Whether you produce petrochemicals, inorganics or intermediates, chemical companies are under cost and margin pressures to deliver products in a timely and efficient manner while maintaining safe and compliant operations. Additionally, chemical companies need to adjust to fluctuating feedstock and energy prices and to provide the most profitable product mix to the market.
Yokogawa has been serving the automation needs of the bulk chemical market globally and is the recognized leader in this market. With products, solutions, and industry expertise, Yokogawa understands your market and production needs and will work with you to provide a reliable, and cost effective solution through the lifecycle of your plant.
Details
Optimizing Production Planning
Yokogawa has the tools and rich experience to build control and instrumentation solutions offering tangible benefits for petrochemical companies.
Challenges
Fluctuations in raw material prices and product supply and demand make it absolutely essential to optimize production planning.
Our Solutions
Yokogawa offers a production management system that bridges the gap between planning and manufacturing for optimal scheduling of petrochemical processes.
Products & Solutions
|
Real-time Production Organizer™ : RPO
Real-time Production Organizer™ (RPO) is a suite of platform applications developed specifically to bridge the gap between production planning and process control, providing a fully integrated business to process (B2P) production environment.
Staying Globally Competitive
Yokogawa has the tools and rich experience to build control and instrumentation solutions offering tangible benefits for petrochemical companies.
Challenges
To stay competitive in the global market, the optimization of processes throughout a plant is no less necessary than the development of a competitive product offering that meets specific user needs.
Our Solutions
Yokogawa provides plantwide automation solutions that enable the agile and flexible control of petrochemical production workflows and are fully integrated with a safety instrumented system.
Product & Solutions
![]() |
The CENTUM VP integrated control system secures interruption-free "uptime only" plant performance for optimal productivity and profitability.
![]() |
The ProSafe-RS safety instrumented system enables truly integrated solutions while delivering the high availability required for safety integrity level 1-4 (SIL1-4) applications.
![]() |
vigilantplant services.® is a suite of comprehensive services that realize Yokogawa's VigilantPlant concept, helping manufacturers achieve safe, reliable, environmentally friendly, and profitable plant operations.
Saving Energy and Reducing Greenhouse Gas Emissions
Challenges
Petrochemical plants consume enormous amounts of energy, so energy saving initiatives at these facilities can go a long way to achieving cost competitiveness and reducing the CO2 emissions that contribute to global warming. One key means by which this can be accomplished is optimizing control of the production process.
Our Solutions
Yokogawa's advanced process control systems make it possible for plants to operate with increased efficiency, thereby reducing energy consumption and CO2 emissions.
Products & Solutions
![]() |
Integrated, validated and timely operational information supporting continuous improvement initiatives and optimization of production performance.
![]() |
Customers face major challenges in achieving efficient plant operations that involve managing quality, cost, delivery time, and environment (QCDE), which are essential elements for improving productivity and profitability. Yokogawa provides real solutions to these challenges based on the VigilantPlant vision for a sustainable future.
Reliability and Maintainability
Reliability is in Our DNA
All automation suppliers take system reliability - a key factor for petrochemical plant availability - seriously. However, none matches Yokogawa in its extreme commitment. At the heart of all of the Company's systems is the unique "Pair and Spare" controller architecture, consisting of a redundant set of CPU modules that, in turn, each contains two micro processors. The two micro processors constantly compare each other's outputs, initiating a bump-less switchover if any mismatch is detected.
The actual availability track record of Yokogawa CENTUM VP distributed control system (DCS) reaches 99.99999% (seven 9s).
CENTUM VP : "Pair and Spare" Architecture
Yokogawa's safety instrumented system, ProSafe-RS, is the world's first, truly integrated safety instrumented system. Its integrated architecture with the production control system enables unified monitoring and an operation environment for the operator. TÜV Rheinland (TÜV), a German certification organization, has certified ProSafe-RS to be compliant to both IEC 61508 and IEC 61511 international standards. Additionally, TÜV has approved its use in Safety Integrity Level 3 (SIL3)*1 applications, such as emergency shutdown (ESD), fire and gas (F&G) and boiler management (BMS). This latest certification of IEC 61508 and IEC 61511 compliance attests to the high level of Yokogawa's technology and the quality of its safety instrumented system.
(*1) To be certified for SIL3, safety systems must be tested by a third party for a risk factor that Measures less than 1/10,000.
ProSafe-RS : SIL3 TÜV Certificate
Improving Maintainability by Diagnostic Technologies
By taking advantage of FOUNDATION fieldbus™, or HART connections with the field devices, Yokogawa's asset management system greatly improves device maintainability that reduces maintenance costs. Now maintenance staff can gain access to field device information anywhere anytime. The system enables staff to set and modify field device parameters, and to check detailed device alarm information. Standard audit trail management allows the tracking of changes to device information.
PRM : PRM System Configuration
Device Diagnosis
With the introduction of FOUNDATION fieldbus technology and compatibility with HART, the results of field device self-diagnoses can be accurately reflected in DCS control operations. Examples of self-diagnostics include:
Valve positioner
- Signature diagnosis
- Valve stick-slip diagnosis
Differential pressure / pressure transmitter
- Clogging diagnosis
- Orifice wearing diagnosis
- Diaphragm corrosion diagnosis
Temperature transmitter
- Temperature element diagnosis
Vortex flowmeter
- Clogging diagnosis
- Vibration diagnosis
For even greater maintenance efficiency based on predictive maintenance, the system also provides advanced diagnostic functions. With these functions, staff can define and perform diagnostics using information from multiple devices or higher level process-dependent diagnostics. Advanced diagnosis examples include:
Differential pressure / pressure transmitter
Valve positioner
Temperature transmitter
|
![]() |
Yokogawa's innovative asset management system provides all the functionality necessary for efficient maintenance of your field devices.
Plant-wide Automation
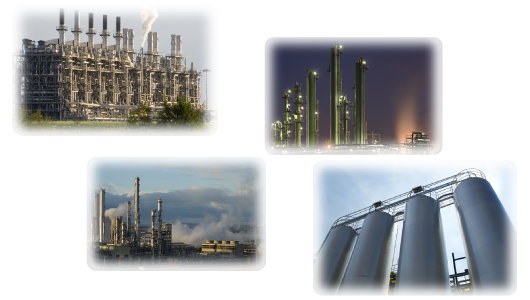
Products & Solutions
Field Instruments
|
|
Environmental & Analytical Instruments Gas Analyzers
Liquid Analyzers
|
|
Harsh - Environment CCTV
|
|
Production Control System
|
|
Safety Instrumented System
|
|
Production Management Solutions
|
|
Advanced Process Control & Optimization Systems
|
|
Asset Management System
|
|
Alarm Management System
|
|
Resources
- Smooth migration to CENTUM CS 3000 at production facility.
- While the pellet transfer section previously relied on customized software, it now uses the CS Batch 3000 package.
- All logistics of raw materials, intermediate products and final products are controlled and managed by MAS.
- MAS enables Operational Excellence with its seamless interface to enterprise resource planning system.
- 16,000 FOUNDATION Fieldbus devices
- Main Automation Contractor (MAC)
- DCS anywhere concept integration with site SAP system
- Long term maintenance contract
- Sustainable development
- Implementation of multivariable optimizing controllers and robust quality estimators within a record short period
- 3% rise expected in CCR feed amount
- ABS plant migrates from CENTUM XL to integrated CENTUM CS 3000 solution.
- CENTUM CS 3000 Integrated Production Control System together with CCTV equipment, a plant information management system (PIMS), the Exaplog Event Analysis Package, and the CS Batch 3000 package.
- Smooth upgrade for fully redundant system and advanced information technology
- Stable and high-quality sulfonate production around the clock
- Stable operation and proactive maintenance were realized at new coal-chemical plant in China.
- Yokogawa engineers ensured a successful and efficient commissioning and startup.
- Meet the IEC 61508/JIS C 0508 functional safety standards
- Proactively introduce leading edge technologies
- Accommodate the plant licensors' safety, reliability, and maintainability requirements
- Improve the monitoring and operation functions of the emergency shutdown system
Operators must receive diagnostic information before a line block leads to a malfunction. Yokogawa provides predictive diagnostics based on trend analysis of the blocking factor, which improves maintenance efficiency and reduces maintenance costs.
If a sensor is not operating, the manufacturer cannot detect moisture in the chlorine and must stop the process. Unfortunately, sensors can deteriorate and deliver inaccurate measurements due to contact with the process.
Automated control of industrial boilers is an excellent application for YS1700 microprocessor-based loop controllers. These instruments can be programmed to perform the operations of plant master, boiler master, fuel and air control with oxygen trim and drum level/feedwater control.
Many different types of gases are consumed in industries as varied as chemicals, food & beverages, and medical. These gases are normally delivered in liquid form by trucks and dispensed at the customer site. Although the flow volume of cryogenic liquefied gas is used for billing purposes, it is not easy to accurately measure this because the gas is always at saturation temperatures.
The GX20 and GX90UT offer an average value computation function making it ideal for controlling temperature and other fluctuating phenomena. The operating status can be controlled in real time, providing operating cost reductions.
Download this eBook and learn:
- The top challenges that drive reinstrumentation
- How to plan for and achieve a successful project
- Best practices in identifying your project scope
- 5 ways to improve operator effectiveness
- Different scenarios and best practices for updating, migrating or replacing process controls, safety systems, and instrumentation in plants
Process automation end users are under more pressure than ever to do more with less. The current economic climate means that many automation capital projects are on hold. With capital budgets tighter than ever, users instead focus on operational budgets (where cost cutting is also a key concern), or on automation investments with a very rapid return on investment.
Yokogawa has come a long way in making its message clear to the world of process automation. Last year, the company embarked on a full-scale global marketing campaign to make customers aware of the company's focus on system reliability, security, dependability, and robustness. Dubbed "Vigilance", the campaign created a unified message for the company and greatly helped expand awareness of the Yokogawa brand and corporate philosophy.
The automation suppliers that will be successful in the long term will be those that effectively address application or industry specific problems for end users with a value proposition that cannot be ignored. These problems exist throughout the process industries today, and they won't be solved by simply offering a product, but through a combination of hardware, software, services, application expertise, and knowledge.
In today's dynamic industrial marketplace, the only constant is change. Raw material costs, energy costs, market demands, environmental and safety regulations, technology, and even the nature of the labor force itself are constantly changing, and not always in predictable directions.
From engineering to installation, commissioning, operations, and maintenance, FOUNDATION fieldbus offer significant cost reductions of 30 percent or more versus conventional analog systems. Many of these cost reductions come from the advanced functions that fieldbus offers versus analog technology.
The world of process automation is governed by procedures. While we like to refer to the process industries as being largely "continuous", this could not be further from the truth. Process manufacturing is constantly in flux.
The worlds of process automation and production management have been converging for some time. What once used to be islands of automation and production management functionality connected through highly proprietary integration schemes that were costly to maintain have developed into integrated platforms that provide seamless data exchange between the world of automation and the plant floor, the functions of production and operations management, and integration with business level systems.
The energy systems, the steps for the implementation of Visual MESA and several features of the model are described in this article, with a focus on the use of the software for the calculation of energy-related KPIs. The EMS implementation project is discussed and the main conclusions relative to the reduction in operating costs are also presented.
Experiences gained during more than 20 years of industrial projects deployed worldwide are commented. Main project steps are explained and critical details to be taken into account to assure successful use and proper technology transfer are presented. Specific case studies will be discussed in the paper. Open loop vs Closed loop implementation is also presented.
This white paper provides an overview of how Yokogawa believes its customers can best prepare for and position themselves to benefit from IIoT-enabled technology and solutions and digitalization in general to emerge as the successful connected industrial enterprises of the future.
Yokogawa’s industrial automation (IA) product and service offerings, industry domain knowledge, and VigilantPlant approach – which emphasizes safe, secure, and uninterrupted operations -- provide a solid foundation for an Industrial Internet of Things that specifically addresses the requirements of process automation, particularly for the OT side of the equation. To be able to provide an equally solid foundation for the IT side, Yokogawa is partnering with Cisco Systems and other industry leaders.
Vortex flow meters utilize a fluid phenomenon in which frequencies of Karman vortex streets released from a shedder bar inserted in a flow are proportional to flow velocities.
As the world's societies become more connected, market competition is becoming more ruthless and transactions are performed at ever increasing speeds. Deregulation has ignited global competition throughout the world. The proliferation of Information and Internet technologies have accelerated the growth of global competition, with life cycles for high tech products having lives measured in "dog years" (in each normal year they advance seven years).
Recently, there is an increasing demand for operation and monitoring of all the various controllers distributed in the field on the same screens to improve plant operation efficiency. The purpose of the Unified Gateway Station (UGS) is to connect external controllers, such as the STARDOM's FCN/FCJ autonomous controllers and other vendors' controllers, to the CENTUM VP integrated production control system and to operate and monitor those external controllers on the Human Interface Station (HIS) screens, the operation and monitoring screens for the CENTUM VP.
Exaopc provides interfaces compliant with each of the DA, A&E and HDA specifications laid down by the OPC Foundation. Ever since Exaopc was put on the market in 1999, it has been used by many OPC client programs including Plant Information Management System (PIMS), advanced operation support packages and advanced control packages as a common interface for looking up process data.
As international price competition becomes increasingly fierce, high value-added, high-efficiency production is essential for the survival of production plants in the oil refining, chemical and other industries. On the other hand, if plant equipment, which is the foundation of these production industries fails, business opportunities will be lost due to loss of yield, environmental destruction, and weakened financial strength due to social compensation.
The first stage in creating next-generation production control system that achieves innovative plant operation is providing "Visualized operation". "Visualized operation" for the customer means that he can reliably access and visualize plant data regardless of plant location and time.
The manufacturing industry has grown based on solid production technologies for creating quality products. However, the economic environment is changing dramatically, forcing manufacturing firms to face tough global competition; firms must ship the right products at the right time as the market requests.
CENTUM VP is a next-generation Integrated Production Control System which provides solutions to improve operation efficiency (Operational Excellence) based on Yokogawa's VigilantPlant concept. In the development of Integrated Production Control Systems, we have expanded the functions of the Human Machine Interface (HMI) maintaining the main essence of CENTUM series, regardless of the changes of platforms.
To date, Yokogawa has focused on DCS (Distributed Control System) which control the entire power generation plant, including boilers, in the electric power industry. In contrast, turbomachinery control has been handled by turbine manufacturers, but as the electric power market has been active internationally, especially in China and India, in recent years, Yokogawa has been developing turbomachinery control systems to to further develop the electric power industry.
The rapid evolution of information technology (IT) has made possible the transmission of a wide range of information in a short period of time, resulting in the transformation of society in aspects such as logistics and business styles. During this transformation, quick assessment of the circumstances and prompt actions were also required in the production lines, making real-time collection of field information indispensable.
Vortex flow meters have been appreciated by users as volume flow meters, which can, in principle, be applied to any flow measurement of liquid, gas, or steam. Volume flow measurement is enough for substances with small variations in density such as liquid.
The environment surrounding the process plant industry has changed dramatically because of the recent economic changes, deregulation, and increasingly fierce competition among global companies. Users are strongly requesting instrumentation equipment vendors to reduce total cost throughout the life cycle and help improve the efficiency of plant operation.
Combustion furnaces such as heating furnaces and boilers in plants include various sizes and types, and serve as energy sources, that is, they are cores in all production activities. Because a large amount of fuel such as gas or fuel oil is consumed in plants, their combustion efficiency directly affects the performance and running cost of the plants.
A laser gas analyzer employing the tunable diode laser absorption spectroscopy (TDLAS) method has a feature capable of measuring the concentration of the sample gas with high selectivity for gas components and without contact only by irradiating the gas sample with light from a tunable diode laser. Thus fast and accurate in-situ measurements can be performed in process lines under various measurement conditions.
The manuals of control systems such as a DCS provide a vast amount of information depending on their multi-functionality and functional integration. A conventional large-scale control system our company offers comes with more than 10,000 pages of paper documents.
A fieldbus is a bidirectional, multidrop, digital communication system developed to replace the conventional 4-20 mA communication lines that connect intelligent field devices with a control system. Fieldbus is continually reviewed in an effort to standardize the fieldbus specifications to comply with the specifications of the IEC and ISA.1
To improve efficiency and quality in the DCS application coding and inspection phases for an entire CENTUM CS system, engineering tools have been developed, along with the training required to operate these tools. In consideration of the time needed for development, the need for adequate operability, the basis of standard CS software architecture, and the use of freeware (e.g., Perl2 and Tcl/Tk3), we began development of these engineering tools with the objectives to reduce development costs and increase efficiency.
The development of communications technologies has formed a system structure known as the communication network. This network has not only established itself in the industrial world but also in the general household. The recent spread of technologies such as the Internet has been quite spectacular.
A communication system for connecting stations in the system plays an important role in a distributed control system (DCS). The communication system determines the superiority or inferiority of the entire control system. In DCS communication as represented by CENTUM, a token-passing system and dual bus have been developed.
It goes without saying that the reduction of the total cost of ownership (TCO) for various facilities and equipment is an important objective for most enterprises, and distributed control systems (DCSs) are no exception.
As controlled objects have become more complex, plant operation schemes more concentrated, and plant operators fewer in number, the degree of engineering for a distributed control system (DCS) has both multiplied and diversified. Despite this, systems are required to be configured in a shorter time while engineering results are required to be of higher quality.
Recently, manufacturing industries are trying to slash the total cost of ownership (TCO). Batch processes are not exceptions. Until recently, in comparison to continuous processes, batch processes have generally not yet undergone systematization and standardization.
As industrial plant systems have increased in scale and their automatic control algorithms advanced, today's operators are required to have more advanced skills and knowledge of theplant systems and to learn the actions to be taken in response to any possible situations including emergencies.
The trend of open system architecture is becoming an important issue with distributed control systems (hereinafter abbreviated as DCSs). To meet this demand, the operation and monitoring functions, and the system generation functions of the CENTUM CS 3000 system are designed to support Windows NT and OLE for Process Control (OPC).
The number of work steps involved in engineering a batch process tends to become extremely large compared to continuously controlled processes, if the work is automated using a DCS. This is due to the nature of batch processes and the plants that handle these processes.
Yokogawa Electric has been using Pair & Spare method as a reliability-enhancing technology for its line of distributed control systems (DCS) since the release of the CENTUM CS in 1993. As a result, the system has achieved an availability factor of seven 9's (99.99999%) for the record of operation to date.
As more fieldbus devices are made practicable, demand is increasing for a distributed control system (DCS) which integrates fieldbus devices in its engineering, operation, and monitoring environments. Conventionally, control has been implemented by the dual-redundant CPUs and control bus within a DCS; however, sufficient reliability must be ensured even when it is distributed over field networks.
The recent increase of devices enabled for a field network such as the FOUNDATION™ Fieldbus is phenomenal. This has been amplifying a requirement for distributed control systems (DCSs) to be capable of constituting a more pliant and efficient production control system by means of flexible connections to field networks in addition to traditional 4 to 20 mA signals.
In order to run 24 hours a day in large-scale plants, such as an oil-refinery or others, a distributed control station (DCS) requires high reliability. In the CENTUM DCS from Yokogawa Electric Corporation, high reliability of each device and a network (bus) connecting devices have been realized by using techniques such as a dual CPU, dual I/O, and a dual communication bus since sales began in 1975.
FCSs, the control stations in a CENTUM CS system, have already demonstrated that they are highly reliable, effective and maintainable. These advantages are the result of such features as the dual-redundant hardware configuration, the online modification of application data, and so on.
The environment surrounding process control systems has changed dramatically as the performance of personal computers improves and the Windows operating system advances, there has been a move towards the trend of open architecture. As we are already aware, in addition to the traditional high reliability level and the unique operability there has been an increase in demand for the interoperability of human- machine interfaces (HMI), which are responsible for the operation and monitoring of our distributed control system (DCS).
Report functions in process control are often positioned as part of the logger functions. However, plant operation data in a batch process should be not only logged regularly but also acquired and managed for each batch execution. The report function for logging plant operations in a batch process mainly comprises a function to print out plant operation data collected for each batch execution, and there are various approaches available to implement this function.
Since their conception in 1975, distributed control systems (hereinafter, referred to as DCSs) have been changed drastically in accordance with the rapid advancements in computer technology. In terms of hardware technology, the development of microprocessors, memory devices, and communication devices has been significant in regard to both quality and quantity.
Drastic changes in the economy of manufacturing industries, has led to increasing demand for plant operations to reduce personnel, improve efficiency, and increase the operation rate of facilities. On the other hand, for plants to operate safely, improvements in reliability and operational safety cannot be neglected.
In this day and age, just simply buying a personal computer, taking it home and turning it on will enable you to be taken to the world of Internet. In such an era, communication connection capability and prospects is increasing in importance. DCSs are no exception for concern.
For a transfer system in a plant, such as a transfer between tanks in a brewery, the transfer of pellets in a pneumatic transport system, or the transfer of oil at an offsite location, it is necessary to monitor the open/close status of valves or the on/off status of motors or blowers in reference to the transfer pattern (a combination of the transfer source(s) and destination(s), route, etc.).
Remarkable progress in information technology has led to open architecture systems and networking in the manufacturing industry. In such industry, remote monitoring systems based on public communication lines or the Internet, and or collaboration of control, information, and corporate systems based on standardized interfaces such as OLE for Process Control (OPC) are now widely used via networks.
There is growing recognition of the importance of preventing serious accidents in the process control field in view of the potential scale of impact on society. The IEC 61508 and IEC 61511 international standards call for the reduction of risk using safety instrumented systems (SIS) as well as the configuration of multiple protective layers in a process control system in order to prevent major accidents.
There are already safety systems on the market that have achieved safety integrity level SIL3 of the functional safety standard, IEC61508. However, most of them have achieved SIL3 by conversion of modules into dual-redundant or triplex form.
In recent years it has become increasingly common for plants to be provided not only with the control layer of a production control system (DCS, etc.), but also with the protection layer of a safety instrumented system (SIS) to reduce the risk of industrial accidents. The safety instrumented system is indispensable for avoiding risks to a plant failure.
The CENTUM CS 3000, a reliable distributed production control system, has been introduced worldwide with the objective of operating plants efficiently 24 hours a day, every day. The CS 3000 handles abnormal conditions in a plant appropriately and minimizes the chance of them developing into faults.
Process automation involves both operation and maintenance. Plant operation and monitoring are mainly conducted by a control system such as CENTUM, while equipment maintenance is handled by Plant Asset Management (PAM) such as Plant Resource Manager (PRM).
Asset Excellence (AE) provides a set of solutions for maintaining a plant in good condition at reasonable cost to ensure that it works as a production infrastructure. To reduce maintenance costs without causing a risk to production, it is necessary to change from breakdown maintenance to predictive or preventive maintenance.
The Coriolis flow meter has many features such as direct measurement of mass flow and measurement of fluid density, which other flow meters do not support. Therefore, since being introduced for practical use in the late 1970s, its market has rapidly expanded in many industries such as oil, chemicals, and foods.
For large scale geographically dispersed projects, there may be a hierarchy of individual Process Automation systems, which in turn are each responsible for a specific region, and are managed by a higher level system. Engineering of systems on this scale is a huge challenge, because each individual system has its own database and its own configuration.
One solution packaged for production control systems today is a system comprising a PLC and SCADA (Supervisory Control and Data Acquisition) software that runs on a PC. An advantage of these systems is that they can be configured at considerably lower cost than systems that use dedicated devices as they use commercially available PCs.
The engineering phase holds the largest ratios in control system configuration in terms of both time and money, so improving engineering efficiency is one of the biggest issues when it comes to system integration. In the STARDOM, Application Portfolios (APPF) are devised to dramatically slash engineering costs and increase software reliability.
We have developed the FCN (field control node) and FCJ (field control junction) autonomous controllers as the core of STARDOM, a solution that actualizes a network-based control system (NCS) Yokogawa proposes for increased production efficiency.
Field instruments are expected to be equipped with diagnostic functions to predict abnormal process conditions, and are also expected to expand these functions. The ability to extract diagnostic information for prediction and prevention from various physical process quantities measured by devices and make it available allows the user to reduce non-essential and non-urgent maintenance and thus cut maintenance costs.
Safe plant operation has long been pursued in all industries. Specifically, in the process automation industry which involves many hazardous elements, safety measures including explosion-protected systems have been adopted based on numerous tragic experiences.
When evaluating mass flow rates using a primary device such as an orifice or nozzle in a differential pressure flow meter in order to make fluid density compensations, the upstream pressure (static pressure) and fluid temperature are measured in addition to the output of a regular differential pressure transmitter.
Since the release of the DPharp EJ series in 1991 and the DPharp EJA series in 1994, nearly 1.2 million of these transmitters have been operating all over the world. Recently, we have also developed the EJX series of even more compact, lightweight and advanced transmitters with multi- sensing capabilities built using silicon resonant sensor technology.
In recent years, more field wireless devices have been used in hazardous areas. Meanwhile, in plants that are usually recognized as hazardous areas, there are numerous metallic tanks and pipes that easily shield or reflect radio waves, as discussed later, thus resulting in a poor environment for wireless communication.
In 1988, Yokogawa launched the ADMAG series of magnetic flow meters with increased resistance to fluid noise and zero stability, employing dual frequency excitation which was developed based on its long-cultivated technology for flow measurement. Since then, the ADMAG family has augmented its application range with such models as explosion-proof and integral types, and a capacitance type.
Yokogawa has formed an alliance with Shell Global Solutions International B.V. (SGSI) for advanced process control and has been jointly developing related products since then. As part of this collaborative work, we commercialized the Exasmoc multivariable model predictive control package and the Exarqe robust quality estimator package in 2000, which are used to control DCS and PLC systems based on SGSI's multivariable predictive control and quality estimation algorithms—namely, SMOC (Shell Multivariable Optimizing Controller) and RQE (Robust Quality Estimator).
Improved plant operation efficiency and reduced maintenance costs based on appropriate predictive maintenance are the common objectives that need to be achieved in every manufacturing domain. Exaquantum is positioned above the Process Control System (PCS) layer and gathers and stores huge volumes of process and laboratory data over long terms.
FieldMate application software runs mainly on a notebook PC and is a key component epitomizing Yokogawa's asset excellence (AE) concept together with Plant Resource Manager (PRM). FieldMate is available in basic and advanced versions. The basic version enables parameter setting and adjustment as well as status check of a field device by directly connecting a FieldMate-installed PC to a Highway Addressable Remote Transducer (HART) device or FOUNDATION™ fieldbus H1 device.
FieldMate is field device adjustment and configuration software applying Electric Device Description Language (EDDL) and Field Device Tool/Device Type Manager (FDT/ DTM) technologies. The FDT/DTM is being standardized and disseminated by the FDT Group, a nonprofit organization. Yokogawa is also aggressively participating in those activities.
The FieldMate versatile device management wizard is PC software mainly used for configuring and adjusting field devices. Under the concept of "one tool for all," Yokogawa has been enhancing this software to support a wide range of field devices and field communication protocols.
One of Yokogawa's corporate philosophies is to contribute to society through broad-ranging activities in the areas of measurement, control, and information. To achieve this philosophy in the control industry, Yokogawa launched CENTUM, the world's first distributed control system (DCS), in 1975.
Progress in digital signal processing and network technologies has enabled advanced functions which cannot be achieved by traditional field devices with 4-20 mA signal, to be implemented on field devices. Standardization of international fieldbus specifications, notably the FOUNDATION™ Fieldbus, has enabled users to build optimum field networks comprised of freely chosen field devices from various device vendors.
The operating principle of the vortex flow meters YEWFLO series, which first became commercially available in 1979, is based on the phenomenon in which the frequency of a Kàrmàn vortex train that occurs from a vortex shedder placed in a fluid flow, is proportional to the speed of that flow.
There has been increasing demand for cost reductions and lower-priced products in the manufacturing industry, and maintaining cost competitiveness and achieving optimum costs have become necessary for the survival of manufacturers. This calls for minimizing TCO (Total Cost of Ownership) over the whole life cycle of plants and maximizing TVO (Total Value of Ownership).
As compared to Distributed Control Systems (DCS) such as CENTUM VP that monitors the operations of the overall plant, PRM is a type of Plant Asset Management (PAM) software package that primarily focuses on the maintenance of devices and instruments.
Yokogawa Electric Corporation promotes the standardization of FOUNDATION™ fieldbus as the communication foundation supporting Asset Excellence for VigilantPlant, which is an approach aimed at the advancement of plant instruments and equipment. With the recent dramatic advancement of fieldbus technologies, information processing technologies, and network speed, it has become possible to process various kinds of information inside the field sensors and transmit the results to the distributed control system (DCS) and host computer.
Large process industry companies have recently started building plants with world-class safety and profitability to reinforce their competitive edge in the global market. As for plant operations, support functions for improving operators' plant operation skills and for extending operators' maximum capability are required to the DCS so that an operator can expand the area of plant monitoring or operate a plant with higher cost- consciousness.
In 2000, we formed a technical tie-up with Shell Global Solutions (SGSI) to enter the advanced process control and optimization solution business. At the same time, we started marketing a solution based package comprising an Exasmoc multi-variable model-based predictive control function, an Exarqe property estimation function, an Exaspot online real-time optimizer and an MD control monitor & diagnosis function by taking full advantage of the SGSI advanced control and optimization technology (APC&O).
In plant sites, there are various places such as those affording an unobstructed view like tank yards, and others surrounded by metal pipes and equipment obstructing the view (hereafter referred to "pipe jungles"), often seen in oil refinery and chemical on-site plants. The frequency band of radio waves used for field wireless communication is 2.4 GHz, which has high straightness and its ability to go around things can hardly be expected.
The changes in social environment, such as globalization of enterprise activities, depletion of natural resources, and eco-oriented movement will affect the structure of mass production. Control systems must be prepared with flexibility and scalability in both size and function to adjust to the changes.
The process industry in Japan faces increasingly critical environmental and safety issues. Additionally, in Japan, many skilled engineers with years of experience will be retiring in 2007. Although the process industries such as petroleum, petrochemical, steel and paper, etc., are highly automated, human skill is still required in an abnormal situation or for a critical production change.
In 2005, Yokogawa announced "VigilantPlant" as a concept to ward the realization of a type of plant operation that is considered ideal by our customers.
Reducing energy consumption and CO2 emissions due to the operation and maintenance of plant equipment is becoming a global challenge. Yokogawa offers the InsightSuiteAE plant asset effectiveness optimization services, including the Asset Performance Diagnostics service, as solutions for plant assets to address such challenges together with customers.
The purpose of blending in a petroleum refinery is to mix semi-finished products that have been rectified during various refining processes so as to manufacture a product that meets specification.
Almost 20 years have passed since MVC came into use commercially. At first, MVC was only used in large-scale petroleum and petrochemical plants, because at that time computers were expensive and incapable of the performance required to execute an MVC package.
In 1999, Yokogawa Electric Corporation formed an alliance with Shell Global Solutions International B.V. (SGSI) in Advanced Process Control (APC), and both companies have since jointly developed products. This alliance successfully combined SGSI's experience gained through more than 800 projects in more than 30 years and Yokogawa's great deal of experience with the process control market, and strengthened the scheme to provide the APC technology.
As a company that has strong relationship with nature and provides products using nature's blessings, Mercian Corporation is committed to the environment. Its environmental philosophy is "Mercian thanks nature's blessings and capability that sustain life, and seeks to balance environmental preservation with creating an affluent society."
Intelligent field instruments and process analyzers accumulate diverse field information including process values and diagnostic results. This data needs to be sent to upper systems such as distributed control systems (DCS) via digital communications such as FOUNDATION Fieldbus and analyzer buses, or hybrid communications such as HART and Brain, and visualized to enable the customer to utilize them for plant operations and maintenance.
Due to the rising energy demand in emerging countries in recent years, the amount of oil and gas production has been increasing, thus investment in the development of new oil and gas fields and replacement of old facilities has been booming.
Recipe management software refers to the computer software used to manage product names and their corresponding recipes and set the recipe data in the control system in order to control the operations of a plant in which multiple materials are blended to manufacture a number of different products.
Many field devices are now being connected to process control systems through fieldbus communication. These field devices have intelligence, and so many settings and adjustments can be made through fieldbus communication.
The development of the CENTUM CS 1000 distributed control system for small- and medium-scale plants was based on two basic design principles: 1) to have the same architecture as the CENTUM CS and 2) with the objective of becoming a global product.
As for a controller used in a distributed control system (DCS) shown in Figure 1, covering as many applications as possible with a single controller will bring cost reduction effects such as easy engineering and a small controller installation area. Therefore, the controller is required to process large amounts of data more quickly.
More than ten years have passed since the first digitized field devices were introduced. These support either a hybrid communication protocol such as HART or a full digital communication protocol such as FOUNDATION Fieldbus.
The specifications of the ISA100.11a wireless communication standard of the International Society of Automation (ISA) for industrial automation were published, and companies are developing products based on the standard. The ISA100.11a has many features such as high reliability including redundancy, network scalability, and support for various protocols for industrial automation.
For safe plant operations, it is critical to correctly understand the conditions encountered by operators inside the plants. In relation to this topic, human cognition has been studied in various fields such as human factors and ergonomics.
The recent variety of industrial and railway accidents happening right before our very eyes make us painfully aware that "safety" must be put first and foremost. "Safety first" is a concept accepted by everyone and there is no room for disagreement. However, the author feels that, in some cases, the concrete objectives of "safety first" are not actually clear, and the grasp of the hazards is insufficient.
In recent years, safety and profitability have become ever more important in the process industry due to fierce global competition. Greater emphasis is being placed on highly efficient plant operation for reducing the increasing energy bill.
The business world surrounding the manufacturing industry is undergoing rapid and drastic changes. Achieving production activities that can respond swiftly to such environmental changes has become an urgent task.
As field instrumentation devices become increasingly digitized and computerized, interactive and remote access to a large quantity of field information becomes possible. This will increase the efficiency of plant equipment maintenance by reducing labor requirements in field patrol work for example.
The requirements for water supply and sewage services are becoming increasingly strict, such as consolidation of facilities, operational efficiency, lower cost, and information transparency due to stagnant demand. There is also demand for greater use of information technologies (IT), encouraged by the government's e-Japan strategy.
After having undergone several improvements, magnetic flow meters have become highly accurate and reliable and are widely used in the industrial instrument field today. Magnetic flow meters consist of a detector and a converter, with the principle of the detector adopting Faraday's electromagnetic induction law.
Yokogawa proposed the VigilantPlant concept as an ideal plant that achieves fully optimized operation where all the necessary information is given to all the operators involved in the plant operation. In VigilantPlant, operators are able to quickly respond to changes in the external environment while the production activities run without any interruption.
Industrial automation (IA) systems and products, which utilize measurement, control and information technologies, are used across the world as fundamental infrastructure for achieving safe, stable and highly efficient plant operation. In order to keep the systems and products effective throughout the plant lifecycle, customers need to periodically check their effectiveness and take prompt action if any problem is identified.
Global market pressures are causing businesses world wide to strive to lower manufacturing costs and to become more agile companies in order to quickly respond to changes in market demands and to fend off competitive threats. Yokogawa's customers in all industries and markets are responding to this pressure by working to more closely integrate their plant manufacturing systems with their enterprise wide business systems in a seamless manner.
In Japanese industries which grew rapidly until the early 1990's, solid production techniques for creating high-quality products supported the development of manufacturing industries. However, the economic environment has been changing rapidly and tough global competition has become unavoidable. Particularly, the manufacturing industry must adapt not only to changes in economic environments but also to changes in social conditions such as emphasis on health, safety, and environment (so called HSE).
Recently, standardization of procedural automation of manual operations has been promoted mainly by the International Society of Automation (ISA), and the functional requirements necessary for automation are being studied by the ISA106 committee in the US.
For a coal fired power generation plant (hereafter referred to as "BTG facilities," in which "BTG" stands for boiler, steam turbine, and generator) supplying power to a large-scale production plant, the CO2 emissions from such facilities are a critical issue today.
Environment and safety are major topics on a global scale in recent times. As symbolized by the effectuation of the Kyoto Protocol, an interest in preserving the environment is growing worldwide, and there is also a tendency to criticize more severely, occurrences of industrial accidents that are accompanied by environmental contamination or which may cause damage, etc., to residents in the surrounding areas.
Conventional safety instrumented system (SIS) is typically installed separated from a distributed control system (DCS) to eliminate interference from the DCS and assure safety. However, users increasingly wish to integrate SIS with DCS while maintaining the safety of safety controllers.
Yokogawa's ProSafe-RS safety instrumented system is used for many applications as a system conforming to the safety integrity level (SIL) 3 defined in the IEC61508 international functional safety standard. To deal with temperature inputs, systems were conventionally configured using signal conditioners.
In recent years, expectations for control systems using wireless communications have been increasing in the process control market. This is because these systems do not require power and communication wiring for field instruments, enabling reduced initial and maintenance costs, and easy installation.
Yokogawa has been leading the process automation industries as one of the pioneers in field digital technologies represented by the FOUNDATION fieldbus™ and Field Device Tool/Device Type Manager (FDT/DTM).
Vortex flow meters were put into practical use in the 1970's; thus their history is relatively short. They have been mainly used at petrochemical plants because of their two main features, the fact that they do not have any mechanical moving parts and are maintenance-free. Yokogawa started research and development on the vortex flow meter before 1970.
Latest field devices have not only various self-diagnosis functions but also process-interface-diagnosis functions such as valve diagnosis of valve positioners and impulse line blockage detection of differential pressure transmitters. The YVP valve positioner can easily perform initial tuning, parameter adjustment, trend monitoring, and valve diagnosis, by using the ValveNavi YVP management software.
Due to emerging competitors from the rapidly growing countries such as India and China and the global economic downturn triggered by the Lehman shock, many companies in the process industries are struggling to survive the severe global competition.
The operation and monitoring functions of a plant control system are important means of understanding the condition of the plant and how it operates. Traditionally, user needs for the system focused on such features as increased operability and durability. As a result, these functions were developed for a dedicated machine in the form of dedicated human-machine interface software.
Downloads
Brochures
Looking for more information on our people, technology and solutions?
Contact Us