Since the ’80s, process industries have embraced digital technology to better understand and manage resources, improve safety, and increase efficiencies. In fact, the field of Industrial Automation (IA) has given rise to this third industrial revolution for nearly half a century.
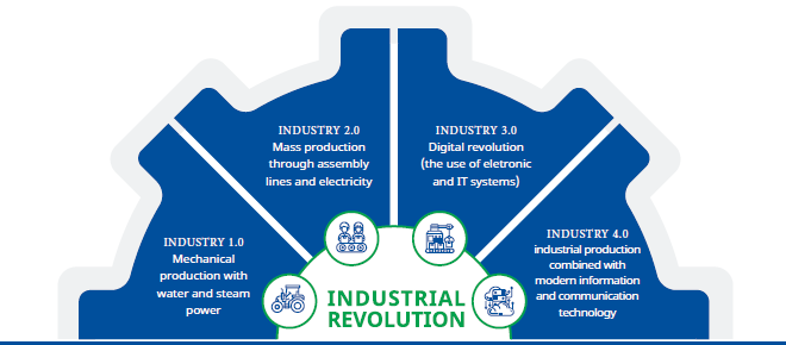
But since then, IT megatrends have driven massive growth in computing power, storage, bandwidth, and information. In this environment, the network effect—a phenomenon whereby a product, service, or platform gains additional value as more people use it—has enabled the open sharing of ideas and development tools and an agile approach to exponentially accelerate the effects of software development, algorithms, and new business models.
As a consequence, concepts such as “digitization,” “digitalization” and “digital transformation” (DX) are becoming increasingly common in boardroom conversations, but their exact meaning sometimes gets lost as leaders work to find the best solutions to their business problems.
The following article will clarify the differences between digitization, digitalization, and digital transformation.
What is digitization?
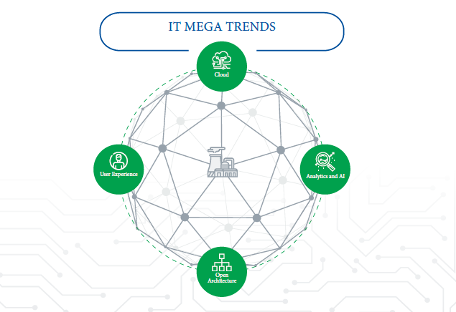
Simply put, digitization means digitizing information. Information visually recognized or recorded on paper is coded with 0 and 1 and electronically recorded as digital information so that computers can process it easily. Digitization facilitates data processing. It’s about the importance of “sensing”, or collecting data. Yokogawa broadly defines digitization as the fundamental process of making analog information available in a digital format. Some examples:
- Creating digital work orders to replace paper-based work or scanning a letter are simple examples of digitization since it creates a digital copy of that letter.
- Converting manual readings to electronic ones is a more common example in manufacturing.
- Delivering asset data integrity through digitization in plant operation and equipment maintenance, for example by automating the data acquisition process that had been performed manually.
Optimally, a small fraction of data is valuable, and the combined data is coming from different sources, sizes, varieties, and velocities. Before digitized data is ready for decision making or supply to a digital technology solution, a process needs to be in place to ensure its quality. It requires data sufficiency, data trustworthiness, data propagation, and data governance.
Data and its corresponding infrastructure must be ready for consumption by plant personnel and software applications for successful digital technology implementations. Having data with a high degree of integrity is important but, on its own, not sufficient as the data also needs to be accessible to multiple users and systems for better and more timely decision making. Critical communications and storage infrastructure needs to be in place, designed with adequate capacity, and secured.
Sensing technology
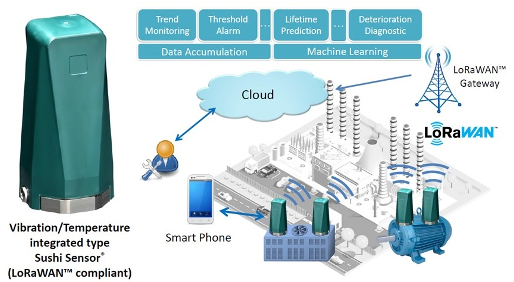
The Industrial Internet of Things (IIoT) and Industry 4.0 are driving the growth of wireless sensors being deployed to digitize field data. Data originates from a sensor, a physical system that converts signals from the real continuous analog world to the digital world. Sensing devices are the foundation of an IT/OT platform and reflect a plant operation’s vital signs because sensor data is used to inform and drive plant operational performance.
Today, a wealth of sensing technology is being used to measure, analyze, or regulate process liquids and gases, temperature, pressure, flow, level, and electrical parameters. They all have become big sources of IIoT data. The great innovation in this space is driven by technology convergence and advances in miniaturization.
“A successful digital journey rests on the quality and reliability of measured data, making suppliers with high instrument accuracy and stability well suited to IIoT applications. Yokogawa has helped develop products and standards for industrial wireless sensor networks that create the foundation for solutions that Yokogawa offers.”
How process manufacturers achieve digitization
Replacing analog instruments and control systems to support additional advanced technologies such as AI, IIoT, etc typically requires manufacturers to update their plant’s technological infrastructure and digital ecosystem. Specific technologies that comprise the framework needed for digitization include the following:
- Wireless smart sensors
- Smart devices
- Automated anomaly detection
- Cybersecurity
- Distributed Control Systems (DCSs)
- Edge computing
- Modeling and simulation
- Process data analytics
- Supervisory Control and Data Acquisition (SCADA)
Application example of successful digitization in process manufacturing
Vibration measurements for 200 items of rotating equipment installed in a chemical plant were being manually recorded by a third-party firm at a cost of $48,000 per year. The inspection results were not digitized and only represented a snapshot of data at a point in time, severely limiting the plant’s use of the information. Wireless vibration sensors were installed and connected to a LoRaWAN network, with data sent to an asset performance management system. Eventually, it eliminated the annual third-party fees and enabled real-time equipment status checks, along with automated alerts sent to plant personnel.
Learn more: Digital Transformation with digital networks
What is digitalization?
The example of vibration measurement offers a glimpse into the basic concept of digitization, but they fail to capture its full scope for a plant embarking on its journey towards a complete digital transformation.
Human operators rely on automation systems to show them the overall state of the process. This should help them identify when there are signs of abnormalities developing and the cause. In reality, the automation system shows operators a wide range of variables, leaving them to make their best interpretation. If a problem occurs, operators must respond quickly and correctly to forestall an incident. But what they really want is a system capable of indicating the state of the process and identifying which sensor to focus on when an error occurs. AI technologies can identify the main factors contributing to abnormal situations and point out the specific sensors indicating the causes. It accomplishes that through the process of digitalization.
https://www.yokogawa.com/special/artificial-intelligence/
While digitization is about the conversion of analog data to digital data for all assets, processes, and measurements, the next step involves data-driven applications, data integration, analytics, and metrics with the purpose of making processes more automated using digital.
Digitalization is the act of increasing the level of automation in processes through the use of digital technologies.
Instead of just ‘sensing’, digitalization is about “sensemaking” (adding value to data). It applies digitized information in ways that fundamentally transform business processes to create new revenue and value-producing opportunities.
More than just data
According to KBC, digitalization is about the improvement of workflows and processes, changes in supply chain relationships, and the application of knowledge and information rather than ‘just data’. KBC sees digitalization in the context of the digital applications and capabilities needed to achieve operational excellence. Applications and capabilities that derive their value from knowledge of how the plant has operated in the past combined with its current and future potential, and an actionable path to achieving and sustaining that potential.
Applied appropriately, digitalization allows manufacturers to manage day-to-day performance safely and reliably, learn from the past and respond to future swings in market dynamics, drive innovation, create value, improve safety, and improve resource management. Successful digitalization (and digitization) requires an infrastructure that supports the hardware and software needed for the act of making processes more automated through the use of digital technologies.
How process manufacturers achieve digitalization
KBC, a Yokogawa company, has published a road map entitled Digitalization Manifesto to help process manufacturers at the beginning of their digitalization journey. This road map consists of the following steps:
- Readiness
- Situational awareness
- Decision-making
- Operational execution
- Value sustainment
Download KBC’s manifesto today to learn more about its digitalization road map.

Examples of digitalization in process manufacturing | Digitalizing the value chains
To digitalize the horizontal value chain, a company can implement a smart supply chain with AI-driven analytics and a transparent shipment-tracking platform. For the vertical value chain, a company can digitally replicate its physical assets with help of a digital twin. This change allows innovations such as a paper-free shop floor and predictive maintenance systems.
The digitization of the horizontal and vertical value chains also allows companies to integrate the two chains more closely, increasing efficiency. This typically requires several operational changes, including the management of internal functions. The digital twinning of assets can also increase the availability of data, allowing for the implementation of advanced planning tools. Furthermore, digitalization adds value by improving the delivery of products.
What is digital transformation?
Digital transformation goes beyond digitalization by creating a comprehensive change to a company’s business strategy. That company might implement an isolated project as a digitalization effort, but a project that has digital transformation as its goal will create change across all departments.
With DX, technology is evaluated as an integrated set in combination with the business strategy, people, processes, data, and assets. DX is often viewed as a program with prioritized digital initiatives oriented around business processes, rather than point solutions or Proof of Concept - POCs. How process manufacturers achieve digital transformation
How to be successful in digital transformation?
Process managers who are serious about pursuing digital transformation need to develop business plans that prioritize digital initiatives, define the disciplines this transformation will use to deliver value to their customers and assess their financial costs. In other words, enterprises should frame their digital initiatives around specific business strategies and objectives.
Manufacturing enterprises also need to lay the foundation for digital transformation by treating people, processes, and technology as an integrated set. This approach helps ensure the digital transformation effort remains aligned with the company’s corporate vision and dominant business strategies such as operational excellence, product leadership, and customer intimacy.
Although the specific process may be unique for each organization, there are some key factors that successful digital transformation initiatives have in common:
Making a plan and achieving buy-in. Leaders can set their enterprises up for success by defining precise goals and fostering a workplace culture that supports digital transformation. They also need to aggressively drive this process forward with a clear business case and keep it on track with performance metrics that ensure it meets its goals for critical milestones.
Have the right people in place. Leaders must recruit and retain the workforce talent needed to achieve a successful digital transformation. This requirement means an enterprise needs workers with expertise in cutting-edge technologies as well as traditional skills like accounting and operation management.
Organize technology around data. Leaders of a successful digital transformation need to oversee new technologies that provide value for the company by improving performance and productivity. In process manufacturing, these technologies commonly include AI, IIoT, and robotics process automation (RPA). The quest for digital nirvana is enabled by technology and built upon a systematic approach to the aggregation and normalization of data.
Breaking organizational silos to collaborate. Digital transformation can eliminate data silos, making information more readily available throughout an organization. Leaders of successful digital transformation projects can take advantage of this information by keeping organization stakeholders up to date. The removal of silos also allows those stakeholders to collaborate more effectively.
Organize processes around customers. Operationalizing a strategy involves understanding, implementing, or improving business processes. Increasingly, these business processes will be oriented around the customer experience and the customer journey.
Identify quick wins and estimate benefits. Having a clear view of your customer-oriented business processes provides a clear connection to the value created for your customer and, therefore, your business.
Build a technology foundation. Leading companies ensure a stable technology foundation before moving to cross-functional integration and acceleration.
Partner up with Yokogawa
Digitization is the first step in digital transformation, which must occur before digitalization is possible. In turn, digitalization is necessary before digital transformation is possible. Digitization provides the technological infrastructure that manufacturers need to realize the full benefits of digitalization and digital transformation.
Leveraging decades of experience in process manufacturing plus our digital fluency, Yokogawa relies on its strong domain knowledge and proven IT and OT skills to help manufacturers on their digital transformation journey.
To learn more, download our eBook about Digital Transformation in the process industry. It is a starting point to layout a digitalization roadmap that thoughtfully considers people, processes, technology, assets, and data.
Zugehörige Produkte & Lösungen
-
Digital Transformation Consulting
DX Consulting provides advice and support with its global industry experience and vast technical expertise stemming from Yokogawa’s trusted digital technology and KBC’s years of improvement consulting.
-
Digitale Transformation
Yokogawa hat langjährige Erfahrung in der Prozessindustrie. Mit dieser Expertise gelingt es Yokogawa, eine digitale Transformation herbeizuführen und dadurch seinen Kunden zu einem zukunftsorientierten Betrieb zu verhelfen.
-
Yokogawa Cloud
Die Yokogawa Cloud ist eine Plattform für die industrielle Transformation und IoT zur Beschleunigung der Entwicklung und Bereitstellung von industriellen Cloud-Anwendungen. Yokogawa entwickelt im Auftrag seiner Kunden ein reichhaltiges Angebot an Plattformanwendungen und Lösungen. Die Plattform unterstützt die Erfassung, Verarbeitung und Aufbereitung von Daten aus verschiedenen Quellen, stellt branchenspezifische Algorithmen und Modelle bereit und bietet anwendungsübergreifende Integrationslösungen, um aufschlussreiche Entscheidungen treffen und einen höheren Automatisierungsgrad erreichen zu können.