現場快速測量工業條件
雷射氣體分析儀(TDLS)可以進行即時氣體分析,提高效率、安全性、產量、品質和環境合規性。非接觸式傳感器可在高溫、高壓、腐蝕/磨蝕、高粉塵濃度等惡劣條件下進行測量。由於TDLS與流程隔離,因此可以在運行中的製程執行維護。TDLS是一款功能強大的製程分析儀,幫助實現穩定和高效的操作。
>>> 應用說明
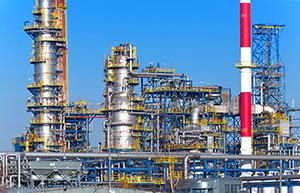
- 可在惡劣環境進行現場測量
- 測量溫度可達1500℃
- 光程長度可達30米
- 可選SIL 2和SIL 3認證,與SIS整合
在不穩定的製程中延長正常運行時間
各種工廠和管道可能含有加壓、高溫、腐蝕性、可燃和/或有毒氣體,這對傳統技術可能造成問題。TDLS8000可以在非直接接觸的情況下即時檢測工業氣體的濃度,實現快速響應,在不損失測量可用性的情況下優化工業可用性。
>>> 原理
改善運營成本和提高安全性
TDLS8000幫助降低總運營成本,在保障安全的前提之下盡可能地提高產量。
例如:TDLS8000可以測量爐長30米輻射部分的頂部,分析有效燃燒。根據氣體濃度,操作人員可以優化空燃比,分析傳熱效率,同時確保安全的環境。
>>> 解決方案
>> Yokogaw橫河TDLS技術幫助各行業提高運行安全性並改善排放<<
TDLS8000 旨在幫助使用者滿足各種操作標準,並且能夠整合到 SIL2 和 SIL3 應用中。
>>> 改善營運
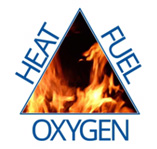
-
TDLS8000在線氣體分析儀
橫河電機的新TDLS™8000功能強大,將諸多先進工業特性集成於一台耐用設備中。其平台設計適用於現場測量,無需進行樣品抽取和樣品處理。
-
探棒型雷射氣體分析儀 TDLS8100/TDLS8200
無需採樣,法蘭僅安裝在一側,保持高速測量/響應的同時,安裝成本也降低一半。與現有設備更換容易。
Details
TDLS 有助於改善您的工作。
TDLS系列的特點
- 在數秒內測量氧氣、一氧化碳、甲烷、氨氣、水分、二氧化碳和其他氣體
- 大多數測量不需要採樣設備,節省了大量維護工作
- 唯一能夠測量長達 30m 的製程 TDLS 平台
- 感測器不與製程氣體接觸,因此可以在高溫、高壓、腐蝕性/磨蝕性和高粉塵條件下進行測量
- 非常適合具有 SIL 等級快速反應速度的關鍵應用
- 最大限度地提高效率,考慮環境,並減少二氧化碳、氮氧化物等的排放。
接受新興科技
全球不斷朝著提高製程效能的方向發展,同時保持安全運行狀態,如果不採用新的測量技術,就很難保持競爭優勢。 >>>原則
TDLS 提供安全、高效且經濟高效的解決方案。
雷射氣體分析儀的基本概念與量測
雷射氣體分析儀的測量原理
可調諧二極體雷射吸收光譜儀 (TDLAS) 的工作原理是測量雷射穿過測量氣體時被吸收的量。由於感測器不與製程接觸,且沒有移動部件,最大限度地減少了維護工作,進而減少停機時間並降低長期總成本 (LTCO)。
由紅外線吸收引起的衰減由蘭伯特比爾斯定律決定。
蘭伯特比爾斯定律
吸收紅外線輻射
橫河電機獨特的光譜分析方法,可以在不同的蒸氣條件下進行高度可靠的測量
獨創的光譜面積法幾乎不受其他氣體的幹擾,並且透過溫度和壓力補償可以實現高精度測量。
即使在低吸收流中,整合參考池也能保持測量完整性
當吸收訊號較弱時,使用參考池可在跡線測量過程中鎖定峰值位定。
可存取最多 50 天的歷史資料、光譜和所有設定變更
此資料對於在發生故障後很長時間內對製程問題進行遠端故障排除非常有用。
測量能力的增強使我們的用戶能夠安全地提高營運效率,同時減少排放。
- 原位分析
由於近乎即時的回應,提高了安全性和製程控制能力 - 可調諧雷射
沒有移動部件,因此不存在消耗品 - 非接觸式感測器
在惡劣環境下運作並最大限度地減少維護 - 長通光學感測器
代表測量的整個過程,而插入或提取測量僅反映一個點。
TruePeak 可調諧二極體雷射光譜儀的工作原理是測量雷射穿過被測氣體時被吸收的量。由於感測器不與製程接觸,也沒有移動部件,因此平均故障間隔時間 (MTBF) 較長,因此長期擁有成本 (LTCO) 較低。
火焰加熱器是工業流程不可或缺的一部分,包括碳氫化合物加工和發電。加熱器專門設計用於燃料和空氣反應產生極高的氣體溫度,透過熱交換器將這種能量轉移到潛在高度易燃的製程流體。它們消耗大量燃料,產生大量排放物,對人員和工廠有安全隱患。
橫河TDLS分析儀有助於以更高的精度和可靠性控制火焰加熱器的燃燒。在低過量空氣 (LEA) 水平下運行火焰加熱器會帶來可觀的回報。在 LEA 燃燒控制中,燃料消耗量最低,燃燒產物被未使用的過量空氣冷卻最少。
這些效率帶來的成本效益非常可觀,只需節省百分之一的燃料,每年就可以節省數萬甚至數十萬美元。將空氣水平控制在不完全燃燒開始點之上也能夠實現「最乾淨的燃燒」。幫助工廠滿足環境排放要求。這尤其減少了氮氧化物的排放。
燃燒
保持熔爐的運作效率,最大限度提高產量並最大限度地降低燃料消耗,同時確保安全運作確實是一項艱钜的挑戰。
傳統的分析儀技術(例如氧化鋯和催化Catalytic bead 測量)是點式測量,無法完全捕獲爐中發生的情況。除了作為潛在的火源之外,氧化鋯在存在可燃物的情況下也會降低其讀數。 COE 分析有其自身的問題,因為在燃燒資產的輻射部分中達到數千 ppm 的典型突破水平需要數分鐘的反應時間,並且通常需要單獨的感測器來進行 CH4 測量。此類問題可能會對熔爐的安全運作產生重大影響。
如果營運商想要優化資產效能,需要存取最值得信賴的可用數據,以快速減少不安全情況的發生。
橫河電機可調諧二極體雷射光譜儀(TDLS)技術的引入可實現即時、原位、無幹擾、可靠且準確的氧氣和二氧化碳測量,最大限度地提高效率。
確保整個設施安全之外,並能有效率地營運資產。
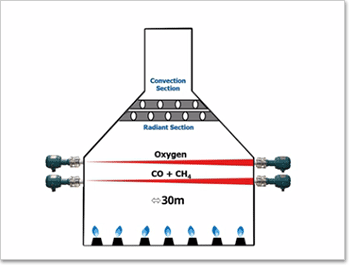
橫河TDLS技術的特性與優勢
- 使用即時資料進行控制
由於空燃比始終處於最佳化狀態,可以安全地提高運作效率和排放,實現效率最大化 - 雷射分析
新技術可以採用業界最佳實踐。 - 非接觸式感測器
在惡劣環境下運作並最大限度地減少維護 - 長光程光學感測器
長路徑平均測量消除了熱點,從而延長了熱交換管的使用壽命(成本最小化)。
安全/製程
當要了解爐子中發生的情況時,傳統分析儀技術對有限數據輸出的依賴使操作員的技能承擔了更大的責任。
TDLS技術可快速提供整個熔爐最值得信賴的數據,實現最佳資產效率和安全性,減輕操作員能力的負擔和潛在的人為錯誤。
您必須有能力檢測、測量和控制 LOC(極限氧氣濃度),以確保您的設施和同事的安全。
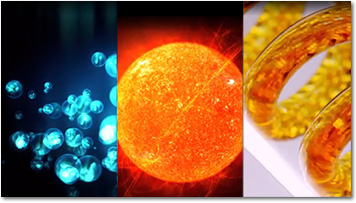
我們的客戶營運安全和營運效率使我們能夠降低營運成本並減少 CO2 和 NOx 排放.
參考
In maintaining and managing industrial plants, monitoring waste water pH/ORP is both a legal obligation and an unavoidable necessity for protecting the environment. Monitoring without an attentive eye can lead to severe consequences.
Considering safety and environmental issues such as combustion efficiency and decreasing NOX and CO in exhaust gas, it has become important to control O2 concentration in garbage incineration processes.
In recent years, shale gas extraction technology has made rapid progress, inducing a shale gas revolution mainly in the USA. Thus, the need for analysis of hydrocarbon gases, including natural gas, is expected to grow rapidly. Traditionally gas chromatography has been used for the analysis of hydrocarbon gases; it can accurately measure the concentration of each hydrocarbon component in a sample of natural gas.
Spectrometric technology can assess many critical characteristics about products, but it has limits. It can be challenging to determine when the line has been crossed
With fired heaters, users hope to get greater efficiency and reduced emissions but often are disappointed. Given the number of fired heaters operating every day and their importance in the process industries, any improvements realized across the board will have huge impacts. More units can reach their potential with some simple changes in work practices and technology upgrades.
The EPA rule, 40 CFR 63 Subparts CC and UUU, is forcing refineries to monitor flares. Fortunately, modern analyzer technology makes it possible to meet the requirements, generate the necessary reports, and stay in compliance.
Here’s how to select the right analyzer to meet these demands.
下載
新聞
-
新聞 | 解決方案&產品相關 2021年4月6日 OpreX分析儀系列推出TDLS8200探棒型雷射氣體分析儀
- 同時測量氧氣、一氧化碳和甲烷的濃度,實現最佳燃燒控制 -
想了解更多技術&解決方案嗎?
聯絡我們