Achieving a step-change in business performance
In a world of accelerating change driven by market demand, the energy transition and sustainable development, successful digital transformation (DX) depends on a data-driven, customer centric approach that leverages the latest technologies. With our consultants, manufacturers break down DX into achievable step-changes in business performance according to an enterprise aligned vision on automation and integration.
Digital Transformation that succeeds
Our approach focuses on your unique situation, by advising on your complex transformation issues and orchestrating digital services for you to successfully adopt and sustain the latest technology.
Discover where you are
Aligning the vision, the as-is and preparing the resources for the acceleration of digital transformation.
Design where you want to be
Integrating process, digital technology and people solution in collaboration with internal and external stakeholders.
Develop how to get there
Implementing and managing the new changes throughout the organization, and providing support for the workforce to adopt the change.
Details
Facing disruptions and opportunities
Digital leaders guiding their organization through the disruptions and opportunities of digital transformation, know that the trajectory of change and interdependencies of operations, technology, and talent are complex. Yokogawa brings the required digital capabilities to the essential next step in enterprise optimization initiative.
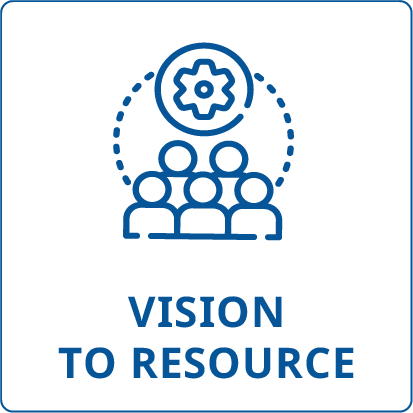
Vision to resource: Ensuring that technology maximizes its value by aligning your business to the sustainable, profitable enterprise of your vision
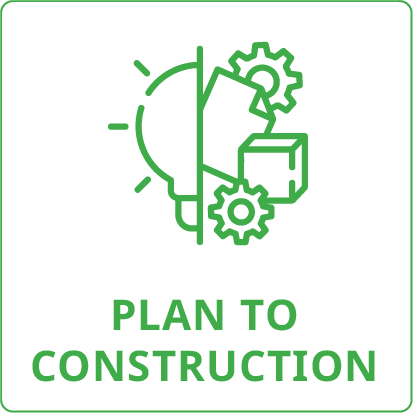
Plan to construction: Formulating and changing all aspects of the digital transformation including people, processes, and technology, in order that holistic value is delivered effectively.
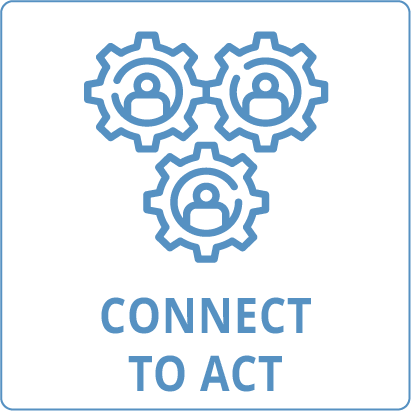
Connect to act: Connecting inputs to the best outcomes by integrating the data sources, including the IT and OT and bringing the technology together to realize the value.
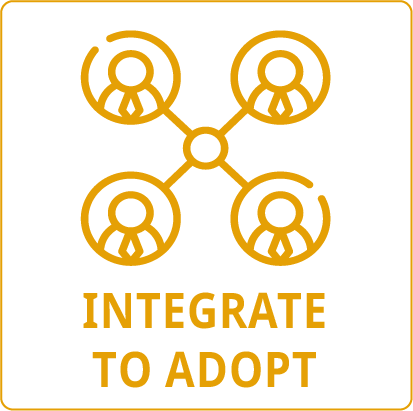
Integrate to adopt: Transforming the enterprise, the way it works, and how people interact with it in order to sustain value with implementation that is embraced throughout the asset.
Who We Are
Our aim is to unify and give your organization the strength and ambition to drive transformation. We blend together the global technical and functional consulting skills that has made Yokogawa deliver our customers millions of hours of uninterrupted operation.
Automation is within our DNA and our commitment to deliver, manage industrial risk and improve your business comes from years of co-innovating the latest technology together.
DX Consulting combines digital services to sustainably implement the latest digital technology in an industrial environment.
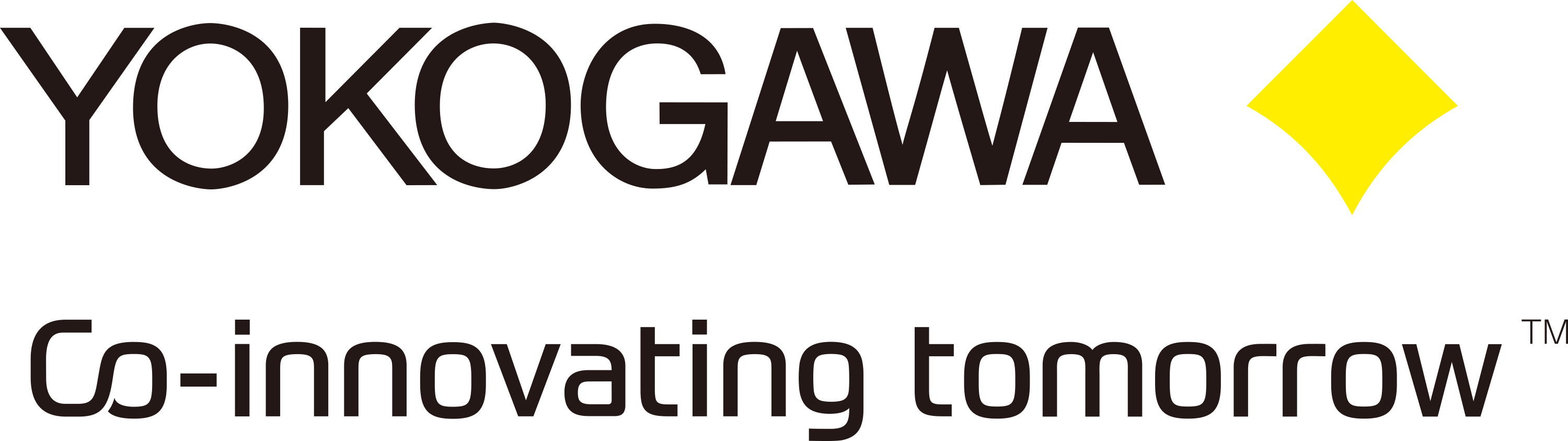
- Evidence of current digital capabilities, required solution architectures and achievable digital maturities
- Perspective on business use case vision alignment, enterprise benefit cases, and digital priorities
- Guidance for holistic transformation through processes, people and digital technology
- Specialist expertise to design, implement and integrate solutions
- Support for critical resource to accelerate returns
- Facilitation of organizational and process changes to sustain the benefits
DX Services
Every company is unique in how it operationalizes its’ business strategy. So too will be the desired approach to digital transformation, smart manufacturing, and industrial autonomy. Yokogawa brings deep and broad experience in operations, process, and technology consulting and services:
Strategy and Planning
A starting point to layout a DX roadmap that thoughtfully considers people, processes, technology, assets, and data.
Secure Implementation
Deploy security solutions for industrial assets to ensure safe operation while adapting to new technology for achieving higher efficiency and productivity.
Operating Model Enablement
Organization change management and human performance improvement utilizing KBC’s best practices and operational discipline.
Use Cases
Data and tacit knowledge integration
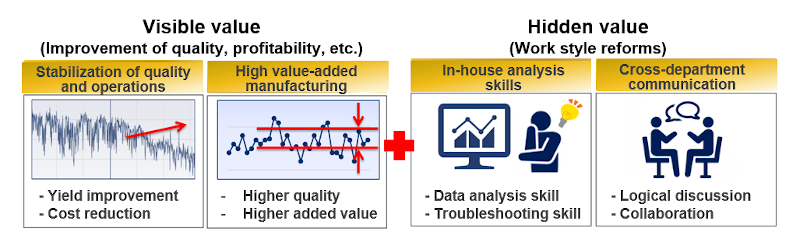
- Client: An engineering company that designs and builds plants.
- Goal: Improve operations to meet ever stricter quality management requirements.
- Challenges: Aging production facilities and the loss of operational know-how through the retirement - have a major impact on product quality and efficiency.
- Solution: Big data analysis / IoT solutions to analyze various data, incorporating raw data from the variety of sources. Knowledge about the production process from operator know-how, alongside the use of advanced analytical techniques, identified root causes and brought together all functional domains to consider and implement practical solutions
- Outcome: We helped the client identify root causes and brought together all functional domains to consider and implement practical solutions. converting tacit knowledge into explicit knowledge, improvement of cross-department communication and upskilling the client’s problem-solving.
External data stabilizes production
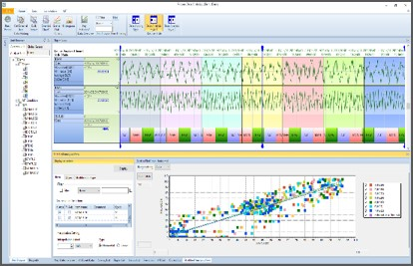
- Client: A continuous process operator
- Goal: Higher product quality and production efficiency,
- Challenge: Operators were required to make adjustments whenever there were fluctuations in the process. For certain reasons, not fully understood, these fluctuations tended to occur more frequently at night.
- Solution: Analyzing the big process data for thousands of tags alongside a good understanding of operator behaviour. During steady state and non-steady states.
- Inclusion of data from all sources was assessed to avoid any preconceptions and it was found that that a 1% difference in feed flowrate was caused by day and night variations in ambient temperature and atmospheric pressure, and that this was causing major fluctuations throughout the production process
- Process data analysis is meaningless if you stop at just identifying the root causes of a problem. To suppress the fluctuations that were occurring at the plant, the staff of the Plant, who are professionals in manufacturing, and Yokogawa and the plant staff considering practical countermeasures, devising a control scheme for stabilizing the process.
- Outcome: Converting tacit knowledge into explicit knowledge, improved cross-department communication as well as upskilling the client’s problem-solving capabilities.
Improving maintenance efficiency and field operations
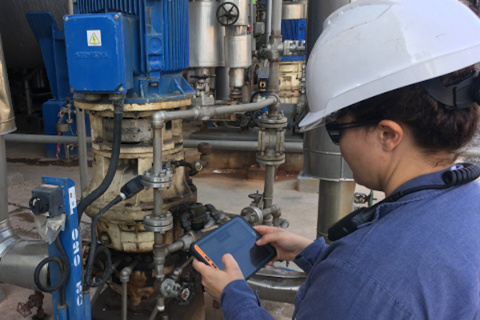
- Client: A polymer plant owner
- Goal: Improving on-site operational efficiency and equipment availability through capturing valuable information contained with the paper-based maintenance reports.
- Challenges: Excessive amount of paper-based inspection and patrol reports made it very difficult for supervisors to keep track of inspection progress and identify problems to be addressed. Result: inspection omission and over-maintenance.
- Solution: Improve access to this information by digitizing with the deployment of a tablet-based solution for field maintenance, enabling personnel in the field to access digitized information such as task lists and related documents. Following the successful completion of the "Field Assistant" PoC, the team gathered information and facilitated discussions on what would be required for a practical implementation of this solution. Yokogawa interviewed field operators, supervisors, and the plant manager, and took current and historical maintenance data into a detailed workflow that was used, via tablet screen by field operators and supervisors.
- Outcome: Maintenance costs are down 10 ~ 15%. Uptime is improved with early detection of abnormalities and the O&M data feeds analysis and visualization of conditions into the decision support tools to maximize manufacturing performance.
Change integration and adoption

- Client: A joint venture Asia Pacific oil and gas exploration operator
- Goal: Increase efficiency and consolidation of all remote operating control rooms into one central location.
- Challenge: Adhere to their safety and environmental core beliefs while expanding from a few hundred wells to about 3,000 operating wells.
- Solution: Consultants worked with the operator to develop a line-of-sight plan, focused on asset development and management of production supply chain, integrity/facility, and reservoir. One of the objectives was to develop a clear vision for business success and risk tolerance aligned the functional groups within the organization. The organization agreed on one common approach and standardize their processes across the board.
- Outcome: With all change management components on target the operator increased their efficiency while upholding their company’s safety values.
Publikationen
Downloads
Videos
Digital transformation is the novel use of digital technology to accelerate your company's business strategy.
Möchten Sie weitere Informationen über unsere Mitarbeiter, Technologien und Lösungen?
Kontakt