The DTSX is a unique and innovative temperature monitoring system that uses fiber optic cable as temperature sensors.
Current Situation and Issues
Drop in Productivity Caused by Temperature Unevenness in Drying Furnace
The temperature inside the drying furnace of the coating drying process for the separators/electrodes that make up a lithium-ion battery is linked to product quality. However, at present, the in-furnace temperature cannot be grasped as a temperature distribution simply by installing thermocouples, for example, at several meter intervals.
In the drying process, changes in the furnace structure, size, heating method, coating material, etc. and various factors even during a single day cause the in-furnace temperature to become uneven.
For this reason, drying performance might vary. This might increase the incidence of quality defects and lead to a drop in productivity.
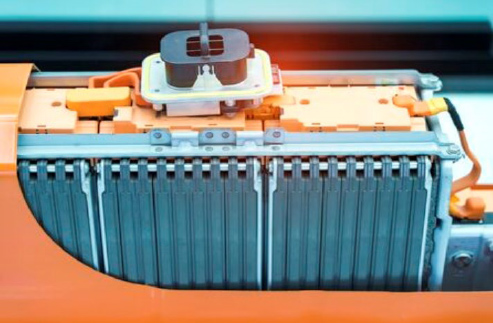
Solutions and Benefits
Fiber Optic Cable Visualizes In-furnace Temperature Distribution
The DTSX fiber optic distributed temperature sensor can monitor temperature distribution every meter along the path of the fiber optic cable.
Thermocouples, etc. are used for heater control as up till now, and by adding DTSX to them, it will be possible to visualize the temperature distribution inside the entire drying furnace.
Resolving heater and other problems by utilizing the result, and passing products through the furnace after setting the in-furnace temperature to the ideal temperature profile result in improved productivity.
When attempts are made to measure multiple points by thermocouples, etc., wiring is complicated, construction costs escalate and periodic maintenance of each individual sensor is required. This is unrealistic when applying it to multiple drying furnaces.
As the DTSX system requires only laying fiber optic cable inside the furnace, both initial and running costs can be reduced.
Moreover, a single DTSX can cover multiple drying furnaces, which improves cost effectiveness.
The DTSX has also been put to use in monitoring the temperature distribution in tunnel furnaces.
Features of Optical Fiber Sensing in DTSX System
The Fiber Optic Cable Is The Temperature Sensor
Temperature distribution monitored every 1 m
- Monitoring distance : to 50 km
- Monitoring temperature : -200 to 300 °C
- Shortest monitoring cycle : Approx. 5 seconds
- Temperature resolution : 0.03 °C
*: each specification dependent on conditions
Main Features
- 24 hours a day, 365 days a year monitoring even in wide areas and ordinarily non-manned areas
- Power supply not required, explosion-proof, not affected by electromagnetic noise
- Flexible installation
- High compatibility with DCS and other host systems (Modbus / TCP)
Other In-vehicle Lithium-ion Battery Applications
Smart Monitoring of Manufacturing Process Shelves and Storage Shelves
Thermal runaway of lithium-ion batteries mounted on individual racks is discovered at an early stage. This enables a quick initial response when an abnormality occurs to limit damage to a minimum.
(For details, refer to "Smart Monitoring of Manufacturing Process Shelves and Storage Shelves -In-vehicle Lithium-ion Battery Applications- ".)
Prevention of Fires in Exhaust Air Ducts in Battery Assembly Process
Fires or dust explosions in exhaust air ducts for preventing the contamination of aluminum dust in the assembly process of lithium battery batteries are monitored. Abnormalities are not overlooked as ducts extending over long distances in blind areas such as roof space are comprehensively monitored.
(For details, refer to "Prevention of Fires in Exhaust Air Ducts in Battery Assembly Process -In-Vehicle Lithium-ion Battery Applications-".)
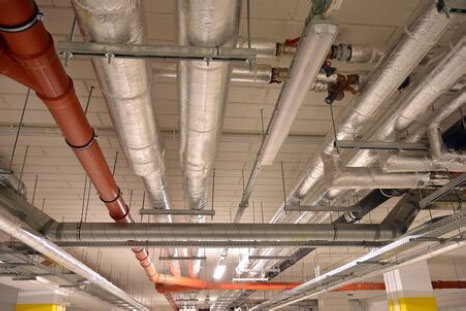
Monitoring of Soundness of Power Supply Bus Bar
The joints of the power supply bus bar are monitored.
Abnormalities are not overlooked as fiber optic cable is built into the bus duct and bus bars extending over long distances in blind areas such as roof space are comprehensively monitored.
(For details, refer to "Monitoring of Soundness of Power Supply Bus Bar -In-vehicle Lithium-ion Battery Applications-".)
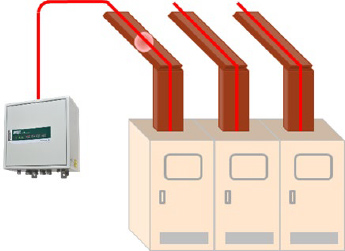
Industrias Relacionadas
-
Química
Chemical plants rely on continuous and batch production processes, each posing different requirements for a control system. A continuous process calls for a robust and stable control system that will not fail and cause the shutdown of a production line, whereas the emphasis with a batch process is on having a control system that allows great flexibility in making adjustments to formulas, procedures, and the like. Both kinds of systems need to be managed in available quality history of product, and to be able to execute non-routine operations. With its extensive product portfolio, experienced systems engineers, and global sales and service network, Yokogawa has a solution for every plant process.
-
Mobility-to-X
Yokogawa is enhancing the quality and performance of European battery technologies; accelerating the growth of electro-mobility, shortening the journey to net zero.
Productos y Soluciones Relacionadas
-
DTSX1 Fiber Optic Heat Detector
DTSX1 stores the functions required for heat detection in one box. DTSX1 analyzes the temperature data with high accuracy by measuring with fiber optic sensor cable and perform high temperature heat detection.
-
DTSX200 Distributed Temperature Sensor
The DTSX200 is a standard version that is ideal for temperature measurement, for medium-sized areas, and for areas where the distance of fiber optic sensor cables is short. It has excellent environmental resistance because it consumes less power and is less dependent on the temperature measurement environment.
-
DTSX3000 Distributed Temperature Sensor
The DTSX3000 is a distributed temperature sensor developed in response to the demand that “one unit be used to monitor temperature distribution a longer distance and a wider area”. A flagship model that meets the expectations for long-distance temperature measurement and high temperature resolution.
-
Fiber Optic Temperature Sensor DTSX
The DTSX fiber optic temperature sensor, which uses optical fiber for the temperature sensor, quickly detects and locates abnormalities in equipment by monitoring temperatures at production facilities located far away and across wide areas 24 hours a day, without omission. Highly accurate predictive maintenance avoids downtime and ensures stable plant operation.