Visualization of Pump and Manifold Maintenance on Production Lines
Maintaining multiple long-distance production lines according to their condition is essential for safe operation. Production lines are made up of a wide range of different equipment, and measurement targets are highly varied. Under these circumstances, adding a new measuring instrument to equipment that has been in use for many years is not a simple task.
How can problems can be detected before they occur under circumstances where it is becoming increasingly difficult every year to recruit employees due to labor shortages?
Predictive maintenance, which can identify the signs of problems and defects in advance, is becoming prominent as a means of solving this difficult problem.
Aging Equipment and Personnel Shortages Threaten the Safety of Production Lines
DX (Digital transformation) has become a key concept in today’s society, and the trend toward innovation in operations using data and IT at manufacturing sites is accelerating. Looking at the circumstances of many companies, however, there are many issues that must be resolved before DX can be implemented such as the difficulty recruiting maintenance personnel due to chronic labor shortages, aging of equipment, and intensification of effects from the COVID-19 pandemic.
To overcome these issues, efforts are underway to automate equipment diagnostics and measurement work and replace the people who performed this work until now with digital devices. Circumstances have arisen where installation of new equipment is not progressing, however, because of difficulty adding new measuring instruments to older-model equipment that have been in operation for many years due to their specifications and the inability to secure installation space.
Centralized management of the measurement data for an entire production line is necessary, but it is not easy to integrate all of the measurement data on a single system. Also, production lines with a combination of both old and new equipment require separate management of the automated portions and the portions that rely on manual labor, and this is a factor that can impede efficiency improvements.
Companies are actively updating their equipment with the aim of implementing DX, but it is not feasible for them to update all equipment at the same time.
This means that companies with multiple long-distance production lines divide up their lines by area and update them in stages from the perspective of continuing operations without impairing productivity.
In such cases, the introduction of measuring instruments that can be easily added to existing equipment offers significant benefits.
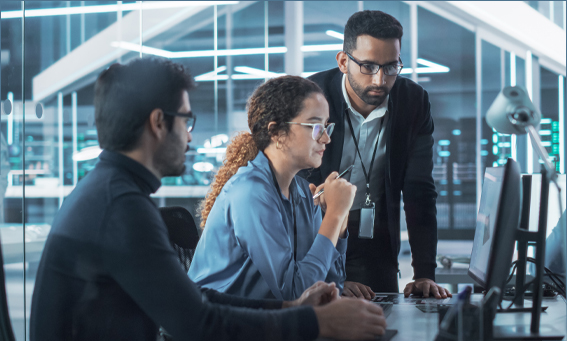
Automation and Labor-Saving in Maintenance and Management Are Keywords for Fundamental Reviews
We develop and propose a variety of solutions to solve these problems that our customers are facing.
Three examples regarding methods for detecting the signs of problems that can occur on production lines and achieving safe operation are presented below.
Example 1 : Customers want to inspect and replace production equipment at the optimal time
All production equipment progressively degrades as a result of long-term operation. To identify the signs of such degradation, it is important to establish measurement points at various locations on the equipment and to take high-speed, simultaneous measurements. Providing highly reliable data can reduce maintenance labor and loss of opportunity, making it possible to inspect and replace equipment at the optimal time.
Example 2 : Customers want to perform deterioration diagnosis, but there are no devices with the needed performance and size that can be installed on their current production equipment
In many instances, production equipment is structured so that there are no gaps or empty spaces, primarily from the perspective of saving space, and it is often difficult to incorporate new equipment, particularly with older-model equipment. It is desirable that measuring instruments be as small as possible, and therefore, we provide business card size products that can be installed in the gaps between existing equipment.
Example 3 : Customers want to prevent breakdowns of production equipment in noisy environments
It is difficult to obtain accurate measurement data in environments where noise is produced during operation, and as a result, there is a heightened risk of production equipment stoppages and breakdowns. Safe operation can be achieved by using insulation between input channels and enhancing noise resistance.
Introduction of the VZ20X Enables High-Precision Measurement and Monitoring Systems, Promotes Predictive Maintenance
The Multi-Remote I/O Analog Sensing Unit VZ20X is a high-speed, high-precision, high-durability, ultracompact unit that can perform multi- channel simultaneous measurement.
The measured analog input data is sent to a host system via Ethernet. Reliable sensing makes it possible to visualize the status of existing equipment that has not been digitalized and facilitates predictive maintenance and other such means by incorporating the IoT and AI to detect signs of degradation.
Specific effects are presented below.
One VZ20X unit can measure DC voltage, a standardized signal, a four-wire resistor, a thermocouple, and a three-wire/four-wire resistance temperature detector (RTD) on a maximum of eight channels with highspeed, 1 ms sampling, and simultaneous multi-channel measurement (up to 120 channels using 15 units) is possible. This makes the VZ20X ideal for remote monitoring of distributed production facilities. Since one unit can perform multi-channel measurements, there is no need to maintain inventories of different types. Also, the inputs are insulated from one another, so the VZ20X can be used with reassurance even in noisy environments.
In addition, multiple VZ20X units can be connected in a daisy chain to create an environment for centralized monitoring of multiple long production lines using GA10 data logging software. The compact and lightweight components can be installed near the measurement target with a minimal footprint. Gaining an accurate understanding of equipment status through accurate sensing contributes to reducing the risk of failure and to solving issues that customers are confronting, such as raising productivity and improving the efficiency of equipment maintenance.
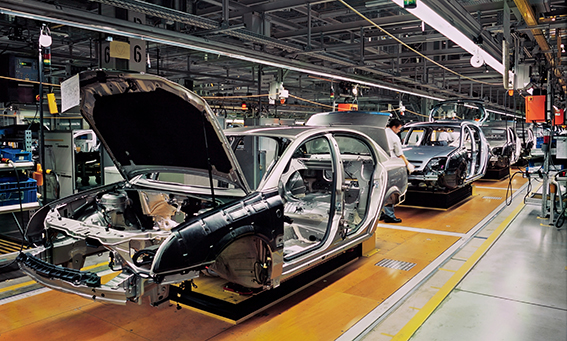
Achieving Both Labor-Saving and Safety on Difficult-to-Manage Long-Distance Production Lines
At manufacturing sites, production equipment stoppages and decreases in performance have a tremendous impact on work. One means of preventing such events from occurring is predictive maintenance, which is used to detect the signs of breakdown or failure in advance and perform maintenance at the optimal time. The VZ20X provides the basis for such predictive maintenance in the form of measurement data.
Updating equipment and eliminating labor shortages is not easy, but installing the VZ20X in locations on multiple long-distance production lines where detailed management and maintenance are difficult and creating a system for centralized management of the entire production facility are effective first steps for achieving predictive maintenance and DX.
Production information on the VZ20X Analog Sensing Unit can be found at the following site.
Looking for more information on our people, technology and solutions?
Contact UsGerelateerde producten & oplossingen
-
Analog Sensing Unit VZ20X
VZ20X is a data measuring device that helps achieve “predictive maintenance,” whereby performance degradation and failures in production equipment are prevented before they occur. Providing a solution for optimally timed equipment inspections and replacements, it addresses the issues of reduced uptime and safety caused by failures.