Cogeneration or combined heat and power (CHP) is an efficient approach to generating power and thermal energy from a single fuel source. Yokogawa contributes to efficient management through its products and solutions.
Challenges
Customer Challenge
Improving power plant efficiency
Solution
Yokogawa helps power plants operate more efficiently by improving the control of fuel, steam, and feed water.
Enabling Technologies
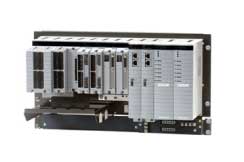
CENTUM VP Integrated Production Control System
The CENTUM VP integrated control system secures interruption-free “uptime only” plant performance for optimal productivity and profitability in the renewable energy field.
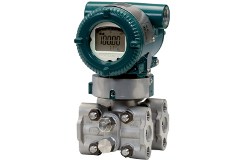
Transmitter
DPharp series digital pressure transmitters use a differential pressure high accuracy resonance pressure (DPharp) sensor that represents one of the most revolutionary advances in transmitter technology.
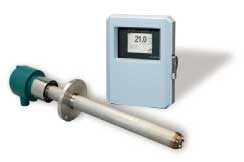
Zirconia Oxygen Analyzers
Yokogawa’s zirconia oxygen analyzers are used for combustion monitoring and control applications and are relied on by a wide range of industries to optimize combustion and reduce NOX emissions.
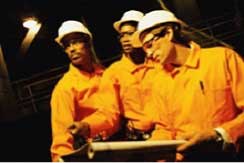
Plant Service
Commissioning, operator training, operation, maintenance, and simulation services
Customer Challenge
Safely and efficiently starting up boilers, a complicated process that requires considerable skill
Solution
Yokogawa systems make startups safer and more efficient by automating processes such as heating with fuel oil and switching over to biomass fuel. Graphic displays give operators a real-time window into the status of each process.
Enabling Technologies
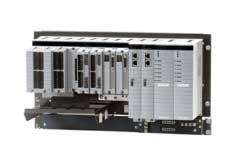
CENTUM VP Integrated Production Control System
The CENTUM VP integrated control system secures interruption-free “uptime only” plant performance for optimal productivity and profitability in the renewable energy field.
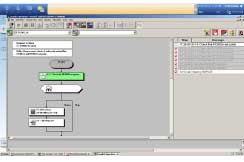
Exapilot Operation Efficiency Improvement Package
The FAST/TOOLS package optimizes performance for renewable energy applications. It ensures high availability and performance and supports online configuration.
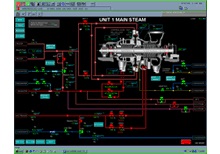
Simulator
High Fidelity, Full-replica Training Simulators
Customer Challenge
Improving combustion efficiency and reducing/eliminating harmful stack emissions
Solution
Yokogawa oxygen analyzers measure the oxygen (O2) concentration in flue gas. With this information, the air-fuel ratio can be adjusted to optimize combustion. Likewise, our stack gas analyzers can be used to reduce harmful emissions by measuring the concentrations of nitrogen oxide (NOX) and sulfur oxide (SOX) in stack gas.
Enabling Technologies
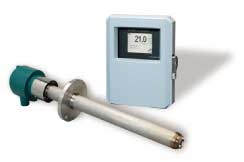
ZR Series Zirconia Oxygen Analyzers
Yokogawa’s zirconia oxygen analyzers are used for combustion monitoring and control applications and are relied on by a wide range of industries to optimize combustion and reduce NOX emissions.
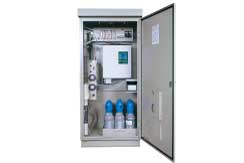
SG Stack Gas Analyzer
The SG stack gas analyzer consists of an infrared gas analyzer unit, a zirconia oxygen analyzer unit, and a sampling unit, and can simultaneously measure up to five components: NOX, SO2, CO2, CO, and O2.
Customer Challenge
Reducing the emission of CO, NOX, dioxins, and other substances into the atmosphere by burning off residual gas components in the stack gas
Solution
Yokogawa gas analyzers measure the oxygen concentration in the stack gas so that adjustments can be made in the O2 supply that will improve combustion efficiency and burn off more residual gas components.
Enabling Technologies
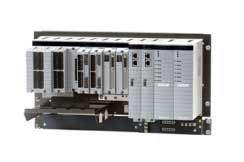
CENTUM VP Integrated Production Control System
The CENTUM VP integrated control system secures interruption-free “uptime only” plant performance for optimal productivity and profitability in the renewable energy field.
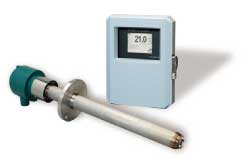
ZR Series Zirconia Oxygen Analyzers
Yokogawa’s zirconia oxygen analyzers are used for combustion monitoring and control applications and are relied on by a wide range of industries to optimize combustion and reduce NOX emissions.
TDLS Laser Gas Analyzer
The TDLS gas analyzer relies on a proprietary peak area integration method and is ideal for in-situ analysis in harsh process environments. It significantly improves the efficiency of boiler operations.
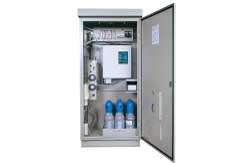
SG Stack Gas Analyzer
The SG stack gas analyzer consists of an infrared gas analyzer unit, a zirconia oxygen analyzer unit, and a sampling unit, and can simultaneously measure up to five components: NOX, SO2, CO2, CO, and O2.
Customer Challenge
Prevent fire accident in coal yard, transmission, and any other facilities
Solution
Distributed Temperature Sensor (DTS) provided by Yokogawa contributes fire detection, Leak/Plugging Detection, Hot (Cold) Spot Monitoring, and Facilities Preventive Maintenance.
Enabling Technologies
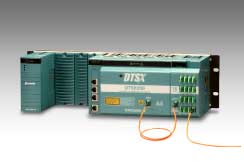
Distributed Temperature Sensor (DTS)
Yokogawa DTSX makes possible gapless detection and monitoring up to 50km.
Resources
- Power supply made dramatically reliable thanks to CENTUM CS 3000 with seven-nines availability
- Visualization of almost all plant data on the same HMI by linking up subsystems via Modbus
- Improved plant performance
- Reduced cabling costs by using a commodity GPRS network infrastructure
- Additional reduction in system cost by making full use of existing components
- Reduction in cost of software by using all web-based technology
- Long-term service contract — no need to worry about a suspension of maintenance services
- Monitoring and control of the entire cogeneration plant including the two once-through steam generators
- Reliable and cost-effective power supply
- Operator-friendly HMI
Nishi Nippon Environment Energy Co., Inc. was founded in 1990 with the concept of a full, safe and comfortable urban life by harmonizing the global environment with energy-savings. Also, as a total energy industry corporation, which is promoting the efficient use of heat energy for the region, it is developing a broad business on the theme of civic improvement in the 21st century by preparing a stable city infrastructure.
- All correct operation procedures are carefully configured in the CENTUM CS 3000 and smoothly in operation
- CENTUM CS 3000 ensures stable supply of electricity and steam to Bangkok's Suvarnabhumi airport
- Yokogawa provided digital transformation solution to TP Utilities power plant under Co-innovation program.
- Operation Management solution digitized shift handover and knowledge base for safe and efficient operations.
- Steady boiler control by CENTUM CS 3000 with dual redundant CPUs and seven 9s availability
- Total plant information integrated into supervisory information system via OPC interface
- Reduced water, coal and other resource consumption
Seawater leak detection is the post-condensation water quality management processes. Damage to the ion exchange resin, which deionizes the supplied water, is also monitored during this process, and both of these applications are executed by a conductivity analyzer. (AN10D01P01-01E)
In general, refineries exhibit a very good potential for real time monitoring and optimization using Visual MESA Energy Management System.
Based on our extensive experience, overall benefit in the range of 2% to 5% of the total energy cost can be achieved. Expected project payback is always less than one year.
Industrial facilities where power and steam is produced (i.e., Cogeneration) exhibit a very good potential for real time monitoring and optimization using Visual MESA Energy Management System.
Based on our extensive experience, overall benefit in the range of 2% to 5% of the total energy cost can be achieved. Expected project payback is always less than one year.
Visual MESA was successfully applied to many industrial facilities worldwide, several of them operating steam and power generation networks of different complexity and capacity but all with energy cost savings.
Looking for more information on our people, technology and solutions?
Contact Us