Introduction
After extraction from sugar cane or sugar beets, juice must be purified to remove the many other organics and minerals that accompany it. The processing to accomplish this is heavily dependent on reliable pH measurement and control as illustrated.
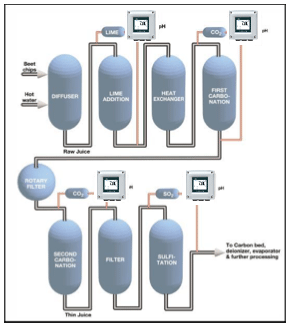
The process for refining raw sugar cane or sugar beets includes the following steps: washing, crushing, extraction, liming, carbonation, filtering, and addition of sulfur dioxide, concentrating, crystallizing and drying. Of these various steps the most critical are: liming, carbonation and the addition of sulfur dioxide. Each of these steps requires continuous pH control.
Lime Addition
Thorough washing of the sugar cane or beets is followed by crushing or cutting into chips and counter-current extraction of the sugar by hot water in a diffuser. The resulting "raw juice" is treated with alkaline 'milk of lime' (calcium hydroxide (CaOH) slurry), based on pH controlling to a set point of 11.0 to 11.5 pH.
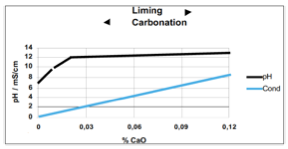
The purpose of adding Lime is threefold:
- Neutralize acids in the cane of beets, thereby preventing the sucrose from turning into starch (hydrolysis) or other forms of sugar (inversion).
- Precipitate the organic acids into salts for subsequent removal.
- Keeping foreign matter (insoluble organics, proteins, etc.) in suspension until a filtration process can remove them.
Carbonation
All traces of lime must be removed before the concentration step to prevent scale buildup. Carbon dioxide, therefore, is added to the juice to precipitate the lime as less soluble calcium carbonate (limestone), which also tends to capture other impurities during precipitation. CaO + CO2 = CaCO3 (solid).
The sugar solution is heated and carbon dioxide is added by pH control. Optimum purification is achieved through two stages of carbonation to avoid an unmanageable type of precipitate that can develop in single stage carbonation. Close pH control is necessary at each stage to assure maximum removal of both impurities and calcium. By the last stage the pH should be reduced to about 9. After carbonation the juice is filtered to remove all traces of solid particles before transported to the sulfitation tower.
Add of Sulfur Dioxide (Sulfitation)
The juice is maintained at high temperatures and treated with sulfur dioxide to lower the pH to roughly 5-6 before it goes on to the evaporators. The sulfur dioxide also bleaches the juice to improve flavor and texture. Without this step an alkaline juice would be produced. The sugar crystals would stick together due to moisture absorption and have an undesirable taste. Again, pH control is essential to efficient operation. The sugar juice is then heated to drive off any residual gases and provide a neutral product.
Further purification sometimes uses carbon beds and ion exchange resins, to remove the last traces of color and impurities. (Conductivity measurement is a key variable in monitoring the operation and regeneration of ion exchange beds.) The purified thin juice then moves on to multi-effect evaporators for concentration, vacuum pans for crystallization, centrifugal separators and dryers.
pH Sensor Requirements
pH sensors must stand up to severe process conditions during the liming and carbonation stages, to provide consistent measurement.
Difficulties
- CaCO3 precipitates on every surface including probes.
- Carbonators operate at 95°C
- Sugar juice temperature compensation curves do not conform to standard temperature correction curves
- Sugar juice contains Sulfur dioxide that reacts with typical reference probes
- Environmental conditions are wet, hot and corrosive
Application Solutions
Analyzer
The Yokogawa FLXA402 has an automatic sensor washing function, self-diagnostics and custom temperature compensation. Besides the cleaning function the sensor washing cycle also provides an online response test, giving an immediate indication of sensor deterioration.
Sensors
In the past mainly single electrodes was used. Installation was done in the bypass together with a chemical cleaning system. To prevent the reference sensor from clogging and poisoning a flowing type reference sensor, like the well- known Bellomatic electrode, was preferred.
As pH- electrode a heavy duty glass electrode with chemical resistances as well designed for high temperatures was used. Today Yokogawa's combined pH- sensors such as SC25, FU20 and FU24 are fulfilling these demands and are used successfully in this application.
If the sensors are cleaned regulatory with diluted acids they will offer good service life. (cleaning frequency depending on the application: carbonation 1st tank or 2nd tank). By using an automatic retractable cleaning system (e.g. EXAtrac) even a direct process installation is possible.
The transmitter stores the calibration data and if the asymmetry potential exceeds 50 mV and the slope drops below 80%, then replacement must be considered.
相關業種
-
食品 & 飲料
在食品製造業中,除了需要應對「食品安全」、「糧食安全」、「降低成本」這些傳統挑戰,還需要面對病菌和減少勞動力的挑戰。
橫河Yokogawa與客戶密切合作、共同應對挑戰、提出理想工廠的解決方案,幫助生產廠商創造更舒適的工作環境。
相關產品&解決方案
-
12 mm SC25V pH傳感器
SC25V是一款12 mm的pH傳感器,包含一個一體型溫度元件和一個液體接地電極。
-
FU20/FU24/PH20一體化pH/ORP (REDOX)傳感器
PH20/FU20/FU24一體化pH/ORP傳感器體現了橫河電機如何將“簡單即好”這句格言應用於傳感器技術。
-
四線式液體分析計 FLXA402
The FLEXA™ 系列分析計是模組化設計的分析計,用於工業裝定中的連續線上測量。提供單一或多sensor測量。
-
數位 SMART SENCOM™ 轉接器: SA11
可重複使用的 SMART 轉接器,只需在感測器達到其使用壽命時進行處理。橫河電機的SENCOM 4.0平台,可降低營運成本和資源浪費,同時貢獻永續未來的長期業務目標。
-
液體分析計
液體分析計用於水質和化學的製程監測,進行製程最佳化和控制。