Geothermal energy can generate a stable supply of electricity throughout the year because it is not dependent on weather conditions. Also, as no fuels are burned aboveground and only extremely small amounts of carbon dioxide are released, it is environmentally friendly. There are abundant geothermal resources along the circum-Pacific belt (also known as the “Ring of Fire”), in countries such as Japan, the Philippines, Indonesia, New Zealand, Mexico, Costa Rica, and the United States, as well countries such as Iceland, Turkey, Kenya and Ethiopia. Yokogawa has participated in dozens of geothermal power generation projects providing a variety of measurement and control technologies that enhance the reliability and maintenance efficiency.
Herausforderungen
Customer Challenge
Preventing corrosion that occurs when using a device in a corrosive atmosphere
Solution
The printed circuit boards that go into Yokogawa’s integrated production control systems all receive a hydrogen sulfide-resistant coating, and an anti-corrosion coating is applied to all Yokogawa field devices.
Enabling Technologies
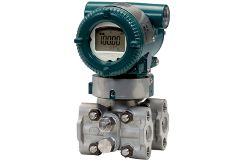
EJX/EJA Series Pressure Transmitters/Differential Pressure Transmitters
DPharp series digital pressure transmitters use a differential pressure high accuracy resonance pressure (DPharp) sensor that represents one of the most revolutionary advances in transmitter technology.

YTA Series Temperature Transmitters
YTA series temperature transmitters convert sensor inputs to a 4 to 20 mA, HART, or FOUNDATION™ fieldbus signal; this eliminates the drawbacks of wire resistance and signal noise that are often experienced with conventional temperature instruments.
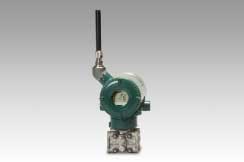
The flexibility of a wireless solution reduces infrastructure costs and enables the installation of transmitters in locations that previously were previously too difficult or prohibitively expensive to wire.
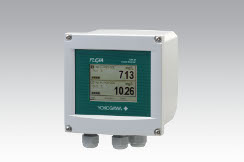
FLXA21 Modular 2-wire Liquid Analyzer
The FLXA21 is a next-generation modular liquid analyzer that can be flexibly configured to measure pH/ORP, contacting conductivity, inductive conductivity, and dissolved oxygen. The FLXA21 also supports the installation of up to two sensors of the same type, thereby reducing installation costs and saving space.
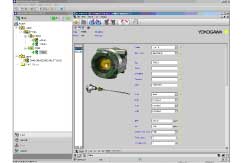
Plant Resource Manager (PRM) makes predictive maintenance easy. Early detection of system and device malfunctions helps prevent catastrophic failures.
Customer Challenge
Reliably performing the remote monitoring and control of facilities such as steam wells and reinjection wells that are located at a considerable distance from a geothermal power plant
Solution
Yokogawa installs remote I/O modules and utilizes a fiber optic redundant ring topology to ensure reliable communications between the integrated production control system and field devices. Wireless field devices are used in difficult to wire locations.
Enabling Technologies
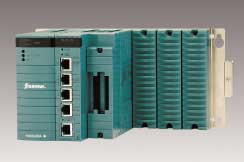
STARDOM Network-based Control System
Dual redundant and low-power configurations are available for the STARDOM hybrid PLC/intelligent RTU. STARDOM supports HART, Modbus, FOUNDATION™ fieldbus, and other network protocols.
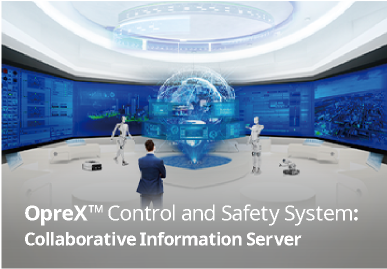
Collaborative Information Server (CI Server)
Yokogawa CI Server allows immediate improvement to production efficiency through digital transformation and reduction of operational maintenance whilst building a digital transformation framework.
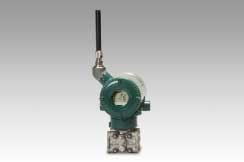
The flexibility of a wireless solution reduces infrastructure costs and enables the installation of transmitters in locations that previously were previously too difficult or prohibitively expensive to wire.
Customer Challenge
Efficiently maintaining equipment that is located at a considerable distance from a geothermal power plant
Solution
Yokogawa’s Plant Resource Manager (PRM) is an integrated device management software package that enhances maintenance efficiency by making it possible to remotely monitor the status of devices and make changes to their settings. This minimizes the amount of time workers need to spend at geothermal sites for troubleshooting and other tasks, and thus minimizes their exposure to hydrogen sulfide gas, which, in sufficiently high concentrations, can present a health risk.
Enabling Technologies
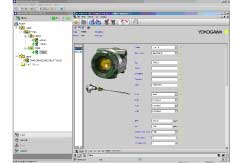
Plant Resource Manager (PRM) makes predictive maintenance easy. Early detection of system and device malfunctions helps prevent catastrophic failures.
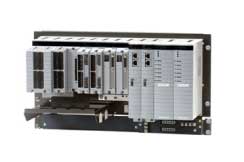
CENTUM VP Integrated Production Control System
The CENTUM VP integrated control system secures interruption-free “uptime only” plant performance for optimal productivity and profitability in the renewable energy field.
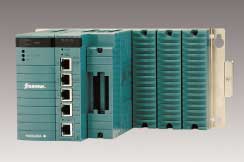
STARDOM Network-based Control System
Dual redundant and low-power configurations are available for the STARDOM hybrid PLC/intelligent RTU. STARDOM supports HART, Modbus, FOUNDATION™ fieldbus, and other network protocols.
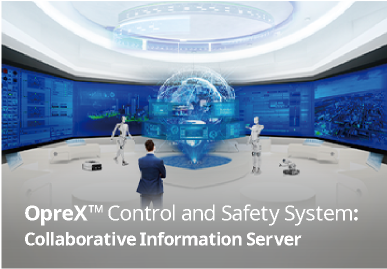
Collaborative Information Server (CI Server)
Yokogawa CI Server allows immediate improvement to production efficiency through digital transformation and reduction of operational maintenance whilst building a digital transformation framework.
Details
Geothermal Power Generation Process
A steam well is dug to draw fluid comprised of steam and hot water from a geothermal reservoir located deep underground. The fluid mixture is introduced to a steam separator that removes the moisture from the steam, and the steam is then used to drive the turbine of an electricity generator. Low-temperature steam discharged from the turbine is passed through a steam condenser to return the water vapor to a liquid state, and the water is then returned to the underground reservoir by means of a reinjection well.
Control and Measurement Technologies
Plant-wide Systems and Instrumentation | ||
---|---|---|
Information
|
Control
|
Measurement
|
Processes | ||
Fluid Transportation | Main Geothermal Power | Turbine |
|
|
|
Publikationen
Aboitiz Power Corporation is a holding company that was set up by the Aboitiz Group to oversee its investments in power generation, distribution, retail, and services. The company owns and operates several hydroelectric and geothermal power plants as well as a number of non-renewable power facilities throughout the Philippines. It also owns distribution utilities that are centered in high-growth areas in Luzon, Visayas, and Mindanao.
PT PLN selected Yokogawa to automate plant and turbine startup/shutdown processes in 2008.
In 2021, a plant expansion project was successfully completed through continuous collaboration between the customer and Yokogawa.
Geothermal power plants create electricity from geothermal energy. These power plants are similar to other steam turbine station; however their heat source is that of the earth's core. The created steam is used to turn the turbine for the production of electricity. Technologies include Dry steam, Flash steam and Binary cycle power stations with Binary cycle being the most common geothermal plant in current production. In the process of geothermal power generation the facility needs to monitor various processes, as in this case steam line pressure sits in remote from control room's location.
The ammonia (NH3) gas is injected to remove the NOx and thus reduce the NOx concentration in the stack flue gas. With conventional NH3 analyzers that perform measurements indirectly, NH3 concentrations are obtained through a sampling system. Therefore, there are problems with the maintenance and running costs of the sampling system, and time delays in measurement. The TDLS8000 Laser Analyzer is the solution to all these problems.
The worlds of process automation and production management have been converging for some time. What once used to be islands of automation and production management functionality connected through highly proprietary integration schemes that were costly to maintain have developed into integrated platforms that provide seamless data exchange between the world of automation and the plant floor, the functions of production and operations management, and integration with business level systems.
Process automation end users are under more pressure than ever to do more with less. The current economic climate means that many automation capital projects are on hold. With capital budgets tighter than ever, users instead focus on operational budgets (where cost cutting is also a key concern), or on automation investments with a very rapid return on investment.
Yokogawa has come a long way in making its message clear to the world of process automation. Last year, the company embarked on a full-scale global marketing campaign to make customers aware of the company's focus on system reliability, security, dependability, and robustness. Dubbed "Vigilance", the campaign created a unified message for the company and greatly helped expand awareness of the Yokogawa brand and corporate philosophy.
The automation suppliers that will be successful in the long term will be those that effectively address application or industry specific problems for end users with a value proposition that cannot be ignored. These problems exist throughout the process industries today, and they won't be solved by simply offering a product, but through a combination of hardware, software, services, application expertise, and knowledge.
In ARC's view, customers need a compelling business value proposition to justify investment in any kind of automation. Vigilance and VigilantPlant were created with this in mind. Yokogawa's vision with VigilantPlant is to create an environment where plant personnel and operators are well informed, alert, and ready to take action.
In today's dynamic industrial marketplace, the only constant is change. Raw material costs, energy costs, market demands, environmental and safety regulations, technology, and even the nature of the labor force itself are constantly changing, and not always in predictable directions.
This white paper provides an overview of how Yokogawa believes its customers can best prepare for and position themselves to benefit from IIoT-enabled technology and solutions and digitalization in general to emerge as the successful connected industrial enterprises of the future.
Yokogawa’s industrial automation (IA) product and service offerings, industry domain knowledge, and VigilantPlant approach – which emphasizes safe, secure, and uninterrupted operations -- provide a solid foundation for an Industrial Internet of Things that specifically addresses the requirements of process automation, particularly for the OT side of the equation. To be able to provide an equally solid foundation for the IT side, Yokogawa is partnering with Cisco Systems and other industry leaders.
Recently, there is an increasing demand for operation and monitoring of all the various controllers distributed in the field on the same screens to improve plant operation efficiency. The purpose of the Unified Gateway Station (UGS) is to connect external controllers, such as the STARDOM's FCN/FCJ autonomous controllers and other vendors' controllers, to the CENTUM VP integrated production control system and to operate and monitor those external controllers on the Human Interface Station (HIS) screens, the operation and monitoring screens for the CENTUM VP.
Recently, manufacturing industries are trying to slash the total cost of ownership (TCO). Batch processes are not exceptions. Until recently, in comparison to continuous processes, batch processes have generally not yet undergone systematization and standardization.
As industrial plant systems have increased in scale and their automatic control algorithms advanced, today's operators are required to have more advanced skills and knowledge of theplant systems and to learn the actions to be taken in response to any possible situations including emergencies.
The trend of open system architecture is becoming an important issue with distributed control systems (hereinafter abbreviated as DCSs). To meet this demand, the operation and monitoring functions, and the system generation functions of the CENTUM CS 3000 system are designed to support Windows NT and OLE for Process Control (OPC).
As more fieldbus devices are made practicable, demand is increasing for a distributed control system (DCS) which integrates fieldbus devices in its engineering, operation, and monitoring environments. Conventionally, control has been implemented by the dual-redundant CPUs and control bus within a DCS; however, sufficient reliability must be ensured even when it is distributed over field networks.
The recent increase of devices enabled for a field network such as the FOUNDATION™ Fieldbus is phenomenal. This has been amplifying a requirement for distributed control systems (DCSs) to be capable of constituting a more pliant and efficient production control system by means of flexible connections to field networks in addition to traditional 4 to 20 mA signals.
The environment surrounding process control systems has changed dramatically as the performance of personal computers improves and the Windows operating system advances, there has been a move towards the trend of open architecture. As we are already aware, in addition to the traditional high reliability level and the unique operability there has been an increase in demand for the interoperability of human- machine interfaces (HMI), which are responsible for the operation and monitoring of our distributed control system (DCS).
Drastic changes in the economy of manufacturing industries, has led to increasing demand for plant operations to reduce personnel, improve efficiency, and increase the operation rate of facilities. On the other hand, for plants to operate safely, improvements in reliability and operational safety cannot be neglected.
In this day and age, just simply buying a personal computer, taking it home and turning it on will enable you to be taken to the world of Internet. In such an era, communication connection capability and prospects is increasing in importance. DCSs are no exception for concern.
The manuals of control systems such as a DCS provide a vast amount of information depending on their multi-functionality and functional integration. A conventional large-scale control system our company offers comes with more than 10,000 pages of paper documents.
Yokogawa Electric has been using Pair & Spare method as a reliability-enhancing technology for its line of distributed control systems (DCS) since the release of the CENTUM CS in 1993. As a result, the system has achieved an availability factor of seven 9's (99.99999%) for the record of operation to date.
Field instruments are expected to be equipped with diagnostic functions to predict abnormal process conditions, and are also expected to expand these functions. The ability to extract diagnostic information for prediction and prevention from various physical process quantities measured by devices and make it available allows the user to reduce non-essential and non-urgent maintenance and thus cut maintenance costs.
Safe plant operation has long been pursued in all industries. Specifically, in the process automation industry which involves many hazardous elements, safety measures including explosion-protected systems have been adopted based on numerous tragic experiences.
Since the release of the DPharp EJ series in 1991 and the DPharp EJA series in 1994, nearly 1.2 million of these transmitters have been operating all over the world. Recently, we have also developed the EJX series of even more compact, lightweight and advanced transmitters with multi- sensing capabilities built using silicon resonant sensor technology.
In recent years, more field wireless devices have been used in hazardous areas. Meanwhile, in plants that are usually recognized as hazardous areas, there are numerous metallic tanks and pipes that easily shield or reflect radio waves, as discussed later, thus resulting in a poor environment for wireless communication.
The first stage in creating next-generation production control system that achieves innovative plant operation is providing "Visualized operation". "Visualized operation" for the customer means that he can reliably access and visualize plant data regardless of plant location and time.
The manufacturing industry has grown based on solid production technologies for creating quality products. However, the economic environment is changing dramatically, forcing manufacturing firms to face tough global competition; firms must ship the right products at the right time as the market requests.
CENTUM VP is a next-generation Integrated Production Control System which provides solutions to improve operation efficiency (Operational Excellence) based on Yokogawa's VigilantPlant concept. In the development of Integrated Production Control Systems, we have expanded the functions of the Human Machine Interface (HMI) maintaining the main essence of CENTUM series, regardless of the changes of platforms.
To date, Yokogawa has focused on DCS (Distributed Control System) which control the entire power generation plant, including boilers, in the electric power industry. In contrast, turbomachinery control has been handled by turbine manufacturers, but as the electric power market has been active internationally, especially in China and India, in recent years, Yokogawa has been developing turbomachinery control systems to to further develop the electric power industry.
There has been increasing demand for cost reductions and lower-priced products in the manufacturing industry, and maintaining cost competitiveness and achieving optimum costs have become necessary for the survival of manufacturers. This calls for minimizing TCO (Total Cost of Ownership) over the whole life cycle of plants and maximizing TVO (Total Value of Ownership).
Process automation involves both operation and maintenance. Plant operation and monitoring are mainly conducted by a control system such as CENTUM, while equipment maintenance is handled by Plant Asset Management (PAM) such as Plant Resource Manager (PRM).
As compared to Distributed Control Systems (DCS) such as CENTUM VP that monitors the operations of the overall plant, PRM is a type of Plant Asset Management (PAM) software package that primarily focuses on the maintenance of devices and instruments.
Asset Excellence (AE) provides a set of solutions for maintaining a plant in good condition at reasonable cost to ensure that it works as a production infrastructure. To reduce maintenance costs without causing a risk to production, it is necessary to change from breakdown maintenance to predictive or preventive maintenance.
Yokogawa Electric Corporation promotes the standardization of FOUNDATION™ fieldbus as the communication foundation supporting Asset Excellence for VigilantPlant, which is an approach aimed at the advancement of plant instruments and equipment. With the recent dramatic advancement of fieldbus technologies, information processing technologies, and network speed, it has become possible to process various kinds of information inside the field sensors and transmit the results to the distributed control system (DCS) and host computer.
In plant sites, there are various places such as those affording an unobstructed view like tank yards, and others surrounded by metal pipes and equipment obstructing the view (hereafter referred to "pipe jungles"), often seen in oil refinery and chemical on-site plants. The frequency band of radio waves used for field wireless communication is 2.4 GHz, which has high straightness and its ability to go around things can hardly be expected.
In 2005, Yokogawa announced "VigilantPlant" as a concept to ward the realization of a type of plant operation that is considered ideal by our customers.
Environmental friendliness (E) must be assessed in today's product design in addition to the conventional design considerations of quality (Q), cost (C), and lead time (D). Hence, the product design system must be urgently restructured in order to minimize the environmental impact of a product throughout its life-cycle from purchase of the materials and parts, through manufacturing and distribution, to use and disposal.
As a company that has strong relationship with nature and provides products using nature's blessings, Mercian Corporation is committed to the environment. Its environmental philosophy is "Mercian thanks nature's blessings and capability that sustain life, and seeks to balance environmental preservation with creating an affluent society."
As for a controller used in a distributed control system (DCS) shown in Figure 1, covering as many applications as possible with a single controller will bring cost reduction effects such as easy engineering and a small controller installation area. Therefore, the controller is required to process large amounts of data more quickly.
More than ten years have passed since the first digitized field devices were introduced. These support either a hybrid communication protocol such as HART or a full digital communication protocol such as FOUNDATION Fieldbus.
The specifications of the ISA100.11a wireless communication standard of the International Society of Automation (ISA) for industrial automation were published, and companies are developing products based on the standard. The ISA100.11a has many features such as high reliability including redundancy, network scalability, and support for various protocols for industrial automation.
For safe plant operations, it is critical to correctly understand the conditions encountered by operators inside the plants. In relation to this topic, human cognition has been studied in various fields such as human factors and ergonomics.
As field instrumentation devices become increasingly digitized and computerized, interactive and remote access to a large quantity of field information becomes possible. This will increase the efficiency of plant equipment maintenance by reducing labor requirements in field patrol work for example.
The requirements for water supply and sewage services are becoming increasingly strict, such as consolidation of facilities, operational efficiency, lower cost, and information transparency due to stagnant demand. There is also demand for greater use of information technologies (IT), encouraged by the government's e-Japan strategy.
Industrial automation (IA) systems and products, which utilize measurement, control and information technologies, are used across the world as fundamental infrastructure for achieving safe, stable and highly efficient plant operation. In order to keep the systems and products effective throughout the plant lifecycle, customers need to periodically check their effectiveness and take prompt action if any problem is identified.
Global market pressures are causing businesses world wide to strive to lower manufacturing costs and to become more agile companies in order to quickly respond to changes in market demands and to fend off competitive threats. Yokogawa's customers in all industries and markets are responding to this pressure by working to more closely integrate their plant manufacturing systems with their enterprise wide business systems in a seamless manner.
Recently, standardization of procedural automation of manual operations has been promoted mainly by the International Society of Automation (ISA), and the functional requirements necessary for automation are being studied by the ISA106 committee in the US.
For a coal fired power generation plant (hereafter referred to as "BTG facilities," in which "BTG" stands for boiler, steam turbine, and generator) supplying power to a large-scale production plant, the CO2 emissions from such facilities are a critical issue today.
Environment and safety are major topics on a global scale in recent times. As symbolized by the effectuation of the Kyoto Protocol, an interest in preserving the environment is growing worldwide, and there is also a tendency to criticize more severely, occurrences of industrial accidents that are accompanied by environmental contamination or which may cause damage, etc., to residents in the surrounding areas.
In recent years, expectations for control systems using wireless communications have been increasing in the process control market. This is because these systems do not require power and communication wiring for field instruments, enabling reduced initial and maintenance costs, and easy installation.
Yokogawa has been leading the process automation industries as one of the pioneers in field digital technologies represented by the FOUNDATION fieldbus™ and Field Device Tool/Device Type Manager (FDT/DTM).
Due to emerging competitors from the rapidly growing countries such as India and China and the global economic downturn triggered by the Lehman shock, many companies in the process industries are struggling to survive the severe global competition.
News
-
Pressemeldung | Corporate Jun 11, 2024 Managementlösungen für erneuerbare Energien: Yokogawa erwirbt BaxEnergy
Die BaxEnergy GmbH mit Hauptsitz in Hannover ist ein führender Anbieter von Lösungen für das Management erneuerbarer Energien (REMS). Yokogawa wird diese Lösungen den Betreibern von Energieanlagen weltweit zur Verfügung stellen.
-
Pressemeldung | Projects Sep 1, 2022 Für maximale Effizienz: Yokogawa installiert IoT-System im größten Geothermiekomplex Afrikas
Das IoT-System nutzt mobile Kommunikation und weitere Technologien für ein innovatives integriertes Remote Performance Management in den Kraftwerken des Geothermiekomplexes Olkaria, Kenia. Gemäß den Anforderungen der UNIDO hat Yokogawa ein System entwickelt und implementiert, das den Zugriff auf die Daten der Kraftwerke I AU, II, IV und V vom Verwaltungssitz des Komplexes aus ermöglicht und so ein integriertes Fernmanagement der Stromerzeugungsleistung in diesen Anlagen erlaubt.
-
Pressemeldung | Projects Jan 25, 2021 Yokogawa erhält Auftrag über Automatisierungssystem für Geothermie-Kraftwerk in In-donesien
Erneuerbare Energien spielen weiterhin eine wichtige Rolle bei den Nachhaltigkeitsanstrengungen des Unternehmens
Möchten Sie weitere Informationen über unsere Mitarbeiter, Technologien und Lösungen?
Kontakt