Executive Summary
Osaka Gas Chemicals Co., Ltd., a group company of Osaka Gas Co., Ltd., plays a role in the global carbon fiber industry. Through the introduction of Yokogawa's Digital Plant Operation Intelligence (DPI) data analysis solution and the engagement of everyone from experienced employees to young engineers in waigaya* discussions, the company has successfully addressed long-standing problems and improved the efficiency of the operations at its Torishima plant, and has established a system for the nurturing and utilization of knowledge by the organization.
* Spontaneous brainstorming discussions in which everyone, regardless of position in the organization, speaks frankly and debates with others.
The Challenges and the Solutions
A long-standing problem with carbon fiber manufacturing
Osaka Gas Chemicals' carbon fiber manufacturing plant sometimes experienced a problem with its heating process that decreased production efficiency, raised costs, and increased operator workload. While significant improvements had been made as the result of continuous efforts to improve the production process, a complete solution had not yet been achieved. Yuki Yoshida, an employee in the plant facility engineering department, initiated this project because he saw that such a challenge could be better addressed by changing the corporate culture to encourage a free exchange of knowledge and ideas across departmental lines and a cross-departmental approach to solving problems.
To assist it in discussing and analyzing data to identify the root causes of the problem and find a solution, Osaka Gas Chemicals turned to Yokogawa for a consulting solution and the provision of DPI training.
Workshop-style problem-solving solution
In response to Osaka Gas Chemicals' request, Yokogawa proposed a hypothesis verification data analysis workshop to construct and verify hypotheses using DPI. A workshop was scheduled to carry out the following:
- Share knowledge and ideas to form hypotheses on possible problem causes
- Analyze data using DPI in order to verify these hypotheses
- Based on knowledge of the process, engage in waigaya to discuss the validity of the analysis results
- Plan improvements
Problem-solving with pyramid structure approach
Session 1: Hypothesis construction
In September 2019, Yokogawa sent a facilitator and an analyst to the customer site to hold the first workshop session. Waigaya discussions focused on what could be causing the problem with the heating process. The participants were young, mid-level, and veteran operators and engineers who worked in manufacturing, manufacturing management, facility engineering, quality management, and development. At first no one seemed willing to speak up, but gradually they started to draw on their own knowledge to express like "It have something to do with the temperature at startup" and "There is a specific temperature rise pattern that precedes the problem". They discussed not only the heating process but also the processes that precede and follow it. This discussion among people who had differing perspectives and experiences brought many discoveries to each other, and this was true also for veteran engineers. During this session, Yokogawa also instructed the workshop attendees in how to analyze data using the DPI software.
Through these waigaya, nine hypotheses were constructed.
Hypothesis pyramid
Session 2: Hypothesis verification
During the second workshop session, which was held in November, the DPI software was used to analyze the data, with the aim of verifying the hypotheses. For the verification of each hypothesis, material data, event data, and process data obtained from the DCS were input into the DPI. While viewing the results of the analysis, they participated in a waigaya discussion that looked at whether the analysis results supported verification of the hypothesis, and whether this matched actual conditions and agreed with their own perceptions. With its extensive analytical knowhow, Yokogawa supported this discussion.
During the waigaya, the participants gave their own interpretations of the visualized data based on their own knowledge of the process and engaged in a vigorous back and forth exchange of views. They also discussed what knowledge and skills should be handed down to young personnel. Through this waigaya, the participants engaged in further analysis of the data for doubtful points which newly emerged in the discussions and shared their ideas on whether this verified the hypotheses.
DPI screenshot
Session 3: Final verification of hypotheses and action planning
In the time leading up to this session, further analysis using DPI was carried out on site by Osaka Gas Chemicals, and progress was made in getting closer to identifying the true nature of the issue with the heating process. Held in December, the third session once again employed waigaya to narrow down the list of hypotheses and identify the key factors that caused this problem.
Result of hypothesis verification (o=supported, x=not supported)
Next, through waigaya, the participants discussed what practical improvements could be made in response to the identified factors, such as adding sensors and revising manuals to monitor particular process values and specifying what measures should be taken in response. The addition of new tags for the process control system and their monitoring were also proposed to facilitate predictive maintenance.
Session 4: Review of workshop activities for implementing actions
The fourth session was held in March, after a busy period of the year at this plant. In this session, the participants reviewed everything that had been done in the three previous sessions and engaged in a waigaya discussion of how the data should be utilized and what further improvements could be made. It was decided that the planned improvements based on DPI data analysis and the knowledge and expertise of the participants would be implemented after the workshop was concluded.
Post-workshop comments from the attendees:
"I'm glad we were able to learn how to reduce the occurrence of this problem from happening."
"We got good result to support our budget planning."
"It’s good to know that the data and discussions back up what I have used as a rule of thumb."
"Skilled staffs actively talked with us to share their technical knowledge."
Results
The hypothesis verification and action planning through waigaya had the following outcomes:
- Stabilization of the manufacturing process by controlling the problem
- Maximization of operational efficiency
- Cost reduction
- The sharing of know-how and passing down of techniques as organizational intelligence
- Establishment of the waigaya methodology and the attainment of the analytical skills needed for continuous improvement activities
- Improved communication across the organization
Following the conclusion of the workshop, the attendees continue to make use of waigaya to discuss other challenges.
Customer Satisfaction
Mr. Mori (manufacturing):
"When this problem with the heating process occurs, operator workload increases. Because this is a large facility, it takes a long time to correct this problem, and it affects the processes that precede and follow it. When I first heard about this analysis project, I wondered if it could really solve the problem. However, the two people from Yokogawa made waigaya enjoyable for us, and they were very serious about taking a good look at our plant operations. Although this was the first time for people from different departments to participate in such an improvement activity, it gave us an opportunity to discuss possible problem causes with each other and to corroborate their suspicions using data. While referring to our own rules of thumb, we clarified the root causes of the problem by verifying hypotheses. It was very good to know that we had been doing the right things. Even after concluding this workshop, all the people who were involved continue to take part in waigaya discussions."
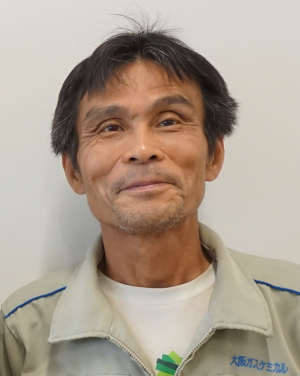
Mr. Kato (manufacturing management):
"I was in charge of analysis using the DPI tool. I had joined the company not long before being assigned to the project. At university I had gained some experience analyzing data using MS-Excel, but this was my first exposure to systematic data analysis. As our manufacturing processes have so many parameters and the operating conditions change frequently, data analysis by mere data comparison does not work. I listened to the rules of thumb that our veteran employees had come up with, and used them as a reference point for determining where to focus our analysis. I’m currently analyzing the same data from different viewpoints and focusing my attentions on raw materials. Discovering new hypotheses through analysis is very interesting to me. I report my findings to others in waigaya sessions. Before this project, I used to always work in the office and didn't have opportunities to learn about the manufacturing process. Through this project, I got a good understanding of these processes and learned the methodology for data analysis."
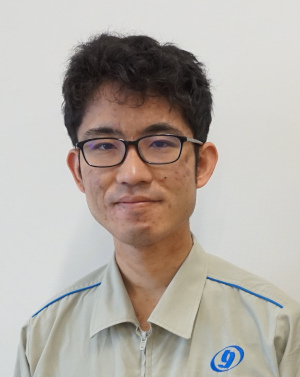
Mr. Okuda (senior technical advisor):
"Dating back to the launch of our carbon fiber business, I have been involved in manufacturing, manufacturing technology, and quality assurance. The manufacturing process for pitch-based carbon fibers involves a lot of know-how that is not widely known. While much of this is local knowhow, I have made an effort to pass on this knowledge to others by creating manuals and holding employee seminars. The factors identified by the project were originally thought to be not so important, but looking back on previous improvements made at our facility, we now understand the relationship that these factors had to this, and the effect that they have in improving productivity. Using data, we quantified the phenomena that were the main causes, and we shared this information with everyone. Waigaya was a very good way to pass on technical knowledge to others. I think our young people have learned a lot from these discussions, and I hope they will continue to think about these things and take on new challenges."
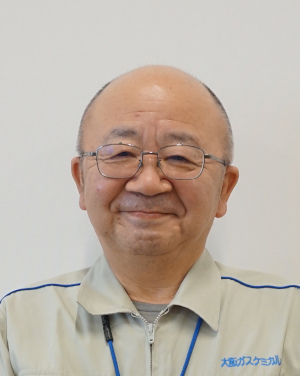
Mr. Takahashi (business development):
"As the executive organizer of an IoT project, I'm promoting the digitalization of in-house business operations, and am also in charge of sharing information about internal activities and projects throughout the company. I knew about the problem because I was once involved in manufacturing. There is a lot of data from the DCS and other sources, and I was wondering if we could figure out the cause by analyzing data. Also, as this was our first experience in carrying out such a challenging analysis project, I was a little concerned over whether we could carry it out on our own. However, working together with Yokogawa was a very good way to achieve our goal. The DPI workshop also had the aim of passing on techniques to the younger generation, and was a valuable opportunity for experienced employees to communicate with our younger employees. I think that backing up each person's insights with data is very meaningful. While our company is a material manufacturer, we will not be able to survive long term if we just manufacture materials. By using data to develop a good understanding of our products’ characteristics, we can develop new applications for existing products and new products and solutions. I believe that our company can be both a manufacturer and a service provider. I hope that we will be able to utilize data to come up with new ideas that will allow us to propose new solutions to our customers."
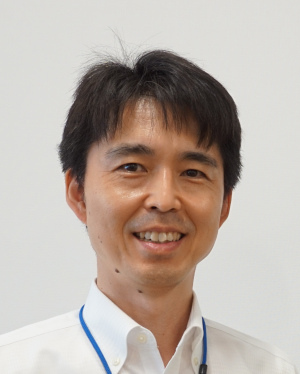
Mr. Yoshida (facility engineering, originator of this project):
"Initially, our people had introduced Yokogawa’s DPI tool so that we could solve these problems on our own. However, when I began to work with this software, I met some resistance from others because we lacked experience with data analysis and were not familiar with the use of this software. After researching case studies of other companies, I decided to follow the advice given by my boss and turned to Yokogawa for consulting assistance. The main reason for our selection of Yokogawa was their experience working with manufacturers, and their expertise in working with data. Yokogawa met our expectations by, for example, preparing topics in advance and bringing materials to facilitate our discussion. In the first session of the workshop, the participants were a bit passive to start, but the atmosphere immediately changed because they sensed that the two people from Yokogawa were trying to understand our manufacturing processes and solve our problem together with us. Through the waigaya, a lot of knowhow was passed on to others. Previously, there was no linkage between our data and process knowledge; by combining them, we were able to reason more objectively. This made it easier for us to get the funds necessary to make improvements.
After this workshop that Yokogawa facilitated, we all continue to conduct waigaya sessions and apply data analysis to new subjects. I have taken on the challenge of continuing and gaining broader acceptance of these activities. The ideal is to be a company that can easily generate profits, and the worst thing is to struggle and not make a profit. I'd like to keep conducting improvement activities that make use of waigaya, with the aim of eliminating muda (waste) and seeing our employees’ efforts generate profits."
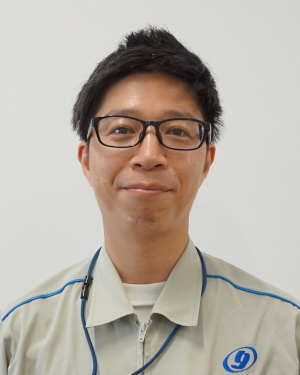
Mr. Fujiwara (general manager of the Torishima Plant):
"Countermeasures have been taken at the plant to correct the problem in the heating process, and a major facility improvement project carried out from 2013 to 2014 produced certain results. The factors identified in this analysis project had some relation to the improvements that had been made earlier. While we had a lot of data on the manufacturing process and wanted to make effective use of it to make further improvements, I honestly wondered if we could identify the actual problem causes at this stage. However, the participants in this analysis project were able to deliver great results that were highly appreciated by management, and our younger employees learned a lot. Mr. Kato acquired analytical skills and is currently working on new themes with the same workshop members, with the aim of improving productivity. There are many people at our plant who are making a positive contribution. I hope that they will continue to enjoy and show an interest in their work, and be willing to take on new challenges."
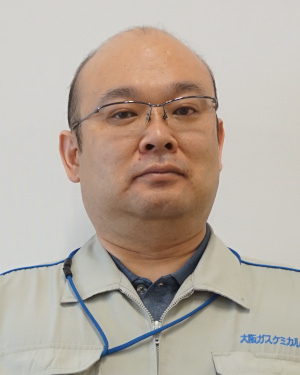
About Osaka Gas Chemicals Co., Ltd.
Osaka Gas Chemical Co., Ltd., a group company of Osaka Gas Co., Ltd., manufactures and sells a variety of unique chemical products, including coal pitch-based carbon fiber, Japan's top-selling Shirasagi brand of activated carbon, and fluorene derivatives, utilizing coal chemical technology that had originally been acquired when Osaka Gas produced city gas from coal.
Osaka Gas Chemicals' DONACARBO® carbon fiber is a unique short-fiber carbon fiber made by curling the coal tar pitch using its unique spinning technology. Its excellent heat insulation, sliding properties, electrical conductivity, and abrasion resistance make it suitable for use in a variety of applications, including insulation for industrial furnaces, and sound-absorbing insulation for railway vehicles.
Participants of the waigaya discussions
Related Industries
-
Chemical
Chemical plants rely on continuous and batch production processes, each posing different requirements for a control system. A continuous process calls for a robust and stable control system that will not fail and cause the shutdown of a production line, whereas the emphasis with a batch process is on having a control system that allows great flexibility in making adjustments to formulas, procedures, and the like. Both kinds of systems need to be managed in available quality history of product, and to be able to execute non-routine operations. With its extensive product portfolio, experienced systems engineers, and global sales and service network, Yokogawa has a solution for every plant process.
Related Products & Solutions
-
Process Data Analytics
Achieving consistent quality by detecting problems at an early stage