World's First Truly Integrated Safety Controller
ProSafe-RS is Yokogawa's IEC61508 and ANSI/ISA 84 compliant safety system. It has been used in over 2,400 projects, ranging from large scale integrated process automation projects to stand-alone solutions. Yokogawa's ProSafe-RS safety systems are built with competence, life cycle support and long term sustainability.
Latest release Information of R4.10 (November 2023)
- Windows 10 Enterprise LTSC 2021 and Windows Server 2022 Standard Support
ProSafe-RS Overview
World's First Truly Integrated Safety Controller
Yokogawa puts an end to DCS-SIS incompatibility with the ProSafe-RS, the world’s first truly integrated "safety PLC" for the process industries. Achieving absolute integrity between distributed control system (DCS) and safety instrumented system (SIS) for plant automation has traditionally raised complex design and integration issues. Conventionally, two separate monitoring and operating environments were required for a DCS and SIS. Different communications and distinctive hardware architectures had to be set up. Plant managers striving to optimize process operations have taken it as a given that project time and expenses would escalate.
About OpreX
OpreX is the comprehensive brand for Yokogawa’s industrial automation (IA) and control business. The OpreX name stands for excellence in the technologies and solutions that Yokogawa cultivates through the co-creation of value with its customers, and encompasses the entire range of Yokogawa’s IA products, services, and solutions. This brand comprises the following five categories: OpreX Transformation, OpreX Control, OpreX Measurement, OpreX Execution, and OpreX Lifecycle. One of the product groups that make up the OpreX Control category is the OpreX Control and Safety System family, which includes the ProSafe-RS. With its various OpreX Control solutions, Yokogawa is able to quickly effect changes for its customers that lead to a transformation in such areas as management and operations, and provides highly reliable control technology that ensures high efficiency, high quality, and safe and stable plant operations.
With the OpreX brand, Yokogawa will deliver integrated solutions that address specific needs and support its customers in their efforts to transform and grow their businesses.
Details
Engineering
ProSafe-RS is composed of the Safety Engineering PC (SENG) equipped with engineering and maintenance functions, the Safety Control Station (SCS) for safety control and Vnet/IP for control network to communicate with each of those equipment.
ProSafe-RS can be integrated with the CENTUM VP. The SCS can be operated and monitored by the HIS (Human Interface Station) of the CENTUM VP. It is also possible to connect to other DCSs and PLCs via subsystem communication (Modbus communication).
HART communication on ProSafe-RS allows Plant Resource Manager (PRM) to manage the HART communication devices connected to I/O modules on SCS. Also, the AO signal allows PRM client to conduct Partial Stroke Test (PST) on HART-supported valve positioner equipped with the PST function.
One architecture
Seamless architecture achieves true integration of DCS and SIS, contributing to plant optimization.
Expected operational benefits:
- faster project implementation at a lower cost - using just one process network saves engineering design time
- greater operational efficiency - integrated information displays are clearer and more usable
- lower cost of ownership - common control and network architecture standards cut maintenance overhead
Eliminating SIS selection complexities
ProSafe-RS is SIL3 certified in a single module configuration. Redundancy is already built-in to each ultra-compact input, output, and processor card. This intrinsically simple modularity makes it possible to design systems with ease. If additional system availability is required, users can add redundancy on a function by function basis by simply plugging in the appropriate module.
Yokogawa's parallel engineering
Application engineering and hardware engineering can progress independently and parallel. This parallel work shortens the project schedule, either by starting later or by possibly enabling an earlier start-up.
1. Early start-up of a plant
Starting up a plant more quickly has long been an issue that directly affects customers’ profits.
Although the start-up of instruments and the installation of I/O modules can be performed in parallel, the loop check is completed only after the FAT (Factory Acceptance Test) is finished and the controller and the engineering environment are installed.
In Yokogawa’s parallel engineering, there is no need to wait for the controller and engineering environment to be completed. The integrity of loops can be checked only with N-IO modules and Field Commissioning Support Package. If any change is found in the I/O definition information, it can be corrected on the spot, and the corrected definition can then be refiected in the master information in the plant.
2. Reducing risks to scheduled project delivery
The I/O definition often needs to be changed due to physical constraints. Such problems usually occur during commissioning and may prolong the project schedule, as well as require costly re-wiring.
The I/O definition of N-IO modules can be changed more fiexibly. Signal types among DI/DO/AI/AO can be switched only with software, and there is no need to change I/O modules. Since signal types can be designated at each channel, there is no need to stock I/O modules for each signal type, reducing maintenance costs.
Automation Design Suite (AD Suite)
ProSafe-RS R4 features AD Suite, the same engineering environment used with the CENTUM VP integrated control system, allowing the integrated management of CENTUM VP and ProSafe-RS data.
With this feature, ProSafe-RS engineers can use AD Suite to design the I/O.
AD Suite also has functions for managing the change history and recording changes that save time when renovating systems.
Better Operations, easier Engineering and Hardware Reduction
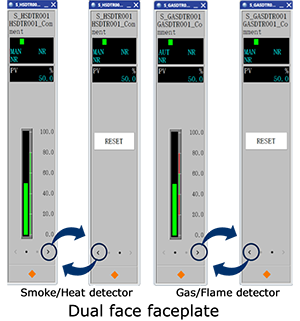
FGS (Fire & Gas System)
- Standard FGS HMI parts for gas, flame, smoke and heat detectors are added for better operations.
- Standard function blocks for FGS detectors are added for easier engineering.
- ProSafe-RS analog module can reset smoke and heat detectors alarms without additional hardware such as relays and DO modules.
The logical solution for perfect control
One network
ProSafe-RS plugs directly onto the same network used by Yokogawa's field-proven CENTUM VP. No gateway or interface hardware is required for data exchange between SIS and DCS functions. Safety communication between SIS controllers is realized and certified in a mixed DCS - SIS configuration.
Expected benefits:
- simple and quick route to system realization
- reduced engineering complexity and cost for connecting SIS and DCS
- lower maintenance costs for large process plants
Safe, reliable and available control without compromise
One architecture
Seamless architecture achieves true integration of DCS and SIS, contributing to plant optimization.
Expected operational benefits:
- faster project implementation at a lower cost - using just one process network saves engineering design time
- greater operational efficiency - integrated information displays are clearer and more usable
- lower cost of ownership - common control and network architecture standards cut maintenance overhead
Eliminating SIS selection complexities
ProSafe-RS is SIL3 certified in a single module configuration. Redundancy is already built-in to each ultra-compact input, output, and processor card. This intrinsically simple modularity makes it possible to design systems with ease. If additional system availability is required, users can add redundancy on a function by function basis by simply plugging in the appropriate module.
Significant gains in the capabilities of plant displays
- Common human-machine interface (HMI)
No more separate monitoring of SIS and DCS. While continuing to use the interface that they are most familiar with, operators can more rapidly predict which process conditions are likely to reach emergency levels. - Unified event data
Sample screens such as "faceplate" style instrument and alarm displays are provided that enable easy data comparison and decision making. - Back-tracking analysis
A further benefit of data integration is the ability to analyze events preceding an alarm - a powerful tool for effective process safety management.
It's now easy to create displays that integrate DCS and SIS data.
Virtualization Platform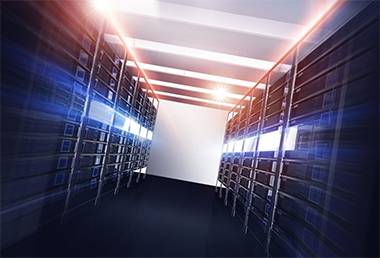
Yokogawa's virtualization separates system software operations from physical hardware dependencies, allows software reusability to optimally commission system hardware.
Virtualization platform enables a single server to perform the work of multiple virtual computers, thus reducing the number of computers required to configure a control system. With this platform, both the hardware and software required to build a virtual environment are provided.
By means of this virtualized server environment, it is possible to separately update and make modifications to hardware and software as required.
This translates to customer's business centric benefits like smooth migration to new physical hardware with reduced downtime, shorter migration process and system tests time.
From maintenance point of view, segregation of hardware and software maintainability are also the significant advantages.
In addition to conventional I/O modules dedicated for specific signal types (FIO module), ProSafe-RS R4 can offer the N-IO module, which handles different signal types at each channel.
By concurrently accepting both types of module, ProSafe-RS R4 can deal more flexibly with a customer’s plant design requirements.
N-IO (Network I/O): Smart Configurable I/O (SCIO)
Features
- DI/DO/AI/AO signals can be handled at a single module.
The types of I/O signal at each channel can be changed with software. - Remote installation up to 50 km is available by using optical cables.
- SIL3 can be achieved with single configuration. Redundant configuration is also selectable.
- Terminal block has a disconnect function of signal loop of field devices as a standard function.
- An N-IO baseplate is available for intrinsically safe barriers.
For more detailed information please visit the below sites. - N-IO eliminates the need for marshalling cabinets, further saving space and costs. Thus this is ideal for flexible and distributed installation in the field.
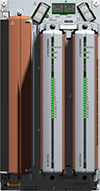
FIO (Field network I/O)
Features
- A variety of I/O modules (AI/AO/DI/DO/Communication function) are available.
- Modbus TCP/RTU communication (Master/Slave) is available by using communication modules.
- Remote installation up to 50 km is available by using optical cables.
- SIL3 can be achieved with single configuration. Redundant configuration is also selectable.
- Dedicated terminal boards, terminal blocks, and cables for FIO are supported.
A single, simple, SIL3 solution
Yokogawa designers have employed state-of-the-art electronic design techniques and component packaging to miniaturize the safety controller circuitry. Every ProSafe-RS processor, input module, and output module features a dual architecture, providing users with SIL3-level protection on a single card. This architecture is simplicity itself to understand, design, install and maintain. Complete safeguarding now comes in one box. Furthermore, the design has an extremely high diagnostic coverage factor of more than 99%, providing users with a means of rapid fault detection that can allow repairs to be effected within an acceptable period - with minimal impact on the process.
Plug-in availability
If even higher system availability and fault tolerance is required, ProSafe-RS can be configured for dual redundancy while maintaining SIL3 by simply plugging in the appropriate additional card. Because the I/O or processing functions of ProSafe-RS have a modularity that extends down to the function level, redundancy can be applied exactly where it is needed - to input, output, or processor modules - providing a combination of safety and economy that is unprecedented in the SIS market. This flexibility allows any mix of dual redundancy to be configured such as a single input and redundant output or a redundant input and single output.
Versatile Modular Redundancy (VMR)
With its flexible selection of redundant CPU and I/O modules, ProSafe-RS delivers the high availability required by even SIL3 applications. Rather than making selections at the system or rack level, you can apply redundancy exactly where it is needed - in specific input, output or processor modules - depending on such factors as the required SIL for a loop or the reliability of field devices.This is possible because the I/O and processing functions of ProSafe-RS have a modularity that extends down to the function level.
Even when an internal failure occurs, safety functionality is maintained, reducing the likelihood of a false trip in a process.
We call this flexible plug-in availability “VMR / Versatile Modular Redundancy™".
Partial Stroke Test (PST)
Under normal conditions, valves that are integrated with a safety instrumented system (SIS) are not activated. (They are only actuated when the SIS initiates a process shutdown after an abnormality is detected in a process.) It is therefore necessary to periodically test valves to ensure that they are in good working order and will respond properly when needed.
This periodic check is called a “proof test,” and generally it involves a full stroke test (completely closing the valves). When a plant is up and running, the costly installation of a bypass is necessary to conduct a proof test. If this is not possible, the only other option for conducting this test is to shut down the plant. As a consequence, proof tests of the valves are usually conducted only once every several years.
An alternative to the full stroke test is the partial stroke test (PST), which involves slightly closing a valve to diagnose problems. A PST can be conducted without stopping a process, and it can be performed remotely from locations such as a control room.
By conducting a PST, plant owners can significantly reduce their maintenance costs. And by checking the valves more frequently than is possible with the full stroke test, they can anticipate great benefits such as increased reliability .
Note: although the PST does not eliminate the need for a full stroke test, it makes it possible to extend the proof test interval without sacrificing the required safety level.
SIL2 wireless gas detection system
SIL2 wireless gas detection system is available for FGS.
In conjunction with expertise in production control, safety instrumentation, field wireless engineering and consulting, Yokogawa offers the most efficient and timely approach to deliver end to end wireless solution.
ProSafe-RS (SIL3 SIS) and
YFGW510 (Field Wireless Access Point)
Wireless devices have a number of advantages such as allowing installation in difficult-to-access locations and the reduction of installation costs, and they are increasingly seen as essential elements in plant safety solutions.
This is a particularly important consideration with gas detection systems, whose operation can be easily influenced by factors such as installation location and ambient conditions. Even after system installation, ongoing efforts to optimize its overall configuration may necessitate occasional changes in the location and number of detection devices. The use of wireless technology eliminates the need to worry about wiring and thus greatly facilitates the process of moving and/or installing additional detection devices.
Complied Certificate
- TÜV SIL3
- ISASecure CSA 1.0.0 Level 1 *1
*1: It complies with IEC 62443-4-2 and IEC 62443-4-1 international standards for security in control devices.
Click here for ISASecure Certification details
Complied Standards
ProSafe-RS system hardware conforms to the standards listed below. Please use the ProSafe-RS system in the industrial environment only.
PLC (Programmable Logic Controller)
- IEC 61131-2
Functional safety
- IEC 61508, IEC 61511-1, IEC 62061
Application
- EN 54-2, EN 298, EN 50156-1, NFPA85, NFPA86, NFPA72
Safety
- CSA
- CE Marking
- EAC Marking
- Morocco Compliance Marking
- UKCA Marking
EMC Standards
- CE Marking EMC Directive
- RCM
- KC Marking
- EAC Marking
- Functional Safety
- Morocco Compliance Marking
- UKCA Marking
Hazardous location equipment
- FM Non-Incendive
- ATEX Ex “ec”
- IECEx Ex “ec”
- ECAS-Ex “ec”
- UKEX-Ex “ec”
Marine Standards
- American Bureau of Shipping (ABS)
- Bureau Veritas (BV)
- Lloyd’s Register
- DNV
Migration from Legacy System to ProSafe-RS
Difficulty in continuing to maintain your legacy system due to higher costs of maintenance, deteriorating performance, unavailable of spares parts (SIS and PC), uncertain documentation and compliance issues. Yokogawa provides latest SIS and engineering services to migrate/replace your existing system.
Depending on your site situation and migration window, Yokogawa ProSafe-RS offers two options of IO system namely F-IO (conventional IO) and N-IO (smart configurable IO) to allow smooth and low risk migration..
Yokogawa offers services to reverse documentation and application of your legacy system. Validation can be done offline in advance with subject matter experts (Operator, Process Engineer, Maintenance Engineer) and leads to high level of confidence of the conversion. Finally, the validated documents can be imported to ProSafe-RS for application generation.
Migration from ProSafe-PLC to ProSafe-RS
Yokogawa is now offering a service that will allow you to migrate from the well proven ProSafe-PLC platform to our latest safety instrumented system, ProSafe-RS. ProSafe-RS uses a faster CPU and is seamlessly integrated with the CENTUM DCS, greatly improving performance and eliminating the need for a dedicated DCS gateway. ProSafe-RS provides complete integration with the operation and monitoring functions of the CENTUM DCS.
Two migrations plans are available to suit your project needs:
Plan 1 (recommended)
This is a complete replacement of the entire ProSafe-PLC system, including control and I/O modules, terminal boards, and wiring, with all elements of the ProSafe-RS system. The compact terminal boards are a key element of this plan.
Plan 2
The ProSafe-PLC control and I/O modules are replaced with ProSafe-RS control and I/O modules. With this plan, the existing field wiring can be used because the modified system continues to use the ProSafe-PLC terminal boards. This plan is implemented with the migration adaptors and the related products.
(Note: The end of support date for the ProSafe-PLC terminal boards is 2018.)
Resources
- A certified emergency shutdown system
- Substantial reduction in maintenance work
- System configuration with reduced footprint
- System scalability
- Meet the IEC 61508/JIS C 0508 functional safety standards
- Proactively introduce leading edge technologies
- Accommodate the plant licensors' safety, reliability, and maintainability requirements
- Improve the monitoring and operation functions of the emergency shutdown system
- Operational Excellence by Asset Maximization, Utilizing Yokogawa's DCS, SIS, Analyzers, and Field Instruments.
- The CENTUM VP PCS and ProSafe-RS SIS were integrated using the same engineering environment.
- Nearly 60 gas chromatographs and a large number of other types of analyzers in several analyzer houses.
- Integrated CENTUM VP and ProSafe-RS Systems Ensure Nonstop Operation of ADU/DKU Processes.
- "This is a real VigilantPlant! We will continue to improve our production efficiency."
- Rapid Implementation of Integrated CENTUM CS 3000 and ProSafe-RS.
- The highly reliable CENTUM CS 3000 system has also helped TOL maintain high productivity at this plant.
- Modern waste to energy facility in UK uses CENTUM CS 3000 and ProSafe-RS
- Lakeside exports at least 34MW per hour to the country's national grid
- As the main automation contractor (MAC) for this plant construction project, Yokogawa Brazil engineered, installed, and commissioned an integrated control and instrumentation solution
- Yokogawa Brazil completed the commissioning of these systems ahead of schedule and the production of green polymer was started just one week later
- World's first offshore regasification terminal relies on Yokogawa ICSS (CENTUM CS 3000, ProSafe-RS).
- LNG carrier scheduling, unloading, tank storage, and vaporizing are all procedure based operations.
- OTS for familialization of liquefaction processes and operator training.
- Yokogawa's integrated solutions contribute to safe and steady production at gas liquefaction plant in Norway.
Yokogawa Romania successfully modernized the control system at ELCEN's combined cycle heat and power plant.
A major challenge in deploying the system when all work moved to the virtual space was the Covid-19 pandemic.
- A robust and reliable integrated control and safety system (ICSS) made up of the CENTUM CS3000 PCS and the ProSafe-RS SIS ensures safe operations while fully automating key processes.
- A variety of analytical instruments accurately measure the concentrations of key components, and this data can be monitored and controlled by the Yokogawa PCS.
- Yokogawa supplied control, monitoring, and protection systems for plant modernization.
- Fine engineering and Yokogawa's products made successful operation without any problem or shutdown.
- Legacy ProSafe-PLC SIS replaced with ProSafe-RS to improve sustainable lifecycle support at LNG terminal.
- The seamless use of the same HMI for both PCS and SIS, and improved safety and integrity.
- DCS, SIS, PRM with FOUNDATION fieldbus and OTS Installed in Thailand First LNG Terminal.
- Alarms are issued before any device fails completely, enabling predictive maintenance that reduces maintenance costs throughout the facility lifecycle.
- FDT compliant FieldMate manages a wide variety of digital process instruments of multi-vendors.
- The SNF engineers can manage the complete lifecycle of assets and configure devices by using FieldMate.
Yokogawa provided integrated control and safety system to Banagas's CGP-3 gas processing plant.
N-IO based system contributes to reducing maintenance and other operating expenses (OPEX).
- Completion of First FPSO Project for Prosafe Production Services Pte Ltd
- Integrated Control & Safety System (ICSS) makes possible centralised plant supervision and management of all control and safety functions on this FPSO.
GC8000 was selected to detect components responsible for stainless steel corrosion of pipeline.
GC8000 with custom container analyzes crude oil components every 4 mins at an offshore platform.
The Mathura refinery is a strategically important facility that supplies diesel, gasoline, aviation turbine fuel, kerosene, liquefied petroleum gas, furnace oil, and bitumen to customers throughout northwestern India.
- Integration of CENTUM CS 3000 with ProSafe-RS improves plant safety and reliability.
- Yokogawa's PRM package manages more than 500 HART field devices including control valves.
To enable central control of the entire plant, all of its subsystems are integrated with Yokogawa's CENTUM VP DCS.
- HMEL selected an integrated solution from Yokogawa
- Yokogawa India oversaw and implemented the engineering, installation, and commissioning of the refinery
In maintaining and managing industrial plants, monitoring waste water pH/ORP is both a legal obligation and an unavoidable necessity for protecting the environment. Monitoring without an attentive eye can lead to severe consequences.
Wireless Hydrogen leak detection solution for Hydrogen cooling system of Turbine generator
Process automation end users are under more pressure than ever to do more with less. The current economic climate means that many automation capital projects are on hold. With capital budgets tighter than ever, users instead focus on operational budgets (where cost cutting is also a key concern), or on automation investments with a very rapid return on investment.
- Biofuel
- Biomass Power
- Bulk & Petrochemical
- Chemical
- Geothermal Power
- Iron & Steel
- Mining & Metal
- Offshore (FPSO FLNG & FSRU)
- Oil & Gas
- Oil & Gas Downstream
- Petrochemical
- Pharmaceutical
- Power
- Pulp & Paper
- Refining
- Renewable Energy
- Specialty & Fine Chemical
- Thermal
- Upstream
- Waste to Energy
- Water & Wastewater
- Water Treatment
Yokogawa has come a long way in making its message clear to the world of process automation. Last year, the company embarked on a full-scale global marketing campaign to make customers aware of the company's focus on system reliability, security, dependability, and robustness. Dubbed "Vigilance", the campaign created a unified message for the company and greatly helped expand awareness of the Yokogawa brand and corporate philosophy.
- Biofuel
- Biomass Power
- Bulk & Petrochemical
- Chemical
- Geothermal Power
- Iron & Steel
- Mining & Metal
- Offshore (FPSO FLNG & FSRU)
- Oil & Gas
- Oil & Gas Downstream
- Petrochemical
- Pharmaceutical
- Power
- Pulp & Paper
- Refining
- Renewable Energy
- Specialty & Fine Chemical
- Thermal
- Upstream
- Waste to Energy
- Water & Wastewater
- Water Treatment
Network and system security is now a necessity in process automation industry. YOKOGAWA provides a service lifecycle solution for cyber security to ensure that the security measures and deployments are continuously enhanced, monitored and inspected.
This white paper explains the details of the security design, implementation, operation and validation solutions from the technical perspective.
Recently, several ARC Advisory Group analysts and management team members had a chance to sit down with the new Yokogawa President and COO, Mr. Takashi Nishijima, and several other top Yokogawa executives to discuss the company's burgeoning presence in the worldwide upstream and midstream oil & gas industry.
Due to emerging competitors from the rapidly growing countries such as India and China and the global economic downturn triggered by the Lehman shock, many companies in the process industries are struggling to survive the severe global competition.
Migration of a refinery's DCS provided an opportunity to reconfigure and consolidate the control rooms and operational management system.
September 2006
Launched in February 2005, Yokogawa's ProSafe-RS safety instrumented system (SIS) quickly gained a significant share of the market. Just 18 months later, 100 units had been sold-quite a feat considering the generally conservative nature of the SIS market. So what is behind this rapid success?
April/May 2007
A Yokogawa ProSafe-RS safety instrumented system (SIS) will be the nucleus of a new fire and gas safety system at Shell's Clyde (NSW) refinery. The contract includes the control system, system engineering and installation and supervision.
LNG Industry, Summer 2012
Martin te Lintelo, Yokogawa, The Netherlands, discusses the need for better automation, measurement and control instruments to cope with the rising popularity of LNG.
Downloads
Brochures
- From ProSafe-PLC to ProSafe-RS (BU 32Q01M20-01E) (1.6 MB)
- Safety Instrumented System ProSafe-RS (BU 32S01B10-01E) (6.3 MB)
- Solutions for the Chemical Operations Executive (2.0 MB)
- Product introduction of ProSafe-RS Release 4 (BU 32P01A20-01EN) (1.2 MB)
- ProSafe-RS Standalone SIS (3.1 MB)
- Sustainable SIS Solution (BU 32P01A10-01EN) (7.3 MB)
- ProSafe-RS Partial Stroke Test (PST) (BU 32S51Q10-01E) (1.1 MB)
- SIL2 Wireless Gas Detection System (2.2 MB)
Certificates
- Certificate - ProSafe-RS - ISASecure Embedded Device Security Assurance Program (167 KB)
- TÜV SIL3 Certificate - ProSafe-RS R4.10 (664 KB)
- Bureau Veritas: Marine and Offshore (5.2 MB)
- ISASecure CSA 1.0.0 Level 1 (193 KB)
- Hazardous Approvals: Certificate of Conformity (515 KB)
- ABS Certificate of Design Assessment (2.4 MB)
- Certificate - Yokogawa - ISASecure Secure Development Lifecycle Assurance Program (230 KB)
- DNV GL Certificate for Ships. Offshore Units, and High Speed and Light Craft (174 KB)
- Lloyd's Register Certificate (378 KB)
Videos
ProSafe-RS is Yokogawa's IEC61508 and ANSI/ISA 84 compliant safety system. It has been used in over 2,400 projects, ranging from large scale integrated process automation projects to stand-alone solutions.
Yokogawa South Africa was appointed to design, supply and commission the Integrated Control and Safety System (ICSS) as well as the overall Terminal Management System at Sunrise Energy’s liquid petroleum gas (LPG) Import Terminal, the largest on- and offshore open-access LPG import terminal facility in Africa. Yokogawa’s Terminal Management System, Terminal Logistic Suite VP (TLSVP), was designed and developed to meet the exacting operational demands and logistic needs in terminals. Yokogawa’s experienced engineering resources ensured the project was successfully delivered, enabling Sunrise Energy to provide accurate mass balances and efficient terminal operations to its customers.
News
-
Press Release Jan 12, 2022 Yokogawa Enhances Cybersecurity and Safety for the OpreX Control and Safety System Lineup
-
Press Release May 24, 2021 Yokogawa Obtains ISASecure CSA Level 1 Certification for ProSafe-RS Safety Instrumented System, a Product in the OpreX Control and Safety System Family
-
Press Release Apr 11, 2017 Yokogawa Releases Enhanced Version of ProSafe-RS Safety Instrumented System
- Easy adoption and use as a fire and gas system -
-
Press Release Jul 14, 2016 Yokogawa Wins Major Refinery Control Systems Order from S-Oil Corporation
-
Press Release Jan 21, 2014 Yokogawa Obtains ISASecure EDSA Certification for ProSafe-RS Safety Instrumented System
Looking for more information on our people, technology and solutions?
Contact Us