Visual MESA® Production Accounting software provides a complete state-of-the art BEST-IN-CLASS solution for production/yield accounting and data reconciliation for the hydrocarbon and chemical process industry. It can model both the process side as well as the utility side.
Key areas for Operational Excellence Transformation
Operational Excellence Transformation is Yokogawa and KBC’s co-innovated portfolio of solutions and services.We provides comprehensive solutions for business automation in all four areas using consulting and digital technology.
Supply Chain Optimization
Supply Chain Management deals with satisfying customer demands by selecting the most appropriate feedstocks the plant can process efficiently, and delivering the products to the customers with maximum efficiency. Today, most of the industry SCM solutions are executed manually and/or separately. In most cases, specialized planning and software packages that have been implemented previously are not connected to other systems, such as sales and distribution and real-time production systems. As a result, the benefits of SCM are not fully realized.
Yokogawa's strategy to improve supply chain management starts with defining the corporate long-term strategy and aligning it with operations, maintenance and all other functions involved in the entire value chain. It includes:
Key Operational Competencies in Supply Chain Optimization
- Term Contract Planning: Commercial and economic evaluation of long-term contract obligations
- Supply Chain Planning: Economic optimization of the hydrocarbon supply chain for short-term, mid-term, long-term and strategic time horizons
- Price Deck Formulation: Generate price forecasts based on optimization boundaries and time horizons for feedstock and products
- Supply Chain Scheduling: Schedule optimized operations (process inventory and blending) over time, taking logistical constraints into account
- Commercial Contracting: Develop and negotiate favorable and competitive contract terms for feedstocks and products
- Inventory Management: Measure and reconcile the amount of each product made and raw materials consumed to produce an accurate material balance through production accounting and oil loss measurement
Yokogawa's approach to supply chain management involves digitalizing operations from supply to distribution. We then adopt the identified end-to-end optimization strategy to discover and manage all hidden costs (wastes) in the long chain. Our main objective is to find the Global Optimum to enable Just-in-Time in manufacturing and delivery for suppliers and customers, using minimum inventory and movement.
By applying digital technologies onto the end-to-end process of the supply chain (manufacturing raw materials to final products and managing purchase orders to good receipts), we may be able to improve the following:
- Customer & Supplier Experience: Deliver personalized engagement with an improved understanding of the product value directly to customers and suppliers
- End-to-End optimization: Extend the optimization horizon using real-time information on supplier delivery and customer demand across organizations and companies involved in the long supply chain
- Information Mobility: Enable optimal delivery and visibility by tracking personal location and activities with mobile technology
- Predictive Insights: Anticipate demand, supply and asset requirements with better insights
- Digital Business: Improve overall business agility and borderless collaborations by eliminating internal information silos
By combining Yokogawa’s product portfolio and KBC’s consulting services, we provide our customers best practices and domain knowledge that empower them to improve their operations, as well as a digital platform that supports such activities and initiatives. Our Operational Risk Management scope does not only cover partial improvements in the organization, but also optimizations in plant operations to achieve continuously improving safety, reliability and operability.
·Asset Operations and Optimization
- Optimize the potential of physical assets, by pushing throughput and maximizing the production of the highest value products, whilst minimizing variable costs such as energy.
- Deliver small and large capex projects, on time and on budget, to deliver growth and meet environmental requirements.
·Operational Risk Management
- Reliably control safety, health and environmental risk at a personal and process level. This assures the robustness required to avoid catastrophic losses.
·Asset Management and Integrity
- Confidently ensure asset reliability and availability, whilst controlling maintenance costs. This assures the asset always meets expectations and is always available to capitalize on short term market opportunities.
Visual MESA Production Accounting
Visual MESA Production Accounting delivers BEST-IN-CLASS Production Accounting by integrating engineering knowledge with expeditious yield accounting techniques creating the single version of the truth serving as the foundation of the facility’s hydrocarbon balance and loss control initiatives by automating the capture, balance, and tracking of complex-wide systems to increase efficiency and reduce operating costs.
Visual MESA Production Accounting provides all Mass Balance applicability in one tool, assisting users with the calculation of their site-wide, unit-wise, monthly, daily, hourly mass, volume, energy balances, in a collaborative environment from operations to the business.
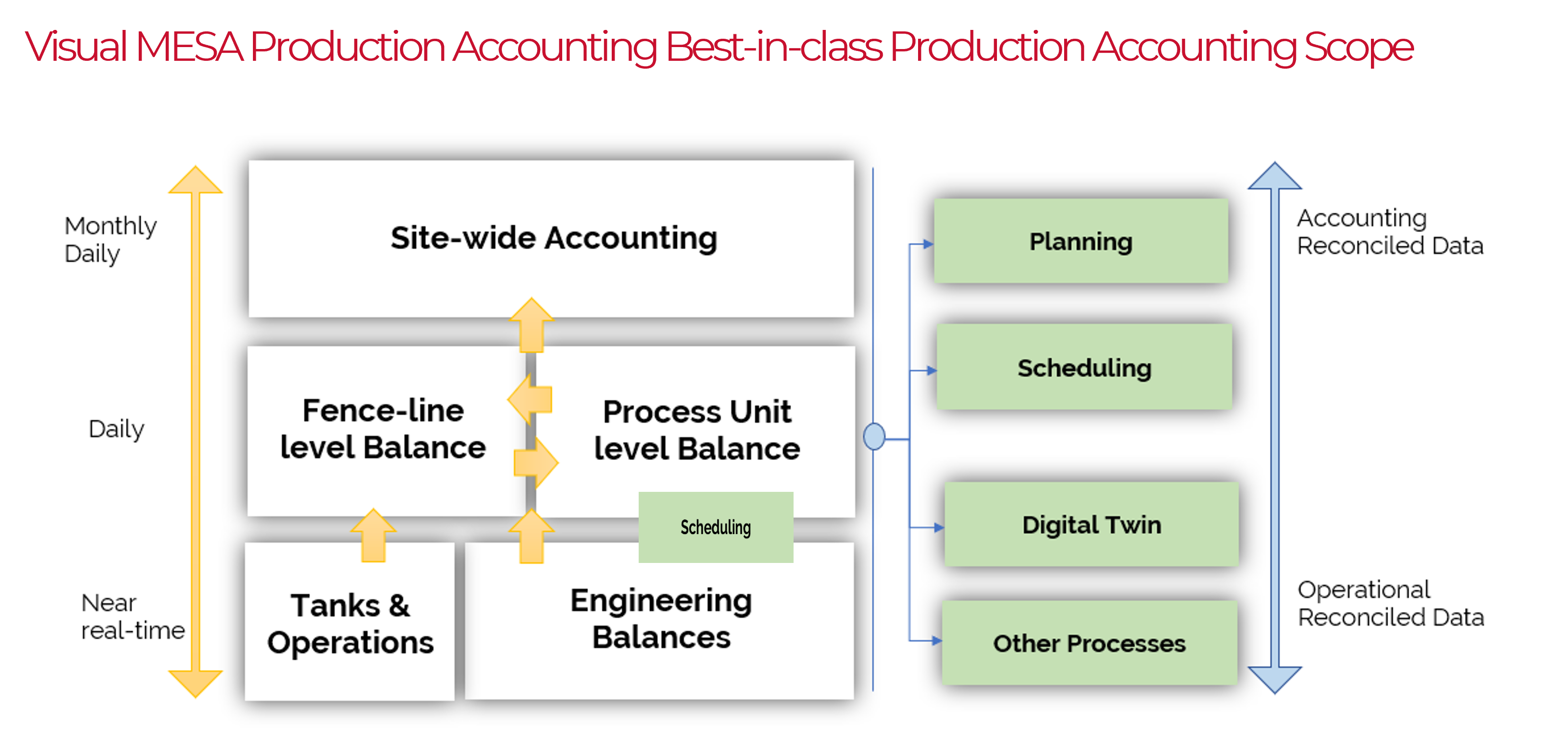
Customer challenges
Oil & Gas operators have huge value potential from their existing information. However, they currently lose thousands of dollars regularly due to the challenge of managing, tracking, and sustaining site-wide accounting data. The complex processes, poorly integrated workflows, lack of accurate information, and the associate costs for maintenance all play a factor in downgrading the value of production accounting as inefficient practices turn this into a tedious effort. Companies marginalize this activity to “only an admin task”.
By adopting accounting best practices to expedite the tasks together with incorporating engineering knowledge beyond the yield accounting methodologies, companies can maximize the value that can be extracted from the reconciled balance data.
The cost of ignoring this is a missed opportunity for improving both the operations and the business decision-making processes.
Visual MESA Production Accounting promotes and supports a set of practices following BEST-IN-CLASS production accounting.
Figure out whether your company is following Best-In-Class Production Accounting:
• Is your Production Accounting an admin task only?
• Is your Production Accounting run as a set of mandatory tasks for monthly balance closure?
• Does your company create new operations and business value out of the reconciled balance results?
• How many “pieces” form your full production accounting process?
• Is our paper accounting getting in the way of your physical accounting and operations?
Our solution
Visual MESA Production Accounting helps solve the issues above by delivering BEST-IN-CLASS approach creating time and the context to use the high-quality reconciled balance data for better opportunities. How we do it:
• By providing a holistic solution (end-to-end) for the whole production accounting business process from data capture, though validation, data exposure and further analytic contexts. This guarantees the larger visibility during the whole process.
• By delivering expeditious procedures that guarantee refinery-wide daily long-term sustainability.
• By integrating engineering knowledge and as built-in context/functionalities to maximize the value of the reconciled balance data.
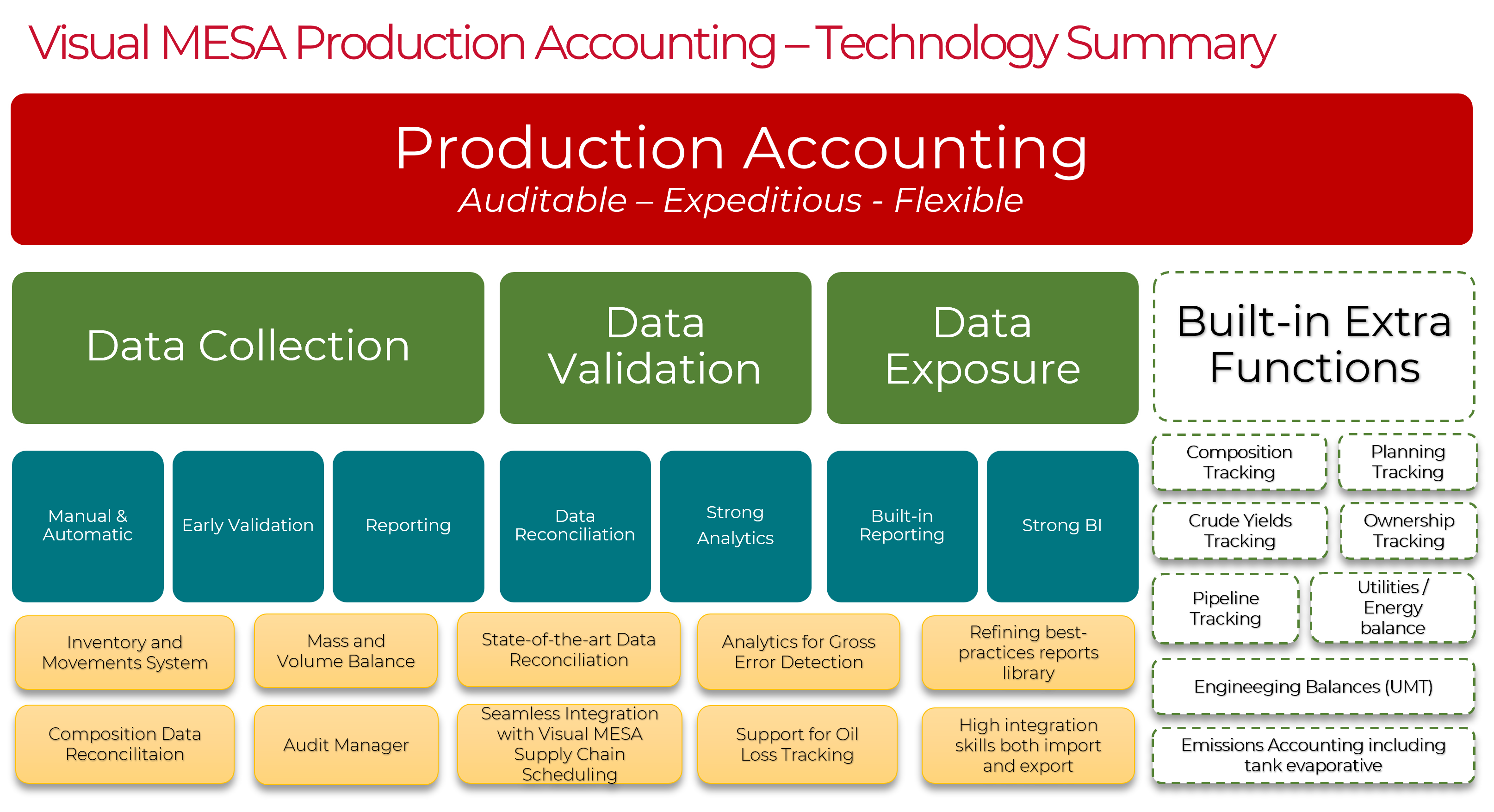
Key Features and Differentiators
All-in-one system
-
Oil movement management
-
Inventory management
-
Process unit balance
-
Library of +40 standard reports + Report Designer
- Powerful gross error detection
- Connectivity to virtually any system (historians, ERPs, etc.)
- Audit Manager
Benefit
1. As opposed to multiples systems, this makes sure data consistency, visibility and control through the whole accounting process generating better quality unique version of the truth.
All in one system also means one vendor, less maintenance, better support.
- Clear proven direction towards leveraging cloud/digital resources
- Best-in-class mass balance data reconciliation algorithm
- Best-in-class analytics
- SME’s support for both software and business processes
2. All this guarantees better quality data and expeditious procedures and hence long-term sustainability. The biggest value proposition of good mass balances is around the building of accurate models. As we transition into AI/ML surrogate models, the ‘true’ mass balance will drive correct optimization decisions from these models. The ML models will rely on good mass balances to find the global optima that may be far away from current operation. The further they are away from optima, the more magnified the error will be without good mass balances.
- Integrated workflow with KBC’s scheduling solution
- Composition Tracking
- Pipeline Tracking
- Planning Tracking
- Hydrocarbon loss tracking
- Tank evaporative emissions
- Metering system quality tracking
- Crude oil traceability
- Mass, volume, and energy balance (hydrocarbon and utilities)
- Balance Monetization
3. All this guarantees that the high-quality reconciled balance data generated will be used for further engineering analysis rather than the accounting process is downgraded to only an admin task. This intends to maximize the value out of the unique version of the truth supporting correct decision-making processes.
Value proposition
- Data consistency, visibility and control through the whole accounting process generating better quality unique version of the truth to support all decision-making processes
- Only one vendor for the multiple “pieces” that form the production accounting business process
- Expeditious procedures to support long-term sustainability
- Better quality and timely reconciled balance data to improve decision making processes
- Maximization of the value of reconciled balance data through built-in context/functionalities and the integration on engineering knowledge
- Improved LP based on site wide model feedback.
Find more details on this page
Looking for more information on our people, technology and solutions?
Contact Us