Introduction
An induction furnace melts metal by creating very large currents in the material. These currents are induced using three electrodes positioned inside the furnace. The furnace is automated so that once the material has been melted, the electrodes are removed and the furnace then tips the molten metal into a crucible where it can be easily transferred to the production line where it will be cast into ingots. The atmosphere is extremely aggressive and the wired infrastructure is both expensive and very unreliable to maintain. The furnace control requires a total of 20 measurement points distributed around and inside the furnace. The harmonic field effects caused by short circuit 40,000 A (300V). The causes significant interference.
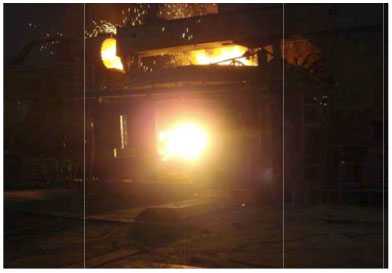
Benefits
- Improved quality of measurements
- Increased reliability by eliminating constant breaking of cables
- Reduced maintenance time and effort to descale the furnace casing
- Four fold improvement in operational up time
- Improved flexibility in changing of furnace itself after each batch
- Improved immunity from high tension electrical interference
Solution
Three YTMX580 (Total of 24 temperature measurements) installed at the upper, middle and lower sections of each induction furnaces. The transmitters move along with the furnace.
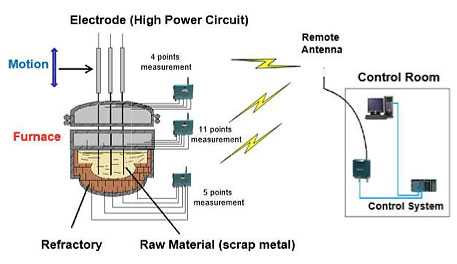
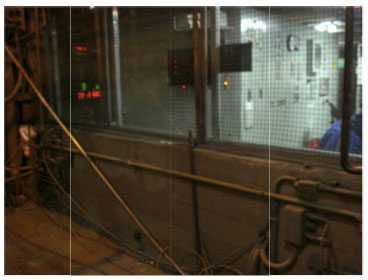
The temperature signal goes straight to the gateway installed inside the control room.
Result
After installing the wireless system, the furnace has operated continuously for more than a year. There were no further temperature measuring failures and the new wireless measurements increased the production time four fold.
Conclusion
The ISA100 wireless system reduced maintenance costs and effort while increasing product time. The most critical point in controlling the furnace, the temperature measurements showed no more failures. After the trial on the first furnace, the user is now moving all of its remaining furnaces to be equipped with ISA100 wireless products.
![]() |
![]() |
![]() |
Deposition chip overheated iron. | The cables suffer frequent damage. | Elimination of remote panels, and a large quantity of interconnecting cables. |
Related Industries
-
Iron & Steel
- Iron and steel industry
- Improve quality of products, manufacturing, and operation technologies
- Address environmental and energy-efficiency issues
- Create the ideal plant and evolve for mutual growth
Related Products & Solutions
-
Field Wireless
Reduce infrastructure investment and increase plant operation insights
-
YFGW410 Field Wireless Management Station
YFGW410 Field Wireless Management Station has system manager/security manager/gateway function based on ISA100.11a, and combining this with Field Wireless Access Point(YFGW510) and/or Field Wireless Media Converter(YFGW610) composes the field wireless system.
-
YFGW510 Field Wireless Access Point
YFGW510 Field Wireless Access Poin has backbone router function based on ISA, and combining this with Field Wireless Management Station (YFGW410) and/or Field Wireless Media Converter (YFGW610) composes the field wireless system.
-
YFGW520 Field Wireless Access Point
YFGW520 Field Wireless Access Poin has backbone router function based on ISA, and combining this with Field Wireless Management Station (YFGW410) and/or Field Wireless Media Converter (YFGW610) composes the field wireless system.
Have Questions?
Contact a Yokogawa Expert to learn how we can help you solve your challenges.