Executive Summary
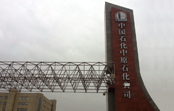
Sinopec Zhongyuan Petrochemical, China
Coal is an important resource of energy in China, and the conversion of coal to a wide range of chemicals has become increasingly important in recent years. Sinopec Zhongyuan Petrochemical Co., Ltd. (hereinafter referred to as "ZPC") is a large joint venture between China Petroleum & Chemical Corporation (hereinafter referred to as "Sinopec") and the government of Henan province. With significant support from its parent organizations, ZPC has built a new 600,000 t/y methanol to olefins (MTO) plant and a 100,000 t/y polypropylene plant, along with all the necessary utility and auxiliary facilities, in Puyang. These plants became operational in October 2011 and are of great strategic significance to the development of Sinopec's coal-chemical business.
An MTO plant uses catalysts to convert coal-derived methanol into olefins such as ethylene and propylene. This MTO project uses Sinopec's proprietary S-MTO process, which is characterized by high olefin selectivity, high methanol conversion, and low catalyst consumption. To ensure safe and stable operations at this MTO plant, which handles materials that are highly flammable and explosive, delicate process control is required.
For this large-scale greenfield MTO plant, ZPC and Sinopec Engineering Inc. (an engineering, procurement and construction company referred to henceforth as "SEI") selected Yokogawa China Co., Ltd. as the main control system supplier. For this project, Yokogawa China delivered the CENTUM CS 3000 process control system (PCS) and the Plant Resource Manager (PRM) software package for plant asset management (PAM).
The Puyang MTO plant
The Challenges and the Solutions
1. Quick implementation
Because the control logic for the S-MTO process is so complicated, the engineering work for this project was very complex and time consuming. Yokogawa engineers made good use of their deep knowledge and experience in the ethylene and coal chemical fields to expedite work on this project and deliver ahead of schedule very high quality work, which helped to ensure a successful and efficient commissioning and startup. ZPC, SEI, and Yokogawa all took a team approach and worked closely from start to end. Thanks to their good synergy, they were able to complete this project ahead of schedule.
2. Safe and stable operation
To ensure safety at these plants, ZPC needed to closely monitor and control its processes, especially those involving chemical reactions and heat exchange. For this S-MTO project, Yokogawa's PCS was integrated with a third-party safety instrument system, compressor control system, and online process analyzer system via Modbus, which allows operators at the human machine interface (HMI) stations in the central control room to monitor and control operations throughout the plant, ensuring that they can respond quickly when faced with an abnormal situation. Plant safety and stability are thus assured.
The MTO plant's central control room
3. Efficient maintenance
The MTO plant has a large number of HART-enabled pressure transmitters, flowmeters, valves, and other devices from different suppliers. Having real-time diagnostics for these devices helps operators keep close track of their status and identify maintenance issues before a device fails. For central management of these devices, they are all integrated with the Yokogawa PCS via the PAM software package. Using the HART protocol and the PCS network, the PAM system gathers all the device data and diagnostic information into a single database. If a device problem is identified, engineers are able to check the device in time and clarify the cause. This centralized asset management minimizes trips to the field and ensures a more proactive maintenance approach. During plant startup, this system also helped the engineers check all loops.
Customer Satisfaction
The Director of the Instruments Department at ZPC points out the following three factors about this project: "First, Yokogawa's CENTUM CS 3000 has excellent reliability and stability. We particularly appreciate its online maintenance capability. Configuration changes are immediately shown on the HMI without interrupting the control function. This is important in completing startup in a short time and improving and optimizing process control. Second, this is an S-MTO pilot project using Sinopec's proprietary technology. During control engineering, Yokogawa's engineers showed that they have a deep understanding of control solutions and a lot of experience in dealing with complex problems. They made good use of their know-how from the petrochemical industry and, working together with engineers from ZPC and SEI, were able in a very short time to produce high quality engineering. Third, ZPC's personnel have considerable experience operating Yokogawa's CENTUM CS 3000 system, enabling the project partners to perform to the best of their abilities during the project implementation phase. At the same time, Yokogawa's engineers were fully involved in the control engineering, FAT, SAT, and startup. Above all, the key to the success of this short-term project was the good cooperation and teamwork of ZPC, SEI, and Yokogawa."
相关行业
-
大宗石油化工
无论是生产石化产品、无机物还是中间产品,化工企业都面临着成本和利润率的压力,必须及时有效地交付产品,同时保持安全、合规地运营。此外,化工企业必须应对原料和能源价格的波动,并为市场提供适合的产品组合。
横河电机长期服务于大宗化工市场,得到大家的广泛认可。通过我们的产品、解决方案和行业专业知识,横河了解您的市场和生产需求,并将与您合作,在您的工厂生命周期中提供可靠、经济的解决方案。
-
石化
石化公司的需求极为多样繁杂。为了在当今激烈的市场中脱颖而出,生产企业必须努力提高质量和生产力。横河电机在石化领域长期耕耘具有广泛的经验,我们可以为客户的需求提供量身定制的解决方案。
-
化工
化工厂依靠连续和批量的生产过程,每个生产过程对控制系统都有不同的要求。连续的过程需要一个强大而稳定的控制系统,该系统不能因为自身失效而导致生产线关闭;批量过程的要点在于拥有一个可以灵活调整地公式和程序的控制系统。两种系统都需要在产品质量记录中进行管理,并且能够执行非常规操作。横河电机凭借广泛的产品组合、经验丰富的系统工程师、广泛的销售和服务网络,为工厂流程提供解决方案。
相关产品&解决方案
-
工厂资源管理系统(PRM)
工厂资源管理系统(PRM)是横河电机用于资产管理的一个关键平台。该平台旨在改进操作和维护,通过获得更大的可预测性,使工厂资产的可靠性和可用性增强。
-
集散控制系统(DCS)
横河电机的集散控制系统(DCS) 可实现工业过程的自动化和控制,并提高业务绩效。30,000多套系统的经营者选择采用横河电机的DCS来实现其生产目标。