Current Situation and Issues
The Throughput in a Mining Operation Is Directly Proportional to the Conveyor Belt Systems Performance
Sometimes, the roller has the difficulty to rotate (mainly due to a bearing failure and the constant friction between the roller and rubber belts) often resulting in a fire occurrences. In that case, the plant has to stop production in long term, which causes catastrophic damage to the management. Hence, continuous monitoring of all rollers temperature is required to prevent fire and minimize downtime.
Manual/route-based monitoring with IR thermal inspections
The onset of temperature spikes cannot be predicted.
It could happen after the route has been completed. Also, some areas of the conveyor belt maybe in unsafe places.
Install wireless point sensors at given points
Only a partial health status visibility of the assets within the plant.
Initial cost and running cost increase when a number of wireless point sensors are installed.
Convectional linear heat detector
It can detect when fire-accident actually happens by the short circuit of twisted pair metal wire with melted outer. It can’t prevent fire and locate the location of fire.
They should aspire to move towards digitalizing the inspection and maintenance processes.
YOKOGAWA's DTSX Solution and Benefits
- Ability to monitor long and wide conveyor belts in real-time.
- HMI graphical drawings enable excellent visibility for operators.
- Centralized monitoring and diagnostics permits failure prediction.
- 7-10x lower downtime and 70% OPEX savings compared to reactive and proactive monitoring models.
Comparison of downtime periods for each maintenance way
The Integrated Conveyor belt Monitoring Solution
Features of Optical Fiber Sensing in DTSX System
Temperature distribution monitored every 1 m
- Monitoring distance : to 50 km
- Monitoring temperature : -200 to 300 °C
- Shortest monitoring cycle : Approx. 5 seconds
- Temperature resolution : 0.03 °C
*: each specification dependent on conditions
Main Features
- 24 hours a day, 365 days a year monitoring even in wide areas and ordinarily non-manned areas
- Power supply not required, explosion-proof, not affected by electromagnetic noise
- Flexible installation
- High compatibility with DCS and other host systems (Modbus / TCP)
Customer Case Studies
Quick implementation of new conveyor belt fire detection system
The customer had implemented a Linear Heat Detector (LHD) to detect fires, however the maximum coverage length was 3kms and was furthermore unable to precisely locate the position of fire.
Eventually, the customer came across an unexpected fire accident and needed to replace a fire detection system very quickly.
Yokogawa performed a quick site feasibility study, implemented the DTSX solution with no lead time, and acquired the customer’s firm trust.
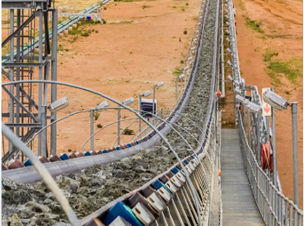
Realize managing bioleaching in vast Copper Mines
Bioleaching is a popular organic process to extract metal from low-grade ores. The organic process involves the application of bacteria, which loses its effectiveness at very high and low temperature extremes. The challenge was to measure the thermal profile of phreatic level over a vast area. As it was difficult to measure temperature over a long distance using traditional electronic based measurement, The customer selected Yokogawa’s DTSX. The solution provided a high resolution temperature profile with no need of specialized knowledge. 24/7 access to temperature data from a HMI panel allowed the customer to take necessary actions to adjust temperature levels.
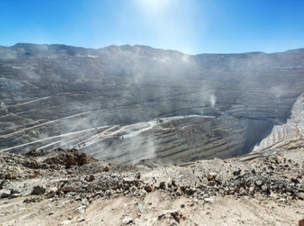
* Some graphs and images are quoted from the eBook ("Digitalize Conveyor Belt Monitoring") created by Frost & Sullivan.
Looking for more information on our people, technology and solutions?
Contact UsRelated Industries
-
Renewable Energy
Renewable energy helps protect the environment and brings both society and industry closer to the goal of achieving sustainability. We provide solutions for renewable energy applications worldwide, thus contributing to the sustainable development goals. I
-
Power
In the mid 1970s, Yokogawa entered the power business with the release of the EBS Electric Control System. Since then, Yokogawa has steadfastly continued with the development of our technologies and capabilities for providing the best services and solutions to our customers worldwide.
Yokogawa has operated the global power solutions network to play a more active role in the dynamic global power market. This has allowed closer teamwork within Yokogawa, bringing together our global resources and industry know-how. Yokogawa's power industry experts work together to bring each customer the solution that best suits their sophisticated requirements.
-
Pulp & Paper
The paper and pulp industry is highly competitive and must meet ever-changing market needs. Yokogawa helps realize energy-efficient plants which are globally sustainable.
-
Iron & Steel
In the iron and steel industry, it is crucial to improve the quality of not only products but also manufacturing and operation technologies, as well as to address environmental and energy-efficiency issues. Yokogawa helps customers to create the ideal plant and evolves with them for mutual growth.
Related Products & Solutions
-
DTSX1 Fiber Optic Heat Detector
DTSX1 stores the functions required for heat detection in one box. DTSX1 analyzes the temperature data with high accuracy by measuring with fiber optic sensor cable and perform high temperature heat detection.
-
DTSX200 Distributed Temperature Sensor
The DTSX200 is a standard version that is ideal for temperature measurement, for medium-sized areas, and for areas where the distance of fiber optic sensor cables is short. It has excellent environmental resistance because it consumes less power and is less dependent on the temperature measurement environment.
-
DTSX3000 Distributed Temperature Sensor
The DTSX3000 is a distributed temperature sensor developed in response to the demand that “one unit be used to monitor temperature distribution a longer distance and a wider area”. A flagship model that meets the expectations for long-distance temperature measurement and high temperature resolution.
-
Fiber Optic Temperature Sensor DTSX
The DTSX fiber optic temperature sensor, which uses optical fiber for the temperature sensor, quickly detects and locates abnormalities in equipment by monitoring temperatures at production facilities located far away and across wide areas 24 hours a day, without omission. Highly accurate predictive maintenance avoids downtime and ensures stable plant operation.