Executive Summary
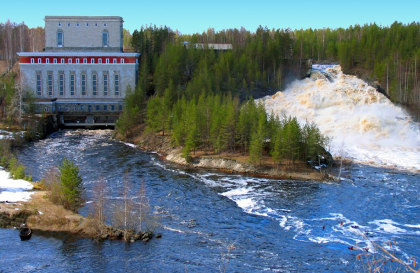
The Pal’eozersk hydro power plant in Russia
The Republic of Karelia is located in the northwest of the Russian Federation and has many hydro power plants making use of the abundant water resources. The Pal’eozersk hydro power plant was built in 1954 close to the Sun River which flows through Girvas city, with two 12.5 MW units. This is a cascade type of hydro power plant which uses the difference in height of the Sun River.
The owner of the plant, Territorial Generating Company number 1 (TGC-1, also referred to as TGK-1 [Territorial'naya Generiruyushchaya Kompaniya No. 1]), is a regional power generation company affiliated with Gazprom, the biggest gas company in Russia.
TGC-1 owns power plants in the northwest of Russia and 40% of its capacity comes from hydro power plants, with a total capacity of 3,000 MW.
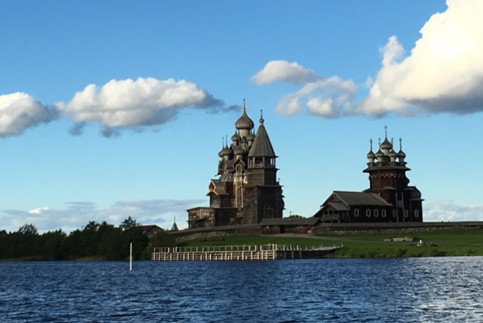
Due to the aging of existing equipment which had been in use for more than 50 years, TGC-1 decided to modernize the equipment and replace the aging control, monitoring, and protection systems with Yokogawa’s latest CENTUM VP distributed control system and ProSafe-RS safety-instrumented system engineered by Forus, the local agent of Yokogawa.
The Challenges and the Solutions
As this area is far from the center of the city, load control is required for island operation in case of a grid shutdown due to a natural disaster, which was difficult to achieve with existing old and awkward hydraulic servo drives for turbine wicket control.
To solve this problem, the existing drives were replaced with redundant motor-driven cylinders and new precise controls. This realized stable load control at less than 3 MW power generation and enabled island operation in case of a natural disaster, which used to cause frequent shutdowns. There has been no problem or shutdown since the plant started operation in December 2015 following the replacement by Forus.
Replacement of drives for turbine wicket control
Replacement with redundant motor-driven electric actuators has brought the following advantages over conventional hydraulic servo drives:
- Eliminated environmental hazards
- Higher reliability and long-term stability of turbine control in normal and emergency situations
- Minimized maintenance and routine manual work, maximized service interval
- Reduced maintenance budget
- Greatly improved static and dynamic turbine controllability
- Tuning flexibility of control modes
- Highly precise control with positioning accuracy of 0.1%
Before replacement: Hydraulic servo drive
After replacement: Electric cylinder actuator with redundant motors
Speed gear and sensors
Replacement of mechanical hydraulic controls
The existing mechanical hydraulic controls were replaced with digital electric controls implemented in the CENTUM VP. The new control system with newly installed speed gear and sensors has dramatically improved speed and load control. Full integration with excitation, electrical protection, vibration control, and more systems combined with such beneficial electric actuators has delivered the following benefits:
- Stable turbine control over a long term and minimized total losses resulting from improper operation by the control and safety systems
- Major improvements in ecological, technical, and financial performance
- Unstaffed and remote HPP operation capability
- Redundant, high-precision electromechanical wicket gate control with the ability to function autonomously for at least one hour during loss of power supply, thanks to accumulators (batteries) provided for guaranteed wicket gate closing in emergency situations
- Unified control platform throughout all system levels: turbines, safety systems, HPP general equipment, whole HPP, regional control centers, and united control center
Island operation test
Full integration with electrical equipment
In addition, the scope of modernization included the supply of new electrical equipment such as variable frequency drives, generator protection relays, and excitation system. This enabled:
- Full integration with excitation, electrical protection, vibration control, and other systems
- Active and reactive power group control implemented in a standard field control station without upper-level computer or server
- Four levels of emergency protection: excitation system and generator electrical safety protection, turbine control system protection, SIL-3 ProSafe-RS system, emergency stop buttons for use at undesirable pressure
Operation graphic window
Customer Satisfaction
TGC-1 operators are satisfied with the result of the replacement. The HPP cascade general manager Evgeniy Lopatin commented, “Before the replacement, we were skeptical about whether Yokogawa could complete this project or not, but our fears proved to be unfounded. After system replacement, we found no malfunction. Also we have suffered no shutdown during operation even in island operation. We are very satisfied with the new system, and Forus’s and Yokogawa’s work. Various companies visit our hydro power plant to see it working thanks to such a successful project”.
Pal’eozersk HPP operators and project members
Verwandte Industrien
-
Power
In the mid 1970s, Yokogawa entered the power business with the release of the EBS Electric Control System. Since then, Yokogawa has steadfastly continued with the development of our technologies and capabilities for providing the best services and solutions to our customers worldwide.
Yokogawa has operated the global power solutions network to play a more active role in the dynamic global power market. This has allowed closer teamwork within Yokogawa, bringing together our global resources and industry know-how. Yokogawa's power industry experts work together to bring each customer the solution that best suits their sophisticated requirements.
-
Hydro Power
Reliable monitoring and control of hydropower plants around the world.
Zugehörige Produkte & Lösungen
-
ProSafe-RS
Das Sicherheitssystem ProSafe-RS wurde von der deutschen Zertifizierungsstelle (TÜV) zertifiziert und erfüllt die Sicherheitsstufe (SIL) 3 nach IEC 61508. Das System wird bereits in mehr als 2.100 Projekten eingesetzt – von großen integrierten Automationsprojekten bis hin zu Standalone-Lösungen. Die ProSafe-RS-Sicherheitssysteme von Yokogawa zeichnen sich durch ihr durchdachtes Design, lebenslangen Support und lange Lebensdauer aus.