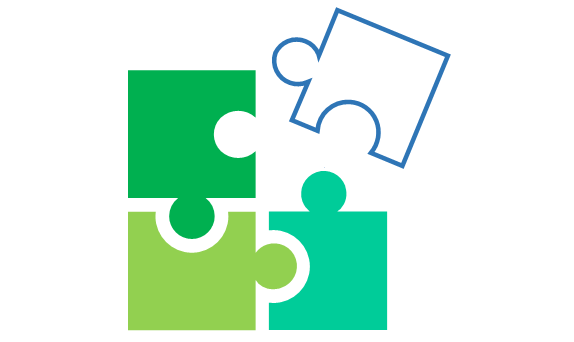
Yokogawa has focused on developing a supply chain that considers environmental protection and human rights. We will actively identify risks that impede sustainable procurement, taking the path to improvement with our business partners, and strengthening activities aimed at achieving our sustainabiliy goals "Three goals".
Summary of Activities
We are identifying risks that impede sustainable procurement with our business partners, focusing on understanding the actual conditions of the following 4 areas(defined in Yokogawa Group Sustainable Procurement Guidelines for Suppliers) : "Labor and Human rights" "Health and safety" "Environment" and "Ethics". In case a risk is realized, we work with our suppliers to take measures against it. We also develop educational programs on sustainable procurement both inside and outside the company. We set KPIs to manage and measure the progress of sustainable procurement activities.
Overview of suppliers
The Yokogawa Group deals with more than 10,000 suppliers in 70 countries annually. The percentage of supplier countries in 2021 is as follows:
Report on Results of Activities in FY2021
In 2020, we positioned the year as the starting year for sustainable procurement, and conducted activities to reduce CSR risks in the supply chain based on human rights due diligence.
How to proceed with activities
1) PDCA cycle of activities
Based on the KPIs established in FY 19, we will strive to reduce supply chain CSR risks through communication with suppliers. The cycle of its activities is illustrated below.
Yokogawa positions this SAQ (self-assessment questionnaire) as a communication tool with important suppliers for sustainable procurement as a human rights due diligence, and uses the analysis results of this survey to analyze risks and promote improvement activities.
2) Global collaborations
We select suppliers to implement SAQ (self-assessment questionnaire) from a global procurement system’s data.
Every year, the procurement control department at the head office formulates an SAQ implementation plan, and affiliated companies of the Yokogawa Group, which deal directly with suppliers, request SAQ implementation.
We also ask our suppliers to submit SAQ responses from the facilities that supply the Yokogawa Group. Therefore, if the direct supplier (Tier 1 Supplier) purchases from another company, the production facility of the purchaser (Tier 2 and lower) submits the SAQ answers.
Below is a schematic diagram of the SAQ request flow.
The ratio of Tier 1 Supplier and Tier 2 and lower in the SAQ response submission facilities of FY21 is as follows.
3) Analysis of FY2021 “Self Assessment Questionnaire(SAQ)” Results
In sending the SAQ, we selected 200 companies and asked them to respond. As a result, we received SAQ responses from 167 business sites.
The SAQ divided the questions into three categories and scored them based on their answers. The average score rate is as follows.
The scoring results were fed back to the facilities that submitted the answers. In addition, we analyze the scoring content and communicate with facilities with a predetermined score or less using a sheet for improvement.
In addition, based on the 2020 score, we communicated with suppliers who were judged to be high-risk suppliers for improvement, and also sent a re-SAQ in FY2021 to monitor the change status.
In 2021, due to the influence of COVID-19, we could not visit suppliers, but based on the SAQ's response, we had an online interview with some suppliers to cooperate in improvement.
Education
Regarding how to proceed with sustainable procurement, we hold regular meetings with the procurement departments of global affiliated companies to deepen the study of the movements of each country's laws and regulations regarding sustainable procurement, and to share and collaborate on SAQ implementation results and implementation plans. In addition, we are actively participating not only internally but also outside the company, such as formulating SAQs for JEITA's "Responsible Corporate Behavior Guidelines" and giving lectures at seminars.
Activity plans and results
Yokogawa group is formulating its sustainable procurement activities with reference to ISO 20400 (Guide to Sustainable Procurement). Since fiscal 2020, we have been conducting a cycle of identifying high-risk business sites, providing written feedback, and monitoring the site, by receiving support from experts and evaluating responses from suppliers.
1) SAQ Implementation Plan and Results
The targets of SAQ are suppliers in high-risk industries among the 1070 suppliers that account for the top 80% of the group purchase amount from the transactions (approximately 10,000 suppliers) with a purchase record of the Yokogawa Group as a whole. We selected 600 suppliers(selected by the experts' knowledge). The Group plans to evaluate and improve "these 600 suppliers" in three years. In 2021, we selected 200 companies other than those that requested SAQ in 2020, and provided SAQ and subsequent feedback.
KPI |
Cumulative number of Companies to be sent |
Cumulative sending(SAQ) companies |
Number of facilities of got filled out SAQ |
Target Fiscal year |
---|---|---|---|---|
Number of work-places of suppliers executing SAQ |
200 companies |
191 companies |
166 facilities |
FY 2020 |
400 companies | 389 companies | 333 facilities |
FY 2021 |
|
600 companies |
FY 2022 |
2)Supplier agreement to our sustainable procurement policy
We have confirmed our support for sustainable procurement initiatives in our group's supply chain in order to work together with our business partners to make improvements.
KPI |
Cumulative number of facilities |
Number of facilities that agreed our code |
Target Fiscal year |
---|---|---|---|
Number of Suppliers who Support Sustainable Procurement |
70 facilities |
135 facilities |
FY 2020 |
140 facilities | 267 facilities |
FY 2021 |
|
210 facilities |
FY 2022 |
An example of the reason for a business establishment that does not support our sustainable procurement was "because it complies with the RBA Code of conduct".