Note:
Original article is published in Gekkan-Keiso July and this article is translated from Japanese into English.
Original article (pdf file, language: Japanese)
1.Introduction
The stable plant operation requires the maintenance of various facilities. The plants have a lot of facilities to need the maintenance because there are the main line of products and lines to supply of compressed air, nitrogen gas, steam, cooling water, fuel, and so on, which are called utilities. However, the reality is that many plants are unable to devote sufficient resources to maintenance work. In addition to the social issue of a shortage of personnel caused by the aging of engineers and fewer children, many plants are facing the problem of aging facilities. To solve these various maintenance-related problems, it is imperative to quickly break away from the dependence on personal experience and intuition in performing work. The key to achieving stable and safe plant operation and overall optimization is to improve the efficiency and labor saving of device maintenance. Vortex Flowmeters VY Series can support these by the digitalization technology to improve the efficiency of maintenance work and the unique sensing structure with excellent maintainability.
1.1 Vortex Flowmeter VY Series Use Digital Technology to Support Efficient and Systematic Maintenance Work
Since its world-first launch in 1969, Yokogawa Electric’s vortex flowmeters have sold more than 500,000 units worldwide. The VY series of vortex flowmeters can measure liquids, gases, and steam, and inherits Yokogawa’s unique sensing structure, offering robustness, stability, and excellent serviceability. It supports wide flow range of connection size from 15 mm to 400 mm. The line-up also includes built-in temperature sensor type including the temperature sensor in vortex shedder, reducer type integrating reduction tube and expansion tube suitable for steam supply line whose flow rate decrease seasonally, high-temperature type up to 450 ℃, cryogenic type, high-pressure type and more to cover a wide range of applications.
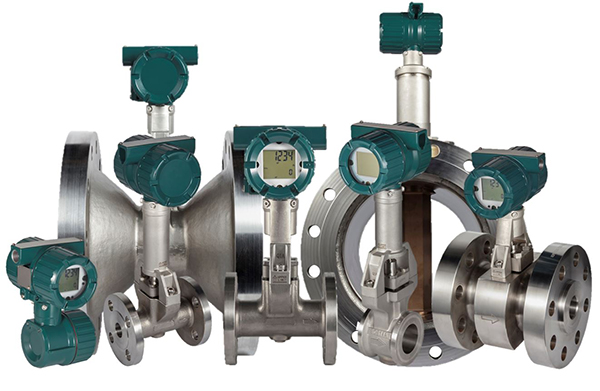
The VY series comply with variety standards such as explosion-proof for each country and PED, in addition to functional safety IEC 61508 and safety integrity level SIL2 requiring higher reliability. The wide range of industry standard, legal regulations and certifications is also complied with such as NAMUR NE21, NAMUR NE107, marine certification, NACE material certification and so on.
2. Digitalization Technology for Efficient Maintenance Work
The VY series have a variety of device diagnostic functions that have evolved through digitalization technology, and compatible verification tools with excellent operability (Figure 1). The VY series have Self-diagnostic Function and Process-diagnostic Function as standard. In addition, by using the FSA130 Magnetic Flowmeter/Vortex Flowmeter Verification Tool (sold separately) and FieldMate of Versatile Device Management Wizard (sold separately), the users can easily to use Verification Function and Remote Maintenance Function on the PC screen. And these functions can dramatically improve the operability of checking and managing the device health. In the following section, we introduce these various device diagnostic functions which make a substantial contribution to improved efficiency and labor savings in maintenance operations.
Figure 1: Diagnostic Function of VY Series
2.1. Self-Diagnosis Function for Easy Identification of Point Requiring Device Maintenance
The VY series, with its advanced digitalization of internal signals, is equipped with self-diagnostic capabilities for the entire device, including the vortex shedder bar and sensor elements. Parameters and alarms can easily identify points where device maintenance is required, helping to minimize plant operation downtime. In addition, because the series complies with functional safety standards (SIL2-compliant), the vortex flowmeters can be used in loops that require high reliability, such as safety instrumentation.
2.1.1. Self-diagnosis Function
The VY series is equipped with self-diagnosis function, including the vortex shedder, the flow sensor elements, the built-in temperature sensor, the internal CPU, IC, and circuit for calculating the flow rate. When the VY series find device abnormalities, alarm output immediately. The upper-layer system can find device abnormalities quickly, thereby contributing to increase a plant’s operating rate. Verification Tool, introduced in Section 2.2.1., also can check device abnormalities.
Figure 2: Scope of the Self-diagnostic Function
2.1.2. Process-diagnostic Function
The VY series has not only Self-diagnostic Function but also Process-diagnostic Function. Process-diagnostic detects anomalies such as fluid pulsation/oscillation and abnormal piping vibration, allowing the user to distinguish between abnormalities on the process side and those on the device side. If there is an output error, it is necessary to separate the Device alarm from the Process alarm. Since the user can determine the status of the device by self-diagnostic, the reliability of the process diagnosis alarm is enhanced, and the user can do appropriate initial response when the alarm occurs (Figure 3). In this way, Diagnostic function of the device helps to identify points in need of maintenance, helps to shorten the down time of plant operation and helps implement smart maintenance practices.
Figure 3: Image of Self-diagnostic and Process-diagnostic by Diagnostic function of the device
2.2. Verification Tool to Monitor Device Health from Remote Location
FSA130 (Magnetic Flowmeter/Vortex Flowmeter Verification Tool, sold separately) and FieldMate (Versatile Device Management Wizard, sold separately) realize remote maintenance from remote location such as an instrument room without going near the device installed in the plant. Figure 4 shows the overview of Verification Tool, Verification Function and Remote Maintenance Function of FSA130.
Figure 4: Overview of the Verification Tool
2.2.1. Verification Function
Figure 5 shows top screen of the Verification Tool of FSA130. Standard Verification can check the health and display the results interactively using the VY series' self-verification (built-in verification) without considering complex parameter settings. Enhanced Verification uses external devices such as a Handy calibrator CA500 and checks the health of Analog Output/Pulse Output/Status Output/Analog Input. Verification results can be saved as database of FieldMate or file, which can be read and checked when needed. The tool also supports the output of reports (PDF file format), which contributes to the efficiency of daily maintenance work.
Figure 5: FSA130 health check result screen of
VY series all function block
2.2.2. Remote Maintenance Function
In the conventional model, when unstable analog output occurred, the users brought oscilloscope (electric signal measuring instrument) to the device on the site, checked the measurement status of the device by oscilloscope, manually tuned parameters, and needed to stabilize the output. In the VY series, Remote Maintenance Function of the FSA130 allows the user to check the measurement status and tune setting as necessary from a remote area, e.g., instrument room. It is easy to check the measurement status even during operation without requiring extensive preparation such as bringing in an oscilloscope. The health check of device by Verification Function and the measurement status by Remote Maintenance Function routinely will contribute to the maintenance works based on the condition. Remote Maintenance Functions include Vortex Waveform Monitor, Vortex Frequency Analyzer, and Vortex Sensor Prediction.
Figure 6 shows Vortex Waveform Monitor screen. Upper line shows the vortex signal waveform, and Lower line shows the vortex waveform after signal processing. The user can check graphically measurement status. And if stable measurement is difficult in the application with automatic tuning, the user can tune the optimal signal waveform according to the customer's application in Vortex Waveform Monitor.
Figure 7 shows Vortex Frequency Analyzer screen. The user needed to acquire the data by a handheld terminal and needed to graph by spreadsheet software, but now FSA130 can be realized by only itself. Vortex Frequency Analyzer shows the signal strength distribution of each frequency band of the vortex signal and visualizes the state of vortex signal and noise contamination such as environmental vibration. Vortex Frequency Analyzer shows that the tuning to remove vibration noise from the vortex signal is done automatically without tuning it individually. Manual adjustment is also possible. Thus, this function supports efficiency of maintenance and labor saving.
Figure 6: FSA130 Vortex Waveform Monitor Screen
Figure 7: FSA130 Vortex Frequency Analyzer Screen
Vortex Sensor Prediction graphically display changes over time in the sensor elements inside the flowmeter and estimate when maintenance is required. Figure 8 shows a demonstration result of the vortex sensor health prediction. The ■ mark shows the measurement data of the sensor in trend, and the ⃞ mark shows the prediction data of the sensor in the future. In this way, enabling maintenance appropriate for the conditions based on objective data supports efficient and well-planned condition-based maintenance. This minimizes the risk of lost production opportunities due to maintenance and helps maintain and improve plant operating rate.
Figure 8: FSA130 Vortex Sensor Prediction screen
3. Hardware Configuration with Excellent Maintainability
In addition to digitalization technology, the VY series has excellent maintainability in terms of hardware. The unique sensing structure is detachable and highly maintainable, and transmitter parameter is backed up to sensor side. These configurations meet the need for labor savings with excellent serviceability in terms of both hardware and software.
3.1. A Unique Sensing Structure That Allows Detachment from the Body for Easy Maintenance
During the long operation of a plant, there will be times when the vortex shedder bar will need to be cleaned or replaced due to fluid deposition and other factors. The vortex shedder bar in Yokogawa Electric’s vortex flowmeters has a unique sensing structure that incorporates two flow sensors and one temperature sensor (optional), providing a high level of robustness and long-term stability. The vortex shedder bar can be easily detached from the body, eliminating the need to remove the entire flowmeter from the piping for cleaning or replacement.
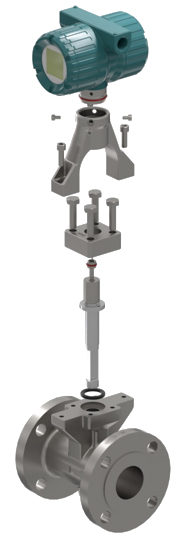
3.2. Backup Transmitter Parameters to Reduce Downtime
It is also assumed that remote transmitter will need to be replaced during long plant operations and vortex flowmeter periods. Manual setup of a large number of sensor specific parameters is time-consuming and may result in misconfiguration when the system is replaced and restored in a short period of time. For this problem, The VY series can back up transmitter parameters to the remote sensor’s memory. This allows for easy restoration of previous conditions when replacing the transmitter, meaning that operation can be resumed after a short downtime. Maintenance that does not cause unnecessary shutdowns ultimately improves productivity and contributes to continuous plant operation.
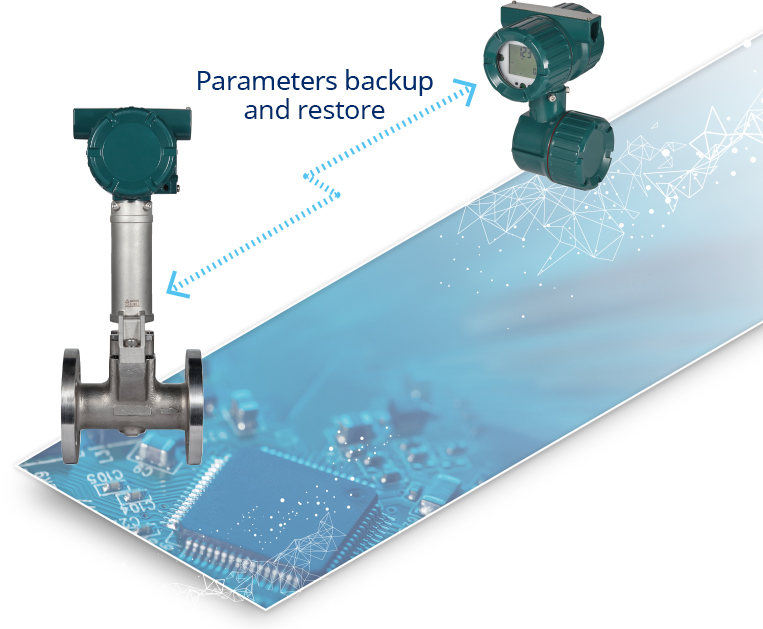
4. Summary
Vortex flowmeters are used in utility lines essential for many industries. The Vortex flowmeter VY series will contribute to the efficiency and labor saving of maintenance work in both software and hardware by digitalization technology and unique structure.
The lack of resources for maintenance work causes the shortage of engineers due to the aging and declining birthrate, and the aging of facilities have been important issues in recent years and will continue. We hope to support the resolution of maintenance work issues by digitalizing and visualizing individual intuitions and experiences.
We hope that the vortex flowmeter VY series introduced in this article will help customers resolve maintenance work issues. We will continue to create value with customers, not be satisfied with current products.
Looking for more information on our people, technology and solutions?
Contact UsRelated Products & Solutions
-
FSA130 Magnetic Flowmeter / Vortex Flowmeter Verification Tool
Magnetic Flowmeter / Vortex Flowmeter Verification Tool provides the diagnosis, reporting and data management for the health check of ADMAG TI (Total Insight) Series AXG or AXW and CA Series with HART protocol and Vortex Flowmeter VY series with HART protocol.
FieldMate should be prepared by customers. FSA130 is the license key to activate the Verification Tool. -
Mobile Field Device Management FieldMate
FieldMate 3.0 is a PC based tool that enables you to see intelligent field devices clearly, know their condition in advance, and act with agility throughout maintenance work flow.
-
Vortex Flowmeters VY series
Vortex Flowmeters VY Series is the latest model of Yokogawa vortex flowmeter and is the successor to the digitalYEWFLO Series.
VY Series consists of the latest digital technology and Yokogawa's unique structure inherited from YEWFLO Series.