in reduced lead-times and less quality problems during commissioning.
4. Summary of Triple Value Benefits
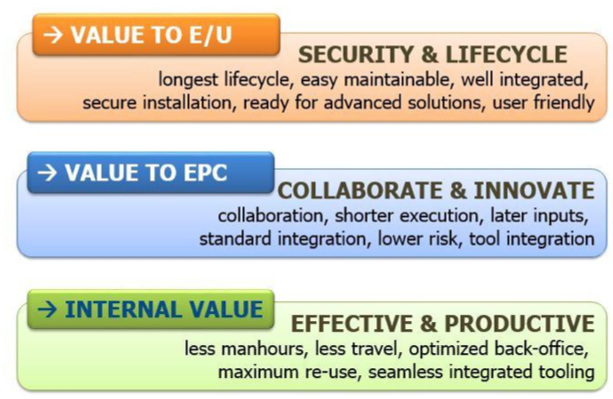
4.1. Value to End-User: focus on integrating all automation assets
Each End-User wants to receive a system on site that is secure and up to date following the latest technological trends and standards. This is a real challenge as the design decisions are usually made years in advance.
A truly innovative MAC, who acts as a representative of the End-User, will always keep this in mind, yet this MAC will know how to be innovative in their approach to direct the EPC's to comply and promote this principle of design. By joining the EPC's, the MAC can contribute in the risk assessments and budgeting to achieve the common value targets and KPI's.
The End-User is keen to start the plant Lifecycle with a partner who understands the challenges of operating the plant, and who has studied these requirements during the projects execution as their partner. A true MAC prepares the system with all required tools to report operation, maintenance and business measurements.
During the first years after start-up, the advanced process control services will improve the production beyond the design considerations of the End-User alone. Only a MAC who thinks from the perspective of total plant lifecycle and total cost of ownership will be able to deliver an integrated solution which can deliver on such a promise.
4.2. Value to EPC: focus on short delivery and include all changes
When designing a new Engineering environment, the EPC's always provided feedback that providing an easier way to engineer was really not a benefit to them. This was regarded as something YOKOGAWA was supposed to provide.
The EPC's were really interested when they were presented with a CENTUM VP R6 system which would provide them shorter delivery time and decoupled application engineering from hardware engineering.
The most interesting feature of the Engg Platform was the ease to manage changes during the project. The fact that YOKOGAWA would change its way of dealing with changes in their contracts was very well accepted as the prime reason to select a system integrator was no longer their knowledge of their own system, but the knowledge of the process, the ease to integrate 3rd party systems and the ability to import engineering data into a central database.
Each EPC will always rely on SPI to populate their P&ID's, but the fact that YOKOGAWA is able to manage all data related to the automation assets delivered in the EPC scope is a key value driver for the EPC's.
4.3. Value to project team: Ease change management, validation and updating of FDS
YOKOGAWA as a quality provider of products and services believes that if it is easy for an engineer to implement, then the final user will be satisfied.
The new generation CENTUM VP is equipped with a new suite of engineering tools which makes it easy to import and export instrument data to any 3rd party engineering tool available.
Having a system which automatically updates the AS-BUILT drawings and Functional Design Specification will provide enormous business value to the End-Users.
Every system these days will accept changes late in the project. It's the readiness of the engineers and suitability of the tools which make it really efficient and easy to use. YOKOGAWA has now made this innovative leap in the new generation of CENTUM VP.
List of Acronyms
yi-MAC |
Yokogawa innovative MAC |
---|---|
MAC |
Main Automation Contractor |
LCDS |
Life Cycle Dynamic Simulator |
ADMDB |
Automation DesignSuite Master Database |
SPI® |
SmartPlant® Instrumentation (Intergraph®) |
ePlan® |
(Rittal) |
PACT |
Plant Automation Common Team |
FEED |
Front End Engg design |
S88 |
short for ANSI/ISA-88 |
VMware® |
Virtualization Software (VMware®) |
MPA |
Modular Procedural Automation |
CoE |
Center of Excellence |
GSME |
Global Subject Matter Expert |
LSME |
Local Subject Matter Expert |
FieldMate® |
Versatile Device Management Wizard (YOKOGAWA) |
Field Digital |
Integration of Digital capabilities in ICSS (YOKOGAWA) |
CM |
Control Module |
EM |
Equipment Module |
UM |
Unit Module |
MAC Toolkit |
Standard set of Functional design Specifications |
ARC |
ARC Advisory Group (www.arcweb.com/) |
Trademarks
All brand or product names of Yokogawa Electric Corporation in this bulletin are trademarks or registered trademarks of Yokogawa Electric Corporation. Any company's names and product names mentioned in this document are trade names, trademarks or registered trademarks of their respective holders.
Zugehörige Produkte & Lösungen
-
Agile Project Execution
Agile Project Execution bietet neue technische Möglichkeiten und ändert die Art und Weise, in der Projekte ausgeführt und geplant werden können. Dies dient dazu, Risiken zu reduzieren und den Projektplan flexibler zu gestalten.
-
Cybersecurity Consulting Services
Die umfassenden Cybersecurity Consulting Services von Yokogawa unterstützen Kunden bei der Umsetzung geeigneter Security-Lösungen für ihre Anlagen, um einen resilienten Betrieb zu gewährleisten und sich gleichzeitig an neue Technologien anpassen zu können. So erreichen unsere Kunden höhere Effizienz und Produktivität.
-
Innovative MAC-Services
Gerne agiert Yokogawa für Sie als MAC (Main Automation Contractor) und bietet so den vollen Umfang an Projektausführungsfunktionen aus einer Hand. Yokogawa übernimmt die Verantwortung für alle Aspekte im Zusammenhang mit der Automatisierung des Projekts und hilft Ihnen dabei, Anforderungen an das Budget, die Zeitplanung, das einzusetzende Personal, die Bereitstellung und das Risikomanagement zu erfüllen.
-
Security-Programm
Die Cybersecurity-Services von Yokogawa verfolgen einen auf dem Lebenszyklus der Anlage aufbauenden Ansatz, um unseren Kunden dabei zu helfen, ihre Security-Risiken zu kontrollieren und anzugehen, um einen bestmöglichen Plan zur Erhaltung der Betriebskontinuität über den gesamten Lebenszyklus der Anlage zu erreichen.